Driving Forward with Composite Materials in Automotive Innovation
- Aditya Verma
- Feb 19, 2024
- 6 min read
TLDR
The Weight of Innovation - Tackling the Automotive Industry's Biggest Challenge
Feeling the Weight: The Pain Points of Traditional Automotive Manufacturing
Shifting Gears with Composite Materials: A New Approach to Automotive Manufacturing
Crafting the Future: Advanced Composite Manufacturing Techniques
The Weight of Innovation - Tackling the Automotive Industry's Biggest Challenge
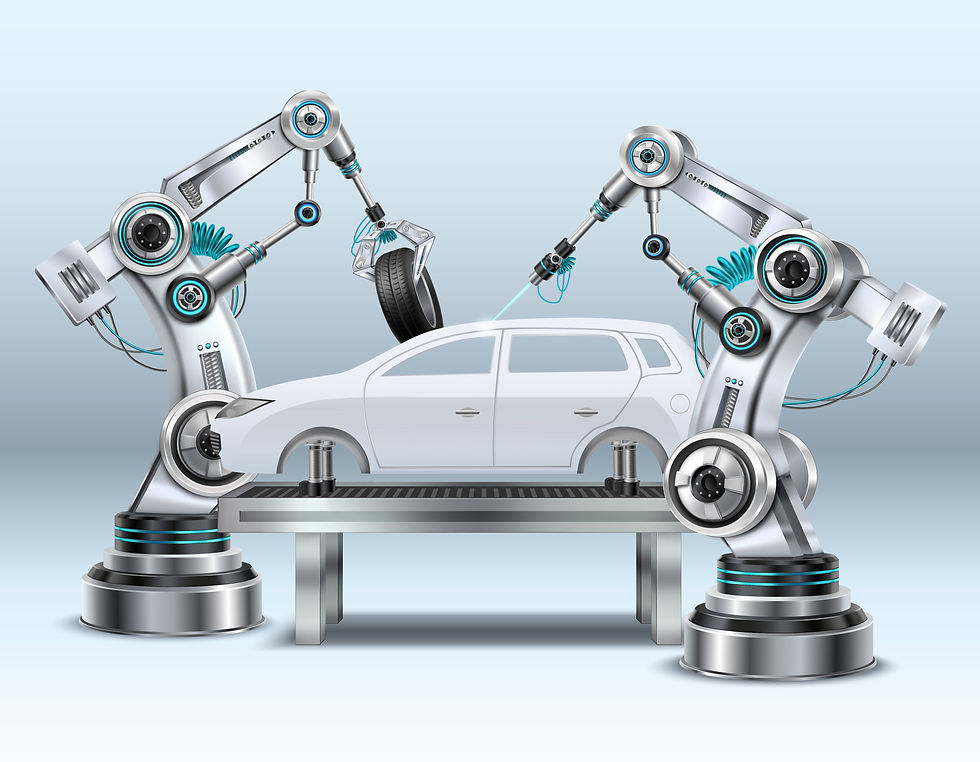
In recent years, the automotive industry has encountered a pivotal transformation driven by the dual pressures of environmental sustainability and technological advancement. The accelerating concerns over environmental pollution and global warming have heightened awareness and regulatory demands worldwide, urging industries, especially automotive, to innovate towards reducing carbon emissions. The transition from traditional internal combustion engine (ICE) vehicles towards electric vehicles (EVs) and the emerging concept of urban air mobility (UAM) epitomizes this shift. Central to this transformation is the adoption of composite materials, celebrated for their lightweight properties and superior mechanical performance, offering a promising avenue to enhance driving range and promote green mobility.
Despite the evident advantages, the mass adoption of composites faces significant hurdles. The balance between performance enhancements and cost implications poses a persistent challenge, hindering the widescale application of composite technology in mainstream automotive manufacturing. Economic factors, alongside the continuous evolution of environmental legislation, play crucial roles in the cautious approach adopted by automotive original equipment manufacturers (OEMs). This cautiousness, however, has not stalled innovation; recent developments have seen a focus on integrating biodegradable composites and leveraging robotic automation in manufacturing processes. These advancements aim at fostering eco-friendly, sustainable, and cost-effective production methodologies.
The blog outlines the automotive industry's journey through these challenges, spotlighting the pivotal role of composites in the quest for sustainability and efficiency. It delves into the latest applications of composite materials in modern vehicles, evaluating the state-of-the-art composite manufacturing and recycling processes. This exploration serves as a testament to the industry's commitment to green mobility, navigating through performance-cost trade-offs towards a sustainable automotive future.
