How To Make Aerospace Manufacturing 10x Better! The Mind-Blowing Method 🤩🛠️
- Pravin Luthada
- Feb 11, 2024
- 8 min read
TLDR
Introduction to CFRP: Carbon Fiber Reinforced Polymers (CFRP) are increasingly used in aerospace for their strength and lightweight properties, but present design and manufacturing challenges.
Pain Points Identified: Manual, time-consuming planning and complex interdependencies in aerostructure manufacturing highlight the need for streamlined operations.
Novel Model-Driven Method: Introduces a graph-based design language and model transformations to integrate design and process planning, enhancing automation and efficiency.
Automating Manufacturing: Demonstrates through a case study how automated process models optimize manufacturing sequences, reduce errors, and improve lead times and resource allocation.
Future of Aerospace Manufacturing: Encourages the adoption of model-driven strategies for scalable, adaptable, and environmentally friendly manufacturing, promising significant efficiency gains and innovation in the industry.
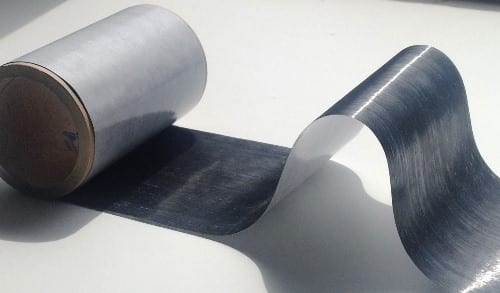
The Rising Role of CFRP in Aerospace and the Integration Dilemma
The aerospace industry is increasingly relying on CFRP for constructing modern aircraft, thanks to CFRP's advantageous properties. This trend is evident in the extensive use of CFRP in aircraft like the Boeing 787, Airbus A350, and Airbus Helicopters H145. However, the integration of CFRP poses significant challenges in design and process planning due to the complex nature of aerostructure manufacturing.
CFRP processing technologies vary widely, each with its unique limitations on part design and manufacturing. These technologies range from infusion and prepreg processes for thermoset composites, which are prevalent in aerospace, to emerging thermoplastic composite processes. The choice of technology affects automation levels, investment, and operational costs, making the selection critical to economic viability.
The development of aerostructures is further complicated by intricate interdependencies between design, material selection, and manufacturing technology. This complexity necessitates an upfront definition of materials and manufacturing processes before the final design can be determined. The traditional sequential product development approach, where manufacturing decisions are made post-design, is thus inadequate. Instead, a more integrated and iterative approach to design and manufacturing is essential, highlighting the need for automation and optimization in the planning stages.
This paper proposes a model-driven approach to address these challenges, utilizing a graph-based design language for integrated design and process planning. This approach aims to automate the generation of process models, optimize manufacturing sequences, and ultimately reduce production lead times for complex fiber composite structures, offering a significant step forward in the integrated product development and design optimization of fiber composite aerostructures.
Identifying the Pain Points: "Navigating the Complexities of Aerostructure Manufacturing"

The manufacturing of aerostructures, especially when involving CFRP, presents a plethora of challenges that significantly impact the design and planning processes. The core issues stem from the manual, labor-intensive efforts required to navigate these complexities, underscoring an urgent need for more streamlined operations.
Key Challenges in Aerostructure Manufacturing:
Diverse Processing Technologies: The wide array of CFRP processing technologies, each with its unique implications on design, manufacturing automation levels, investment, and operational costs, complicates the selection process. This diversity demands a high level of expertise to choose the most economically viable technology.
Complex Interdependencies: There are intricate interdependencies between the structure design, materials, and manufacturing technology. These relationships necessitate an integrated approach to design and manufacturing, where decisions on materials and processes must be made upfront, rather than sequentially. This significantly slows down the design process and increases the potential for errors.
Need for Iterative Design Loops: Given the complex interdependencies, the design and manufacturing process of a component requires multiple iterative design loops. This iterative nature is time-consuming and can be highly inefficient without automation.
Automation and Optimization Needs: The efficiency of the design process can be greatly improved through automation, specifically by automating the forward path of product development. However, current methodologies are limited in their ability to handle the complexity and requirements of aerostructure manufacturing, particularly in automating process planning and optimizing manufacturing sequences.
