How to Identify the Defects and Damage in Composites Materials and Structures?
- Pravin Luthada
- Jun 27, 2022
- 4 min read
Updated: Jan 20, 2023
Contents
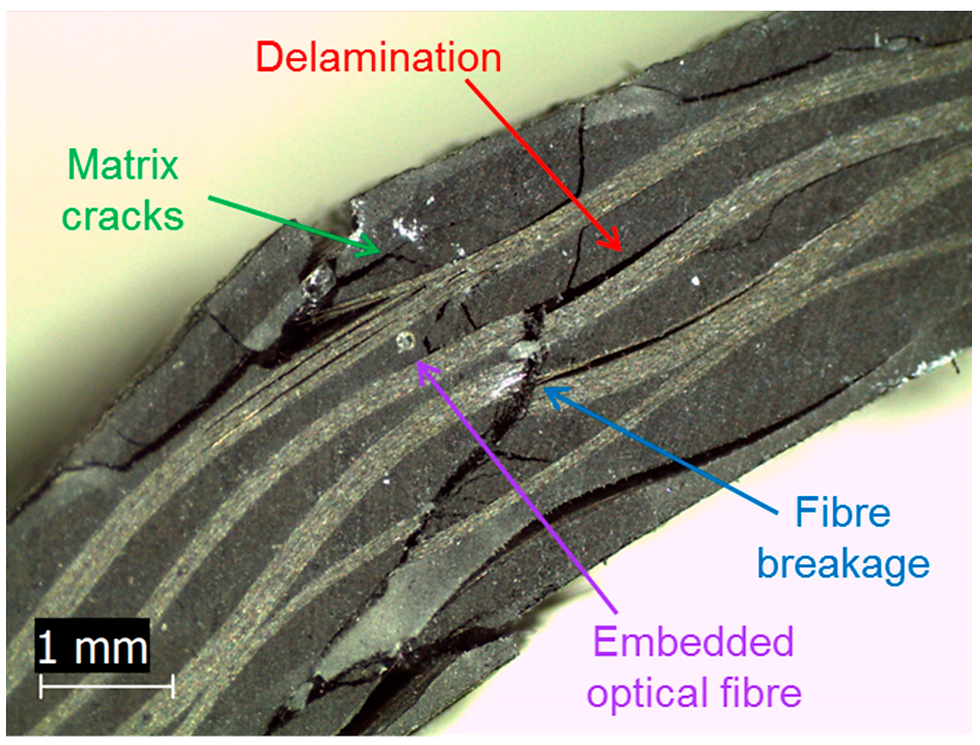
The application of advanced materials in components and structures has evolved due to the need to reduce structural weight and improve performance. Other attributes of composite materials, such as corrosion resistance, excellent surface profiles, enhanced fatigue resilience, and tailored performance, have also been significant contributors to the rapid rise in composite materials application. As a result, these new materials are required to perform at higher stress levels than previous applications while also providing adequate levels of damage tolerance.
Type of damages
Manufacturing and defects/damages

