Programming Techniques, CAM, and Simulation Software in Filament Winding
- Pravin Luthada
- Oct 8, 2023
- 7 min read
1. Introduction
Brief Overview
The subsequent blog delves into various aspects of filament winding, from programming techniques, historical contexts, and advanced programming methodologies to practical applications, challenges, and case studies.
The exploration encompasses a range of topics, including specific winding patterns, geodesic surface modeling, and parametric methods, providing a comprehensive insight into the technicalities and applications of filament winding.
Through detailed analyses, case studies, and technical discussions, the content aims to provide a thorough understanding and appreciation of the complexities and advancements in filament winding.
Definition of Filament Winding
Filament winding is a specialized process for fabricating composite structures, where continuous reinforcements (such as filament, wire, yarn, or tape) are strategically placed over a rotating form or mandrel.
The reinforcements may be pre-impregnated with a matrix material or impregnated during the winding process, adhering to specific stress conditions and geometrical considerations.
The process is generally applied to surfaces of revolution and may include end closures, after which the wound form is cured and the mandrel removed.
Importance in the Composites Industry
Filament winding has emerged as a low-cost method of manufacturing composite preforms, particularly in the production of pipes for fluid transport and cylindrical structures for pressure or storage vessels.
The evolution of filament winding machines and methodologies, from mechanical systems to advanced computer-aided techniques, has significantly enhanced the capabilities and applications of filament winding in the composites industry.
The ability to optimize performance through specific winding angles and patterns has made filament winding a crucial technique in the composites industry, offering precision, efficiency, and versatility in manufacturing.
2. Introduction to Programming Techniques
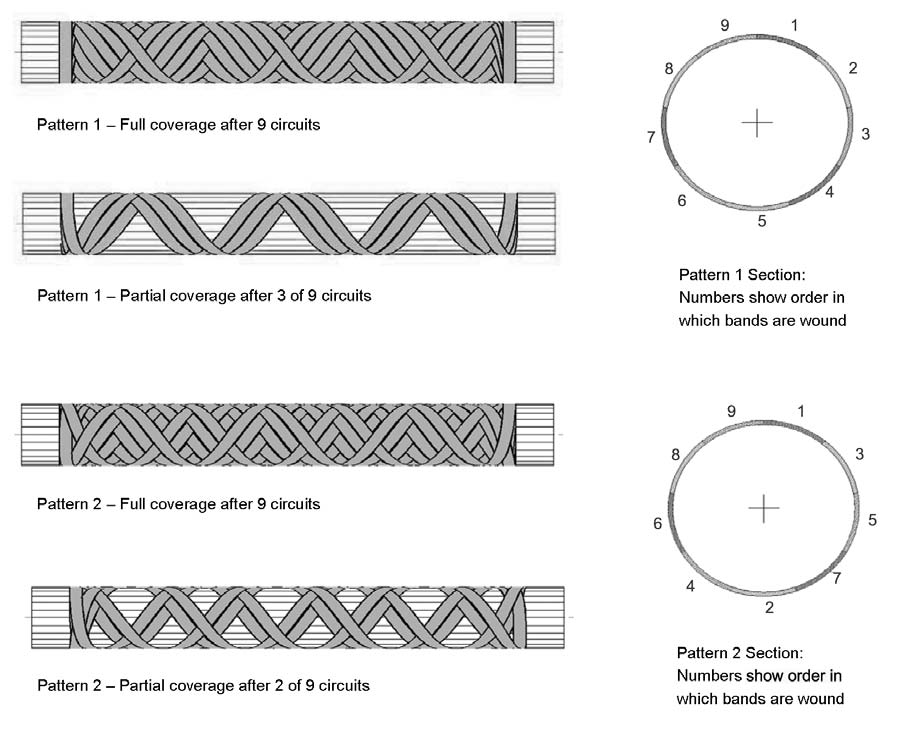
Exploring Predictive Formulas
Key Point: The Significance of Predictive Formulas in Filament Winding
Predictive formulas play a pivotal role in filament winding, particularly in programming various geometries.
Advanced software tools leverage these formulas to facilitate the winding program generation, ensuring precision and consistency in the process.
The application of predictive formulas is not isolated but is often intertwined with the material being used and the geometry being achieved.