The Pain Points of Traditional Automotive Manufacturing
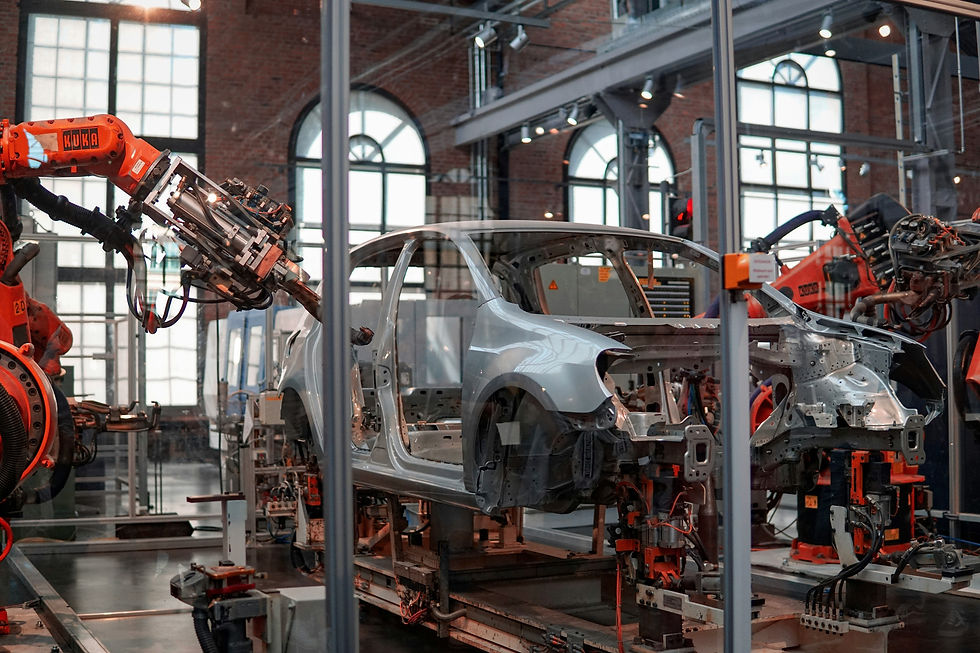
The automotive industry, at the intersection of innovation and tradition, faces formidable challenges in its quest for sustainability and efficiency. Traditional manufacturing methods and materials, while proven, are increasingly at odds with the pressing demands for environmental stewardship and performance optimization. This section delves into the core pain points that underscore the imperative for a paradigm shift.
Environmental Impact: Traditional automotive materials such as metals are not only heavy but also resource-intensive to produce and recycle. This contributes significantly to the carbon footprint of vehicles, exacerbating global warming and environmental pollution.
Weight Reduction Challenges: The quest for lighter vehicles clashes with the limitations of metal materials. While essential for structural integrity, metals add considerable weight, reducing fuel efficiency and driving range, especially critical for electric vehicles (EVs) and urban air mobility (UAM) platforms.
Manufacturing Complexity: Traditional materials often require complex, multi-step manufacturing processes. These processes are not only time-consuming and costly but also less adaptable to automation, hindering scalability and innovation.
Economic and Legislative Pressures: Amid tightening environmental regulations and the global push towards green mobility, automotive manufacturers grapple with the economic implications of transitioning to sustainable materials and processes. The initial higher costs and the performance-cost trade-offs of alternative materials like composites present significant barriers to mass adoption.
Recycling and Sustainability Concerns: The end-of-life recycling of traditional automotive materials poses yet another challenge. The process is often inefficient, with a significant portion of materials ending up in landfills, leading to environmental degradation and lost economic value.
A New Approach to Automotive Manufacturing
The automotive industry is at a critical juncture, seeking sustainable, efficient manufacturing methods without compromising performance. Composite materials, with their blend of lightweight properties and mechanical strength, emerge as the beacon of innovation in this landscape. This segment explores the transformative potential of composites, underscoring their role in navigating the industry towards a greener future.
Automated Lay-Up and Fiber Placement

Automated Lay-Up: Revolutionizes the placement of composite materials, enhancing precision and reducing labor costs. Key to manufacturing complex shapes, it sets a new standard in component fabrication.
Automated Fiber Placement (AFP): Offers unmatched accuracy in laying fibers, optimizing material usage and part performance. This technique is vital for producing high-strength components with intricate designs.
Advanced Molding Techniques
Resin Transfer Molding (RTM): A game-changer for creating complex shapes with superior finish and strength. Its cost-effectiveness and scalability make it a preferred method for automotive parts.
Compression Molding: Offers a fast, efficient process for high-volume production, suitable for a wide range of components from body panels to structural parts.
