Automated Fiber Placement in Automotive Manufacturing
- Pravin Luthada
- Nov 27, 2023
- 7 min read
The quest for efficiency has long propelled innovation in the automotive industry, with lightweighting emerging as a key strategy to enhance fuel economy and reduce emissions. This drive towards lighter vehicles has its roots in the aerospace sector, where every ounce saved can lead to significant gains in performance and cost savings. As manufacturers strive to meet the evolving demands of electrified and conventional powertrains, the adoption of advanced materials and manufacturing processes has become paramount. Among these, AFP stands out as a transformative approach, enabling the precise creation of complex geometries and optimized strength-to-weight ratios in composite materials. This blog explores the journey of lightweighting from concept to implementation across industries, highlighting OEM success stories, the pivotal role of composites, and the revolutionary impact of AFP in reshaping automotive manufacturing for a sustainable future.
The Evolution of Lightweighting Across Industries
Aerospace Origins
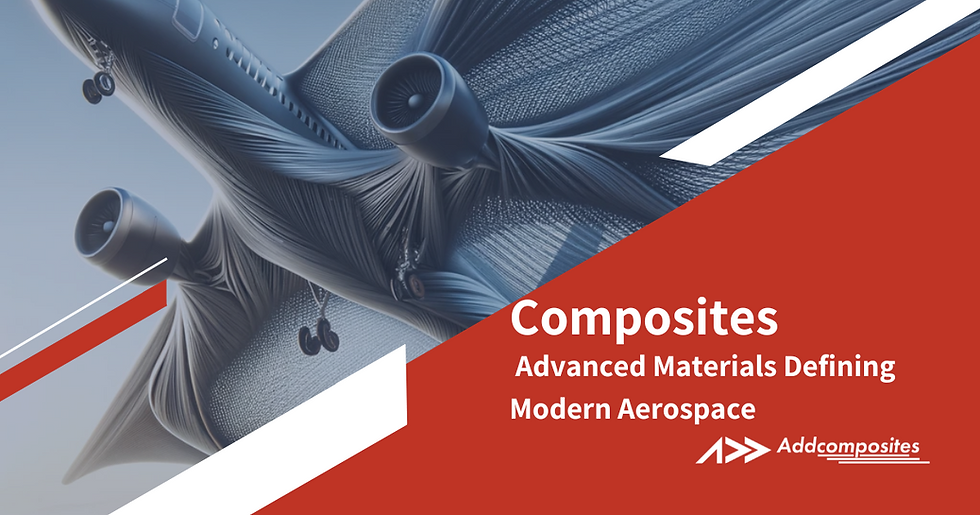
The pursuit of lightweighting began in earnest within the aerospace industry, where every ounce matters. The philosophy is simple: lighter aircraft use less fuel, which not only cuts costs but also reduces environmental impact. Aerospace engineers have long utilized materials like titanium and advanced composites to shave weight while maintaining structural integrity. The innovations and materials developed for aircraft have set the stage for cross-industry applications. Transition to Automotive The automotive industry, facing similar pressures to reduce emissions and enhance fuel efficiency, has taken cues from aerospace. OEMs have shifted from the traditional use of steel to a broader palette that includes aluminum, magnesium, and particularly, carbon-fiber composites. The transfer of knowledge from aerospace to automotive is not without challenges, but the shared goal of lightweighting has facilitated a cross-pollination of technologies and materials.
