Lightweight Electric Motor Design: Paving the Way for the Next Generation of Electric Vehicles
- Pravin Luthada
- Aug 13, 2023
- 10 min read
Updated: Aug 16, 2023
Imagine an electric vehicle that not only matches the range of traditional gasoline cars but significantly surpasses them. Or an EV that accelerates twice as fast as the fastest internal combustion engine vehicle on the market. Sounds too good to be true? The secret might not be where you think.
While most discussions focus on battery technology, there's another silent revolution happening: the weight of the electric motor. Did you know that by simply reducing the weight of specific motor components, we can drastically increase an EV's range and performance? A hybrid shaft that's 50% lighter than its conventional counterpart, a magnet carrier weighing less than half a kilogram, and protective sleeves that are thinner yet more efficient than ever before.
Dive into our latest article, 'Innovative Approaches to Lightweight Electric Motor Design,' and discover how these cutting-edge methods are not just reshaping motors but redefining the very potential of electric vehicles
Credit: We would like to express our deepest gratitude to the authors of the article "Lightweight Design and Manufacturing of Composites for High-performance Electric Motors". The authors, Simon-Frederik Koch, Manuel Peter, and Jürgen Fleischer, affiliated with the Karlsruhe Institute of Technology, have delved into innovative approaches for reducing the weight of electric motor rotors. They explored the design and manufacturing of a hybrid shaft made of carbon-reinforced plastic and stainless steel, as well as the use of soft magnetic compounds (SMC) in a unique two-component injection molding process. Their research contributes to the understanding of these methods' potential applications in electric vehicle motors and other high-performance industries. Their work has significantly contributed to the following blog.
1. Introduction
Global Shift to Green Mobility:
The world is witnessing a significant transition in propulsion systems, moving from traditional combustion engines to electric motors. This change is driven by the increasing global demand for carbon-saving solutions and the push for green mobility.
Challenges with Current Electric Motors:
As we stand today, battery capacities remain limited, necessitating improvements in the range of automotive vehicles. This brings to the forefront the need for high-performance electric motors that are not only energy-efficient but also lightweight.
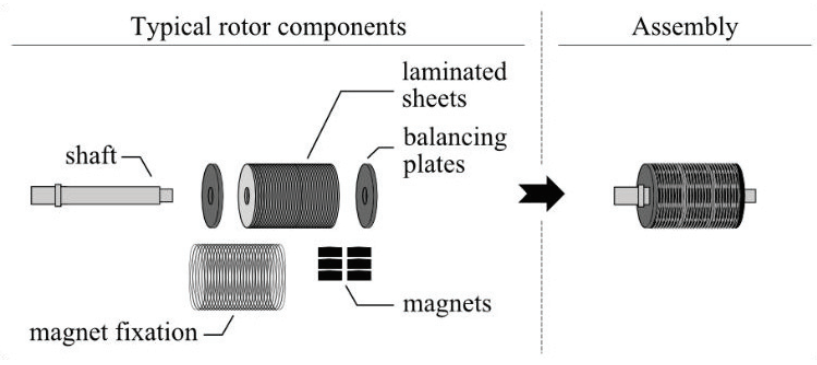
The Role of Lightweight Technology:
One of the promising avenues to address these challenges is the integration of lightweight technology. Fiber-reinforced plastics, especially carbon fiber-reinforced plastics (CFRP), present a significant opportunity. These materials can substantially reduce the weight of electric drive trains while simultaneously enhancing their electrical and mechanical properties.
The objective of Weight Reduction:
For electric traction drives, which are commonly found in cars, robots, and other platforms, the goal extends beyond just reducing weight. There's a specific emphasis on decreasing the rotor’s mass inertia. By achieving this, we can realize higher accelerations, which in turn positively impact the dynamics or productivity of the system.
2. The Weight Challenge in Electric Motors
Main Components Contributing to Weight:
Rotor Shaft: This component alone accounts for approximately 30% of the total rotor weight. Typically manufactured from solid metal, its weight is primarily due to the dense material used, which is steel with a density of approximately 7850 kg/m³.
Laminated Magnet Carrier: This is a significant component, representing about 61% of the rotor's total weight. The weight primarily stems from the electric sheets used in its assembly, which have a high magnetic permeability and a density of around 7600 kg/m³.
Metal Rotor Sleeve: Traditional rotor sleeves, made from steel or other metals, add significant weight to the motor. These sleeves, while providing necessary protection and structural support, contribute to the overall weight challenge of the electric motor. Their metallic nature also has implications for the motor's electromagnetic efficiency.

