Hybrid manufacturing cells: Complete digitization of production
- Pravin Luthada
- Oct 17, 2019
- 4 min read
Updated: Jan 8, 2021
What is a hybrid manufacturing cell?
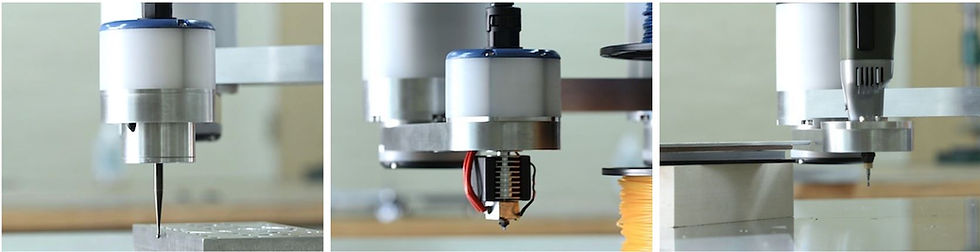
A hybrid manufacturing cell is a single cell that is scalable and contains extensible multi-process manufacturing platforms. These cells provide integrated solutions needed to go from CAD to final finished part, assembly, or product; all in a single process without human interaction.
Key Characteristics
Hybrid
Similar to how hybrid vehicles use a combination of gas and electricity to generate the full amount of energy to drive, a hybrid manufacturing cell combines many different processes to create the final product all in one cell. These different processes are all based on robotics and contain multiple end-effectors offering different functionalities. The end-effectors mount onto a single motion platform to perform their tasks, such as EOA tooling for additive manufacturing, machining, gluing, welding, fiber placement, etc. The multiple processes that happen all in the same location decrease waste in the form of time and material savings.
Scalable
Since these hybrid manufacturing cells have the core ingredient of robotics, it is relatively simple to implement an identical cell to double the production, and so on, as demand increases. When implementing more production capabilities, the workflow can be optimized, lowering the production cost and achieving economies of scale through Network Driven Scaling.
Flexible
The modularity of each tool can enable ultimate freedom for manufacturing sequencing. Providing an agile system capable of coping with rapid changes in market demand by simply changing out the plug & play end-effectors gives manufacturers the ability to change just as quickly as the market does.
Extensible
As the available variety of motion platforms is growing, the size of the manufactured parts becomes only an indicator on which motion platform you need to support production. Can the angles be reached with a stationary robotic arm, or does it need tracks to access each end? Does there need to be multiple robots on the track to meet production rates? Only you have those answers based upon your business model and vision.

Advantage of a hybrid manufacturing cell
Waste elimination
The main cost savings in production comes from the elimination, or even slight reduction, of waste. The main waste in traditional manufacturing centers is time and material. When parts are not being fabricated or being fabricated inefficiently, it is wasting time and money. Time waste comes in many different forms: setting up each different manufacturing station, time to transfer the part between stations for different processes, and even time performing manual labor when automation could make more sense.
Traditional manufacturing is not only inefficient with time but also material. With the advent of FDM, or 3D printing, metallic parts can be printed "near net shape", or even in the final form, thus reducing the amount of material needed to create the part.
Processing speed
While conventional manufacturing processes, such as CNC machining, are very fast at their specific operation, multiple operations combined in a single cell bring the overall processing time down and increase cost savings.
Material flexibility
The currently available end-effectors offer a wide range of material deposition. You can build parts with only polymer, fiber-reinforced polymer, and metal; or any combination of those materials.
Optimized structure
Freedom of choosing the right material, and it's placement in the structure, allow designers to take full advantage of generative design and FEA capability, optimizing the part design for the task it will perform.
Game changer: Additive Manufacturing (AM)
Complete end-to-end automation is possible today due to the emergence of AM. As many conventional processes required tooling before anything can be produced, AM with its capability to generate objects ground up with no additional input is the game-changer. Fusing this ability with the right end-effectors in a hybrid production cell provides new production cell possibilities. Few of these possibilities for fiber-reinforced plastics (composites) are presented below,

AM with Automated Fiber Placement (Thermosetting)
In order to start laying a fiber-reinforced composites part, it requires a negative shape mold. Conventionally it has been made out of machined wood, foam, metals, etc. AM tooling from Stratasys has already demonstrated the capability for producing thermoset composite parts. A cell with FDM extruder and plug-n-play AFP would enable fast and digitized production of composite’s most labor-intensive parts. There have been trails in this regard in the Digital Manufacturing and Design Centre, Singapore.
AM with Automated Fiber Placement (Thermoplastic)
Thermoplastic fiber placement has been the dream that is always "the big thing next year". However, with thermoplastic AM gaining traction in industrial application, thermoplastic composite production is back in the limelight. Thermoplastic AM parts, produced via FDM, have been lacking inter-layer bonding strength, so they have been missing out on many industrial applications. Thermoplastics composites, on the other hand, are excellent at providing the much-needed strength with great bonding capabilities.

A hybrid manufacturing cell, where an FDM extruder provides the thermoplastic AM shape and AFP machine actually bonds the thermoplastic fibers to the shape and provides the much-needed strength in the critical areas. This hybrid cell would have the ability to produce near-net products with complete digitization.
Digitization of production — changing the way products are realized…
We at Addcomposites believe in the vision of accessible digitization of production. We believe our plug-n-play AFP-XS solution is optimal for hybrid cells, be it for thermosets or thermoplastics composite production. Check out the trailer of our plug-n-play solution here!
Comments