A Roadmap to Automated Composites
- Pravin Luthada
- Aug 7, 2019
- 5 min read
Updated: Jan 8, 2021
Transforming your manual production processes to automated composites manufacturing is going to be the norm in the future. However, this is not going to be an easy exercise to perform in your organization, as the workforce involved needs to be informed and retrained; and new systems/processes have to replace the old ones.
The goal of this article is to provide you a framework to walk through whilst you are thinking of automating your existing production. The framework here will get you involved in analyzing elements in your production process in a structured manner and could help provide greater insight on how your personalized road map looks.
Why we love doing things by hand, but to a certain extent!
The manual process forms the backbone of the composite production industry, as it is easy to get going without high capital investment. This is why many manufacturers want to stick to the manual processes, despite the increase in production volumes.
This becomes a major business challenge, as it is becoming increasingly challenging to find workforce skilled in the art of making composites. Not that workers do not enjoy the smell of epoxy/styrene resins, or chopped glass fiber, in the air. It is just becoming harder to find them.
So as a decision maker for your company, you need to step up the game and find automation that is suitable for you!
Analyzing the present workflow. I would not skip this
The first step is to understand the ground reality on the shop floor. In order to do this, we need to break down the present production methods into sections. It could be split up by process type, material, parts, etc. create a visual that gives you a better understanding, such as:
Further, each of these elements can be analyzed through the following questions:
Which part of the processes, that you see, takes a lot of manual labor (time/personnel)?
Which part of the process, if made faster or improved in quality, can make the process flow more smoothly?
Which parts make sense to automate (e.g. chemical-intensive work, quality critical, time critical, etc.)?
Please feel free to add your own question to the list. The goal here is to identify the section of each process and part that can benefit the business most from automation in the most pragmatic manner. Once you have gone through the exercise, scoping and defining the problem can be considered half the battle. Now we have a well-defined set of challenges at our hand that, if solved, can impact business in an intended manner.
Identifying the solution; a long yet fruitful process
This is a slightly boring part of the process, as it takes the longest to define and complete. In order to get started, an industry sourcebook and suppliers are great sources of information. The key characteristics of your solution can be divided into the following:

Adaptability: A standard solution that can adapt to your need. Do not request a customized solution for your need, as you will limit yourself to a specialized supplier with no guarantee of future support.
Scalability: Given that you would want to expand the production in the future, the system should be able to scale up your production without any changes in the process.
Digitized: The key is to be able to capture process data. The main point here is to identify process critical data and a way to capture it. This has the potential to reduce or eliminate periodic quality inspection, as everything becomes in-situ.
Major roadblocks in change
After identifying the solution that would fit your requirements, the next step is to inform and execute the change in the organization.
People
It is very critical that the information on upcoming changes is communicated with positive intent and everyone involved in the value chain is aware of the “Why”. The goal is to get the workforce prepared, geared up, and onboard for the coming change. They want to feel like change-makers, not the reason for the change.

Capital
Once everyone is on-board the change wagon, now the team is ready to present the case to the approval authority e.g. the finance department. This department will never accept a heavy Cap-ex investment that is not proven on the shop floor.
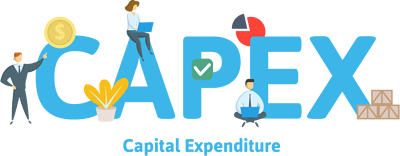
The subscription model of acquisition: From vehicles to housing, you haven't had to make a long term purchase to reap the benefits. Now, this approach has also come to the composites industry.
AFP-XS by Addcomposites has created a plug-n-play toolhead that is easily mounted onto any existing manufacturing robotic arm. With the popular assumption that most future factories would employ robots and automation, this toolhead can be moved around anywhere in the facility without disturbing ongoing production. The subscription-based model, with its low monthly payments, greatly reduces the main challenge of high acquisition costs, while maintaining the quality standards expected of tape laying systems.
Not that this is a one-size-fits-all solution, but it provides a great springboard into composites manufacturing automation for only a few thousand euros!
Expected benefits
The end goal is to experience a tangible improvement in the process. The best way to provide indisputable evidence of improvement is to quantitatively analyze the process before and after the implementation of such a system.
Product quality and reliability
In a world where social media has made the voice of the customer far more public, warranty returns and defective materials that elude quality assurance practices and make it into the field can be very damaging to the reputation of manufacturers. Additionally, the cost and time associated with rework parts during the manufacturing process is delaying production. If the matrix is applied too thick, the surface becomes susceptible to cracking – too thin and the gel coat won’t cure correctly, resulting in durability and appearance concerns. A robotic solution provides a repeatable outcome that can improve these product quality and performance issues through increased consistency and uniformity.
Material savings and wastage
Reducing waste at the point source of origin is the key to material savings. Robots and their dispensing systems are very accurate, with precise trigger timing and constantly repeatable motion dramatically reducing variance in the amount of material used. A robotic application pattern reduces excess material placement, leading to material optimization and a reduction in material waste. Closed loop material delivery systems can be included in a robotic solution to monitor and provide consistent fiber application, adjusting the material feed delivered in line with minor changes in the manufacturing environment.
Shorter cycle times
A robot can repeat difficult ergonomic tasks with speed and accuracy. Normally, the robot is limited by the application speed, which best practice may dictate as 500 mm/s, however the robot is able to transition between trigger ON and OFF points at much greater speeds. Assuming consistent operation, it is typical that a robotic cycle time will be less than compared with manual operation, and the layer application is typically more uniform. A robotic solution is often able to operate across multiple shifts, amortizing the value of the equipment and the factory when competing on a global platform for manufacturing economies of scale.
Increased employee safety and the environment
Removing manual operators from potentially hazardous fumes in a resin or fiber application can support improvements in workplace safety. Robots can be designed to operate in Class 1 Division 1 environments, meaning potentially hazardous tasks can be completed in a far safer manner, reducing the exposure of employees in a manufacturing facility to potentially hazardous environments.
The environmental, financial and quality benefits of introducing robotic automation to the composite industry cannot be overlooked, as manufacturers continue to strive to compete on a global platform.
Reaping the Benefits
When you do decide to implement composite automation at your facility, you need to know how the speed of layup compares to your current labor. The following case study was performed by Addcomposites, which compares the AFP-XS to average manual layup speeds.
With the implementation of only a single AFP-XS, it is possible to quadruple the production capacity within the cell, while increasing quality standards and improving repeatability.
Implementing new automation can be a daunting task, but by breaking the entire process into manageable sections, it becomes much more achievable. Reach out to us today to request a demo of the AFP-XS, and determine if it is the right addition to your facility! We look forward to joining you on your automation journey.
Comentarios