How to Produce a Jet Engine Blade via Automated Fiber Placement (AFP)?
- Pravin Luthada
- Jun 27, 2022
- 3 min read
Updated: Jul 1, 2022
In this blog, we will explore about
What is a Jet Engine?
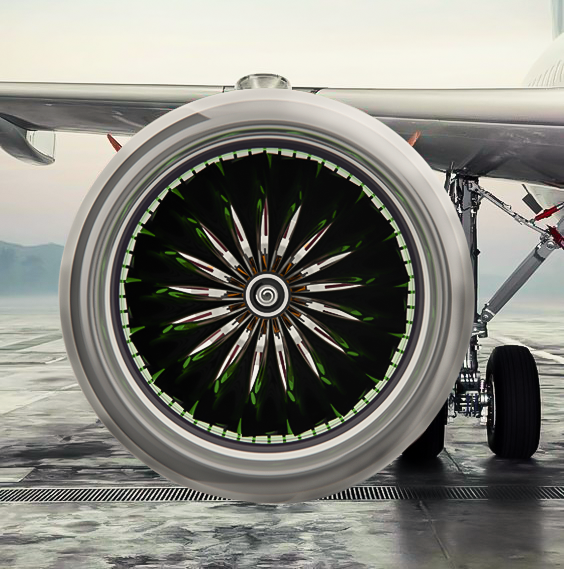
A turbofan is a type of air-breathing jet engine that is widely used in aircraft propulsion. A turbofan engine is the most modern variation of the basic gas turbine engine. As with other gas turbines, there is a core engine, but in the turbofan engine, the core engine is surrounded by a fan in the front which sucks in air, and additional turbine(s) at the rear for exhaust. Most of the air flows around the outside of the engine, making it quieter and giving more thrust at low speeds. Most of today's airliners are powered by turbofans. Such engines have many components and we will focus on the components that are made using continuous fiber composites.
Which components are made with AFP today?
A leader in the jet engines, Rolls-Royce has recently set up a facility to make fan blades and containment casings using the automated fiber placement process. They used Accudyne and Mtoress AFP systems to make the fan blades and containment casing respectively.

UltraFan, which the company says will be the world’s largest aero-engine and will contribute to sustainable air travel, features what will be the world’s largest fan rotor blades made from carbon fiber-reinforced polymer (CFRP). Here is a video showing glimpses of the overall manufacturing process from Bristol 24/7.
How to program the blade layup via AFP?
In order to produce a known geometry using AFP, a few sequential steps must be followed:
Mold model
Planning and programming with AFP
Running AFP manufacturing simulation
Mold modeling
A demo blade model can be downloaded from publicly available databases or your own CAD model of the blade can be used as well. In order to make the fan blade mold, the following steps should be followed:

Remove any holes from the fan blade surface
Extend the edges of the surface by up to 50-100 mm, up to 150mm if possible
Plan for the trimming allowance and draw an outer boundary
Sperate the layup and the boundary area by splitting the surface
Solidify the surface with vertical walls
Add mounting and alignment points for placement in AFP robotic cell
Consider markings or orientation points for fiber orientation definition
Planning and Programming with AFP
Planning the layup on a 3D mold shape has been made very simple and accessible thanks to AddPath. A step-by-step process of planning via AddPath is depicted in the picture below. The process also allows user to define their own paths by simply drawing a curve in the chosen CAD modeling software and importing it.

Running AFP manufacturing simulation
Simulating the process via 3D Programming Software - AddPath is very critical to make sure the following items are being met without error:
Mold is positioned correctly
The robot can reach the entire layup area without overextending or reaching a point of singularity
Motion sync between robot and mold is smooth and without error
No collisions are occurring
Fiber is being placed where you designed them to be among others...
AddPath allows for modification of mold position to optimize the planned layup placement, thus enabling the part to be optimally designed. Below is the video showcasing the simulation in the finalized position.
Setup your own production facility
Setting up your facility for such production used to be very difficult as it would cost millions of dollars and would require the hiring of experts. With the advent of open-access software like AddPath, everyone interested in digitally producing composites can join the movement. This virtual production environment provides very critical data for the end-user i.e. material, time, steering/gaps, overlap, feasibility, BOM cost, etc. You can download the 3D Composites Manufacturing Software - AddPath with the instruction here.
As a user feels confident in their business case, they can lease the AFP systems to run onto any available robotic arms (e.g., KUKA, ABB, Fanuc). The lease prices are equivalent to hiring a skilled technician.
For more information and knowledge about composites manufacturing, you can find it on the “Blogs” page. If you have further questions, please contact us directly and we are happy to support you.
If you have any trouble or further questions on getting started with AFP, feel free to reach out.
About Addcomposites
Addcomposites is the provider of the Automated Fiber Placement (AFP) ecosystem - including the Fiber Placement System (AFP-XS), 3D Simulation and Programming Software (AddPath), and Robotic Cells (AddCell). With the leasing program for the AFP system (AFPnext), composites manufacturers can work with thermosets, thermoplastics, dry fiber placement, or in combination with 3D Printers on a monthly basis.
Subscribe to our newsletter and get our guidebook - "Composites Manufacturing Methods: An Ultimate Guide for 2022"
Comments