Advanced composites manufacturing: research opportunities
- Pravin Luthada
- Aug 27, 2020
- 4 min read
Updated: Jan 8, 2021
The marvel of FRP composites
Advanced fiber-reinforced polymer composites, which combine strong fibers with tough plastics, are lighter and stronger than steel. While advanced composites are currently used for select purposes, such as aircraft, military vehicles, satellites, and luxury cars, it comes at a high cost. At a lower cost, these materials could help manufacturers deliver more advanced and more affordable products such as:
Lightweight vehicles with record-breaking fuel economy
Lighter and longer wind turbine blades
High-pressure tanks for natural gas-fueled cars
Lightweighting is directly tied to energy efficiency. With just a 10 percent weight reduction, fuel efficiency rises by 6-8 percent for internal combustion engine vehicles. For battery-electric vehicles, that 10 percent weight reduction increases vehicular range by 10 percent.
In automotive applications, advanced composites could reduce the weight of a passenger car by 50 percent and improve its fuel efficiency by about 35 percent without compromising performance or safety – helping to save families thousands of dollars in fuel costs over the car’s lifetime.
In the wind energy industry, advances in low-cost composite materials will help manufacturers build longer, lighter, and stronger blades to create more energy. In fact, doubling the length of a turbine blade can quadruple the amount of electricity generated.
Key supply chain aspects: Manufacturing FRP composites
FRP composite manufacturing can be an energy-intensive process with high heat
and pressure needed to bond the composite material together. In addition, carbon
fiber precursors and the raw materials that make up the polymer resin are typically made via conventional energy-intensive petrochemical processes.
Fiber Fabrication
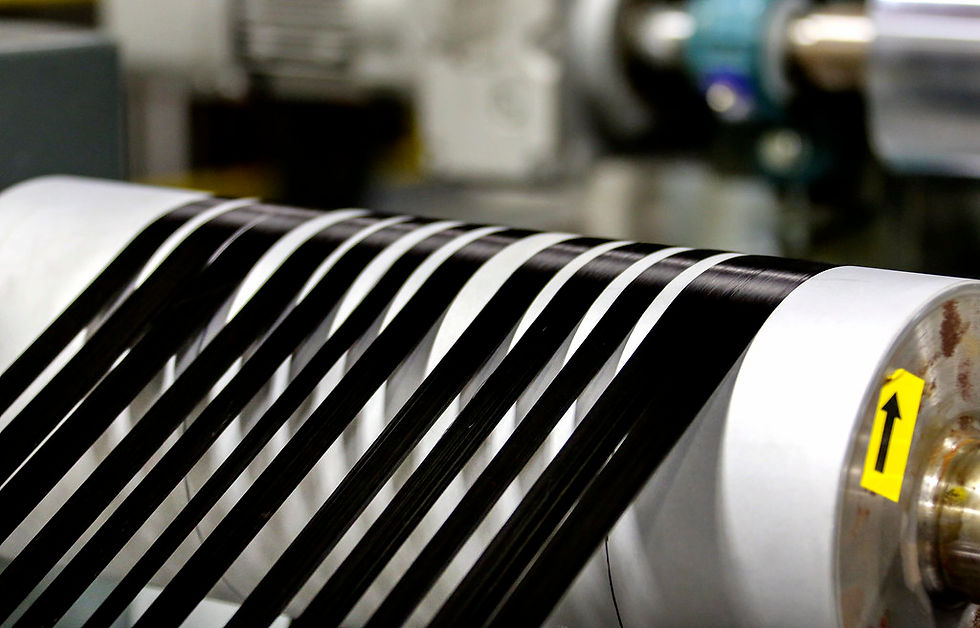
High temperatures are required in the manufacture of both carbon and glass fibers. Carbon fiber can be made from petroleum raw materials that are spun into ‘white fiber’, a carbon fiber precursor processed in a series of high-temperature ovens (to oxidize and carbonize the fiber), and then wound onto spools as ‘black fiber.’ Glass fiber is made by melting silica in a high-temperature furnace and spinning the resulting thermal-resistant borosilicate onto spools. The fibers can be woven into a fabric or formed into a tape, depending upon specifications for the component to be manufactured. In some cases, the long fibers are arranged in one direction or the fibers are chopped short and set in multiple directions.