Insight into Programming Various Geometries
Key Point: The Complexity and Necessity of Programming Diverse Geometries
The programming of various geometries is not a straightforward task and involves a deep understanding of both the material and the desired final product.
Different geometries require distinct programming approaches, each with its unique challenges and solutions.
The programming of geometries is not only influenced by the physical attributes of the shapes but also by the materials used, such as rovings, tow-preg, and woven materials.
Understanding Material Influence on Winding Program Generation
Key Point: The Interplay between Material Type and Winding Program Generation
Different materials, including rovings, tow-preg, prepreg tape, and woven materials, have distinct influences on winding program generation.
The choice of material can dictate the complexity and approach of the winding program, impacting factors like the geodesic path and the final product's structural integrity.
Understanding how each material interacts with the winding program is crucial for optimizing the filament winding process and ensuring the quality of the final product.
3. Historical Context and Early Techniques in Filament Winding
Early Identification of Shapes for Winding
Key Point: The Genesis of Filament Winding and Initial Challenges
Richard E. Young pioneered what could be considered modern-day filament winding in the early 1940s, starting with a simple mechanical winder that applied fiberglass onto a wooden mandrel.
The initial process involved manually applying an epoxy resin with a paintbrush after the winding process, followed by oven curing and mandrel removal.
This early method, while foundational, was rudimentary and manual, paving the way for the evolution of more sophisticated techniques and machinery in filament winding.
Utilization of Computers for Calculating Geodesic Paths
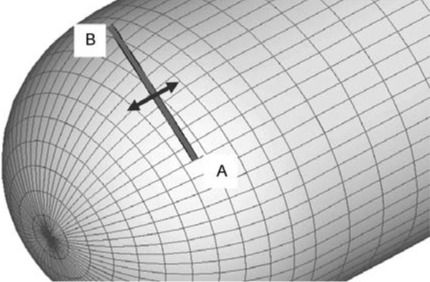
Key Point: The Transition from Manual to Computer-Aided Techniques
The transition from manual to computer-aided filament winding techniques marked a significant advancement in the industry, particularly in calculating winding paths and angles.
Early filament winding machines, up until the 1980s, were mechanically controlled, utilizing gearboxes to determine winding angles and chains to define the part length to be wound.
The introduction of computers not only enhanced the precision in calculating geodesic paths but also significantly improved efficiency and possibilities in filament winding.
Overview of Early Systems for Calculating Paths
Key Point: The Evolution from Mechanical to Automated Systems in Filament Winding
Early systems for calculating paths in filament winding were predominantly mechanical, involving manual adjustments for winding angle changes and part length modifications.
For instance, to change the winding angle, operators had to manually adjust gearboxes, understanding the relationship between sprockets within these gearboxes and how they related to produced winding angles.
The evolution towards automated systems has significantly revolutionized the filament winding process, incorporating advanced technologies and methodologies that have enhanced both the efficiency and capabilities of filament winding.
4. Advanced Programming Techniques in Filament Winding

Introduction to CAD/CAM Systems
Key Point: The Advent and Impact of CAD/CAM Systems in Filament Winding
The evolution of filament winding saw a significant leap with the introduction of Computer-Aided Design and Computer-Aided Manufacturing (CAD/CAM) systems.
CAD/CAM systems brought about a paradigm shift from the manual and mechanical methods of winding to a more precise, efficient, and automated approach.
The integration of computers into the filament winding process not only enhanced precision in calculating geodesic paths but also opened up new possibilities and efficiencies in the winding process.
Discussing Challenges and Solutions in Programming Techniques
Key Point: Navigating through the Complexities of Programming Techniques in Filament Winding
The programming of mechanical machines for filament winding, especially before the widespread adoption of computers, presented numerous challenges, including the manual adjustment of gearboxes and chains to alter winding angles and part lengths.
Operators needed a thorough understanding of the relationships between sprockets within gearboxes and how they related to produced winding angles, requiring meticulous manual adjustments for each part and winding angle.
The modernization of filament winding, particularly in the last decade, has seen a transition from these manual practices to more automated and precise programming techniques, mitigating earlier challenges and enhancing the capabilities of the winding process.
