Designing and Optimizing Composite Structures for Automated Fiber Placement Processes
- Pravin Luthada
- Feb 16, 2023
- 10 min read
Updated: Apr 6, 2023
Introduction
In this article, we will explore the design and optimization of composite structures in automated fiber placement (AFP) processes. We will discuss the advantages and limitations of constant stiffness and variable stiffness design approaches, as well as design guidelines for optimizing composite structures for AFP production process. We will also cover various layup strategies, including reference curve strategies and coverage strategies, and the concept of coverage density in AFP production process.

In addition, we will delve into the importance of process parameters in ensuring good layup quality and the influence of speed, pressure, temperature, and tension on layup quality. We will also discuss the various defects that can occur during AFP and the importance of online defect detection techniques in ensuring good layup quality. Finally, we will review various methods for assessing the quality of AFP layups after the layup process is complete.
Jump right to the point

Designing Composite Structures with Constant and Variable Stiffness: Advantages and Limitations
Composite materials have a range of advantages, such as improved mechanical properties, corrosion resistance, fatigue life, and fracture toughness. However, careful design and optimization are required to fully utilize these benefits. There are two categories of composite structure design: constant stiffness and variable stiffness.
Constant stiffness design uses the same stacking sequence throughout the structure, while variable stiffness design involves changing the fiber angles across the structure to optimize performance. In industry, composite manufacturing is currently limited to using conventional constant stiffness laminates with fiber angles restricted to 0, ±45, and 90 degrees. There are also guidelines for laminate design to ensure robustness, including using symmetric and balanced laminates, limiting the maximum number of consecutive plies, limiting the maximum and minimum ply angle jump, and using ±45-degree surface plies.
Fiber steering capabilities can be used to increase design flexibility and create more efficient composite structures through variable stiffness laminates. However, there are constraints on these designs, including the minimum turning radius of fibers and continuity constraints.
Design Guidelines for Optimizing Composite Structures in Automated Fiber Placement Processes
This table summarizes common design practices for composite structures, including guidelines for balanced and symmetric laminates, ply angle jumps, surface plies, fabric layers, and ply drops to ensure structural integrity and optimize performance.

Design Practice: Employ balanced and symmetric laminates Effect: Minimizes [B] matrix, avoids bending, coupling, warping, and twisting effects |
Design Practice: Maximum number of consecutive plies Effect: Prevents delamination and residual stresses |
Design Practice: Maximum and minimum ply angle jumps Effect: Decrease inter-laminar stress and obtain dispersed laminates |
Design Practice: ±45-degree surface plies Effect: Increases damage tolerance, buckling load of thin laminates, and protects load-carrying plies from impacts |
Design Practice: Add fabric as inner and outer layers Effect: Absorbs impact damage and minimizes drilling “breakout” |
Design Practice: Pair +45- and -45-degree plies Effect: Minimizes inter-laminar shear and inplane shear is carried in tension and compression in the 45-degree layers. Use a larger fraction of +/- plies in shear regions. +/- piles are better at handling shear loads. |
Design Practice: Minimum steering radius Effect: Prevents fiber buckling and minimizes steering defects |
Design Practice: Ply drops Effect: Helps with laminate continuity |
Layup strategies
Layup strategies in composite manufacturing refer to the method by which fibers are laid down on a tool surface in order to create a composite structure.