Component Production
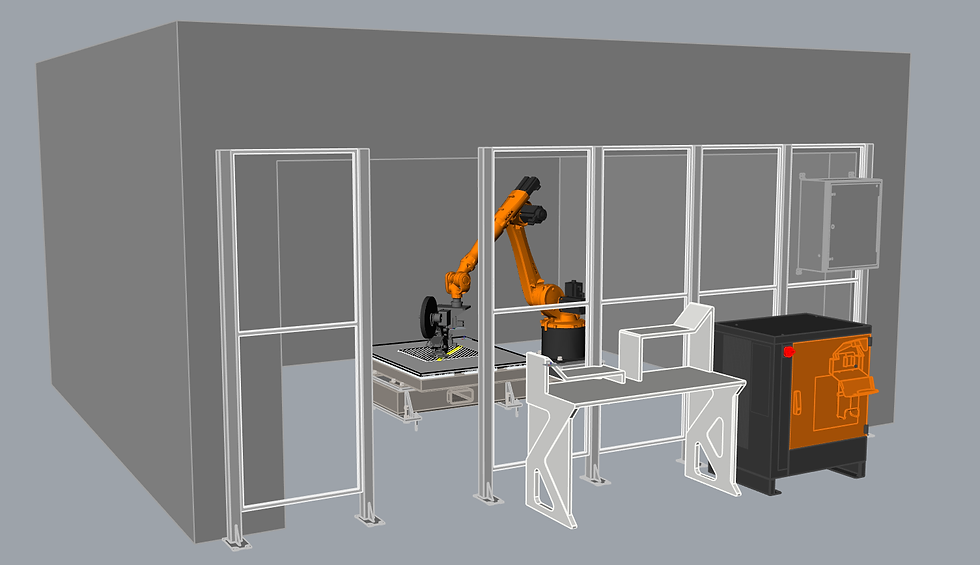
There are many different ways to make composite parts. Typically, the strong, stiff, reinforcing fibers are combined with the polymer either before or during part fabrication. These parts are made by layering the composite material over a mold in the final shape of a part (much like the layering of plywood) and then heated under pressure. For some parts with more angles and complex shapes, fiber and resin may be placed together in the cavity of a mold, which is then compressed and heated. For pipes and other long parts, fiber and resin may be extruded through a die and then cured at high temperatures.
Key application areas
Improved fabrication processes could lower the cost and energy intensity of FRP composites, potentially opening a wide range of applications that promote clean energy and energy efficiency.
Motor Vehicles

Lightweighting is a key strategy to increase transportation energy efficiency and fuel economy while continuing to meet safety standards. A 10% reduction in vehicle weight can improve fuel economy by 6–8% or increase the range of a battery-powered vehicle by up to 10%. Compared to conventional steel, glass FRP composite systems can reduce mass by 25−30%, while carbon composite systems can reduce mass by 60–70%.
Wind Turbines
Rigid, high-strength, and lightweight yet fatigue-resistant carbon FRP (CFRP) composites can enable the lighter, longer turbine blades that are needed to increase the generation of wind power. The wind sector was the third largest consumer by weight of CFRP in 2018, with 13% of the worlds carbon destined for wind turbines. This market is expected to grow drastically in the next couple of years, becoming the second largest market for CFRP by 2025, unsurprisingly behind only aerospace and defense.
Compressed Gas Storage Tanks
Lightweight, high-strength materials are needed to make the storage tanks for vehicles that run on hydrogen and natural gas. Although carbon FRP composites meet the target performance criteria for on-vehicle storage, the costs associated with manufacturing them remain too high.

Industrial Equipment
Composites can impart corrosion resistance and other properties that improve the performance of industrial equipment and components. For example, FRP composites could enable:
More efficient heat exchangers
Fans and blowers
Other equipment capable of withstanding corrosive or high-temperature processes and environments
Pipes and tanks with extended service life
Better electrical insulation for machinery.
Other industries could benefit by substituting low-cost high-performance FRP composites for existing materials. Examples include structural materials for buildings, roads, and bridges; marine vessels; flywheels for electricity storage; and electrical transmission lines.
Research Opportunity
To achieve a more diverse range of applications, research will need to overcome some key challenges associated with advanced FRP composite materials and their manufacturing methods.
Energy Intensity
Carbon fiber demand in industrial and energy applications is expected to grow 310% within the next 10 years. This rapid growth underscores the need to reduce the energy required to produce these carbon FRP composites, as they can be three to five times more energy-intensive to fabricate than conventional steel.
Production
Fiber and part fabrication are both complex processes. Lowering costs will require more effective and predictable manufacturing processes that reduce cycle times without diminishing performance characteristics. In addition to lowering manufacturing costs, broader use of FRP materials and structures will require more innovative design
concepts, predictive modeling, robust characterization of material properties, performance validation, and process automation.
Composites Manufacturing Simulation & Validation
Develop a comprehensive set of simulation tools that connect composites from their birth in manufacturing to their lifetime prediction.
Advance the certification of composite products by analysis validated by experiments and teach the use of these tools to the current and future generations of engineers.
Work with industry, academia, and government to put these tools in the hands of engineers.
Composites Additive Manufacturing
Predict and measure the anisotropic deformation that occurs in printed elements.
Include a description of anisotropic element shape change during deposition.
Anticipate the performance of the printed element
Recyclability
Enhancing the cost-effective recyclability of FRP composites would save a significant amount of energy—particularly if the process enables repeated recycling without loss of quality and represents a fraction of the original manufacturing energy use and emissions. Advanced recycling capabilities could greatly improve the life-cycle energy footprint of these composites and help meet the rising recycling goals of many industries.
References
The information above was gathered from
Comments