Design and Development of Sustainable Compressed Hydrogen Storage Tank: Course
- Pravin Luthada
- Sep 21, 2022
- 6 min read
Updated: Apr 3, 2023
What's covered
This course aims to provide
An overview of the development perspective of hydrogen storage solutions.
Starting with highlighting the need for lighter and more reliable tanks.
Following up with the discussion on types of hydrogen tanks and their usage scenario.
Manufacturing of these tanks from traditional and upcoming new methods. A special section is dedicated to thermoplastic hydrogen tanks to highlight the sustainability aspect of the materials.

A selection guide to identifying the right liner, matrix, and fiber material are presented to provide an overview of the importance of each component.
Design-related methods for modeling the tank are summarized with essential tools and their limitation are covered. Special attention is dedicated to dome design and design process flow compared to detailed processes.
Towards the end, a full chapter is dedicated to Regulations, Codes, and Standards regarding the safe and reliable operation of hydrogen tanks. Special attention is paid to each sector's specific standards and main tests required for their certifications.
Key Takeaways from the author's point of view are highlighted towards the end.
Possible Learning
Why there is a need for lighter hydrogen tanks?
Why there are different types of hydrogen tanks? What are Type-I or Type-V tanks?
What are the present manufacturing methods for Hydrogen Storage Tanks?
How does selecting the right material impact the sustainability of Hydrogen Storage Tanks?

How does selecting the right manufacturing methods impacts the sustainability of Hydrogen Storage Tanks?
How to select Hydrogen Storage Tank Liners and overwrapping composites?
What are the safety considerations to be taken into account while designing the Hydrogen Tanks?
What testing standard to follow for Hydrogen Storage tanks for different types of vehicles?
What are the most common type of tests that a Hydrogen storage tank has to go under for getting safety approval?
Introduction
Hydrogen fuel cell technology is securing a spot in the future of advanced mobility and energy revolution, as engineers explore multiple avenues in the quest for decarbonization. The feasibility of hydrogen fuel cell vehicles specifically relies on the development of safe, lightweight, and competitive solutions for hydrogen storage. After demonstrating hundreds of vehicles, today commercial hydrogen tanks are in the early stages of market launch, adopting configurations using composite materials. However, the production rate is still low and the cost is high.
Jump directly to the right information
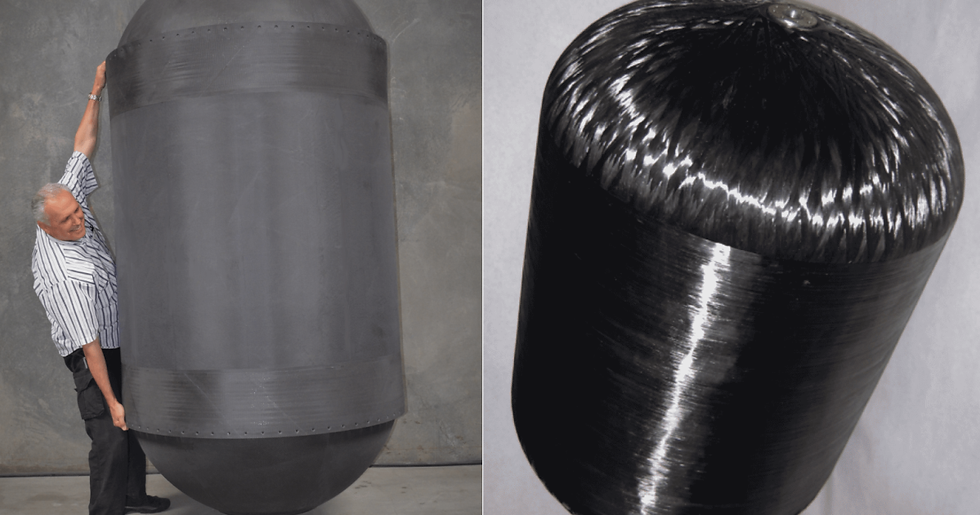
Hydrogen fuel cell technology is securing a spot in the future of advanced mobility and energy revolution, as engineers explore multiple avenues in the quest for decarbonization. The feasibility of hydrogen fuel cell vehicles specifically relies on the development of safe, lightweight, and competitive solutions for hydrogen storage. After demonstrating hundreds of prototype vehicles, today commercial hydrogen tanks are in the early stages of market launch, adopting configurations using composite materials. However, the production rate is still low and the cost is high.
2. What is a Hydrogen Tank & Tank-Types
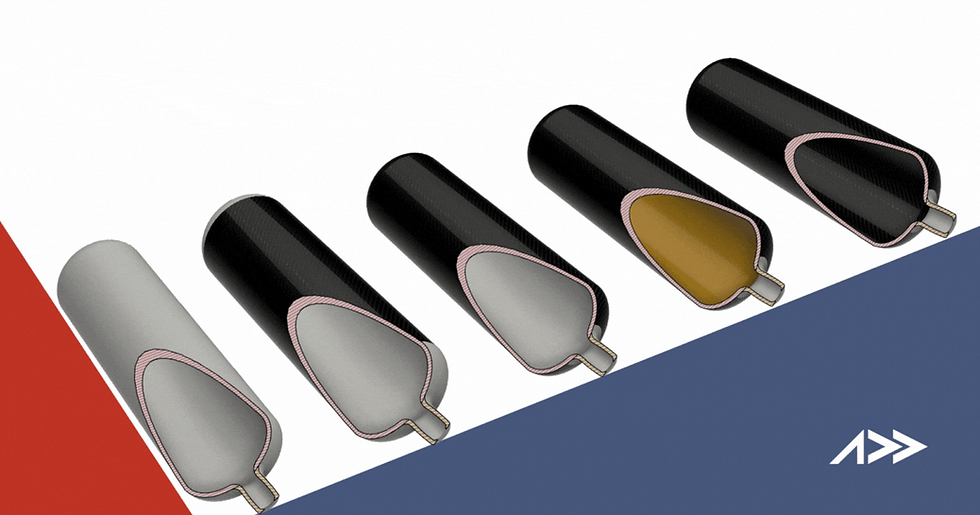
The article highlights the different types of hydrogen tanks and their capabilities. Highlighting specifics of why such tank classification exists in simplifying the terminology and benefits of the type of tanks' for particular applications.
3. Filament winding hydrogen tanks (Thermoset)

