AFP Machines and Components
- Pravin Luthada
- Feb 4, 2024
- 13 min read
Introduction
Welcome to our comprehensive guide on Automated Fiber Placement (AFP) Machines and Components. This blog serves as your gateway to understanding the pivotal elements that define AFP technology, a cornerstone of modern composite manufacturing. Here's a brief overview of what to expect, providing you with essential insights before diving deeper into the detailed exploration:
Anatomy of an AFP Machine: We dissect the AFP machine into its core components, offering clarity on its sophisticated mechanisms.
Key Components and Their Functions: Delve into the specifics of robotic platforms, compaction rollers, heating sources, and the innovative modular AFP heads.
Machine Setup and Material Handling: A step-by-step walkthrough on setting up an AFP machine for optimal performance, focusing on material storage, feeding, and the crucial cut, clamp, and restart mechanisms.
Calibration and Troubleshooting: Learn the art of fine-tuning your AFP machine for precision and efficiency, along with expert tips on troubleshooting common issues.
This blog is crafted for those who seek a deeper understanding of AFP technology—whether you're a seasoned professional aiming to refine your knowledge or a newcomer eager to learn the ropes. By the end of this guide, you'll be equipped with the insights necessary to navigate the complexities of AFP machines and their components.
We hope you find this exploration enlightening and that it sparks further curiosity about the evolving role of AFP in manufacturing. Let's embark on this journey together, and here's to expanding your expertise in the field of composite material production.
Jump to the right sections
Anatomy of an AFP Machine
Introduction to AFP Machine Platforms
Automated Fiber Placement (AFP) technology has evolved significantly, with advancements leading to a wide array of machine platforms designed to meet diverse manufacturing needs. This section delves into the anatomy of AFP machine platforms, highlighting the transition from gantry to robotic arm systems and the factors influencing platform selection.
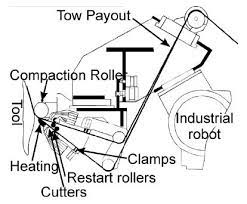
AFP Machine Platforms: From Gantry to Robotic Arms
Historically, AFP machines were predominantly based on two types of gantry systems: horizontal and vertical. These gantry systems, characterized by their six or seven axes of freedom, were once the backbone of AFP manufacturing, especially for large, plate-like structures that required less complex motions. The horizontal gantry was preferred for projects where the part had a significant height or needed rotation during the process, as its structure offered no obstruction to the tool. Conversely, vertical gantries were suitable for laying up materials from above, generally without the need for a rotating mandrel.
However, these gantry systems have become increasingly rare, primarily due to the substantial investment required for setup and their limited flexibility in adapting to more complex structures. The industry trend has shifted towards smaller, lighter, and more versatile systems, with robotic arm platforms emerging as the predominant choice. These robotic platforms, capable of supporting up to 12-axis systems, offer unparalleled flexibility, allowing for intricate movements and the ability to handle complex shapes with ease. This adaptability has facilitated the integration of additive manufacturing techniques with AFP processes, further enhancing the capabilities of these systems.

The robotic platforms' dominance is reflected in their widespread availability, with up to 97% of AFP applications now utilizing these systems. Their prevalence is due in part to the industry's familiarity with robotic systems for other manufacturing processes, such as drilling and polishing. This familiarity has made the transition to using robots for AFP more accessible and cost-effective, significantly increasing their adoption rate.
Selection Criteria for AFP Machine Platforms
Selecting the appropriate AFP machine platform involves several critical considerations, shifting away from the traditional focus on part size and gantry capabilities. The primary criteria include:
Cost: The investment required for setup and operation is a paramount consideration, with robotic arm systems offering a more cost-effective solution for a wide range of applications.
Adaptability to New Projects: The ability of the system to adapt to different shapes, sizes, and complexities of parts without significant additional investment is crucial. Robotic arm platforms excel in this area, providing flexibility to accommodate a broad spectrum of manufacturing requirements.