The Implications of Weight:
Performance Impact: The weight of the rotor's components, especially the rotor shaft, magnet carrier, and metal rotor sleeve, directly influences the performance of the electric motor. A heavier rotor can limit the motor's acceleration capabilities.
Efficiency Concerns: A heavier motor can consume more energy, reducing the overall efficiency of the electric vehicle. This is especially crucial given the limited battery capacities of current EVs. The metallic nature of traditional rotor sleeves can also interfere with the motor's electromagnetic field, potentially reducing its efficiency.
Need for Weight Reduction: To enhance both the efficiency and performance of electric motors, there's a pressing need to reduce the weight of these primary components. Addressing the weight of the rotor shaft, laminated magnet carrier, and traditional metal rotor sleeve is crucial for the next generation of lightweight and efficient electric motors.
3. Innovative Solutions for Weight Reduction
To achieve significant weight reduction in electric vehicle (EV) motors, researchers have proposed several innovative solutions. Among these, three main approaches have been highlighted in the research articles:
The Hybrid Shaft Approach
Soft Magnetic Compounds (SMC) Approach
AFP/ATL for Sleeve Manufacturing
Let's delve deeper into each of these approaches:
4. The Hybrid Shaft Approach
The Hybrid Shaft Approach is a groundbreaking method that combines the strengths of both carbon-reinforced plastic (CFRP) and stainless steel to create a lightweight yet robust rotor shaft for electric motors. Here's a detailed look:
Combination of Materials:
Key Point: Leveraging the best of both worlds.
Details: Carbon fiber reinforced plastics (CFRP) are known for their excellent specific rigidity and strength properties, making them ideal for manufacturing hollow shafts. The hollow construction of CFRP shafts allows for high material utilization due to its high geometrical moment of inertia and low weight. On the other hand, stainless steel provides the necessary strength, especially in areas of high tribological stress, such as bearings or gear wheels.
Manufacturing Process:
Key Point: A novel process chain combining dry filament winding with centrifugal casting.
Details:
Wet Winding: Currently, CFRP shafts are primarily produced using wet winding. In this method, dry yarn is pulled through a resin bath and wound onto a rotating mandrel. The winding patterns can be flexibly adapted to the arising loads. After winding, the component is cured in an oven. However, this method has its limitations, including long cycle times and reduced productivity.

Dry Filament Winding: A new multistage process has been developed. It begins with a dry winding process to create a dry fiber preform. This preform is then impregnated using centrifugation. The entire process can be automated on a turning center. The winding process requires a polygon-shaped mandrel coated with Teflon (PTFE) to reduce friction and allow for easy removal of the preform.
Centrifugal Casting: After the winding, the preform is impregnated using centrifugal casting. This involves rotating the mold and pouring in a liquid resin-hardener mixture. The rotation ensures even distribution and impregnation of the resin. The hybrid shaft can then be removed from the mold and, if necessary, further refined.
Integration with Metal Elements:
Key Point: Seamless integration for optimal performance.
Details: After the winding process, the CFRP shaft is connected to metal elements. These metal elements introduce the load into areas of high stress, while the CFRP section transfers loads over longer distances, significantly reducing weight compared to a full steel shaft. Various joining technologies are employed, including adhesion, interface fit assembly, screw or bolt connections, and polygonal couplings.

Advantages:
Key Point: Significant weight reduction without compromising strength.
Details: The hybrid shaft approach can achieve a weight reduction of up to 50% compared to traditional steel shafts. The combination of CFRP and steel ensures that the shaft is both lightweight and robust, capable of handling the demands of high-performance electric motors.
This innovative approach not only addresses the weight challenge in electric motors but also offers a scalable and flexible manufacturing process, paving the way for the next generation of efficient and lightweight electric vehicles.
5. Soft Magnetic Compounds (SMC) Approach
Soft Magnetic Compounds (SMC) have emerged as a promising solution in the quest for weight reduction in electric motors. Here's a comprehensive look at this innovative approach:
Introduction to SMC:
Key Point: A blend of magnetic and non-magnetic materials.
Details: SMCs are materials that combine soft magnetic particles with a non-magnetic matrix. In the context of the research, a Fe-Ni material with high magnetic permeability was chosen as the SMC material. This was compounded in polyamide (PA) plastic with a filling degree of approximately 57%. The soft magnetic particles provide the necessary magnetic properties, while the PA matrix offers structural stability.
Role in Weight Reduction:
Key Point: Lightweight yet functional.