Limitations and Needs:
Integrated Design and Manufacturing: The traditional sequential product development approach is inadequate for aerostructure manufacturing due to the early need to define materials and manufacturing processes. An integrated and iterative approach is essential but currently lacks sufficient automation and optimization tools.
Automation in Process Planning: While there are methodologies for automating parts of the product development process, such as graph-based design languages, these have not been fully exploited in the context of aerostructure manufacturing. There's a significant gap in tools that can automate and optimize the entire process from design through to manufacturing planning and scheduling.
Optimization of Manufacturing Sequences: The optimization of manufacturing sequences, crucial for reducing production lead times and costs, is not fully addressed in current methodologies. This optimization is essential for managing the limited resources and constraints inherent in aerostructure manufacturing.
A Novel Approach: "Introducing a Model-driven Method for Aerostructure Design and Planning"
The development and manufacturing of aerostructures, particularly when involving complex materials like CFRP, necessitate a paradigm shift towards more integrated and efficient processes. Addressing this need, a novel model-driven approach has been formulated, leveraging graph-based design languages and model transformations to seamlessly integrate design and process planning.
Core Components of the Approach:
Graph-Based Design Language: At the heart of this model-driven approach is the implementation of a graph-based design language, where models are conceptualized as semantic graphs. This allows for the structured representation of design and manufacturing processes, making them amenable to automation and optimization.
Model Transformations: Central to this methodology are model transformations, facilitated through graph transformation rules. These transformations enable the conversion of design models into process planning models, encompassing manufacturing tasks, requirements, and resource allocation.
Design to Production Sequence Mapping: This involves mapping the product structure directly to a production sequence, ensuring that design intricacies are accurately reflected in the manufacturing plan.
Specialization of Process Planning: Abstract process planning models are specialized to detail required resources and zones, facilitating precise planning of manufacturing steps.
Cycle Time Estimation Models: For each task within the process plan, cycle time estimation models are generated, providing a basis for effective scheduling and resource allocation.
Optimization and Analysis: With the transformation from design to detailed process plans, the approach enables the application of optimization algorithms. These algorithms aim to identify the most efficient manufacturing sequence by considering constraints such as resource limitations and production timelines.
Integrated Scheduling Algorithm: An integral part of this approach is the scheduling algorithm, which optimizes the manufacturing sequence. This is crucial for managing the complexities and constraints inherent in the production of fiber composite aerostructures.
Automation and Efficiency: By automating the forward path from design to process planning, the approach significantly enhances efficiency. It reduces the iterative loops traditionally needed to refine the design and manufacturing plans, thereby minimizing errors and lead times.
Implementation and Tools:
The approach is implemented using the Design Cockpit tool suite, which supports the creation and manipulation of graph-based models. This environment facilitates the application of the model-driven paradigm, from the definition of class models and object models to the execution of model transformations.
Automating Aerostructure Manufacturing with Model-Driven Engineering
The model-driven approach to aerostructure manufacturing automation represents a leap forward in the design and production of complex structures, particularly those involving CFRP. Through the utilization of graph-based design languages and model transformations, this method offers significant advancements in efficiency, optimization, and error reduction. A case study involving the design and planning of an aerostructure showcases the tangible benefits of this approach.
Case Study Highlights:
Automated Process Planning: For a composite aerostructure, the model-driven approach enabled the automated creation of process plans. This was particularly evident in the manufacturing of components using a thermoset 3D automated fiber placement process, where both robot-based bonding and bolting, including tolerance compensation, were utilized.
Efficiency and Optimization: The approach facilitated the analysis of arbitrary designs against production characteristics, significantly streamlining the planning phase. The design graph of an aircraft shell, for instance, could be automatically converted into a detailed process plan, including tasks for manufacturing composite single parts and assembling them into a cohesive structure.
Error Reduction: By generating cycle time estimation models for each task, the approach ensures accurate scheduling and resource allocation, thereby minimizing potential errors and inefficiencies in the manufacturing process.