Reference Curve Strategies in Automated Fiber Placement Processes
There are several strategies that can be used to create reference curves, which are the lines that guide the laying down of fibers. There are three main strategies for creating reference curves in automated fiber placement (AFP) processes:
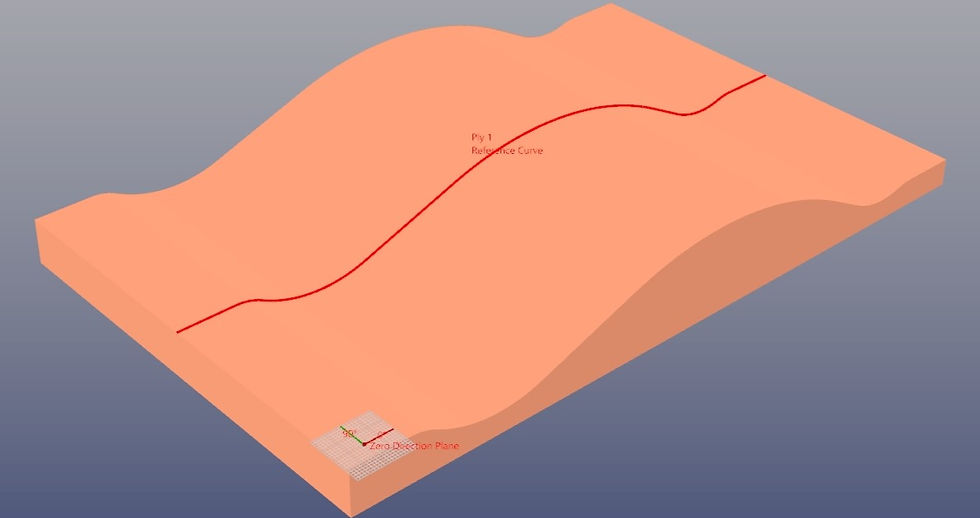
Fixed angle: This involves creating a curve from a given starting point that has a constant angle from a given axis or direction along the entire surface.
Geodesic: This method involves using the shortest possible line between two points on a curved surface, resulting in a straight line on a flat plate. The path can be obtained either by specifying a start point and a direction of travel or a start and end point on the surface, and the curve will follow the natural path of the surface.
Variable angle: This method involves varying the fiber orientation along the curve to create variable stiffness laminates. There are three main strategies for defining these reference curves: constant curvature, linear variation, and nonlinear variation. Each of these strategies uses a slightly different method to define the points and curves for layup trajectories.
Coverage Strategies in Automated Fiber Placement: An Overview
Coverage strategies are methods used to create course centerlines across a tool surface in automated fiber placement (AFP) processes. There are three main coverage strategies:

Independent curves: This method involves using independently drawn curves to cover the surface. It is often used on highly complex tool surfaces where it is possible to draw the courses in different directions with a constant length to limit gaps and overlaps. However, this method can be time-consuming and is not often used for conventional surfaces.
Offset or parallel curves: Tit is a common method for creating course centerlines in AFP processes. It involves creating adjacent curves from a reference curve to cover the entire surface. There are two approaches for defining these adjacent curves: a parametrical approach, which involves solving a system of equations numerically, and a mesh approach, which involves starting from a random reference curve on the mesh surface and using the Fast Marching Method to create the other courses. The advantage of this method is that the parallel curves are equidistant, preventing gaps and overlaps between courses. However, on complex surfaces, the fiber directions of the offset curves may vary from the reference curve and increased curvature may result in defects.
Shifted curves: This method involves shifting the reference curve by applying a translation in its perpendicular direction. The main advantage of this method is its simplicity in covering the surface with course centerlines. However, on complex surfaces, the fiber directions of the shifted paths may not be guaranteed, and there may be an increase in gaps and overlaps between courses.
Coverage Density in Automated Fiber Placement: Types and Considerations
Coverage density is a measure of the amount of fiber that is laid down on a surface in automated fiber placement (AFP) processes. It is usually expressed as a percentage of the surface area that is covered by fiber. There are two main types of coverage density:
![Coverage strategy illustration [3]](https://static.wixstatic.com/media/dfe896_3fa227abb8514b0597355bbc905297af~mv2.png/v1/fill/w_685,h_271,al_c,q_85,enc_avif,quality_auto/dfe896_3fa227abb8514b0597355bbc905297af~mv2.png)
Uniform coverage density: This involves laying down the same amount of fiber across the entire surface. It is often used in applications where the loads on the component are uniform.
Variable coverage density: This involves varying the amount of fiber laid down on different parts of the surface. It is often used in applications where the loads on the component are non-uniform, or where certain areas of the component require more strength or stiffness than others. Variable coverage density can be achieved by varying the width of the fibers, the overlap between fibers, or the number of layers of fiber.
![Edge Coverage strategy illustration [3]](https://static.wixstatic.com/media/dfe896_47a1ae821e164450a41b5e322bf0cc6b~mv2.png/v1/fill/w_980,h_254,al_c,q_85,usm_0.66_1.00_0.01,enc_avif,quality_auto/dfe896_47a1ae821e164450a41b5e322bf0cc6b~mv2.png)
By carefully choosing and optimizing layup strategies and controlling coverage density, it is possible to achieve a high-quality composite structure with minimal defects.