Details: The magnet carrier made from SMC weighs only 398 g. This lightweight construction, when compared to traditional materials, offers significant weight savings without compromising on the essential magnetic properties required for efficient motor operation.
Production Process:
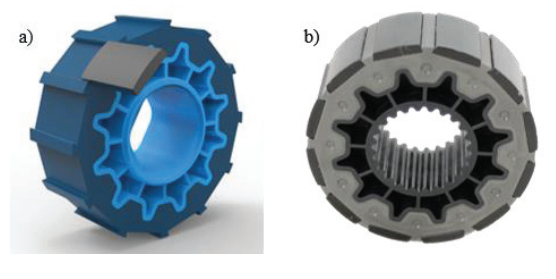
Key Point: Conventional injection molding with a twist.
Details:
Material Preparation: The particle size of the soft magnetic material is chosen to be smaller than 100 µm to ensure a uniform distribution within the matrix.
Molding Process: The technology required for the production of SMC components is a conventional injection molding machine equipped with a specific injection mold. This process is highly suitable for mass production.
Advantages over Traditional Methods: Unlike the conventional Metal Injection Molding (MIM) process, the SMC approach doesn't require the removal of a binder material. This simplifies the process and reduces time, complexity, and costs. After the injection molding process, the components are ready for immediate use.
Benefits of Using SMC:
Key Point: Efficient, lightweight, and cost-effective.
Details: SMCs offer several advantages:
Weight Reduction: As mentioned, the magnet carrier made from SMC is significantly lighter than its traditional counterparts.
Magnetic Efficiency: The Fe-Ni material ensures high magnetic permeability, making it ideal for electric motor applications.
Structural Stability: The combination of soft magnetic particles with the PA matrix ensures that the material can withstand the operational demands of an electric motor.
Cost and Time Efficiency: The production process is streamlined, eliminating the need for binder removal and allowing for immediate use post-molding.
The Soft Magnetic Compounds (SMC) approach, with its blend of efficiency, weight savings, and production advantages, presents a compelling case for its adoption in the next generation of electric motors.
6. AFP/ATL for Sleeve Manufacturing
Automated Fiber Placement (AFP) and Automated Tape Laying (ATL) are advanced manufacturing techniques that have revolutionized the production of composite components. In the context of EV motor protection, these methods offer a unique approach to manufacturing sleeves that are both efficient and lightweight. Here's a detailed exploration:
Introduction to AFP/ATL Process:
Key Point: Advanced manufacturing techniques for composite components.
Details: AFP can be used with either thermoset or thermoplastic composite prepreg. For the sleeve application, consolidation is performed using a laser heating system, enhancing the speed and efficiency of the process compared to conventional methods. This process allows for a one-step overwind process, eliminating the need for a secondary oven or autoclave consolidation.
Significance in EV Motor Protection:
Key Point: Enhanced protection with lightweight construction.
Details: The rotor sleeve adds distance between the rotor magnets and the stator. The ideal sleeve offers high strength in as thin a structure as possible. Design produces a sleeve that maximizes the PMM’s power density, ensuring efficient motor operation.
Advantages of Carbon Fiber-Reinforced PEEK Prepreg Tape:
Key Point: Superior material properties for demanding applications.
Details: The sleeve is made from carbon fiber-reinforced polyetheretherketone (PEEK) prepreg tape. This material offers superior toughness, resistance to wear, fatigue, and chemicals, making it ideal for the harsh conditions of an EV drivetrain.
Unique Design Freedom:
Key Point: Thinner, more efficient sleeves with AFP/ATL.
Details: The AFP/ATL manufacturing process offers new design freedom. The rotor sleeve produced is both thinner than thermoset composites and stronger per unit thickness than steel. This design freedom has enabled a more efficient manufacturing workflow.
Role of Pretensioning in AFP:
Key Point: Ensuring the composite sleeve remains secure during high rotational speeds.
Details: Pretensioning the composite material is crucial for handling high rotational speeds. This pretension creates a hoop stress that acts as compressive stress, keeping the composite sleeve in place over the rotor.
Comparison with Alternatives:
Key Point: Thermoplastic composite sleeves vs. thermoset composites and steel.
Details: Alternatives to the carbon fiber/PEEK sleeve include thermoset composite versions and steel versions. The properties of thermoplastic matrices, including their superior toughness and resistance, make them well-suited to the harsh conditions of an EV drivetrain. In contrast, thermoset composite sleeves require a multi-step process, and steel sleeves do not offer the same level of efficiency and weight reduction.
The AFP/ATL process for sleeve manufacturing presents a compelling case for its adoption in EV motors, offering a blend of efficiency, weight savings, and production advantages.