Material Processing Capability: While the choice between thermoset and thermoplastic materials was once a significant factor, advancements in AFP head technology have made it possible for both types of platforms to process a variety of materials effectively. Thus, this criterion has become less about the platform and more about the specific capabilities of the AFP head and the heating systems employed.
AFP Head: The Heart of the AFP Machine
Overview

The AFP head is a sophisticated assembly that performs the critical tasks of heating, applying, and compacting the fiber tows onto the tooling surface. It is the primary interface between the machine and the material, directly influencing the quality, efficiency, and versatility of the AFP process. Understanding its components and functionalities is essential for those operating in the field of composite manufacturing.
Components and Functionalities
Tow Feeding Mechanism: The AFP head is equipped with a series of spools that feed the fiber tows into the head. Precise control mechanisms ensure the tows are fed at consistent rates, critical for maintaining uniform material deposition and preventing defects.
Heater Element: Before the tows make contact with the substrate, they are heated to a specific temperature to activate the resin (for thermoset composites) or to melt the matrix (for thermoplastics). The heating element can vary (e.g., infrared, laser, hot gas) depending on the material being used and the specific application requirements.
Compaction Roller: This component applies pressure to the tows as they are laid onto the substrate, ensuring proper adhesion and consolidation while removing air voids. The roller's material, shape, and durometer are selected based on the composite material and the contour of the part being fabricated.
Cut/Clamp/Restart Mechanisms: These mechanisms control the start and end points of the tows, allowing for precise placement. The cutting mechanism trims the tow at designated stop points, while the clamping mechanism holds the tow in place for a restart without slipping or creating defects.
Control Systems: Integral to the AFP head, advanced control systems manage the coordination of the feeding, heating, and compaction processes. These systems rely on real-time feedback and adjustments to maintain optimal placement conditions, ensuring high-quality layups.
Simplified Representation for Easier Understanding

To simplify the complexity of the AFP head, imagine it as a highly specialized printer that instead of ink, uses continuous fiber tows. Just like a printer adjusts the ink flow, changes cartridges, and ensures even application on paper, the AFP head precisely controls the feed rate of the fibers, heats them to the right temperature, and applies them with consistent pressure to form a composite material layup. The cut/clamp/restart mechanisms act similar to how a printer manages paper feed, ensuring that each new line starts and ends correctly for a flawless final product.
Critical Equations and Logic
While the operation of an AFP head involves complex physics and material science principles, a fundamental understanding can be derived from the heat transfer and compaction mechanics:
Heat Transfer Equation: The amount of heat required to activate or melt the resin in the tows is determined by the specific heat capacity of the material and the desired temperature change. ΔQ=m⋅c⋅ΔT, where ΔQ is the heat energy, m is the mass of the material, c is the specific heat capacity, and ΔT is the temperature change.
Compaction Force Logic: The compaction force applied by the roller is critical for achieving proper consolidation. This force is adjusted based on the roller's material and the substrate's contour to ensure uniform pressure distribution and minimize voids. The force is often controlled by pneumatic or hydraulic systems, calibrated to apply a specific pressure P=F/A, where P is pressure, F is force, and A is the area of contact.
Key Components and Their Functions
Robotic Platforms and Degrees of Freedom
Robotic Platforms: The evolution of AFP machines has seen a significant shift towards robotic platforms due to their flexibility, precision, and ability to handle complex geometries. The choice of platform, particularly the number of degrees of freedom (DoF), profoundly impacts an AFP machine's versatility and efficiency.

Six Degrees of Freedom (6DoF): Standard robotic arms with 6DoF are adept at performing tasks on 2D and open 3D surfaces, limited by their reach while maintaining the AFP head normal to the layup surface. However, their utilization in composite layup is often constrained by these spatial limitations.
Seven Degrees of Freedom (7DoF): By introducing a seventh axis, typically through a rotary positioner for the mold or tooling, robots gain the ability to maintain the AFP head orientation more effectively across the entire mold surface. This setup excels in producing closed geometries and complex shapes without overextending the robot's position, making 7DoF systems highly recommended for enhanced flexibility and coverage.