The Push for Composite Materials in Lightweight Automotive Design
Role of Composites in Performance Enhancement
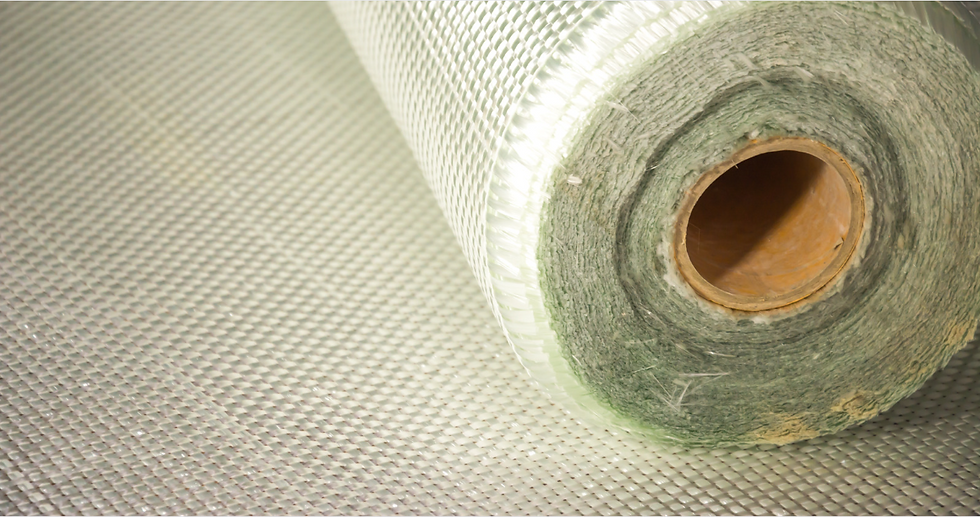
Composite materials have become the cornerstone of lightweight automotive design, offering unmatched strength-to-weight ratios. Carbon-fiber reinforced plastics (CFRP), for instance, provide superior stiffness and strength compared to metals like steel and aluminum, which directly translates into enhanced vehicle performance and fuel economy. The integration of these materials into structural components and body panels can significantly reduce vehicle mass without sacrificing safety or functionality.
Technological Advancements
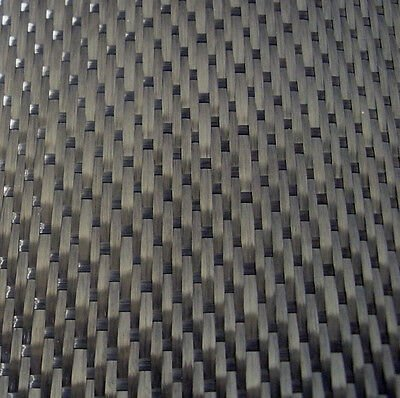
The use of composites was once restricted to high-end sports cars and luxury vehicles due to cost and production constraints. However, advancements in materials technology have now made composites viable for mass-produced vehicles. Techniques such as AFP have allowed for precise control over fiber orientation and placement, leading to more efficient use of materials and improved structural properties. As a result, composites have found their way into mainstream models, where they contribute to weight reduction and energy efficiency.
Automated Fiber Placement: Automotive Composite Manufacturing
Intricacies of AFP Technology

AFP is a game-changing technology in the field of composite manufacturing. It involves a robotic system that lays down fibers in predetermined paths, allowing for precise fiber orientation and placement. This precision is key to optimizing the strength-to-weight ratios critical to automotive performance. The technology utilizes advanced software that calculates the optimal path of fiber placement to ensure that the composite material bears load efficiently, reducing excess material use while maximizing strength.
Transforming Automotive Part Fabrication
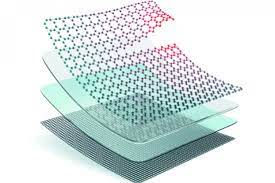
AFP's precision is particularly beneficial when creating parts with complex geometries that are difficult to mold using traditional methods. For instance, the layup can be adjusted for varying load cases across a single part, enhancing performance where needed without adding unnecessary weight. This approach is integral in manufacturing intricate components like aerodynamic body panels, curved frames, and parts with internal structures, which would otherwise require multiple pieces and joints.
