Things to Consider in Additive Manufacturing using Continuous Fiber - Placement or Printing?
- Pravin Luthada
- May 31, 2022
- 4 min read
Updated: Jul 13, 2022
Ever since continuous fiber 3D printers burst onto the scene in 2014, engineers around the world have sought a system that could 3D print large-scale continuous fiber-reinforced parts.

The ability to purely additively produce complex parts with high strength and low weight, without expensive layup tools or autoclaves, was increasingly sought after. This has created a niche of opportunity for new innovations among the machine tool building startups, who are challenging the status quo and aiming for the multi-billion euro rapid large-scale thermoplastic composites market.
Reality
Many in the 3D printing industry will argue that large-scale continuous fiber 3D printing already exists in the form of continuous fiber extruders. For example, fused filament fabrication (FFF) 3D printers have a mechanism that introduces the continuous fiber in the molten thermoplastic stream, embedding it in the printed part.
Other processes use UV-catalyzed thermoset resins, mixing their continuous fiber reinforcement with the resin right at the tool point, and initiating the snap-cure resin with UV radiation in the process.
However, any composites engineer who has worked in the Aerospace or Formula-1 industry can notice that the composites produced this way has a limitation of 2.5d motion and lacks the critical layer-to-layer bonding. These technologies are however capable of producing larger FDM style prints with less thermal distortion.
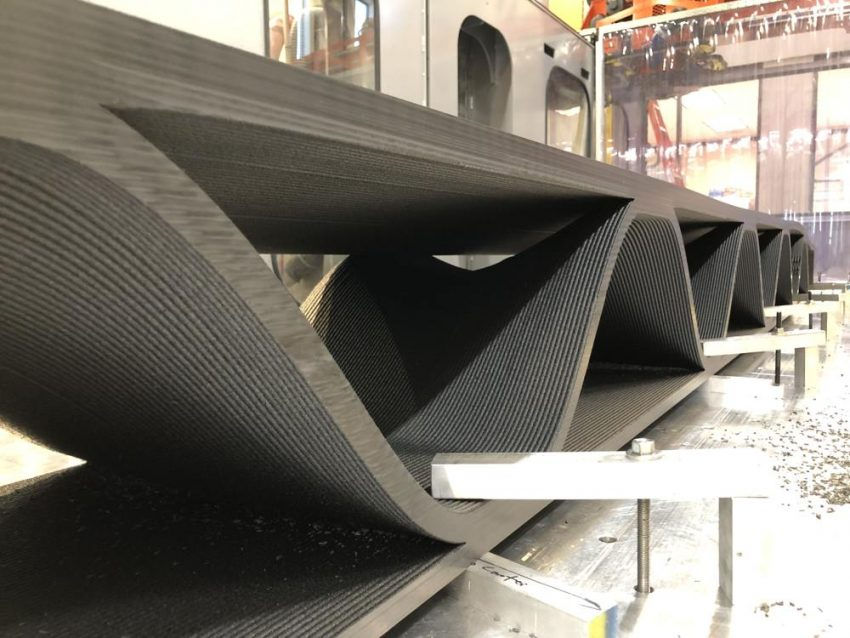
Vision
A True Continuous Fiber Placement/Printing is a platform that leverages the benefits of FDM and Placement technologies that do not require layup tools, vacuum bagging, autoclave, or other secondary processes. The platform enables agile accessible composites production, accelerating advanced composites manufacturing for all industries and manufacturers alike.
Physics-first principle approach
Any structural component's main function is to allow smooth stress flow to enable the transfer of loads and moments from one end to another. Continuous fibers are the most efficient load-carrying members, acting as smooth channels for stresses to flow, without any breakage. The matrix material joining the fibers makes sure that all the stress flows are equally distributed among these fiber channels. In order to build the most effective composites structure needs to make sure the stress flow is continuous, smooth, and well-aligned without any breakage. To achieve this you want to have:
Well distributed fiber along the stress flow direction
Optimal Fiber Volume Fraction (FVF) ratio
No porosity in the matrix
Bent fiber has zero stress flow

Attributes of solution
Use pre-impregnated tapes, that ensure distributed fiber
Compact the tapes to get the maximum number of fiber-packed
Heat & press to achieve a minimum porosity
Place fiber under tension to get them straight
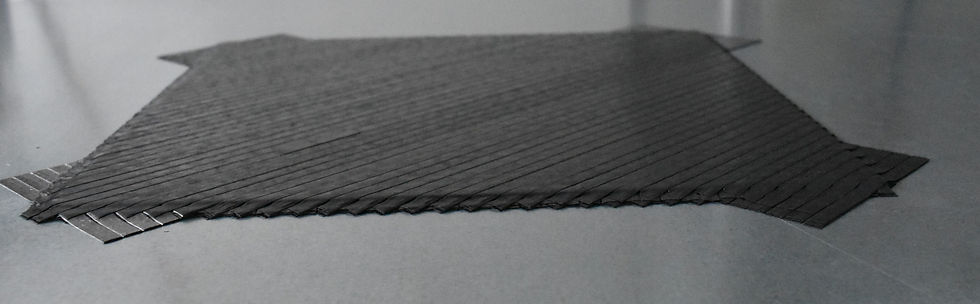
Figure 4. Example of a laminate produced by the Single-tow Fiber Placement System
The above solution results in a compact AFP solution. Now to address the other aspect of True Continuous Fiber Placement, it has to create shape without a given mold and should not require post-processing
No mold: Print a mold/substrate shape with FFF type printing.
No Autoclave: Use thermoplastic in-situ consolidation
Solution
A 6D motion platform capable of mounting AFP and FFF head interchangeably, creating a True Continuous Fiber Placement/Printing solution.
Building the solution
In order to build the most capital-efficient true continuous fiber placement and printing solution, you need to identify:
1. 6D Motion platform of choice (KUKA, ABB, FANUC, etc.)
There are many different brands of industrial robots to choose from, and they are all becoming more and more accessible every day. The key benefit of these standard platforms is they are available worldwide and are highly scalable.
2. Thermoplastic reinforced fiber placement head
Addcomposites provides thermoplastic-compatible fiber placement tool heads that can be integrated into the latest robotic platform. One-day installations are possible and available for select robotic platforms.

Figure 5. Example of a 3D laminate produced by the Single-tow Automated Fiber Placement (AFP)
3. FDM extruder
With the open-source movement in this area, pallet extruders are available from many suppliers around the world, so finding one that suits your needs is easy and affordable.
Addcomposites has the answer
Integrating all the solutions is also a big challenge, as each system has its own safety and communication protocols that need to be met. At Addcomposites, we have experts at your disposal to focus on your problems at hand. Besides that, the opening access to AFP programming and simulation software (AddPath) will enable everybody to plan using all these systems together, and our automation expert can be contacted to help connect all these systems for seamless communication on their personal or work computers, enabling digital composites additive manufacturing from home or the office based on the cloud-based license.
Video 1. Turbofan Blade Case Study Simulated on AddPath
About Addcomposites
Addcomposites is the provider of the Automated Fiber Placement (AFP) ecosystem - including the Fiber Placement System (AFP-XS), 3D Simulation and Programming Software (AddPath), and Robotic Cells (AddCell). With the leasing program for the AFP system (AFPnext), composites manufacturers can work with thermosets, thermoplastics, dry fiber placement, or in combination with 3D Printers on a monthly basis.
Sources
Subscribe to the newsletter and get our guidebook - "Composites Manufacturing Methods: An Ultimate Guide for 2022"
Comments