Pultrusion for Linear Components
Pultrusion: Known for its efficiency in producing linear, constant cross-section profiles. This process has been refined to create automotive parts like bumper beams and chassis rails, offering a blend of strength, lightweight, and cost-efficiency.
Additive Manufacturing: A Complementary Technique
3D Printing: Brings design freedom and customization to the forefront, allowing for the creation of complex components that would be challenging or impossible with traditional methods. Although not a replacement for mass production techniques, it serves as a complementary method for specialized, low-volume parts.
The Promise of Automation and Robotics
The integration of robotics into composite manufacturing promises a leap in production efficiency and a reduction in costs. Robotic automation in processes like filament winding and automated lay-up is paving the way for increased adoption of composite materials in mainstream automotive manufacturing. These technologies not only enhance production speed and flexibility but also open the door to innovative designs and applications.
Advanced Composite Manufacturing Techniques
The advancement of composite manufacturing techniques represents a cornerstone in the automotive industry's evolution, pushing the boundaries of performance, sustainability, and cost-effectiveness. This section delves into the innovative manufacturing processes that enable the integration of composite materials into automotive applications, spotlighting their contributions to the industry's future.
Automated Composite Manufacturing Techniques
Automated Fiber Placement (AFP) and Automated Tape Laying (ATL): AFP and ATL techniques offer precise control over fiber placement, optimizing the structural performance of composite parts and enabling the production of complex geometries with high efficiency.
Resin Transfer Molding (RTM): RTM has emerged as a pivotal process for manufacturing high-performance composite parts, offering cost-effectiveness alongside superior part quality. Variants like Low-Pressure RTM (LP-RTM), High-Pressure RTM (HP-RTM), and Compression RTM (C-RTM) further refine this process, balancing cycle times, costs, and mechanical properties to meet diverse application requirements.
Robotics in Composite Manufacturing
The integration of robotics into composite manufacturing, particularly in processes like AFP, ATL, and RTM, enhances precision, reduces labor costs, and increases production scalability. This automation is crucial for meeting the automotive industry's demands for high volume and consistent quality in composite part production.
Challenges and Developments
While these advanced manufacturing techniques offer significant advantages, they also present challenges such as the need for high initial investments and the management of complex process parameters. However, continuous innovation and the development of cost-efficient processes like C-RTM demonstrate the industry's commitment to overcoming these barriers.
The Path Forward
As the automotive industry continues to evolve, these advanced composite manufacturing techniques stand at the forefront of the transition to green mobility. By leveraging automation, innovative molding processes, and the strategic application of robotics, the industry is poised to achieve unprecedented levels of efficiency, sustainability, and performance.
References
Let's extend our heartfelt appreciation to the authors for their significant contributions to the comprehensive study on composite manufacturing processes for future mobility. Their dedication and expertise have provided invaluable insights into this critical area, shaping the narrative of our blog post. A special thank you to:
Jun Young Choi
Ji Ho Jeon
Jang Hyeon Lyu
Jungwoo Park
Geun Young Kim
Suk Young Chey
Ying‑Jun Quan
Binayak Bhandari
B. Gangadhara Prusty
Sung‑Hoon Ahn
Your collective efforts have not only advanced the field of composite manufacturing but also highlighted the potential of these materials in enhancing the sustainability and efficiency of future mobility solutions. Your work serves as a foundation for ongoing and future innovations in the automotive industry. Thank you for your invaluable contributions!
What's Next!

Discover the future of composite manufacturing with Addcomposites! Here's how you can get involved:
Stay Informed: Subscribe to our newsletter to receive the latest updates, news, and developments in AFP systems and services. Knowledge is power, and by staying informed, you'll always have the upper hand. Subscribe Now
Experience Our Technology: Try our cutting-edge simulation software for a firsthand experience of the versatility and capability of our AFP systems. You'll see how our technology can transform your production line. Try Simulation
Join the Collaboration: Engage with us and other technical centers across various industries. By joining this collaborative platform, you'll get to share ideas, innovate, and influence the future of AFP. Join Collaboration
Get Hands-On: Avail our educational rentals for university projects or semester-long programs. Experience how our AFP systems bring about a revolution in composite manufacturing and leverage this opportunity for academic and research pursuits. Request for Educational Rental
Take the Next Step: Request a quotation for our AFP systems. Whether you're interested in the AFP-XS, AFP-X, or SCF3D, we are committed to offering cost-effective solutions tailored to your needs. Take the plunge and prepare your production line for the next generation of composite manufacturing. Request Quotation
At Addcomposites, we are dedicated to revolutionizing composite manufacturing. Our AFP systems and comprehensive support services are waiting for you to harness. So, don't wait – get started on your journey to the future of manufacturing today!
Comments