Best of 2020 in Composites Blogs
- Pravin Luthada
- Jan 28, 2021
- 3 min read
Updated: Nov 16, 2021
Our learning platform grew throughout 2020, bringing you 40+ blogs on composites and their manufacturing technologies! Some were more popular than others, so we decided to put together a list of the most popular blogs from Addcomposites! To receive more content like this, consider following us on LinkedIn.
1. Carbon Fiber Composites: Processing Guide Processing carbon fiber (CF) composites is a tricky (and sticky!) business, considering most engineers thinking of producing or designing come from a background of designing metallic parts. It's been called black aluminum, and its design and fabrication have been described as black art. What is it, really?

The purpose of this design guide is to provide general information and specifications on carbon fiber composite materials and some guidelines for designing lightweight high-performance products with carbon fiber composites.
What are they and how do they differ? Each process has its strengths and weaknesses. In this blogpost, we dive into them and provide insight on how to determine which process is best for your specific application.
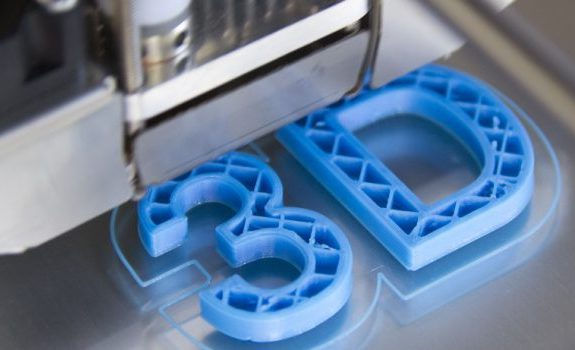
Here we combine the theories discussed in Beam Bending and Fiber Strength, and how to combine them in the world of composites to create strong, lightweight structural parts.
When combined, beam bending and fiber strength can be used to create what is called a Sandwich Panel. Similar to an I-Beam, a sandwich panel places reinforcing material on the top and bottom planes of the beam.

When people think of composites, they immediately picture the black carbon fiber weave that is prevalent on high-end sports cars. While that is not incorrect, there is much more to a composite material than that. The very basic definition of a composites material is ...

As one of the main steps in the ATL/AFP processes is to use a roller as the final stage of the fiber deposition process, this causes some inherent limitations in the part shape that can be produced. The limitation mainly comes from the mold, minimum fiber width, roller radius, and tool interference.

Using OLP, the engineer is able to visualize most, if not all, aspects of how the robot will function in real life through the software. This includes:
- Simulation
- Collision detection
- Material usage
- Layup time
- Waste estimation

7. Virtual Demo: How to make flat laminate using AFP-XS Witnessing the entire process of digitized composite layup usually requires you to travel and visit the facility where the AFP/ATL systems are running. This blog post walks you through a virtual demo video experience; showing you how to program and operate the AFP-XS for your products or shapes.
A natural fiber composite with an outstanding combination of properties is no longer a pipe dream. The use of proper processing techniques, fiber treatments, and compatibilizers, or coupling agents, can lead to composites with optimum properties for a particular application.

Conventionally, the processing of natural fiber thermoplastic composites involves extrusion of the ingredients at melt temperatures followed by shaping operations such as injection molding and thermoforming. Oftentimes creating a sheet of natural fiber-reinforced composites (NFRC), and then shaping it via a thermoforming or similar process.
Freedom to digitally design structures with continuous fiber trajectories enables 10x enhanced structural and other properties, this presents an opportunity to utilize composites in even more industrial applications.
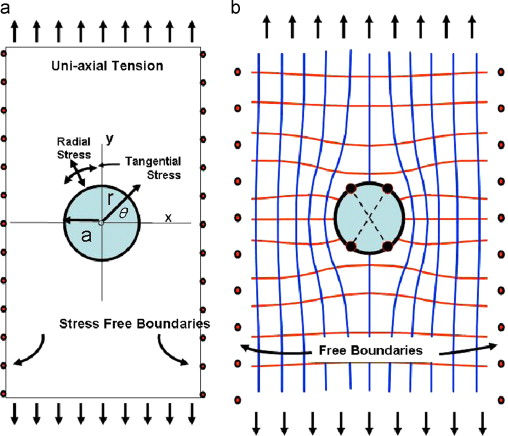
Research scholars working in this field have long waited to get access to such a system for testing new materials, optimizing structural constructions, gain insight into the sustainable design of natural composites, etc. It is now possible to have a digital production system that can be installed in labs with little to no capital expenditure and in no time. Some possible research topics using the newly accessible system are discussed in this blog.
10. Additive Manufacturing using Continuous Fiber: Placement or Printing? Ever since continuous fiber 3D printers burst onto the scene in 2014, engineers around the world have sought a system that could 3D print large-scale continuous fiber-reinforced parts

The ability to purely additively produce complex parts with high strength and low weight, without expensive layup tools or autoclaves, was increasingly sought after. This has created the niche of opportunity for new innovation among the machine tool building startups, who are challenging the status quo and aiming for the multi-billion euro rapid large-scale thermoplastic composites market.
If you are interested in what Addcomposites doing to achieve accessibility to the advanced additive manufacturing industry, please reach out to either Pravin or James and we'd be happy to help! We are actively looking for collaborations, projects, and partnerships!
Comentarios