Technical Nuances
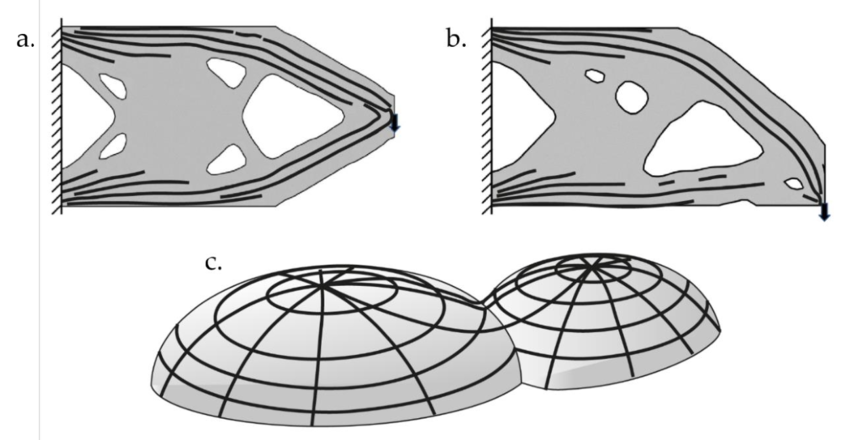
From a technical standpoint, AFP allows engineers to apply classical laminate theory in new ways. By manipulating the orientation of fibers in each ply of a laminate, engineers can tailor the material's anisotropic properties to withstand specific stress profiles. This level of customization is unparalleled in traditional manufacturing methods and showcases the fusion of material science with advanced manufacturing techniques.
List of Automotive Parts Potentially Manufactured Using AFP
Wheels

AFP can be applied to create lightweight and strong wheels with selective reinforcement in specific load-bearing areas, improving performance without the weight penalty of traditional materials.
Chassis Components The chassis benefits from AFP by allowing for complex shapes and tailored strength properties, resulting in a lighter yet stiffer structure that enhances vehicle dynamics and safety.
Battery Enclosures for EVs

AFP enables the manufacturing of robust battery enclosures that are lightweight, ensuring protection and contributing to the overall energy efficiency of electric vehicles.
Body Panels

AFP allows for the creation of aerodynamic, lightweight body panels with varying thicknesses and material composition, optimizing them for strength and impact resistance while contributing to fuel efficiency.
Motor Sleeve

AFP allows for the creation of high-strength motor sleeves using thermoplastic material while reducing weight allowing for high rpm motors increasing range efficiency and better performance at higher speeds.
Structural Components
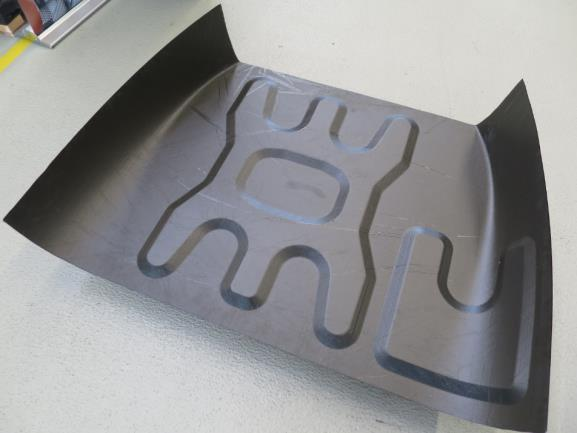
Components like the vehicle's subframe can be optimized for weight and rigidity using AFP, directly impacting the vehicle's handling and performance characteristics.
Aerodynamic Components

AFP's precision is ideal for manufacturing complex aerodynamic components like spoilers and diffusers, which require a balance of lightness and structural integrity. By integrating AFP into the manufacturing process, automotive engineers can exploit the full potential of composite materials, creating parts that are not only lighter and stronger but also more integrated and functionally optimized than ever before.
Challenges and Solutions in the Integration of Composites
Joining Dissimilar Materials
One of the primary challenges in using composites is the difficulty of joining them to traditional automotive materials like steel or aluminum. This is because composites and metals differ in thermal expansion, corrosion characteristics, and mechanical properties. Engineers are tackling this issue with new joining technologies such as adhesive bonding, mechanical fastening, and hybrid methods that combine both. These solutions aim to maintain the integrity of the joint over the vehicle's lifespan despite the different behaviors of the materials involved.
