Automating the Future: The Role of Automated Fiber Placement in Structural Battery Manufacturing
- Pravin Luthada
- May 29, 2023
- 7 min read
1. Introduction
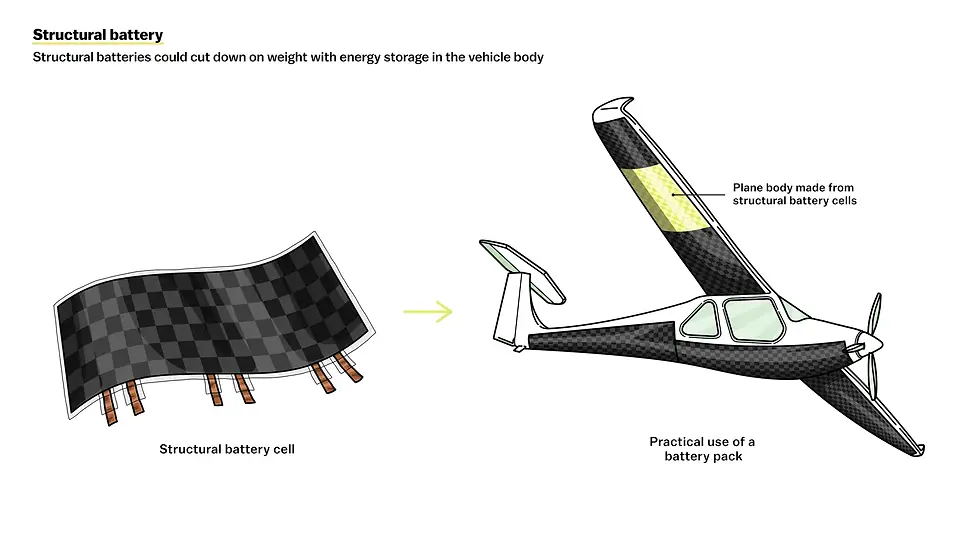
In the rapidly evolving world of electric vehicles and devices, the concept of structural batteries is emerging as a game-changer. These aren't your typical batteries; they're integral components of the device or vehicle's structure, contributing to its overall strength and stiffness. This introduction will provide a brief overview of structural batteries and the transformative role of Automated Fiber Placement (AFP) technology in their manufacturing.
Table of Content hyperlink
1.1 The Concept of Structural Batteries
1.2 The Role of AFP Technology in Composites Manufacturing
2. Understanding Structural Batteries
2.1 The Manufacturing Process of Structural Batteries
2.2 Multifunctional Constituents in Structural Battery Manufacturing
3. The Role of AFP in Structural Battery Manufacturing
3.1 Integrating AFP Technology in Structural Battery Manufacturing
3.2 Unique Characteristics and Benefits of AFP Systems
4. The Power of Automation Software in Composites Manufacturing
4.1 Introduction to AddPath
4.2 Enhancing Structural Battery Manufacturing with AddPath
5.1 The Potential of AFP Technology
5.2 Looking Ahead
1.1 The Concept of Structural Batteries
Structural batteries are a novel concept that combines energy storage and structural function into a single unit. Unlike traditional batteries that simply add weight to a vehicle or device, structural batteries contribute to the overall strength and stiffness of the structure. This dual functionality can lead to significant weight reductions, making vehicles and devices more energy-efficient. [1]
The significance of structural batteries extends beyond just weight reduction. By integrating the battery into the structure of the vehicle or device, designers can free up space, allowing for more innovative and flexible designs. This has far-reaching implications for the future of electric vehicles and devices, potentially revolutionizing the way they're designed and manufactured.
1.2 The Role of AFP Technology in Composites Manufacturing [2]
AFP technology is a cutting-edge manufacturing technique used in the production of composite materials. It involves the precise placement of carbon, glass, or other types of fibers onto a mold using a computer-controlled system. This allows for the creation of complex shapes and structures that would be difficult, if not impossible, to achieve with traditional manufacturing methods.