Importance of Process Parameters in Automated Fiber Placement Layup Quality: Speed, Pressure, Temperature, and Tension
Process parameters play a crucial role in determining the quality of the layup in automated fiber placement (AFP) processes. The choice of process parameters involves balancing layup quality and the high layup speeds demanded by the industry. Adequate process parameters are important in influencing the resulting mechanical properties of the composite part. Different process parameters, such as speed, pressure, temperature, and tension, can affect the layup quality in different ways

Influence of Speed on Layup Quality
The effect of speed on layup quality in automated fiber placement (AFP) processes is complex and depends on various factors. Generally, lower speeds result in longer thermal exposure which can improve polymer healing up until the applied temperature causes material degradation. However, higher speeds may result in less time for the compaction force and temperature to be applied to the material, leading to weaker cohesive forces and potentially lower layup quality. The optimal layup speed will depend on the specific materials and process conditions being used.
Role of Compaction Pressure in AFP Layup Quality
Compaction pressure is a major parameter that impacts the final quality of the layup in automated fiber placement (AFP) processes. The main concept of applying compaction pressure is to adhere the incoming tows to the substrate and remove voids. The pressure is critical in developing intimate contact between the plies, but excessive compaction can lead to material degradation. However, for thicker laminates, the influence of compaction pressure decreases significantly. It is important to find the right balance of compaction pressure to ensure good layup quality while avoiding material degradation.
The Role of Temperature in Automated Fiber Placement Processes: Effects on Interlaminar Strength, Material Degradation, and Layup Defects
The temperature is the main parameter responsible for the development of interlaminar strength in automated fiber placement (AFP) processes, as it helps create the optimal interface between incoming tows and the substrate.
Thermoplastic layup
The applied temperature heats the material above the melting temperature and is then consolidated by applying pressure, and solidifies as it cools. It is important not to have a processing temperature significantly above the material's melting temperature, as this can lead to material degradation. Deviation in temperatures across the part can also lead to non-uniform cooling rates, resulting in residual stresses and part deformation. Cooling rates also affect the degree of crystallinity, which can impact the mechanical properties of the material.
Thermoset Layup
The goal is not to reach the melting point but to achieve an appropriate level of tackiness. Tackiness is the key mechanism in the formation of most layup defects with thermoset materials and is most influenced by layup temperature. Higher tack is considered favorable to hold the prepreg on the tool surface and ensure adhesion to subsequent plies. However, excessive temperatures can lead to material degradation. The appropriate temperatures for either case are often determined through trial and error, but tack characterization can provide a good starting point for properly applied temperatures.
Importance of Process Parameters
process parameters play a crucial role in determining the quality of automated fiber placement (AFP) layups. Speed, pressure, temperature, and tension are all important factors that need to be carefully balanced to ensure good layup quality while avoiding material degradation. The optimal process parameters will depend on the specific materials and conditions being used and may require trial and error to find the right combination. Proper process parameter optimization can improve layup quality and result in composite parts with the desired mechanical properties.
Understanding and Classification of Defects in Automated Fiber Placement Processes
Automated fiber placement (AFP) is a complex manufacturing process that is prone to defects. These defects can have a significant impact on the performance of the resulting composite structure and can be caused by factors such as tool geometry, fiber steering, and material imperfections. Defects can be categorized into four main types: positioning defects, bonding defects, tow defects, and foreign bodies. Understanding the causes and effects of these defects is important in order to minimize their occurrence and ensure high-quality layups. In this section, we will provide a detailed discussion of four main types of defects, including gaps, overlaps, angle deviation, and steering, along with information on their anticipation, existence, significance, and progression. Visual models of each defect type are also provided to aid in understanding the geometrical aspects of each defect.
Gaps and overlaps
These defects occur when there is a misalignment between the incoming tows, resulting in gaps or overlaps on the layup surface. They can be caused by fiber steering or layup over complex surfaces. Gaps and overlaps can be sites for failure initiation and resin-rich areas, and can also cause wrinkling.
Twist
This defect is initiated by folding or rotation during bi-directional layups and can lead to an increase or decrease in local thickness.