Production of hydrogen tanks has been done using wet/dry filament winding for many decades now. This article focuses on describing the filament winding with the Wet and Towpreg approach. Highlighting the benefits of each process.
4. Thermoplastic Tape Winding of Hydrogen Tank

Thermoplastic Tape Winding (TTW) is a highly automated process for manufacturing tubular-like fiber-reinforced thermoplastic composites such as flywheels and pipes. One of the crucial parameters in the TTW process is the temperature of the nip point at which the incoming prepreg tape is bonded with the substrate by a compaction roller.
5. Traditional Filament winding vs. Robotic Winding
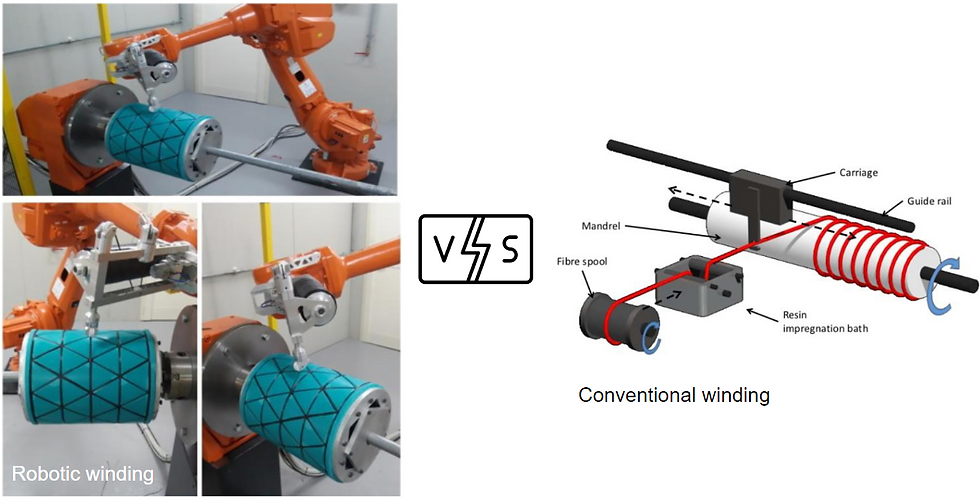
Traditional filament winding is a fairly common industrial low-tech process, limited to axially symmetric shapes such as tubes, ducts, or pressure vessels. The emergence of industrial robot technology has enabled the realization of novel winding approaches. In these methods, the fibers are either pulled off by the translation of a fiber guide around turning points or by the rotary motion of a mandrel about multiple axes instead of the traditional way of rotating about just one axis. The article covers a brief description of each winding approach with their pros and cons. towards the end hybridization trend is highlighted with AFP and CFRP 3D printing technology.
6. How to select the right Hydrogen tanks Liners, Metrix, and Fiber materials