In the context of structural battery manufacturing, AFP technology can play a crucial role. It can be used to precisely place the carbon fibers used in the negative electrode of the battery, ensuring optimal performance. Furthermore, AFP technology can automate the layering process involved in the manufacturing of structural batteries, enhancing accuracy and consistency.
2. Understanding Structural Batteries
In the realm of electric vehicles and devices, the concept of structural batteries is gaining significant traction. These batteries are not just energy storage systems; they are integral parts of the structure of the device or vehicle, contributing to its overall strength and stiffness. This section delves into the manufacturing process of structural batteries, based on the research paper "A Structural Battery and its Multifunctional Performance".

2.1 The Manufacturing Process of Structural Batteries
The manufacturing process of a structural battery is a fascinating blend of materials science and engineering. Here's a step-by-step breakdown:
Carbon Fiber Negative Electrode: The process begins with the creation of a negative electrode made from carbon fiber (CF). The CF serves a dual purpose: it adds stiffness and strength to the battery, and it also acts as a current collector.
Structural Electrolyte: Next, a structural electrolyte is introduced. This electrolyte is responsible for both load transfer and ion transport. It's a key component that allows the battery to function as a structural element.
Glass Fiber Fabric Separator: A glass fiber fabric is used to separate the CF negative electrode from the positive electrode. This separator is crucial for maintaining the integrity of the battery and preventing short circuits.
Aluminum Foil-Supported Positive Electrode: The final step in the process is the addition of an aluminum foil-supported lithium–iron–phosphate positive electrode. This electrode is responsible for the electrochemical reactions that generate electricity.
2.2 Multifunctional Constituents in Structural Battery Manufacturing
The manufacturing process of structural batteries is unique in that it employs multifunctional constituents. Each component serves multiple functions, contributing to both the structural integrity and the electrical performance of the battery. Here's a closer look at these constituents: [3]
Carbon Fibers (CFs): CFs are used as the negative electrode in the battery. They not only add stiffness and strength to the battery but also act as a current collector. This dual functionality makes CFs a critical component in structural batteries.
Structural Electrolyte: The structural electrolyte in the battery serves two main functions: load transfer and ion transport. This allows the battery to function as a structural element while also facilitating the necessary electrochemical reactions.
Glass Fiber Fabric: The glass fiber fabric serves as a separator between the negative and positive electrodes. This prevents short circuits and maintains the structural integrity of the battery.
Aluminum Foil-Supported Positive Electrode: The positive electrode in the battery is supported by an aluminum foil. This electrode is responsible for the electrochemical reactions that generate electricity, while aluminum foil provides structural support.
3. The Role of AFP in Structural Battery Manufacturing
AFP technology is revolutionizing the way we manufacture composite materials, and its application in the production of structural batteries is no exception. This section explores how AFP technology can be integrated into the manufacturing process of structural batteries and the unique benefits it brings. [4]
3.1 Integrating AFP Technology in Structural Battery Manufacturing
AFP technology can be a game-changer in the manufacturing process of structural batteries. Here's how:
Precision Placement of Fibers: AFP technology allows for the precise placement of fibers, which is crucial in creating the carbon fiber negative electrode in structural batteries. This precision ensures optimal performance of the electrode and, by extension, the battery.
The Layering of Components: The manufacturing process of structural batteries involves layering different components, including the carbon fiber negative electrode, the structural electrolyte, the glass fiber fabric separator, and the aluminum foil-supported positive electrode. AFP technology can automate this layering process, ensuring accuracy and consistency.
Scalability: AFP technology can significantly speed up the manufacturing process, making it easier to scale up production. This is particularly important as the demand for structural batteries is expected to grow in the coming years.

3.2 Unique Characteristics and Benefits of AFP Systems
AFP systems like AFP-XS, AFP-X, and SCF3D each bring unique characteristics and benefits to the table. Let's take a closer look:
AFP-XS: This introductory and modular single-tow AFP system is ideal for experimentation with different widths and types of materials. Its versatility and modularity make it suitable for a wide variety of applications, including the production of structural batteries.