Beyond Seven Degrees of Freedom: For long mold geometries or spherical shapes that require extensive coverage and aim to avoid robotic singularity issues, adding linear axes or additional rotational degrees can be crucial. Systems with up to 9DoF and beyond enable comprehensive coverage of complex geometries, significantly increasing the versatility and capability of AFP operations.
Compaction Rollers: Solid and Perforated
Compaction Rollers play a pivotal role in the AFP process, ensuring proper fiber tow placement and consolidation. The choice between solid and perforated rollers is dictated by the application's specific needs, material properties, and geometric complexities.

Solid Rollers: Preferred for their simplicity and effectiveness in flatter geometries, solid rollers can suffer from reduced conformability on complex shapes. Their cooling mechanisms and hardness are critical for their performance, with softer rollers providing more uniform force distribution but potentially less durability under high-temperature conditions.
Perforated Rollers: These rollers offer improved cooling efficiency and can be designed to provide more even pressure distribution across the tow. The perforations allow for better heat dissipation, extending the roller's lifespan, especially in thermoplastic applications where high temperatures are prevalent.
Heating Sources: IR, Laser, and Pulsed Light
Heating Sources are essential for activating the resin or melting the matrix in the composite material. The choice of heating technology affects material compatibility, process controllability, and temperature profiles.
Infrared (IR) Heaters: Suited primarily for thermoset composites and low-speed dry fiber placement, IR heaters offer a balanced approach for applications not requiring intense heat. They are limited in their ability to process thermoplastics efficiently due to their lower energy density.
Laser Systems: Lasers, including single-point and VCSEL (Vertical-Cavity Surface-Emitting Lasers), provide high-energy, focused heating capable of processing thermoplastic composites efficiently. While offering precise control and high-quality outcomes, the safety, cooling, and optical requirements add to the system's complexity and cost.

Pulsed Light Systems: Representing a versatile and controllable heat source, pulsed light systems can rapidly heat materials with varying control over pulse parameters. This technology allows for high-quality thermoplastic layups with relatively simple safety measures, akin to using standard welding curtains.
Modular AFP Heads: The Future of Composite Manufacturing
Modular AFP Heads have revolutionized the AFP field by offering unparalleled flexibility, ease of use, and integration capabilities. Developed by companies like Addcomposites, these heads transform any standard robot into an AFP machine, capable of handling thermoset, dry fiber, and thermoplastic materials across various widths.
Advantages: These modular systems facilitate rapid setup changes, support Industry 4.0 data capture for process optimization, and offer a plug-and-play solution that drastically reduces the barrier to entry for composite manufacturers. Their ability to function as filament winding or tape laying systems further enhances their value, providing a multi-functional platform for a wide range of composite applications.
Impact on the Industry: The introduction of modular AFP heads has significantly broadened the accessibility of advanced composite manufacturing technologies. With over 50 units already deployed globally, these systems match the versatility of traditional, more cumbersome AFP machines while offering improved efficiency, customization, and adaptability to small-scale manufacturers.
Machine Setup and Material Handling
Material Storage and Feeding
Material Storage: The correct storage of materials is paramount in ensuring the quality and usability of the fibers in the AFP process. For thermoset materials, storage typically occurs in cold environments, around -20°C, to prolong their shelf life. Thawing times vary based on the form of the material, with pan spools and bobbins requiring between 3 to 8 hours to reach a usable state. It's critical to monitor the duration materials spend out of cold storage to prevent exceeding their work life. Conversely, thermoplastic materials and dry fibers benefit from dry, dehumidified storage to minimize moisture absorption, which could affect processing and final part quality.
Feeding Mechanism: Modular AFP heads integrate a tensioning system to manage material feed from bobbins or pan spools mounted directly on the head. During setup, operators manually thread the material through rollers toward the cut, clamp, and restart (CCR) mechanism. This process may be assisted by partial activation of the feed mechanism for ease. Ensuring the material remains untwisted and tensioned is crucial to prevent defects. The AFP head's design accommodates varying materials, with specific mechanisms like cooling in the CCR area for thermosets to prevent premature sticking, a feature not required for thermoplastics or dry fibers.
