Automated Fiber Placement Process: A Revolutionary Way to Create Composite Parts
- Pravin Luthada
- Dec 26, 2022
- 3 min read
Updated: Jan 19, 2023
Introduction

Automated fiber placement (AFP) is a relatively new process that has revolutionized the way composite parts are created. This process can be used to create complex geometries with high accuracy, without sacrificing any of the structural benefits associated with composites. In this blog post, we will discuss some of the key advantages of using automated fiber placement for creating composite parts.
Faster Production Time and Improved Efficiency

One of the most significant benefits of AFP is that it allows for faster production times without sacrificing quality or accuracy. The process involves laying down unidirectional fibers in a pre-programmed pattern, as opposed to traditional manual hand layup processes which require technicians to place individual strands on a part manually. As a result, AFP can reduce production times by up to 40%, while also improving efficiency and reducing material waste. Additionally, AFP can be used on large-scale projects where manual labor isn’t feasible due to time constraints or cost restrictions.
Another advantage of AFP is that it can produce more consistent results than manual hand layup processes. Because the fibers are laid down in a predetermined pattern, they form stronger bonds between each layer and provide increased performance and strength in the finished product.
Increased Performance and Strength

Another advantage of AFP is that it can produce more consistent results than manual hand layup processes. Because the fibers are laid down in a predetermined pattern, they form stronger bonds between each layer and provide increased performance and strength in the finished product. This means that composites produced with AFP have greater resistance to fatigue and other environmental factors than those produced through traditional manual methods. Additionally, because AFP creates such strong bonds between layers, it eliminates any potential delamination issues that may arise from inconsistencies in the layup process.
The use of a predetermined pattern for the placement of fiber material can also help to eliminate potential delamination issues that may arise from inconsistencies in the layup process. Composites produced with the AFP process tend to have greater resistance to fatigue and other environmental factors due to the strong bonds between layers.
It is worth noting that the benefits of increased performance and strength may vary depending on the specific application and the materials used in the composite. However, in general, the use of the AFP process can result in improved composite parts with enhanced performance and strength compared to traditional manual manufacturing techniques.
Cost Effectiveness
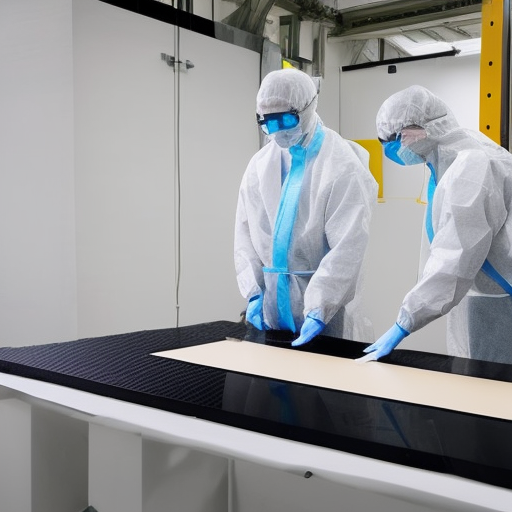
Finally, automated fiber placement is cost-effective compared to other manufacturing processes due to its improved efficiency and reduced material waste. As previously mentioned, AFP reduces production times by up to 40%, so manufacturers don’t have to invest as much time or money into their projects. Additionally, because there is less material waste associated with AFP than with manual hand layup processes, manufacturers don’t have to worry about purchasing excess materials or disposing of unused materials after the job is completed.
A Cost-Effective Solution for Automated Fibre Placement and Automated Tape Laying
Addcomposites has developed an innovative and cost-effective solution for automated fiber placement (AFP) and automated tape laying (ATL) processes with the AFP-XS system. The ability to convert an existing robotic arm into an AFP system with a monthly subscription can be beneficial for manufacturers looking to adopt the AFP process without making a significant upfront investment in equipment.
The ability to produce aerospace-grade quality composite parts with the AFP-XS system is also a significant advantage for manufacturers, as it allows them to produce high-quality parts for a variety of applications. The ability to work with a range of materials, including thermoset, thermoplastic, and dry fiber systems, can also provide manufacturers with greater flexibility in their production processes.
Overall, it seems that the AFP-XS system from Addcomposites can be a valuable tool for manufacturers looking to adopt the automated fiber placement process and improve their production capabilities
Conclusion
Automated fiber placement offers many advantages for researchers looking for an efficient way to create composite parts with increased performance and strength without sacrificing quality or accuracy. It drastically reduces production times while cutting down on material waste and eliminating potential delamination issues due to inconsistent manual layup processes. Finally, its cost-effectiveness makes it an attractive option for those looking for an efficient manufacturing solution without breaking the bank!
Don't miss out on the opportunity to see how continuous fiber AFP can benefit your developments. Contact Pravin Luthada or James Kuligoski via LinkedIn now to schedule a demo.
About Addcomposites
Addcomposites is the provider of the Automated Fiber Placement (AFP) ecosystem - including the Fiber Placement System (AFP-XS), 3D Simulation and Programming Software (AddPath), and Robotic Cells (AddCell). With the leasing program for the AFP system (AFPnext), composites manufacturers can work with thermosets, thermoplastics, dry fiber placement, or in combination with 3D Printers on a monthly basis.
Comments