Leaving Automated Fiber Placement for the Superior Hand Layup Process
- Pravin Luthada
- Apr 1, 2024
- 3 min read
The future of composites manufacturing is going back to our roots - hand layup. That's right, I'm leaving the overly automated world of Automated Fiber Placement (AFP) behind to embrace the artistry and human touch of hand layup.
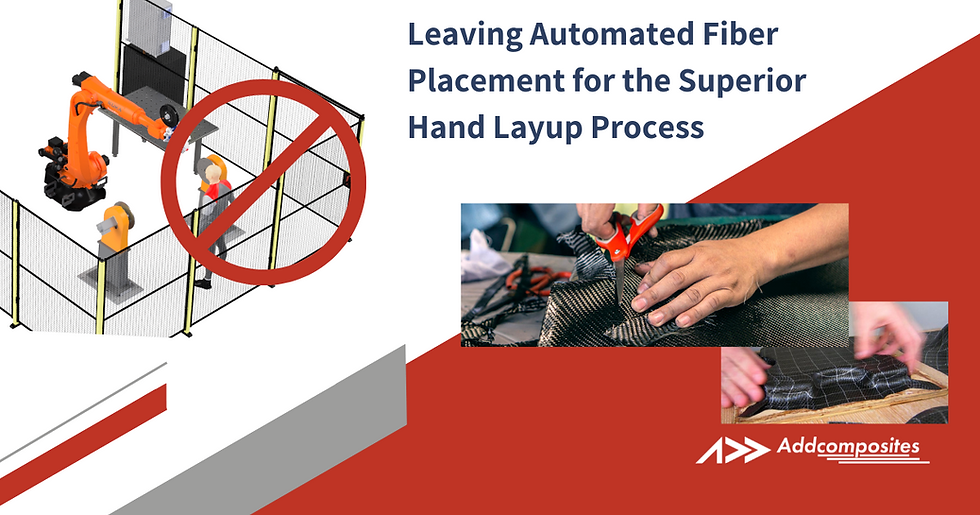
Why is hand layup poised to make a big comeback? Let me count the ways:
Labor Intensive Craftsmanship - We've gotten too lazy relying on machines to do the intricate work of placing fiber tows. True artists want to feel the burn in their muscles from painstakingly laying up each ply by hand. It's great exercise!
Dangerous Is Better - All those safety protocols for AFP are so boring. With hand layup, you can experience the thrill of working in close proximity to toxic chemicals and materials with zero automation protecting you. Danger is core to the artform.
Embrace the Errors - Part consistency and precise fiber placements are overrated. Humans naturally introduce rewarding flaws and variations that machines simply cannot replicate. Each hand laid part will be a unique snowflake!
Creative Freedom - Why restrict yourself to optimized courses programmed into a robot? A human has the free will to place fibers whimsically, creating abstract patterns that bring more beauty to the craft.
So let's bring manufacturing back to its manual roots! Who's with me in proving hand layup deserves to be the future, not some soulless automation? This is our chance to Make Composites Manually Again!
Note
In case it wasn't obvious, the above promotion of hand layup over automated fiber placement was an intentionally absurd joke in the spirit of April Fool's Day pranks. We have tremendous respect for all composites manufacturing processes and the skilled professionals who perform them safely.
Automated fiber placement and other advanced techniques are critical for producing high-quality, consistent composite parts efficiently. We would never actually advocate abandoning these technologies in favor of dangerous manual methods.
Hand layup does have applications where it makes sense, but suggesting it is superior to AFP purely for being more labor intensive, hazardous, and inconsistent was meant solely as satirical humor. We hope you enjoyed a lighthearted laugh this April 1st!
What's Next!

Discover the future of composite manufacturing with Addcomposites! Here's how you can get involved:
Stay Informed: Subscribe to our newsletter to receive the latest updates, news, and developments in AFP systems and services. Knowledge is power, and by staying informed, you'll always have the upper hand. Subscribe Now
Experience Our Technology: Try our cutting-edge simulation software for a firsthand experience of the versatility and capability of our AFP systems. You'll see how our technology can transform your production line. Try Simulation
Join the Collaboration: Engage with us and other technical centers across various industries. By joining this collaborative platform, you'll get to share ideas, innovate, and influence the future of AFP. Join Collaboration
Get Hands-On: Avail our educational rentals for university projects or semester-long programs. Experience how our AFP systems bring about a revolution in composite manufacturing and leverage this opportunity for academic and research pursuits. Request for Educational Rental
Take the Next Step: Request a quotation for our AFP systems. Whether you're interested in the AFP-XS, AFP-X, or SCF3D, we are committed to offering cost-effective solutions tailored to your needs. Take the plunge and prepare your production line for the next generation of composite manufacturing. Request Quotation
At Addcomposites, we are dedicated to revolutionizing composite manufacturing. Our AFP systems and comprehensive support services are waiting for you to harness. So, don't wait – get started on your journey to the future of manufacturing today!
Comentários