Comprehensive Comparison: Hybrid Shaft vs. Soft Magnetic Compounds (SMC) vs. AFP/ATL Sleeve Manufacturing:
Weight Reduction:
Hybrid Shaft: Offers about a 50% mass reduction compared to a conventional solid steel shaft.
SMC: Provides a lightweight magnet carrier that meets the required functional separation of torque transmission and the magnetically active part.
AFP/ATL: Uses lightweight carbon fiber-reinforced PEEK prepreg tape, allowing for thinner and more efficient sleeves.
Manufacturing Process:
Hybrid Shaft: Manufactured using a combination of dry filament winding and centrifugal casting.
SMC: Produced using a two-component injection molding process.
AFP/ATL: Manufactured using the Automated Fiber Placement (AFP) or Automated Tape Laying (ATL) process.
Mass Production:
Hybrid Shaft: Can produce 18,000 parts per year.
SMC: Can produce 127,000 magnet carriers per year.
AFP/ATL: Suitable for mass production, but specific numbers are in 10k - 100k units.
Innovation:
Hybrid Shaft: Combines dry filament winding with centrifugal casting.
SMC: Uses a unique two-component injection molding method.
AFP/ATL: Offers unique design freedom and uses pretensioning to ensure the sleeve stays in place during high rotational speeds.
Material Composition:
Hybrid Shaft: Primarily uses carbon-reinforced plastic combined with stainless steel.
SMC: Uses a Fe-Ni material compounded in a polyamide (PA) plastic.
AFP/ATL: Uses carbon fiber-reinforced PEEK prepreg tape.
Each of the three processes offers unique advantages in the realm of electric motor design and manufacturing. The hybrid shaft focuses on the combination of materials for weight reduction, the SMC process emphasizes efficient injection molding, and the AFP/ATL process prioritizes design freedom and the use of advanced materials. The choice between these methods would depend on specific application requirements, production capabilities, and cost considerations.
8. Conclusion
Revolutionizing Electric Motor Manufacturing:
The global shift towards green mobility and the need for efficient electric vehicles has necessitated innovations in electric motor manufacturing.
The research has presented groundbreaking approaches, including the hybrid shaft, Soft Magnetic Compounds (SMC), and AFP/ATL sleeve manufacturing, each offering unique advantages in weight reduction and efficiency.
Potential Impact:
The hybrid shaft, with its combination of carbon-reinforced plastic and stainless steel, offers a significant mass reduction compared to conventional solid steel shafts.
The SMC approach provides an innovative solution for magnet carriers, replacing traditional electric sheets and offering a lightweight alternative.
The AFP/ATL process introduces a new dimension in EV motor protection, using carbon fiber-reinforced PEEK prepreg tape, which is not only lightweight but also efficient.
A Nod to the Future:
As the electric vehicle industry continues to grow, the innovations presented in these research papers could play a pivotal role in shaping the next generation of EVs.
The integration of these advanced manufacturing processes and materials could lead to vehicles with extended ranges, improved performance, and reduced environmental impact.
As the industry moves forward, continuous research and development in this field will be crucial in ensuring that electric vehicles remain at the forefront of sustainable transportation solutions.
What's Next!
Discover the future of composite manufacturing with Addcomposites! Here's how you can get involved:
Stay Informed: Subscribe to our newsletter to receive the latest updates, news, and developments in AFP systems and services. Knowledge is power, and by staying informed, you'll always have the upper hand. Subscribe Now
Experience Our Technology: Try our cutting-edge simulation software for a firsthand experience of the versatility and capability of our AFP systems. You'll see how our technology can transform your production line. Try Simulation
Join the Collaboration: Engage with us and other technical centers across various industries. By joining this collaborative platform, you'll get to share ideas, innovate, and influence the future of AFP. Join Collaboration
Get Hands-On: Avail our educational rentals for university projects or semester-long programs. Experience how our AFP systems bring about a revolution in composite manufacturing and leverage this opportunity for academic and research pursuits. Request for Educational Rental
Take the Next Step: Request a quotation for our AFP systems. Whether you're interested in the AFP-XS, AFP-X, or SCF3D, we are committed to offering cost-effective solutions tailored to your needs. Take the plunge and prepare your production line for the next generation of composite manufacturing. Request Quotation
At Addcomposites, we are dedicated to revolutionizing composite manufacturing. Our AFP systems and comprehensive support services are waiting for you to harness. So, don't wait – get started on your journey to the future of manufacturing today!
Comments