AFP-X: This production-class multi-tow AFP system is designed for achieving a higher production rate for complex parts. It can carry up to 4x more materials than the AFP-XS, making it a great choice for the large-scale production of structural batteries.
SCF3D: This system is Addcomposites’ response to the increasing demand for continuous fiber additive manufacturing. It incorporates continuous fibers throughout the printing process, eliminating the need for additional reinforcement steps. This system can deliver high-quality, structural components, making it ideal for the production of structural batteries.
4. The Power of Automation Software in Composites Manufacturing
Automation software plays a pivotal role in modern composites manufacturing, enhancing efficiency, precision, and flexibility. One such software is AddPath, an offline programming tool designed for path planning needs. This section explores how AddPath can enhance the manufacturing process of structural batteries.
4.1 Introduction to AddPath
AddPath is a user-friendly, open-access offline programming software designed to streamline and optimize the path planning process in composites manufacturing. Here are some of its key features:
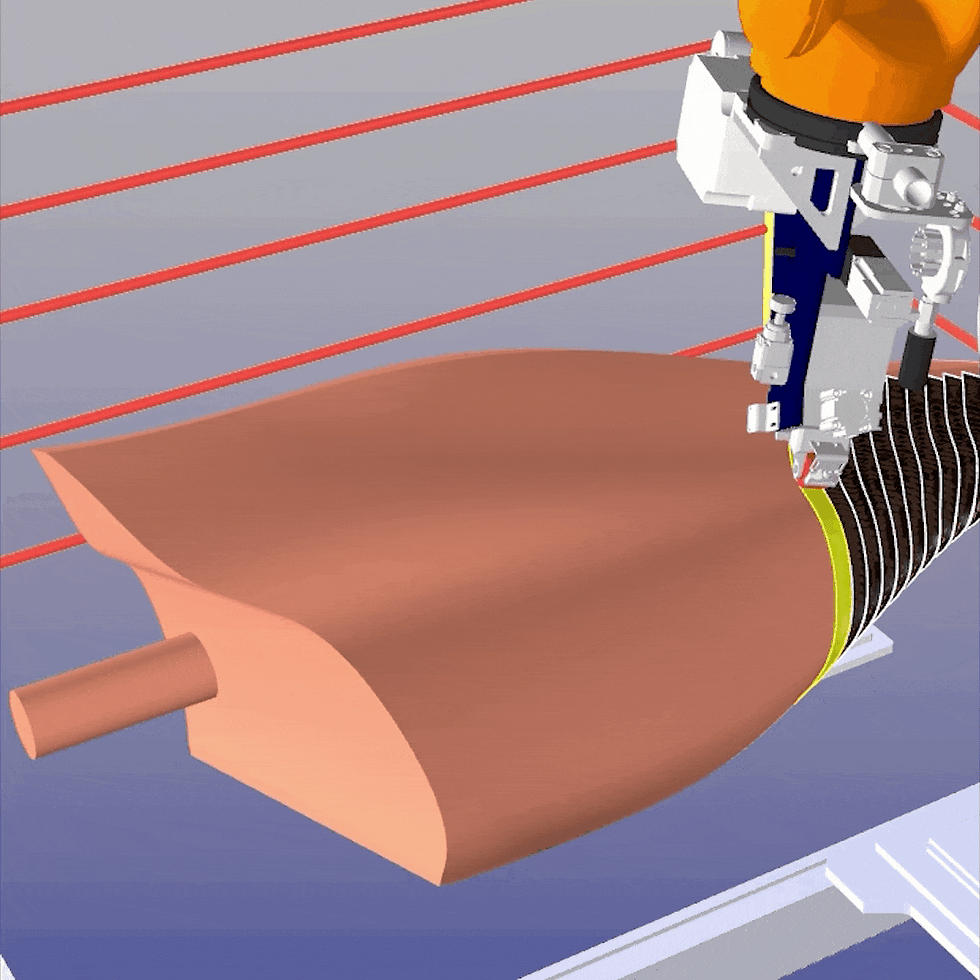
CAD Surface Reading: AddPath can read CAD surfaces, allowing for precise planning and execution of the manufacturing process.