Missing tow
This defect occurs when the material feeding is discontinued or the tack adhesion is insufficient, leading to local thickness variations and resin-rich pockets.
Boundary coverage
When the material cannot perfectly meet at the edge of the part, it can affect the shape of the part and create failure points if not trimmed.
Angle deviation
Incorrect roller coverage or small steering radii can cause angle deviation, resulting in overlaps and resin-rich areas.
Wandering tow
Unsupported portions of the tow between the roller and cutter can lead to gaps and overlaps
Position error
Obstruction of the tow during feeding, incorrect machine reference, or machine control issues can result in gaps and can be a site for failure initiation, especially when close to the boundary.
Folds
Tensioner errors, long or complex towpaths, or steered paths can cause folds, which have a significant influence on local fiber volume fraction and create resin-rich areas.
Puckers
Excess tow feeding can result in puckers, which can cause significant loss of strength.
Wrinkles
Tow placement at small steering radii can cause wrinkles, which can lead to gaps and folded tows and cause a loss of strength.
Bridging
Too much tow tension or insufficient tack adhesion can cause bridging, resulting in resin-rich areas and delamination.
Loose tow
If the length of the tow is shorter than the length between the roller and cutters, it can result in gaps/overlaps and missing tows.
Splice
When two tows are joined end to end during the slitting process, it can cause a local thickness change and be a site for failure initiation, particularly under compressive loads.
FOD (Foreign Object Debris)
Resin or fiber fuzz that collects on the head or other debris from the production area can cause improper adherence to the next ply.
Overview of Online Defect Detection Techniques in Automated Fiber Placement Processes: Advantages and Limitations
Online defect detection techniques are used to identify defects during the automated fiber placement (AFP) process in order to improve process reliability and reduce quality inspection efforts. These techniques include machine vision, digital image processing, thermographic monitoring, and optical sensors.
Laser Line Scanners
laser line scanner mounted on a robot or on an AFP head that can scan the projected laser line over the layup surface along a programmed path, which can determine the relative positions of neighbored courses and detect most visual defects e.g. Gaps, overlaps, FOD, etc.
Thermal Camera
Thermal cameras with image processing can analyze the visible temperature difference between the laid-up tow and its surface to identify surface defects such as gaps, overlaps, twisted tows, and bridging. However, this method cannot detect internal defects or their evolution in the laminates. Convolution neural networks (CNNs) are used to classify thermal images of CFRP materials, which can identify various prepreg materials and defects during the AFP process.
FBG
Optical fiber Bragg grating (FBG) sensors, can identify the type and size of defects by analyzing reflected wavelength changes. However, this method is not yet industrially applied and may not be suitable for detecting small, micro-scale defects.
Overall, online defect detection techniques in AFP processes offer various advantages such as improved process reliability, reduced inspection efforts, and the ability to detect different types of defects. However, each technique also has its own limitations, including the inability to detect certain types of defects or the need for specialized equipment.
Post-Layup Quality Assessment: Techniques and Measures
Quality assessment can be performed using several techniques, including:
Peel test: This test measures the interlaminar bond strength between layers in the layup.
Electric microscopy: This technique can be used to assess void content through a cross-section, as well as surface roughness.
X-Ray CT scan: This method allows for the assessment of void content throughout the entire laminate.
Short beam strength (SBS) test: This test measures the interlaminar bond strength between layers.
Double cantilever beam (DCB) test: Similar to the SBS test, the DCB test measures interlaminar bond strength between layers.
Conclusion
Design and process parameters play a crucial role in optimizing the performance of composite structures fabricated using automated fiber placement (AFP) processes. Constant stiffness and variable stiffness design approaches have their own advantages and limitations, and it is important to consider the specific requirements and limitations of the application when choosing the appropriate design approach. Process parameters such as speed, pressure, temperature, and tension also need to be carefully balanced to ensure good layup quality while avoiding material degradation. Defects can occur during the AFP process and can have a significant impact on the performance of the resulting structure. Online defect detection techniques can be used to monitor the layup process in real-time and improve the efficiency and reliability of the manufacturing process. Quality assessment techniques are also important for ensuring that the final composite structure meets the required mechanical and performance specifications.
Comments