Overview of Automated Fiber Placement Process
- Pravin Luthada
- Feb 4, 2024
- 15 min read
1. Introduction
In the realm of composite material manufacturing, the quest for precision, efficiency, and innovation has led to the development of groundbreaking technologies that redefine traditional processes. Among these, Automated Fiber Placement (AFP) stands out as a transformative approach, offering a leap forward in the production of complex, high-performance parts. This technology, which melds the precision of automation with the flexibility of composite materials, has not only revolutionized the way we think about manufacturing but also opened up new avenues for design and application across various industries.
From its origins in the late 1980s to its current state-of-the-art applications, AFP has undergone significant evolution, marked by technological advancements that have expanded its capabilities and accessibility. Today, AFP is at the forefront of composite manufacturing, providing unparalleled efficiency, quality, and material optimization. It embodies the fusion of advanced robotics, sophisticated programming, and material science to create lightweight, strong, and durable components essential for today's high-tech sectors such as aerospace, automotive, and renewable energy.
This blog delves into the history, principles, and impact of the Automated Fiber Placement process, exploring its advantages, limitations, and potential applications. Through a detailed examination, we aim to provide a comprehensive overview of AFP, highlighting its role in advancing composite material applications and its promising future in the ever-evolving landscape of manufacturing. Join us as we unravel the potential of AFP in modern manufacturing, shedding light on how this technology is shaping the future of industry and innovation.
2. History and Evolution of AFP

The journey of Automated Fiber Placement (AFP) technology is a testament to the relentless pursuit of innovation in the field of composite manufacturing. From its nascent stages in the late 1980s to the present, AFP has undergone transformative changes, each phase of development marking significant technological leaps that have enhanced its capabilities, efficiency, and application scope.
Early Developments in the Late 1980s and Early 1990s
Initially introduced to overcome the limitations of Automated Tape Laying (ATL) and manual hand layup processes, AFP technology emerged as a groundbreaking method that combined the precision of ATL with the flexibility of filament winding. This period was characterized by the development of systems capable of laying down narrow bands of material with high precision. A pivotal advancement was the introduction of systems that featured separate bobbins and individually driven tapes, which addressed the challenge of uniform material placement over complex contours.
Technological Advancements from 1990 to 2000
The 1990s marked a period of rapid advancement for AFP technology. Integration with Computer-Aided Design (CAD) systems enabled the automation of layup paths, allowing for more complex geometries to be manufactured with unprecedented accuracy. Improvements in layup speed were significant, with machines achieving speeds of up to 7 m/min, a notable increase that matched the productivity levels of ATL systems. This era also saw enhancements in the reliability of the layup process, with innovations such as cooled creel houses improving the consistency of material deposition. A key focus during this time was on optimizing the mechanical properties of laminates, with research showing that AFP could match or exceed the quality of hand-laid composites.
Developments from 2000 to 2012
The dawn of the new millennium brought a shift in focus towards making AFP technology more affordable, reliable, and productive. This period saw AFP's adoption beyond aerospace and into the realms of military and space programs, driven by its ability to produce high-quality, lightweight composite structures. Significant strides were made in process reliability through the introduction of automated splicing and layup error detection systems. Moreover, the adoption of infrared heating techniques for thermoset tapes marked an improvement in material handling, reducing layup errors and enhancing the overall quality of the composites produced.
Current State and Recent Advancements

Today, AFP stands at the forefront of composite manufacturing technology, driven by reductions in cost and the integration of industrial robotics. Modern AFP systems can be mounted on any industrial robotic arm or CNC machine, significantly lowering the barrier to entry for small and medium-sized enterprises. The advent of sophisticated sensors, networks, and software has led to the creation of "smart" AFP systems capable of real-time monitoring and adjustment, ensuring optimal placement of fibers and reducing material waste.
One of the most notable advancements in recent years is the dramatic decrease in the cost of AFP systems. With leasing options starting as low as $3,000-$4,000 per month, the technology has become accessible to a broader range of manufacturers. This democratization of AFP technology is poised to spur innovation across various industries, from aerospace to automotive, and beyond.
3. Basic Principles of AFP
The Automated Fiber Placement (AFP) process represents a significant leap in composite material manufacturing, offering unparalleled precision, efficiency, and quality. Understanding the basic principles behind AFP is crucial for leveraging its full potential in various applications.
Description of the AFP Process: From Material Preparation to Layup
The AFP process begins with material preparation, where composite fiber tapes or tows are loaded into the machine's creel system. These materials can vary widely in their composition, including pre-impregnated carbon fibers (prepregs) with thermoset or thermoplastic resins, depending on the application requirements.