Exploring Advanced Software Tools and Their Applications

Key Point: Leveraging Advanced Software Tools to Elevate Filament Winding Programming
Advanced software tools, such as CADfil from Crescent Consultants Ltd., have been instrumental in navigating through the complexities of winding program generation, especially when dealing with different materials and geometries. New software tools from Addcomposites have added a new dimension with AddPath where upto 12 axes of robots can be used for doing filament winding.
These software tools leverage predictive formulas and provide a platform for programming various geometries, ensuring that the winding paths are calculated with precision and consistency across different materials and shapes.
The application of these advanced software tools is pivotal in optimizing the filament winding process, ensuring that the materials are applied in a manner that adheres to the desired geometrical outcomes and maintaining the structural integrity of the final product.
5. Practical Applications and Challenges in Filament Winding
Deep Dive into Winding Pipe Elbows and Tees

Key Point: The Intricacies and Methodologies in Winding Pipe Elbows and Tees
Filament winding, especially in the context of winding pipe elbows and tees, has evolved significantly from its inception, where manual methods were predominant.
The early stages of filament winding involved manually loading mandrels, manually mixing and applying resin, and manually tying fibers to the mandrel to start winding.
Modern-day filament winding has seen a revolution, with fully automated winding facilities where mandrels are loaded/unloaded with a robot or handling device, and automatic resin-mixing systems are employed.
Exploring Different Types of Winding and Their Applications
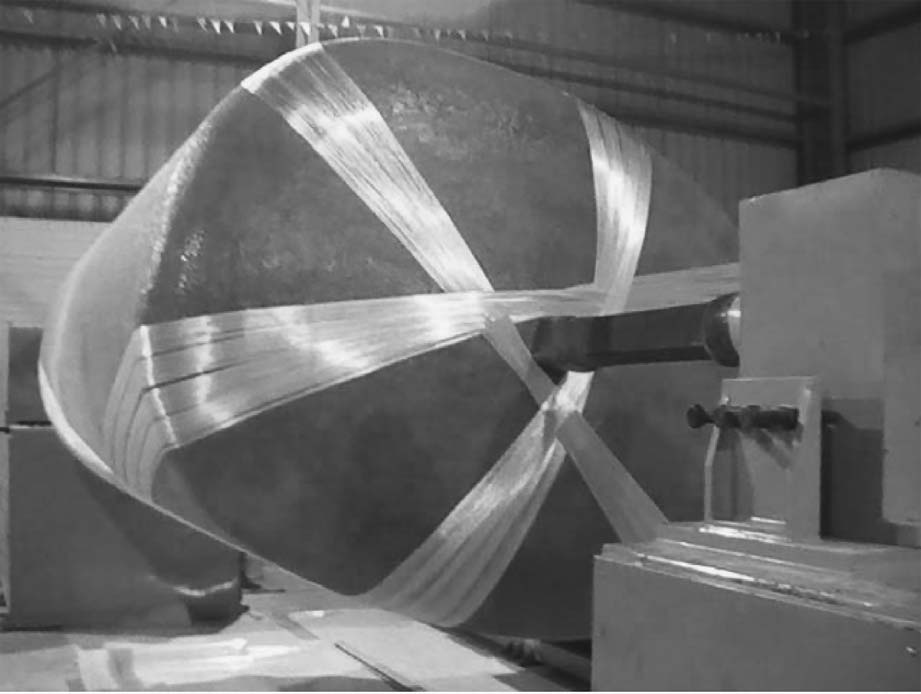
Key Point: The Diversity and Applicability of Various Winding Types
Filament winding is not confined to a singular methodology but encompasses a variety of winding types, each with its unique applications and challenges.
Axisymmetric shapes, such as cylinders, tapered shafts, spheres, and cones, have been prevalent in filament winding due to their rotational symmetry, which simplifies the winding process.
The winding of these shapes, while seemingly straightforward, involves meticulous programming and understanding of the material and geometrical properties to ensure optimal outcomes.
Addressing Challenges and Solutions in Specific Winding Applications
Key Point: Navigating Through Challenges to Optimize Filament Winding Applications
The challenges in filament winding are multifaceted, involving aspects related to materials, geometries, and the winding process itself.
The evolution from mechanical to automated systems in filament winding has mitigated numerous challenges, enhancing the capabilities of the winding process.