Cut, Clamp, and Restart Mechanism in Material Handling
The CCR mechanism is critical for precision in tape placement, allowing for the seamless start, cut, and hold of the tape during layup. This module's design dictates the AFP system's capability to handle multiple tapes, their width, and the complexity of geometries it can produce. The intricate balance between cutting precision, clamping pressure, and feeding rate directly impacts the layup's quality, enabling the production of complex shapes without wrinkles or misalignment. The tension applied by the tensioning system plays a vital role in this balance, ensuring the tape is consistently taut, preventing any folding or twisting that could compromise the layup's integrity.
Calibration and Alignment
Calibration of the AFP Head: Calibration is a meticulous process that establishes the tool center point (TCP) of the AFP head, crucial for accurate fiber placement. Utilizing a specialized calibration tool, the process transforms the compaction roller's point into a precise representation of the TCP. Methods vary from standard 4-point XYZ calibration to more sophisticated techniques involving reference tools and geometries for enhanced precision. This calibration ensures the AFP head aligns perfectly with the programmed paths, avoiding any collisions or misplacements during operation.
Aligning the Base and External Axes: Calibration extends to the machine's base and any external axes, like rotary positioners, to ensure the entire setup's alignment matches the programmed model. Techniques involve probing known points on the base or external axis to define their positions accurately in the robot's coordinate system. This information, once integrated into the simulation software, ensures the physical setup's alignment with the virtual model, critical for accurate fiber placement.
Importance of Virtual and Physical Simulations
Virtual and physical simulations play a pivotal role in bridging the gap between theoretical models and real-world execution. These simulations validate the calibration and alignment processes, ensuring that the AFP head's movement and material placement precisely follow the designed paths. Discrepancies between the simulated environment and actual setup can lead to errors in fiber placement, affecting the final part's quality. Accurate simulations help in preempting potential issues, allowing for adjustments before full-scale production, thereby minimizing material waste and enhancing the manufacturing process's efficiency.
Calibration and Troubleshooting
Calibration and troubleshooting are critical to the optimal performance of Automated Fiber Placement (AFP) machines. This section provides a more detailed look at ensuring precise calibration and effective troubleshooting methods.
Calibrating the AFP Machine
Effective calibration of an AFP machine involves adjusting and verifying the accuracy of several key components to ensure optimal performance. Here’s a detailed guide:
Material Feed and Cut Calibration:
To calibrate the feed and cut system, run a series of tests to determine if the actual feed length matches the programmed length. Adjust the system settings if discrepancies are found. This ensures the tape starts and ends precisely at the desired points on the layup.
For the cut length calibration, perform cuts at minimum and maximum lengths, measuring the outcome. Adjust the blade or control settings to match the expected lengths, critical for accurate tape placement and overlap.
Tension Calibration:
Calibration of the tensioning system is essential for accurate placement. Incorrect tension can lead to tape folding or similar errors. Calibrate the tension force to ensure not over tensioning or lose placement.
Sensor Calibration:
Material runout sensors ensure the machine stops before the material fully depletes, preventing dry runs. Calibrate these sensors for different spool sizes or material types to accurately detect material presence.
Temperature sensors require calibration to ensure the heat applied to the material is within the optimal range for bonding without degrading the material. Adjust the sensor settings based on the emissivity of the material being used, ensuring accurate temperature readings and adjustments.
Calibration of the Base and Mold Positioning:
Precise positioning of the base and mold is critical for the AFP process. Use a similar process as base calibration to verify the position of the mold relative to the machine's coordinate system. Adjust the position in the software based on the data acquired to align with the programmed paths accurately.
For molds without predefined locating features, create a detailed map of reference points on the mold surface. Use these points to locate the mold on the pre-calibrated base, this allows for easy setup and repeatable placement.
Troubleshooting Common Issues
Troubleshooting is essential for maintaining AFP machine efficiency and reducing downtimes. Here are solutions to common issues:
High Tackiness in Thermoset Tapes:
Cool the environment or AFP head, or use non-sticky pinch rollers to manage tape stickiness.