Once the materials are prepared, the AFP machine, equipped with a robotic arm or CNC machine, starts the layup process. The machine head deposits the fiber tapes or tows onto a mold or mandrel, following a specific path and orientation dictated by the part design. This process is meticulously controlled to ensure optimal fiber alignment and compaction, which are critical for achieving the desired mechanical properties in the final part.
A key aspect of the AFP process is the use of heat to activate the resin in the prepreg material, ensuring proper bonding between layers. This heating is typically achieved through various means, such as hot gas, infrared lamps, or lasers, immediately before the material is placed onto the tool surface.
Programming logic plays a significant role in this process, where the path of fiber placement is optimized for load-bearing efficiency, minimizing material waste, and ensuring the part's integrity. For instance, the layup path might be programmed to avoid gaps and overlaps, crucial factors that can affect the strength and durability of the final composite structure.
Role of Automation and Robotics: Enhancements in Precision, Efficiency, and Quality
Automation and robotics are at the heart of AFP, driving significant enhancements in the manufacturing process. Robotic arms equipped with AFP heads offer a level of precision that manual processes cannot match, allowing for the placement of fibers at exact angles and positions with repeatable accuracy. This precision is particularly important for components with complex geometries or those requiring highly directional strength characteristics.

The efficiency gains from using automated systems are substantial. Robots can operate continuously with minimal downtime, significantly reducing the production time compared to manual layup methods. Moreover, the integration of advanced sensors and monitoring systems enables real-time adjustments during the layup process, further enhancing the quality and consistency of the final product.
Importance of Programming and Operation: Key Considerations for Successful AFP Implementation
Effective programming and operation are foundational to the success of AFP manufacturing. The programming of AFP machines involves generating a toolpath from the digital model of the part, which dictates the sequence, orientation, and placement of fibers. This step requires a deep understanding of both the part's design requirements and the capabilities of the AFP system.
Operators must consider several factors during the programming phase, including the material properties, the desired thickness of the composite, and the geometric complexity of the part. Advanced simulation software is often used to validate the toolpath before actual production, ensuring that potential issues are identified and mitigated early in the process.
During operation, continuous monitoring of the layup process is crucial for detecting and correcting any deviations from the planned path or material misplacement. This vigilance helps in maintaining the integrity of the composite structure, ensuring that it meets all specified performance criteria.
4. Programming and Operating AFP Systems
The programming and operation of Automated Fiber Placement (AFP) systems are complex tasks that require a detailed understanding of both the software and hardware involved. This section delves into the crucial steps for programming AFP systems, the operational considerations to keep in mind, and addresses some of the common challenges and solutions in AFP programming and operation.

