Introduction to Composite Materials and Processes: Unique Materials that Require Unique Processes
- Pravin Luthada
- Apr 17, 2023
- 4 min read
Introduction
Composite materials have emerged as a game-changing solution in various industries due to their unique properties, such as high strength-to-weight ratios and anisotropic behavior. This has led to increasing popularity and adoption of composites in aerospace, automotive, marine, and sports equipment industries, among others.
Basics
Laminates
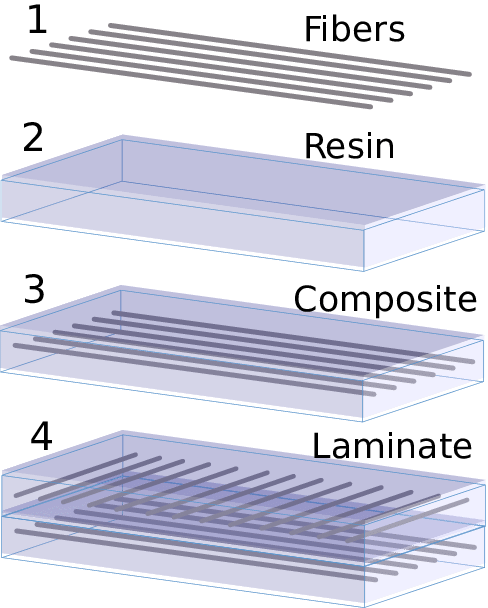
laminates are continuous-fiber composites in which the individual layers, plies or laminae are oriented in directions that enhance the strength in the primary load direction. In other words, laminates are made up of multiple layers of fibers that are oriented in a specific way to optimize their strength and stiffness.
Unidirectional (0°) laminates are extremely strong and stiff in the 0° direction; however, they are also very weak in the 90° direction because the load must be carried by the much weaker polymeric matrix. While a high-strength fiber can have a tensile strength of 500 ksi or more, a typical polymeric matrix normally has a tensile strength of only 5-10 ksi.
The Crucial Role of Fibers in Composite Materials: Balancing Strength, Stiffness, and Durability
The primary function of fibers in composite materials is to provide strength and stiffness. Typically, fibers are composed of high-strength materials like carbon, glass, or aramid, and are embedded within a polymeric matrix material. In a composite, fibers bear most of the load due to their exceptional strength and stiffness, while the polymeric matrix serves to bind the fibers together and facilitate load transfer between them.

It is crucial to recognize that, in general, high-strength fibers exhibit brittle characteristics and display linear stress-strain behavior. Consequently, they may be susceptible to failure under specific conditions, such as impact or fatigue loading. To ensure composite components fulfill performance requirements while minimizing weight and cost, designers need to meticulously evaluate factors such as fiber orientation and matrix material selection. By doing so, they can strike an optimal balance between the material's strength, stiffness, and durability.
The Essential Functions of Matrix Materials in Composites: Protection, Load Transfer, and Temperature Resistance
The matrix in composite materials fulfills several critical roles.

First and foremost, the matrix maintains the fibers' proper positioning and safeguards them from abrasion. Without a matrix material, fibers would be vulnerable to damage and incapable of effectively transferring loads among themselves.
Secondly, the matrix enables load transfer between the fibers and supports them under compression. While fibers exhibit strength in tension, they are relatively weaker in compression. The matrix material plays a crucial role in evenly distributing compressive loads across all fibers in the composite material.
Lastly, the matrix typically dictates the maximum temperature at which the composite can be utilized. The glass transition temperature (Tg) is a significant property of the matrix, representing the temperature at which the matrix transitions from a rigid, glass-like state to a softer, more rubber-like material. A matrix should not be employed beyond its glass transition temperature unless the intended service life is exceptionally brief.
By understanding these essential functions of matrix materials in composites, designers and engineers can better optimize composite structures for their intended applications.
Unique Materials and Processes
The unique properties of composite materials, such as their high strength-to-weight ratios and anisotropic behavior, have a significant impact on the design and engineering of composite components. Unlike traditional isotropic materials, composites can be tailored to meet specific performance requirements by strategically placing and orienting the fibers within the matrix.

Manufacturing processes for composites vary greatly, with each process offering different advantages and limitations. Some common methods include hand lay-up, vacuum bagging, resin infusion, and automated processes like automated fiber placement (AFP) and automated tape laying (ATL). These processes can significantly impact the final properties of composite components, such as their strength, stiffness, and durability.
Advantages of Composite Materials

The use of composite materials in various industries can lead to improved performance, reduced weight, and increased fuel efficiency. For example, in aerospace, composites have allowed for lighter aircraft structures, which translates to lower fuel consumption and reduced emissions. In the automotive industry, composites can contribute to improved crashworthiness and vehicle performance. Additionally, composites can provide corrosion resistance and durability in marine applications, while offering lightweight and high-performance solutions in sports equipment.
Challenges Associated with Composite Manufacturing
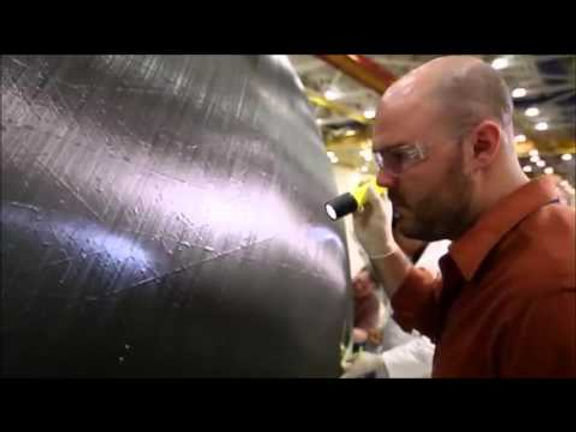
Manufacturing composites comes with its own set of challenges, including delaminations, quality control, and specialized tooling and equipment requirements. To mitigate these challenges, careful design and planning, stringent quality control measures, and proper training and education for operators are crucial.
Delaminations, a common issue in composite manufacturing, can be minimized through optimized lay-up techniques, proper surface preparation, and the use of high-quality materials. Implementing quality control measures, such as non-destructive testing (NDT) techniques, can help identify defects and ensure the reliability of composite components. Additionally, investing in specialized tooling and equipment, as well as continuous training and education for operators, is essential to achieve high-quality composite products.
Conclusion
Understanding the unique properties of composite materials and the processes required to manufacture them is critical for the successful design and engineering of composite components. By leveraging these unique materials and processes, industries can benefit from improved performance, reduced weight, and increased fuel efficiency. As the adoption of composite materials continues to grow, overcoming the challenges associated with their manufacturing will be crucial to unlocking their full potential in various applications.
Comments