Key Results:
Automated Computation and Evaluation: The implementation allowed for the automated computation and evaluation of production scenarios, with the total manufacturing and assembly time estimated at 101.1 hours for a specific design case.
Optimized Process Schedule: By applying a scheduling algorithm, the approach successfully minimized lead time, achieving a substantial reduction from the initial estimate to an optimized lead time of 38.1 hours.
Resource Dimensioning Optimization: Further optimization was achieved through resource dimensioning, where Bayesian optimization techniques were utilized to balance resource costs against lead time, ultimately reducing the lead time by an additional 5 hours.
Implementation and Tools:
The methodology was implemented using the Design Cockpit tool suite, supporting the creation and manipulation of graph-based models. This integrated development environment allowed for the application of model-driven paradigms, from class and object modeling to the execution of model transformations and optimizations.
The Future of Aerospace Manufacturing: Embracing Model-Driven Strategies
The culmination of the research into a model-driven approach for the design and process planning of fiber composite aerostructures marks a significant step forward in aerospace manufacturing. By integrating design and process planning into a cohesive, graph-based design language workflow, the approach not only streamlines production but also paves the way for the incorporation of new manufacturing technologies and optimization techniques. This integration is instrumental in generating tasks, zones, and resources of the process plan, enhancing the efficiency and flexibility of manufacturing operations.
Highlights of the Approach:
Scalability and Adaptability: The model-driven approach demonstrates exceptional scalability, enabling the generation of comprehensive process plans for entire airframes based on preliminary design. This adaptability extends to incorporating new composite manufacturing and assembly technologies, further broadening its applicability.
Technological Advancements: Future enhancements could see the inclusion of additional composite manufacturing technologies, such as thermoplastic process routes and advanced assembly technologies like welding. These advancements promise to further refine the production of next-generation aerostructures.
Enhanced Precision and Efficiency: Ongoing development of more precise time estimation models, based on physical process simulations, and the scalability of scheduling and resource dimensioning algorithms, promise to tackle larger assemblies more effectively. This will likely reduce optimization complexity and improve overall manufacturing efficiency.
Environmental Considerations: An exciting avenue for future research is the computation of additional metrics, such as the environmental footprint of production. This aligns with the increasing emphasis on sustainable manufacturing practices and could contribute significantly to the development of eco-friendly aerospace components.
Reference
A big thank you to the authors Maximilian Holland, Nathalie Paul, Christian Linder, Hossam Elsafty, Gunar Ernis, and Steffen Geinitz for their significant contributions to the blog "MODEL-DRIVEN APPROACH FOR INTEGRATED DESIGN AND PROCESS PLANNING OF FIBER COMPOSITE AEROSTRUCTURES." Their work is paving the way for groundbreaking advancements in aerospace manufacturing, specifically in the efficient design and production of fiber composite aerostructures. Their affiliations with the prestigious Fraunhofer Institute and the University of Bonn highlight the depth of research and expertise involved in developing this innovative approach. Your dedication and effort in pushing the boundaries of aerospace engineering are truly appreciated. Thank you for your invaluable contributions to the field!
What's Next!
