Will COVID-19 accelerate automated manufacturing of advanced composites?
- Pravin Luthada
- Jun 8, 2020
- 3 min read
Updated: Jan 8, 2021
Advanced composites industry
Demand for composites is growing as manufacturers seek to make products lighter, stronger, and more durable. The global market is predicted to be worth $105.8 billion in 2020 and growing at 6.5% per year. Given the current scenario of labor-intensive techniques, manufacturers can no longer meet the market demand. Meeting this demand means radically re-thinking how composites are manufactured!
COVID-19 has accelerated the need for automation technologies that prevent transmission of the virus
Labor-intensive composites manufacturing has now become even more challenging to perform
Now is the time for small composites manufacturers to venture into manufacturing automation with rental systems
Impact of coronavirus on manufacturing facilities

Locked facilities
Lower production following social distancing
Increased awareness of worker safety
Disrupted supply chain
COVID-19: Accelerants for composites manufacturing automation
Prior to the advent of COVID-19, manufacturing suffered from tight labor markets and eyed robotics and automation to bolster efficiency and reduce costs. According to the MHI report on the supply chain in 2020, the adoption rate for robotics and automation increased more than any other supply chain technology between 2019 and 2020. Adoption clocked in at 32% and 39% adoption, respectively.
Even with COVID-19 and its associated budget constraints in many sectors, the industry continues to view robotics as a key long-term investment. According to an IDC 2020 supply chain survey, 73% of respondents say that robotics will be important or very important to their organization in the next three years.
In our personal interactions with both the industrial and R&D sectors, we are witnessing a shift in the perspective of the industry towards automated composites part production. With the advent of new composites additive manufacturing, now every manufacturer can witness the power of composite materials.
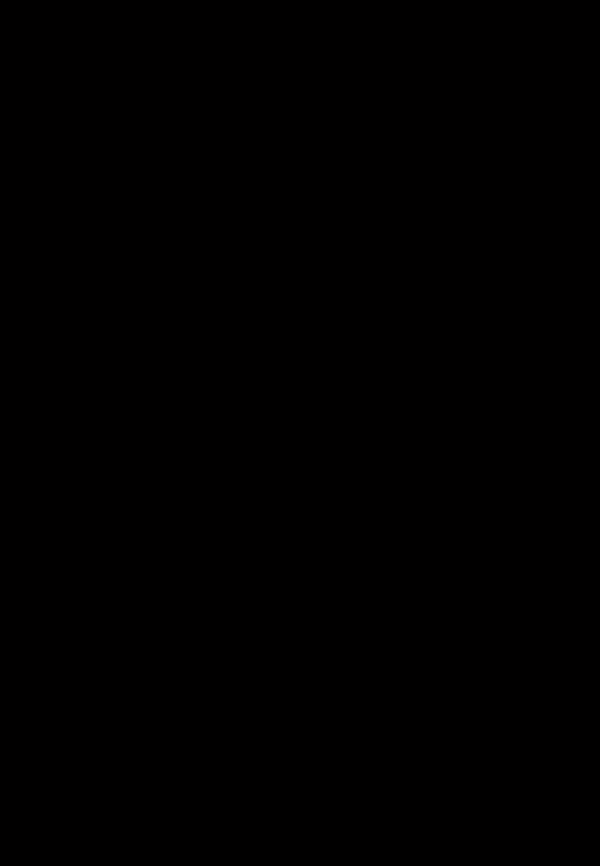
Increased digitization in production planning
Increased governmental spending
Extensive use of digital production tools
An increasing market in Composites additive manufacturing
Planning your move to automation
With the growing demand for manufacturing operations and safe working environments, now is the right time to start planning for your R&D activities, including production pilots to determine feasibility of automation for your specific project. Below, we have explained some key steps in the approach to help you initiate such operations; with low capital investment and maximum gain.
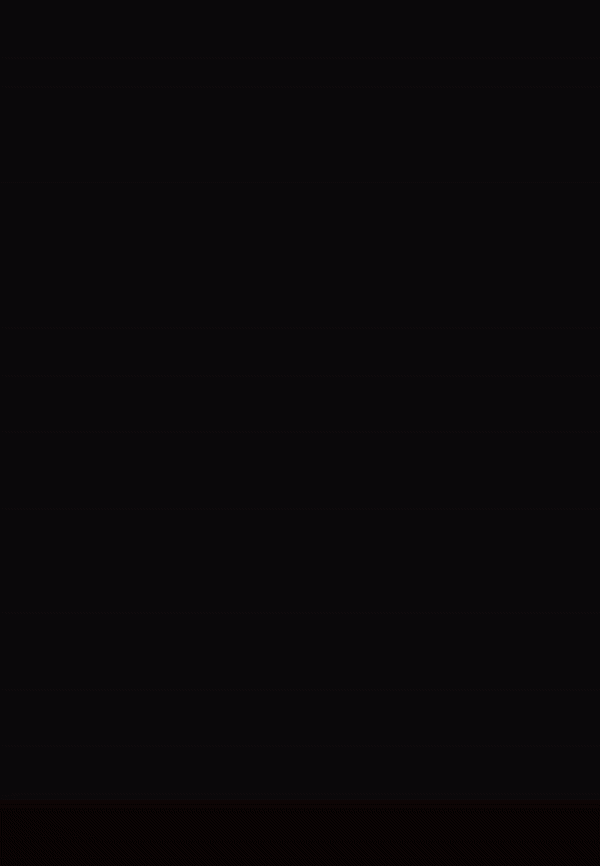
1. Start with digital tools
Start with an accessible design and planning software. Take one of the products that you think will be easy to automate and run a simulation to see if the required part quality can be achieved. Do not think of the manufacturing cost at this point, but a back of the envelop calculation doesn't hurt. Ask for your free planning and simulation software at addpath@addcomposites.com.
2. Plan and apply for support where you can
As this is the first trial, you might be needing some initial finances to support the work. If not, you can skip this step. There are many government-funded opportunities to support your technology advancement, We at Addcomposites collaborate with a lot of R&D centers and SMEs, and certainly would be able to help you identify few opportunities with such grants.
3. Utilize the piloting opportunity with partners
If you do not want to start production on your own, you might want to find such facilities that can help you make your first automated part production a reality. We at Addcomposites, along with R&D centers, can certainly help you identify few opportunities with such pilots near you and get the project started.
4. Start with a rental
Sometimes it is really difficult to find ideal facilities to run the production of your parts. A tool rental that are mounted onto exiting robots is a good option, as this provides:
Complete freedom to experiment
Explore new approaches
Overall less cost than hiring a manufacturing firm
5. Buying your first automated solution
Choosing the first automated system, you really want to evaluate the suitability of such a production system for your production needs. The key factors to consider
Capital cost and ROI: Does it require millions to invest
Flexibility: Can the manufacturing system adopt to different parts
Human resources requirement(s): How simple is it to operate?
Utilization: Upcoming projects, pilots, small series production?
Scalability: Can you add more of the same system to scale the production
Comments