Hand layup: understanding the manual process
- Pravin Luthada
- Aug 5, 2021
- 3 min read
Updated: Nov 16, 2021
Overview
The hand layup of pre-impregnated woven materials is still a large part of the composite manufacturing industry, requiring the skills and experience of a human workforce to form flat plies into complex shapes. It is capable of producing high-performance and complex parts but can be an expensive and variable process. The actual methods and techniques used by workers to manipulate flat sheets of composite material into shape during layup are described in this article.
Techniques
One-handed guiding
One hand holds the prepreg securely onto the mold surface while the other hand is used to grasp the ply and move it in order to align it with a datum on the mold surface, as can be seen in Figure. Once aligned, the grasping hand generally lowered the prepreg onto the mold surface, and then both hands were used to stick it down.

Corner consolidation methods (Top) participant using fingernails to get prepreg into the corner, (Bottom) participant using dibber tool
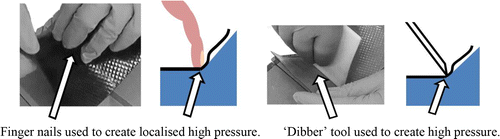
Two-handed guiding
Both hands grasp the ply in order to position the ply on the mold. Often one or both hands then stick the prepreg to the surface once it is aligned. This can also be used to ‘shape’ the ply to fit in or around a mold, as can be seen in the Figure below.
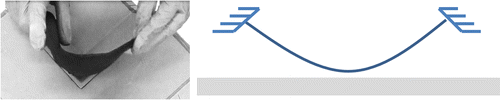
Manual folding
One or both hands are used to manipulate the prepreg out-of-plane in order to create organized and manageable folds in the prepreg, often to deal with a material excess in the prepreg, as seen in the Figure below
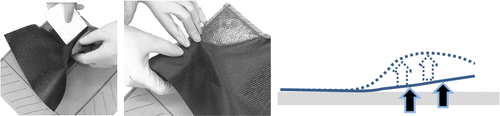
Hoop shearing
Fingers, thumbs, or other molds are arranged into a single curved front, which is slowly moved across a region of prepreg, sticking it to the mold while also creating a ‘hoop’ stress in the folded region of the material, which in turn creates shear. The figure below (A, B) shows two examples of Hoop shearing using either fingers or thumbs to form a single front, C schematic of the Hoop shearing technique from the side view, D schematic of the Hoop shearing technique from the top view
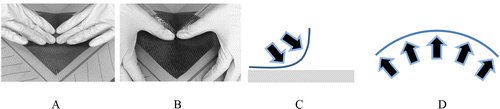
Double-tension shearing
Both hands grasp the reinforcement at two separate locations, which are along a line ± 45° to the fiber directions and apply tension in opposing directions to create shear, as shown in the figure below

Tension-secured shearing
One hand grasps the prepreg and applies tension in order to create shear, while the other hand secures the prepreg to the mold surface in order to prevent slippage, as seen in the figure below. Once shear is created, the ply is either released or lowered onto the mold surface to be stuck down.
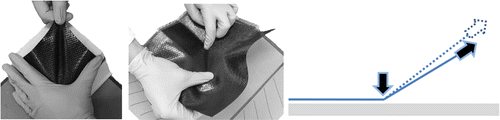
Tension and sticking
The same as tension-secured shearing but the securing hand slides along the ply, sticking down the prepreg at the same time as shearing, as seen in the figure below

Mold interaction shearing
The ply is pushed into a recessed region of the mold, which creates sufficient tension in the ply to create the required shear deformation, as seen in the figure below

Summary
The hand lay-up techniques described here do provide the complete picture but gives a general idea about the process and how to interact with different geometry while draping the given prepreg.
About Addcomposites
Addcomposites is the provider of the Automated Fiber Placement (AFP) system. The AFP system can be rented on a monthly basis to work with thermosets, thermoplastic, dry fiber placement, or in combination with 3d printers.
Comments