How to advance composite manufacturing with Machine Learning, Computer Vision, and Digital Twin?
- Pravin Luthada
- Feb 16, 2022
- 3 min read
Updated: Apr 4, 2022
Table of Content
This article explores possible composite manufacturing advances using newfound technologies such as machine learning, computer vision, and digital twin.
The key idea here is to understand the benefits and roadblocks of each of the technologies from a composite manufacturing SME’s perspective, and provide some food for thought for future roadmaps!
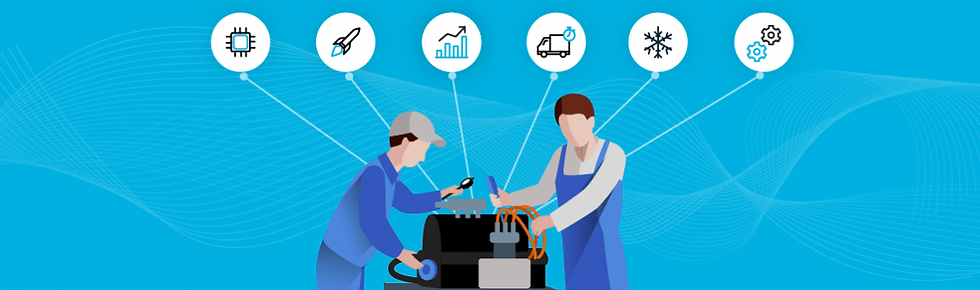
The focal elements of composite manufacturing are engineering design, quality, and process optimization.
Design and Structural Simulation - Combining knowledge from composite design engineers and manufacturers at no cost
What if we can input the constraints, the loads, and manufacturing technique as input, and let the Machine Learning BlackBox design the part as a structural designer?
The entire design running through numerous neurons in a few seconds produces a design with the best manufacturability and structure without input from human structural designers.
The ML experiments in the area of structural simulation are accurately trying to achieve this by creating a self-learning finite element method and engineering applications.
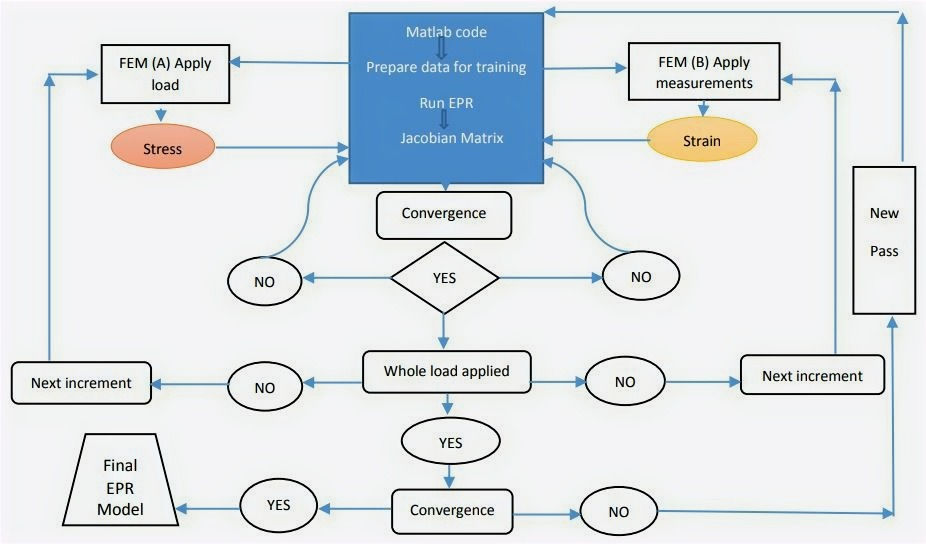
80–90% of engineering schools do not provide composite design courses, let alone the new advancements in the analysis.
ML tool has the possibility to learn from the knowledge of existing engineers and FEA software to generalize the learning and create a tool that can be used by SMEs to exploit the benefit of advanced composites design at a very low cost.
This would solve the present scenarios for SME manufacturers:
Can not hire or find engineers with relevant design engineering know-how.
Available FEA software capable of handling composites is too expensive, as they are built on the legacy of traditional FEA or provide very partial composite simulation capability.
Automated Layup Inspection: Low-cost identification of defects
Automated inspection used to be one of the distant dreams for the SME composite manufacturer, due to the high cost associated with the system.
However, with advances in hardware and software, images taken from a low-cost camera can be analyzed over the cloud to provide rapid feedback for in-situ defect detection and failure prevention.
Digital Twin: Planning and resource optimization at the shop floor

Creating a digital twin on a manufacturing floor for a composite manufacturer is quite challenging, as the majority of the processes are not yet automated, and gathering data from each source is a very labor-intensive task.
Automation of a process with the right sensor module to simulate the digital environment can bring a lot of benefits to SMEs such as:
Assess rough design concepts for producibility and predict yield coming out of operations
Make proactive changes to schedules and resource allocation
Collect data on individual processes to build libraries of data that may help improve aspects of the business
Evaluate anomalous signal data for risk identification to take preventive actions before the breakdown or defects in the product
A good example of a study titled "A digital twin for composite parts manufacturing: Effects of defects analysis based on manufacturing data" highlights how to merge incoming sensor data into the database and use this data to determine the margin of safety for the part.
Key challenges with implementation
The inherent challenge of implementing these techniques is that it requires repeatable processes and accurate data from those processes. The good part is there is an immense amount of literature on the design and simulation to build on and test models against ground reality.
Another challenge is that the industry is full of manual manufacturing processes, that include no automatic data capturing for the process. Without a good amount of data, most of the techniques discussed do not produce intended results.
Please let us know your thoughts in the comments about what technologies or challenges you envision for the future of composite manufacturing!
Addcomposites
Addcomposites is the provider of the Automated Fiber Placement (AFP) system. The AFP system can be rented on a monthly basis to work with thermosets, thermoplastic, dry fiber placement, or in combination with 3d printers.
Subscribe to our newsletter and get our guidebook - "Composites Manufacturing Methods: An Ultimate Guide for 2022"
Commentaires