Manufacturing damage includes anomalies, such as porosity, microcracking, and delaminations resulting from processing discrepancies. It also includes such items as inadvertent edge cuts, surface gouges, scratches, damaged fastener holes, and impact damage. Manufacturing defects include:
Delamination
Resin starved areas
Resin rich areas
Blisters, air bubbles
Wrinkles
Voids
Thermal decomposition
Examples of flaws occurring in manufacturing include a contaminated bond-line surface or inclusions, such as prepreg backing paper or separation film, that is inadvertently left between plies during layup. Inadvertent (non-process) damage can occur in detailed parts or components during assembly or transport or during operation.
A part is resin rich if too much resin is used, for nonstructural applications this is not necessarily bad, but it adds weight. A part is called resin starved if too much resin is bled off during the curing process or if not enough resin is applied during the wet layup process. Resin-starved areas are indicated by fibers that show to the surface. The ratio of 60:40 fiber to resin ratio is considered optimum. Sources of manufacturing
defects include:
Improper cure or processing
Improper machining
Mishandling
Improper drilling
Tool drops
Contamination
Improper sanding
Substandard material
Inadequate tooling
Mislocation of holes or details
Damage can occur at several scales within the composite material and structural configuration. This ranges from damage in the matrix and fiber to broken elements and failure of bonded or bolted attachments. The extent of damage controls repeated load life and residual strength and is critical to damage tolerance.
In-Service Damages
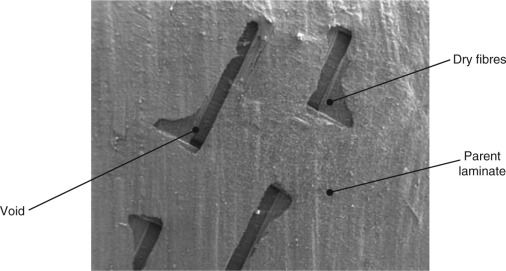
Many honeycomb structures, such as wing spoilers, fairings, flight controls, and landing gear doors, have thin face sheets which have experienced durability problems that could be grouped into three categories: low resistance to impact, liquid ingression, and erosion. These structures have adequate stiffness and strength but low resistance to a service environment in which parts are crawled over, tools dropped, and service personnel is often unaware of the fragility of thin-skinned sandwich parts. In-service defects include:
Environmental degradation
Impact damage
Fatigue
Cracks from local overload
Debonding
Delamination
Fiber fracturing
Erosion
Damages to these components, such as core crush, impact damages, and disbonds, are quite often easy to detect with a visual inspection due to their thin face sheets. However, they are sometimes overlooked or damaged by service personnel who do not want to delay aircraft departure or bring attention to their accidents, which might reflect poorly on their performance record. Therefore, damages are sometimes allowed to go unchecked, often resulting in the growth of the damage due to liquid ingression into the core. Nondurable design details (e.g., improper core edge close-outs) also lead to liquid ingression.
Damage and Defect Description
Defects and damage in structural components are common occurrences, whether they arise during material processing, component fabrication, or in-service action. The effect of the defect or damage on the composite component’s structural integrity is essential in understanding the criticality of the defect. The defects can be listed in terms of developing a common stress state. These common stress states are delaminations, transverse matrix cracks, holes or fiber fracture, and design variance

Composite Structure Repair Procedure

Advanced composite materials provide the necessary damage tolerance through relatively low, applied design strains. However, defects and damage still occur in composite materials, and it is the assessment of defect and damage criticality and the subsequent repair requirements that are currently challenging for operators of composite materials. When composite materials components are damaged or defective in some way, the engineer/technician needs to determine the size, shape, depth, type, and extent of the anomaly and restitution approach. A typical repair procedure is shown below
Locate the damaged area
Assess the extent of damage
Evaluate the stress state of the damaged area stress state
Design the repair scheme
Remove damage and repair structure
Fabricate and prepare the repair scheme
Apply the repair scheme
Conduct post-repair quality checks
Document repair procedures
Monitor the repair region
Of immediate importance is the ability to identify the damage and determine its extent by some suitable nondestructive inspection (NDI) technique. Most, if not all of the standard NDI techniques currently used require high levels of operator experience to successfully apply the NDI technique and interpret the results. This book is written to provide an in-depth study of defects and damage in composite materials. It is significantly focused on the defect and associated structural response to the presence of defects.
Virtual Production to Reduce the Defects and Damages
To reduce the defects and damages in composite materials and structures, Addcomposites introduces open access to our virtualized production software - AddPath as a solution for everybody to identify the possible faults and errors before the manufacturing process.
The video below is a simulation conducted to demonstrate how the tape will be placed and how it will behave while passing over a corner compared to the straight portion of geometry. A strategy optimized at these levels can be applied to much bigger shapes with similar shape features.
For more articles about Composites Manufacturing and Automated Fiber Placement (AFP), please visit our Blogs. If you have any questions, feel free to send us an email at info@addcomposites.com.
About Addcomposites
Addcomposites is the provider of the Automated Fiber Placement (AFP) ecosystem - including the Fiber Placement System (AFP-XS), 3D Simulation and Programming Software (AddPath), and Robotic Cells (AddCell). With the leasing program for the AFP system (AFPnext), composites manufacturers can work with thermosets, thermoplastics, dry fiber placement, or in combination with 3D Printers on a monthly basis.
Source:
Subscribe to our newsletter and get our guidebook - "Composites Manufacturing Methods: An Ultimate Guide for 2022"
Comments