Parameter Input: The software allows for the input of a variety of parameters, providing visual notifications to guide the user through the process.
Simulation Capabilities: With AddPath, you can simulate programmed AFP tape courses, predict and measure the effects of various factors on your process, and plan single or multiple tow paths in one course of motion.
Data Analysis: AddPath is equipped with features for exporting tape course geometry to standard CAD formats for further evaluation and importing captured data during the process for production data analysis.
4.2 Enhancing Structural Battery Manufacturing with AddPath
AddPath can significantly enhance the manufacturing process of structural batteries in several ways:
Precision Planning: By reading CAD surfaces and allowing for the input of various parameters, AddPath enables precise planning of the manufacturing process. This is particularly important in the production of structural batteries, where precision is key to achieving optimal performance.
Process Simulation: AddPath's simulation capabilities allow manufacturers to predict and measure the effects of various factors on the manufacturing process. This can help in optimizing the production of structural batteries, ensuring that each component is manufactured to the highest standards.
Data Analysis: The ability to analyze production data can provide valuable insights into the manufacturing process, helping to identify areas for improvement and ensure the consistent quality of the structural batteries produced.
5. Conclusion
As we reach the end of this exploration into the intersection of structural battery manufacturing and Automated Fiber Placement (AFP) technology, it's clear that we're standing on the precipice of a new era in composites manufacturing.
5.1 The Potential of AFP Technology
AFP technology has shown immense potential in revolutionizing the manufacturing process of structural batteries. With its precision, scalability, and versatility, AFP systems like AFP-XS, AFP-X, and SCF3D can significantly enhance the production of structural batteries. These systems allow for the precise placement of fibers, efficient layering of components, and rapid scaling of production, making them invaluable tools in the manufacturing process.
Moreover, the integration of automation software like AddPath further amplifies the capabilities of AFP technology. By offering precision planning, process simulation, and data analysis capabilities, AddPath can help manufacturers optimize their processes, improve product quality, and increase efficiency.
5.2 Looking Ahead
Looking ahead, the future of structural batteries and AFP technology is bright. As the demand for lightweight, energy-efficient electric vehicles and devices continues to grow, so too will the need for advanced manufacturing technologies like AFP.
In the coming years, we can expect to see further advancements in AFP technology and automation software, leading to even more efficient and cost-effective production of structural batteries. Moreover, as more manufacturers adopt these technologies, we can expect to see a rise in the quality and performance of structural batteries.
What's Next!
Discover the future of composite manufacturing with Addcomposites! Here's how you can get involved:
Stay Informed: Subscribe to our newsletter to receive the latest updates, news, and developments in AFP systems and services. Knowledge is power, and by staying informed, you'll always have the upper hand. Subscribe Now
Experience Our Technology: Try our cutting-edge simulation software for a firsthand experience of the versatility and capability of our AFP systems. You'll see how our technology can transform your production line. Try Simulation
Join the Collaboration: Engage with us and other technical centers across various industries. By joining this collaborative platform, you'll get to share ideas, innovate, and influence the future of AFP. Join Collaboration
Get Hands-On: Avail our educational rentals for university projects or semester-long programs. Experience how our AFP systems bring about a revolution in composite manufacturing and leverage this opportunity for academic and research pursuits. Request for Educational Rental
Take the Next Step: Request a quotation for our AFP systems. Whether you're interested in the AFP-XS, AFP-X, or SCF3D, we are committed to offering cost-effective solutions tailored to your needs. Take the plunge and prepare your production line for the next generation of composite manufacturing. Request Quotation
At Addcomposites, we are dedicated to revolutionizing composite manufacturing. Our AFP systems and comprehensive support services are waiting for you to harness. So, don't wait – get started on your journey to the future of manufacturing today!
Comments