Additive Manufacturing 2.0: Metal and Continuous fiber
- Pravin Luthada
- Sep 28, 2020
- 3 min read
Updated: Jan 8, 2021
Additive Manufacturing
Additive manufacturing adds material to create an object. It uses data from a computer-aided-design (CAD) software to direct hardware to deposit material, layer upon layer, in precise geometric shapes
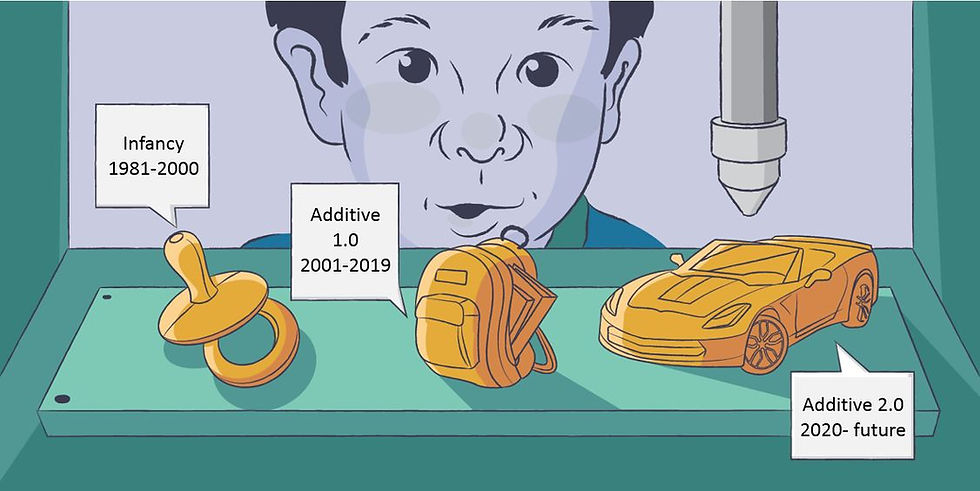
Additive Manufacturing 1.0
Starting in the early 1980s and development of the first “three-dimensional printing” technologies — SLA and FDM (FFF) — and the entrance of “rapid prototyping” into more vocabularies. Rapid prototyping is tightly interwoven into this part of the history of the technology that many long-time industry participants still refer to “RP” instead of “3D printing” (much less “additive manufacturing”).
Until 2016, additive manufacturing using FDM & SLS remained the primary form of the 3D printer (less of additive manufacturing) and have been mainly used for rapid prototyping and lower throughput applications. This complete era of FDM/SLS based 3D printing can be referred to as Additive Manufacturing 1.0.
Growth and inflection
The additive manufacturing industry grew at a 20% annual compound rate between 2006 and 2016 before accelerating to 25% compound annual growth over the last three years - a rate that is expected to continue over the next decade as the market surges from $12 billion in 2019 to an estimated $146 billion in 2030.
Additive Manufacturing 2.0
In 2020, the market has reached an inflection point, shifting the applications from simple design prototyping and tooling to mass production of final components. This shift is enabled by the emergence of what is referred to as "Additive Manufacturing 2.0" - a wave of next-generation additive manufacturing technologies that unlock throughput, repeatability, and competitive part costs.
The key additive manufacturing technologies that are enabling the shift are
Desktop metal printers (Desktop metal, Markforged metal x)
Continuous fiber placement/printing (Addcomposites, 9Tlabs, CEAD, AREVO, Continuous composites)
These solutions are key innovations across hardware, materials, and software and pull additive manufacturing into direct competition with conventional processes used to manufacture $12 trillion in goods annually.
A new wave of investment
Recently, investors have also realized that additive manufacturing is at an inflection point, now to be acknowledged as a separate industry in itself. Following recent investments in the industry, the graphic below is a clear indication of that!
Desktop metal - $275,000,000 (SPAC-deal) / IPO
Mark forged - $82m Series D
AREVO - $25m in Series B
Role of Continuous Fiber Placement in Additive Manufacturing 2.0
Continuous fiber placement also dates back to the 1980s when the first AFP machines were developed for the aerospace industry. Since this technology was confined to a specific sector for so long, other industries haven't even considered implementing this form of technology. From the inception itself, the continuous fiber placement systems were good for producing aerospace-grade parts however, the high capital cost of this equipment and high cost of raw materials limited its industrial application.
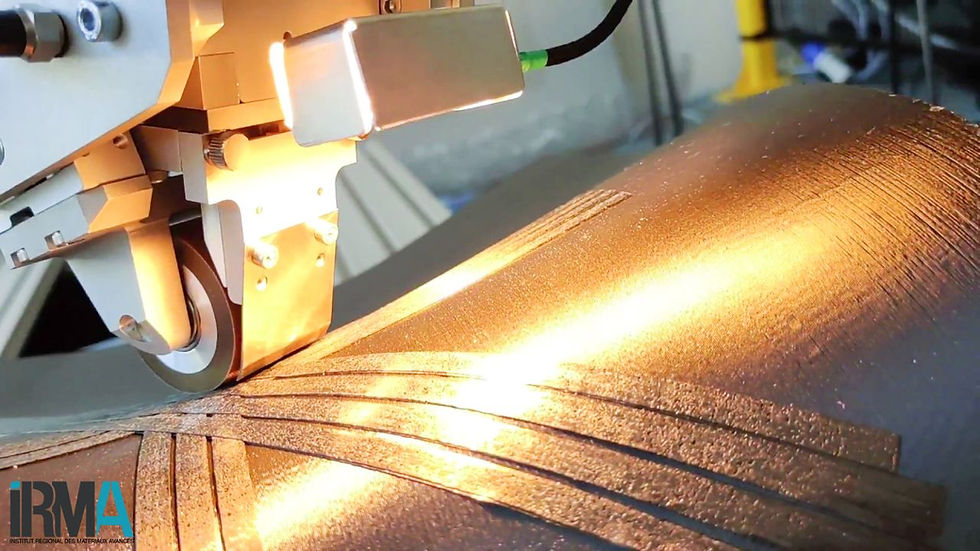
In the era of Additive Manufacturing 2.0, fiber placement systems themselves have become 100 times more accessible. The material has also reduced in price, as more and more companies invest in manufacturing efficiency, enabling aerospace-grade technology to become available to other industries. This has enabled the prices of final components into direct competition with conventional composites shops. The digitized process has its benefits with consistent quality, a safer work environment, and optimal material usage. This benefits the supply chain in both ways i.e. while it is capable of producing light and strong products for the users, at the same time manufacturers save on labor cost and waste reduction.
Comments