The Multi-Material Approach
The contemporary design and manufacturing of vehicles are increasingly adopting a multi-material strategy. This approach leverages the strengths of various materials—metals for their toughness and durability, and composites for their lightweight and stiffness. By using advanced simulation software and manufacturing techniques, engineers can design vehicles where each part is made from the optimal material for its specific function. This method not only enhances the vehicle's performance but also maintains or improves safety standards and manufacturing efficiency.
Case Study: General Motors and Automated Fiber Placement
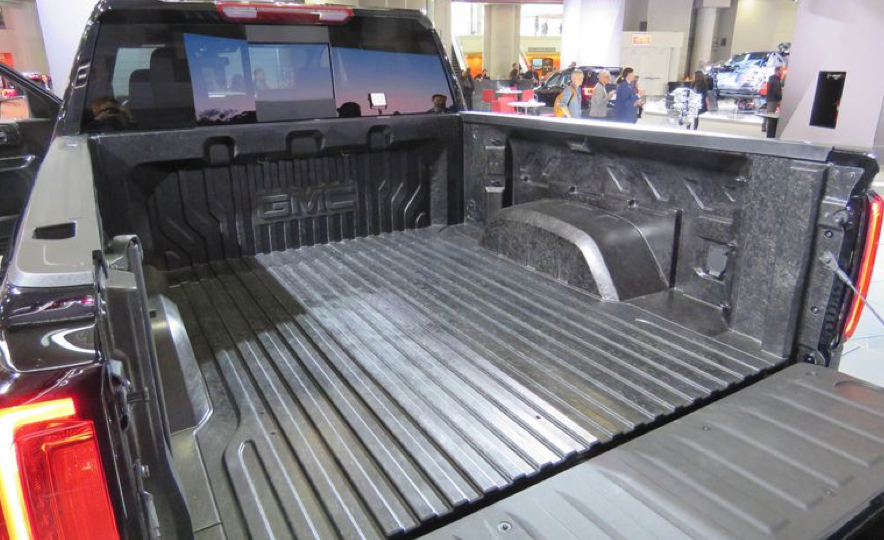
General Motors (GM) is a prime example of AFP in action within the automotive industry. By incorporating AFP into their manufacturing processes, GM has been able to produce lighter vehicle models, significantly reducing total vehicle mass. For instance, in their new-generation trucks, GM utilized AFP to create a body that is 88 pounds lighter than its predecessor, as well as a fully boxed steel frame that is both lighter and offers greater torsional rigidity. The success of AFP in GM's manufacturing process underlines the technology's potential to revolutionize automotive production by enabling the creation of lighter, stronger, and more efficient vehicles.
Future Prospects and Sustainable Practices
Advancing AFP for Mass Production

The scalability of AFP technology is pivotal for its future in automotive manufacturing. As the demand for lightweight vehicles grows, AFP must evolve to meet high-volume production needs without sacrificing the precision and quality that are its hallmarks.
Embracing Sustainable Materials

A significant trend is the shift towards sustainable materials like thermoplastics in AFP processes. Thermoplastics not only offer the benefits of being lightweight and strong but also are recyclable, aligning with the industry's increasing commitment to sustainability.