Understanding the key requirements of hydrogen storage for a given application provides a good initial ground for configuring the overall design including the liner shape. This article covers Liners details from the perspective of hydrogen tank storage. Following it up with the over-wrapping of a linerless liner for novel applications. In addition, the liners and the overwrapping materials also affect the performance and sustainability aspects of the H2 tank production. The article dives into thermoset-thermoplastic materials and related challenges. In addition, the article discusses different reinforcements in the context of the application. A summary is presented as a TLDR for the article towards the end.
7. Optimal design for composite high-pressure hydrogen storage tank
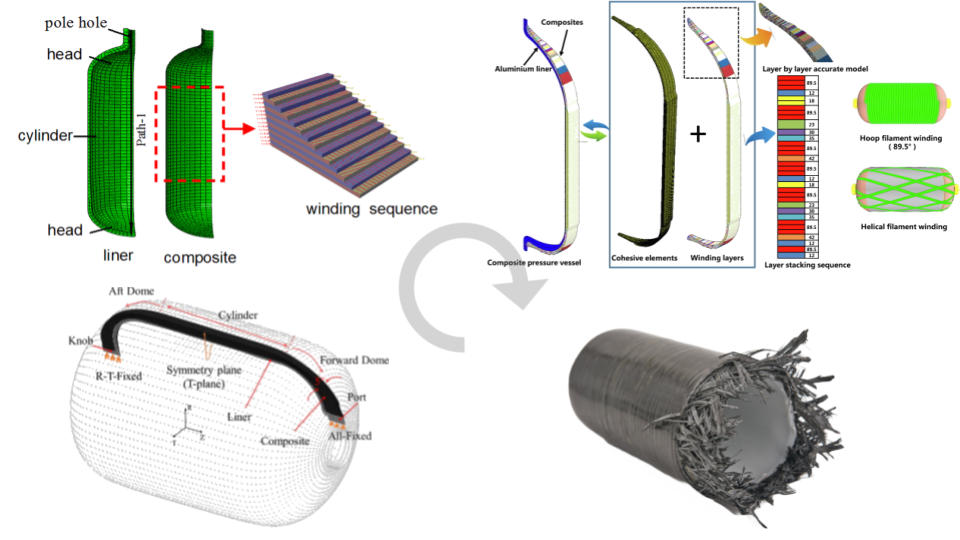
The article covers the design of composite vessels from the physical and mechanical aspects. The design heavily relies on the properties of materials to the geometry. The design cycle of hydrogen tanks begins with general characteristics, such as the tank capacity, working pressure, material attributes, and safety factors. followed by dome design and fiber placement orientation. The same finite element technique has been widely used to predict the failure properties and strengths of composites based on different failure modalities. The ultimate goal of all of these techniques is to arrive at a reliable burst pressure. ensuring the design conforms to the local authorities' standard, the burst pressure design has to be optimized for safety and reliability. The article leaves on a positive note by talking about the prospect of h2 vessels.
8. Hydrogen storage tanks: testing, certification, codes & standards

High-pressure tanks (250 bar) have been used safely in compressed natural gas vehicles for many years. Improved versions of these tanks made of high-strength composite materials are now used to store hydrogen at higher pressures (350 and 700 bar) to achieve a greater range in hydrogen-fueled mobility. High-pressure hydrogen tanks are designed not to rupture and are held to rigorous performance requirements. This article summarizes major regulations, codes, and standards in different aspects of hydrogen tank storage. The article further dives into the testing and certification process of hydrogen tanks.
Key takeaways
For manufacturers/ Designers focusing on being the preferred supplier of the tanks the weight of the tank compared with the cost of production becomes the most important driver of sales.
To further increase the service pressure of hydrogen tanks or to slightly decrease the weight, metallic cylinders can be wrapped with continuous fiber composites. different combination of cylinder and composites overwrap gives birth to Type of cylinder.
Production of hydrogen tanks is traditionally carried out using filament winding techniques. For sustainable tank production, Thermoplastic Tape Winding uses revolutionary heating technology to improve process control, and during its lifecycle, it produces fewer emissions than traditional process.
Selecting the liner or linerless design depends on the application temperature. Majority of the tank production today uses glass/carbon thermoset combination, however it is slowly changing towards glass/carbon thermoplastic.
The design heavily relies on the properties of materials to the geometry. The design cycle of hydrogen tanks begins with general characteristics, such as the tank capacity, working pressure, material attributes, and safety factors. followed by dome design and fiber placement orientation.
High-pressure hydrogen tanks are designed not to rupture and are held to rigorous performance requirements tested against major regulations, codes, and standards in different aspects. These guidelines and rules are constantly evolving and should be kept in check all time.
Comments