Adjust layup strategy or material selection if tackiness persists.
Fuzz Buildup in Dry Fiber:
Implement regular cleaning schedules and checks to prevent and remove fuzz accumulation.
Optimize material handling and consider alternative material suppliers for better quality control.
Tape Tearing with Thermoplastics:
Ensure tape edges are cleanly cut and inspect for tearing at cut points.
Use water-cooled rollers or additional cooling mechanisms for compaction rollers when processing at high temperatures.
Maintenance Tips for AFP Machine Efficiency
Routine Cleaning: Regularly clean the AFP head and components to prevent buildup of materials and ensure sensors and mechanisms function correctly.
Consumable Management: Monitor and replace consumables such as blades and compaction rollers according to usage and wear patterns.
Temperature Management: For thermoplastic processing, ensure all components exposed to high temperatures are adequately cooled to prevent degradation.
Sensor Maintenance: Keep sensor sights clean to avoid erroneous readings that could impact machine operation and material placement accuracy.
Conclusion
The exploration of Automated Fiber Placement (AFP) technology throughout this blog has shed light on the critical aspects and intricacies of AFP machines, emphasizing the importance of each component and its function. Here, we distill the essence of our discussion into key takeaways and future perspectives.
Understanding AFP Machine Components
Crucial for Optimization: A thorough grasp of AFP components enhances operational efficiency and product quality.
Technical Proficiency Required: Mastery over machine setup, calibration, and troubleshooting ensures smooth production processes.
Continuous Learning: As technology evolves, staying updated with the latest advancements in AFP components and practices is vital.
Future Outlook on AFP Technology
Innovation and Expansion: Anticipate advancements in artificial intelligence and machine learning to refine AFP precision and versatility.
Accessibility and Versatility: Modular AFP heads are making the technology accessible to a wider range of industries, fostering innovation.
Sustainability Focus: The precision of AFP in material placement aligns with sustainable manufacturing goals, especially with the adoption of recyclable thermoplastics.
Final Thoughts
AFP technology stands at the forefront of manufacturing innovation, with its impact only set to grow.
Embracing continuous learning and adaptation to new technologies will be key for professionals in the field.
The future of AFP promises not only enhanced manufacturing capabilities but also a stride towards more sustainable practices.
Complete course
The above article is part of the course Mastering Automated Fiber Placement: A Comprehensive Guide for Manufacturers. This course offers an in-depth understanding of Automated Fiber Placement (AFP) in composite manufacturing. It covers the basics of composites, AFP processes, machine operation, programming, troubleshooting, and practical applications, aimed at empowering manufacturers with the knowledge and confidence to efficiently operate AFP systems.
What's Next!
Discover the future of composite manufacturing with Addcomposites! Here's how you can get involved:
Stay Informed: Subscribe to our newsletter to receive the latest updates, news, and developments in AFP systems and services. Knowledge is power, and by staying informed, you'll always have the upper hand. Subscribe Now
Experience Our Technology: Try our cutting-edge simulation software for a firsthand experience of the versatility and capability of our AFP systems. You'll see how our technology can transform your production line. Try Simulation
Join the Collaboration: Engage with us and other technical centers across various industries. By joining this collaborative platform, you'll get to share ideas, innovate, and influence the future of AFP. Join Collaboration
Get Hands-On: Avail our educational rentals for university projects or semester-long programs. Experience how our AFP systems bring about a revolution in composite manufacturing and leverage this opportunity for academic and research pursuits. Request for Educational Rental
Take the Next Step: Request a quotation for our AFP systems. Whether you're interested in the AFP-XS, AFP-X, or SCF3D, we are committed to offering cost-effective solutions tailored to your needs. Take the plunge and prepare your production line for the next generation of composite manufacturing. Request Quotation
At Addcomposites, we are dedicated to revolutionizing composite manufacturing. Our AFP systems and comprehensive support services are waiting for you to harness. So, don't wait – get started on your journey to the future of manufacturing today!
Comments