A Greener Footprint
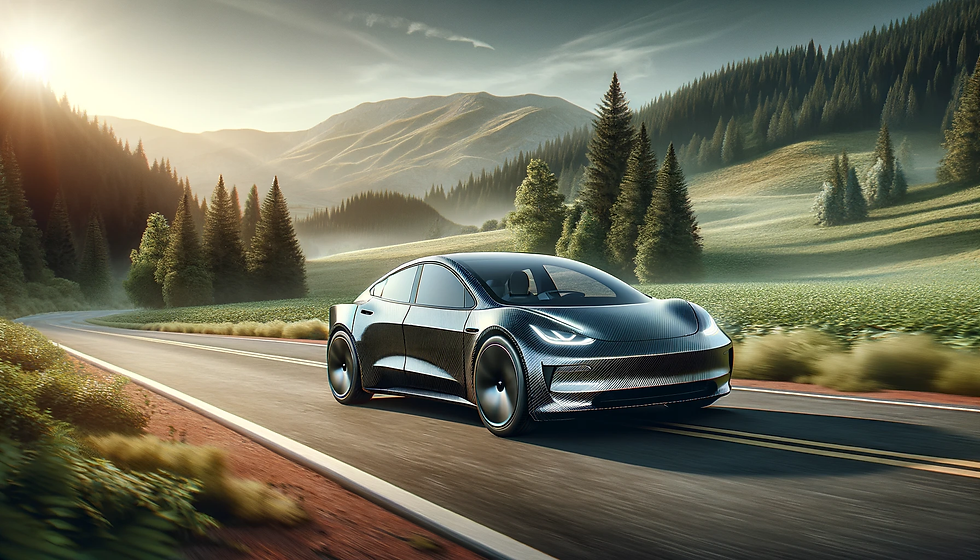
The future of AFP in the automotive industry is not just about technological advancements but also about integrating eco-friendly practices into the lifecycle of automotive parts—from manufacturing to end-of-life recycling. This holistic approach promises to redefine the industry’s impact on the environment, making the vehicles of tomorrow not just more efficient but also more harmonious with environmental sustainability goals.
Conclusion: Shaping the Future of Automotive Manufacturing with AFP
As the automotive industry accelerates towards a lighter, more efficient future, the role of AFP has become increasingly significant. This innovative manufacturing process has demonstrated its ability to drive the lightweighting agenda, markedly improving fuel economy and meeting stringent emissions standards. From aerospace to automotive, AFP's precision in fiber placement has been instrumental in crafting parts that redefine vehicle performance and design.
The transition to using composites, particularly in mass-produced vehicles, is a leap forward, enabled by AFP's capabilities. The success stories from OEMs like General Motors validate the tremendous potential AFP holds in optimizing weight without compromising strength or safety.
Looking ahead, AFP is poised to play a central role in the evolution of automotive manufacturing, integrating sustainable practices and materials. Its scalability will be key to meeting the demands of an industry that not only prioritizes performance but also environmental stewardship. In the grander scheme, AFP and composite materials stand as cornerstones for the future of transportation, underpinning everything from today's fuel-powered vehicles to tomorrow's electric models. As we embrace these advancements, we are not just engineering vehicles; we are crafting the future of mobility.
What's Next!
Discover the future of composite manufacturing with Addcomposites! Here's how you can get involved:
Stay Informed: Subscribe to our newsletter to receive the latest updates, news, and developments in AFP systems and services. Knowledge is power, and by staying informed, you'll always have the upper hand. Subscribe Now
Experience Our Technology: Try our cutting-edge simulation software for a firsthand experience of the versatility and capability of our AFP systems. You'll see how our technology can transform your production line. Try Simulation
Join the Collaboration: Engage with us and other technical centers across various industries. By joining this collaborative platform, you'll get to share ideas, innovate, and influence the future of AFP. Join Collaboration
Get Hands-On: Avail our educational rentals for university projects or semester-long programs. Experience how our AFP systems bring about a revolution in composite manufacturing and leverage this opportunity for academic and research pursuits. Request for Educational Rental
Take the Next Step: Request a quotation for our AFP systems. Whether you're interested in the AFP-XS, AFP-X, or SCF3D, we are committed to offering cost-effective solutions tailored to your needs. Take the plunge and prepare your production line for the next generation of composite manufacturing. Request Quotation
At Addcomposites, we are dedicated to revolutionizing composite manufacturing. Our AFP systems and comprehensive support services are waiting for you to harness. So, don't wait – get started on your journey to the future of manufacturing today!
Comments