Addressing these challenges involves a comprehensive understanding of the interplay between materials, winding programs, and the desired final product, ensuring that the winding process is optimized for various applications.
6. Case Studies and Examples in Filament Winding
Analyzing Specific Winding Patterns
Key Point: The Nuances and Methodologies in Various Winding Patterns
Filament winding patterns are pivotal in determining the structural and functional attributes of the final product, with each pattern offering unique characteristics and applications.
Axisymmetric shapes, such as cylinders, tapered shafts, spheres, and cones, have been prevalent in filament winding due to their rotational symmetry, simplifying the winding process.
The winding patterns for these shapes, while seemingly straightforward, involve meticulous programming and understanding of the material and geometrical properties to ensure optimal outcomes.
Exploring Geodesic Surface Modeling

Key Point: The Role and Significance of Geodesic Surface Modeling in Filament Winding
Geodesic surface modeling is instrumental in filament winding, ensuring that the fibers adhere to the surface of the mandrel in a manner that maintains the structural integrity and desired properties of the final product.
The concept of friction is pivotal in geodesic surface modeling, where the resistance to fiber slippage can come from several physical mechanisms, including mechanical friction, adhesion in tow-preg, and mechanical interlock during wet winding.
Advanced software systems used for programming filament winding machines must incorporate the concept of friction, allowing the user to specify a limiting (non-slip) value for the materials being used.
Understanding Parametric Methods with Friction-Limit Checking
Key Point: Navigating Through Parametric Methods and Friction Considerations in Filament Winding
Parametric methods in filament winding involve a comprehensive understanding of the interplay between materials, winding programs, and the desired final product.
The resistance to fiber slippage, which can be attributed to various mechanisms like mechanical friction and adhesion, plays a crucial role in determining the winding path and ensuring the quality of the final product.
The incorporation of friction-limit checking in parametric methods is vital to ensure that the winding process adheres to the desired geometrical outcomes and maintains the structural integrity of the final product.
Conclusion
Summarizing Key Takeaways
Filament winding has undergone a significant evolution, transitioning from manual, rudimentary methods to sophisticated, computer-aided techniques.
The journey from mechanical systems, involving manual adjustments and calculations, to the implementation of CAD/CAM systems and advanced software tools, has revolutionized the filament winding process.
The technical depth, from understanding predictive formulas to navigating through various winding patterns and understanding the influence of materials, has been pivotal in advancing the filament winding field.
References
M. do Carmo, "Differential Geometry of Curves and Surfaces," Prentice Hall, 1976, p 257.
Cadfil, Crescent Consultants Ltd., United Kingdom, http://www.cadfil.com.
G.R. Dunbar, “Filament Winding,” Paper 66-MD-86, ASME Meeting, May 9–12, 1966.
G. Menges, B. Wodicka, and H.L. Barking, “Non-Geodesic Winding on a Surface of Revolution,” 33rd Tech. Conference, Reinforced Plastics/Composites Institute, SPI Inc., 1978.
L.A. Lyusternik, "Shortest Paths—Variational Problems," Popular Lectures in Mathematics, Vol 13, Pergamon Press Ltd., 1964.
E.A. Hille and S. Menges, "GRP Pipe Fittings Produced on a Computer Controlled Filament Winding Machine," 35th Tech. Conference, Reinforced Plastics/Composites Institute, SPI Inc., 1980.
W. Braun, "Problems of Determining and Preparing Control Data for Non-Rotationally Symmetrical Winding Bodies Explained Using the Geodetically Wound Elbow," Paper 17, Proceedings Third Technical Conference SAMPE European Chapter, Engineering with Composites, Vol 2, 1983.
D.H. Bowen, “Filament Winding in the 1980s,” Fibre Reinforced Composites ‘84 Conf., April 3–5, 1984 (University of Liverpool).
G.C. Eckold and G.M. Wells, "Computer Aided Design and Manufacture of Advanced Composites," Proceedings of Second Conference on Materials Engineering, I. Mech. E. & P.R.I., Nov 5–7, 1985.
R. Ulrich and R. Friedrich, "Fiber Reinforced Plastic Pipe Tee," U.S. Patent 4,601,770, Sept 19, 1983.
Comments