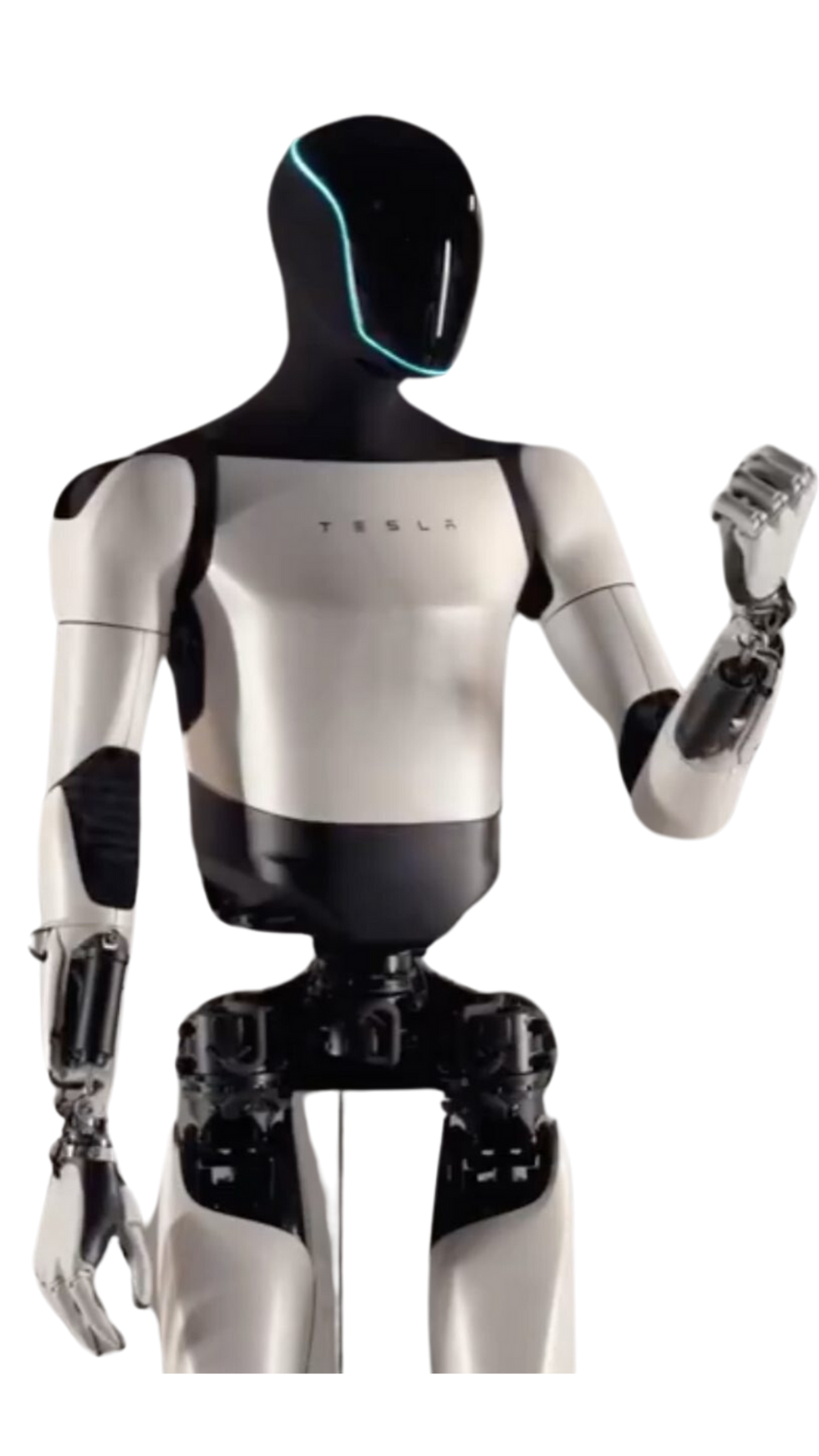
Discover the future of composite manufacturing with Addcomposites! Here's how you can get involved:
Stay Informed: Subscribe to our newsletter to receive the latest updates, news, and developments in AFP systems and services. Knowledge is power, and by staying informed, you'll always have the upper hand. Subscribe Now
Experience Our Technology: Try our cutting-edge simulation software for a firsthand experience of the versatility and capability of our AFP systems. You'll see how our technology can transform your production line. Try Simulation
Join the Collaboration: Engage with us and other technical centers across various industries. By joining this collaborative platform, you'll get to share ideas, innovate, and influence the future of AFP. Join Collaboration
Get Hands-On: Avail our educational rentals for university projects or semester-long programs. Experience how our AFP systems bring about a revolution in composite manufacturing and leverage this opportunity for academic and research pursuits. Request for Educational Rental
Take the Next Step: Request a quotation for our AFP systems. Whether you're interested in the AFP-XS, AFP-X, or SCF3D, we are committed to offering cost-effective solutions tailored to your needs. Take the plunge and prepare your production line for the next generation of composite manufacturing. Request Quotation
At Addcomposites, we are dedicated to revolutionizing composite manufacturing. Our AFP systems and comprehensive support services are waiting for you to harness. So, don't wait – get started on your journey to the future of manufacturing today!
Comments