Future Composite Manufacturer: Agile-Smart-Small series
- Pravin Luthada
- Nov 28, 2019
- 3 min read
The majority of composite manufacturers are engaged in providing small volume production service, and believe that the small volume production does not have room for automation; either due to high cost or will introduce unnecessary complexity. Let's dive into where these thoughts usually come from...

High capital Investment

Automation systems very expensive. It is primarily due to the amount of R&D that goes into technologies like Automatic Tape Laying (ATL) and Automatic Fiber Placement (AFP), as well as their traditional customer segment. But implementation of fully automated cells for Resin Transfer Molding (RTM) are also quite costly, which are found to be used for high volume fabrication of composite structures, such as for the automotive industry. These manufacturing equipment are associated with huge capital investments, because they took time to develop and are priced based upon perceived value added to each one's end user.
Not flexible

All the above-mentioned processes have been proven in their specific use cases, and have always been used for single part type production. Despite the AFP process capability, it has been largely restricted to the single wing shape application. So the common notion among composite manufacturers is that these automation processes are rigid and something that is unable to change or react with little penalty in time, effort, cost, or performance.
Only limited materials
Be it small or big, the material that has dominated the composite industry has been carbon fiber. Additionally, this has kept most automation systems restricted and unable to use glass, natural, or other fibers. This provides more evidence that these systems are only optimal for very select material.
Lets cut the bullshit and get to what is actually possible
Despite the common notion, recent technological developments can help us understand what is possible today and make our own judgment. Misconception about cost, flexibility, and material can be well addressed with a demonstrable solution like a mini-factory. Below we tried to estimate the cost for building a mini-factory at a composite shop floor and evaluate the above-mentioned misconceptions that are held!
Mini Agile factory of composites
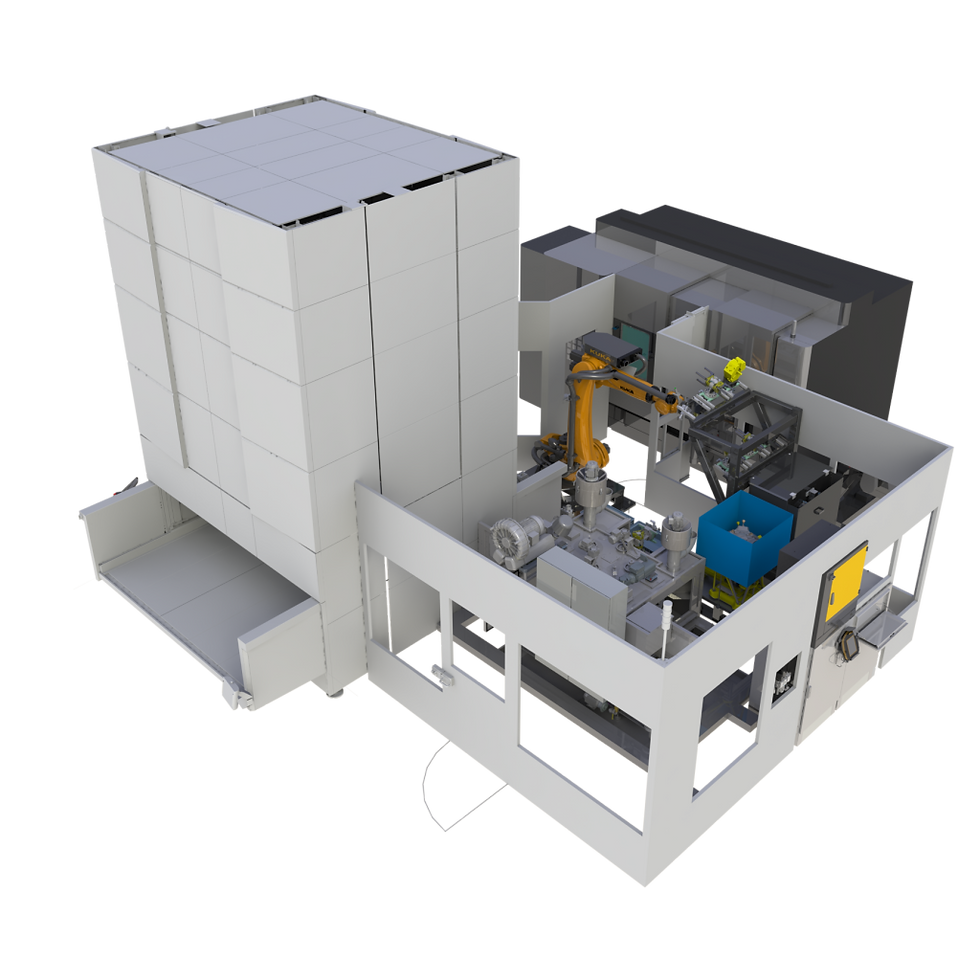
With the digitization of each process, a manufacturer can envision a shop-floor, and respond quickly to customer needs with a fast-changing market.
Tooling: Digitally produce your tooling with Stratasys and Plyable solutions.
Layup: AFP-XS is the plug-and-play into any motion platform to start producing composites.
Finishing: trimming and polishing with Mirka® AIROS.
Capital needed: 27 000€ to 42 000€
The complete manufacturing setup above can be implemented with a single robotic cell in your composites production floor. Below we have estimated the cost for each element and in total it comes out to between 27 000€ and 42 000€ to get your Mini Agile factory of composites up and running.
Tooling: 0 €, leveraging the digital platform no capital needed
AFP-XS: 1999 - 2750 €/ month
Mirka Aros: 500–1500 €
Robotic Cell: 40 000 € for working of 1x1 meter for complex shapes
X-Y motion platform: 25 000 € for working of 1x2 meter for flat preforms
Freedom of material

Given the immense freedom any manufacturer can have in making composites, most manufacturers have preferred expertise. Given the process know-how, it is usually difficult to find an automation platform that will perfectly automate that process. This is where the manufacturer can choose to automate part of the process that he/she believes is more repetitive and can be automated easily. For each of the well-known process, we have provided the key steps that are most valuable and practical to automate with quick ROI,
Thermoset
Resin Infusion process: Cutting and placing fiber using AFP-XS Dry preform: resin infusion
Out of Autoclave Curing process: Create prepreg layup of the desired shape
Thermoplastic
Preform: Create thermoplastic tape preform for the thermoforming process
Thermoplastic welding: Adding reinforcement to thermoplastic parts made by injection molding, 3D printing
Reinforcement
Natural fiber
Glass fibers
Carbon Fibers
Hybrid: Mix of the fiber
Opportunity to Build a sustainable and safe future
Given the information above between what the common view is and what is possible, there seems to be a big divide. The goal of this article is to increase awareness about the possible alternatives and make composite manufacturing one of the fastest growing industries of today. The above practices not only will grow business, but inherently provide a safe and sustainable ecosystem for the employee to work and use more nature-friendly products.
댓글