Overview of Programming Steps
Programming an AFP system involves several critical steps designed to ensure that the fiber placement process is optimized for the specific part being manufactured. These steps include planning, simulating, and generating Numerical Control (NC) code, which collectively form the backbone of AFP programming.
Planning: The first step involves detailed planning of the layup strategy based on the part design and material requirements. This includes determining the orientation, order of layup, and the specific paths that the fibers will take over the tooling surface. Considerations such as material type, thickness, and the desired mechanical properties of the final part are taken into account during this phase.
Simulating: After planning, the next step is to simulate the layup process using specialized software. This simulation helps identify any potential issues with the layup strategy, such as gaps, overlaps, or areas where the fiber orientation may not meet the design requirements. Simulation tools can also predict potential problem areas in the toolpath that could lead to defects or inefficiencies in the layup process.
Generating NC Code: Once the layup strategy is optimized and validated through simulation, the next step is to generate the NC code that will control the AFP machine. This code instructs the machine on where to place fibers on the tooling surface, including the direction, speed, and order of layup. The generated NC code is then uploaded to the AFP system for execution.
Operational Considerations
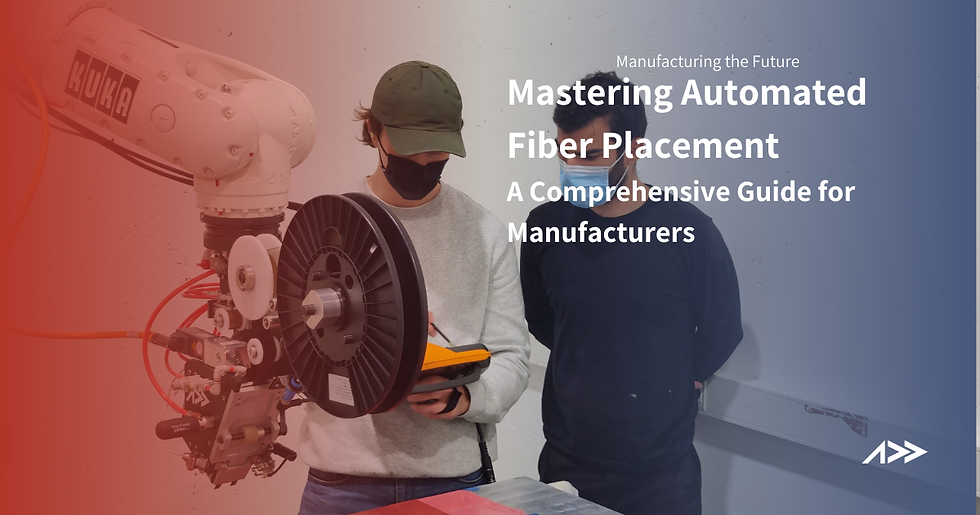
Material Setup: Before starting the layup process, the material must be properly prepared and loaded into the AFP machine. This involves ensuring that the fiber spools are correctly positioned and that the material is fed through the machine without twists or tangles. Proper tensioning of the tows is also critical to prevent any distortions during the layup.
Process Monitoring and Quality Control: Continuous monitoring of the layup process is essential to ensure that the AFP system is correctly executing the NC code. Advanced AFP systems are equipped with sensors and cameras to detect any deviations in real-time, allowing for immediate corrections. Quality control measures, such as ultrasonic inspection, can be integrated into the process to detect any defects or anomalies in the laid-up composite layers.
Challenges and Solutions in AFP Programming and Operation
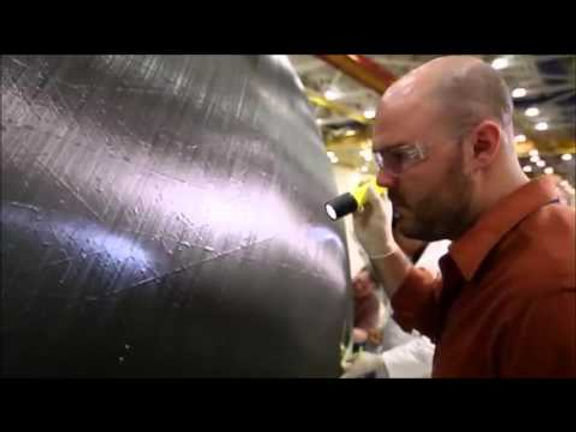
Challenge: Material Wrinkling and Gaps: One of the common issues in AFP is material wrinkling or the formation of gaps during layup, which can compromise the structural integrity of the part.
Solution: This challenge can be addressed through careful planning of the layup paths and optimizing the tension and pressure applied by the AFP head. Advanced simulation tools can predict these issues before actual production, allowing for adjustments in the programming phase.
Challenge: Complex Geometries: Manufacturing parts with complex geometries can present significant programming challenges, particularly in maintaining consistent fiber orientation and compaction.
Solution: To overcome this, software algorithms that specialize in generating toolpaths for complex shapes can be employed. These algorithms can automatically adjust the layup strategy to accommodate challenging geometries, ensuring that the fibers are accurately placed according to design specifications.
Challenge: Integration with Existing Manufacturing Processes: Integrating AFP systems into existing manufacturing workflows can be challenging, especially in facilities that are accustomed to traditional composite manufacturing methods.
Solution: Successful integration requires a comprehensive strategy that includes training for operators, adapting quality control processes to accommodate AFP, and ensuring that the design and manufacturing teams are aligned on the capabilities and limitations of AFP technology.
5. Comparison with Other Manufacturing Processes
The Automated Fiber Placement (AFP) process has redefined the landscape of composite manufacturing, offering distinct advantages and differences when compared to traditional methods like Hand Layup and Automated Tape Laying (ATL). Understanding these comparisons provides insight into why AFP has become a preferred method for producing composite materials in various industries.

AFP vs. Hand Layup: Efficiency, Quality, and Cost Considerations
Efficiency: AFP dramatically increases the efficiency of composite manufacturing. While hand layup is labor-intensive and time-consuming, AFP automates the process, significantly reducing the time required to produce composite parts. AFP machines can operate continuously, laying up materials much faster than manual methods.
Quality: AFP offers superior quality control compared to hand layup. The precision of robotic systems ensures consistent material placement and orientation, reducing the likelihood of defects such as gaps, overlaps, or misalignments. This consistency is challenging to achieve with hand layup, where variability can arise due to the manual nature of the work.
Cost Considerations: Initially, the investment in AFP technology may be higher than the cost required for hand layup due to the need for specialized equipment. However, the long-term cost benefits of AFP, including reduced labor costs, higher throughput, and lower waste, often justify the initial investment. Additionally, the improved quality and reliability of parts can lead to further cost savings in terms of reduced inspection, rework, and material usage.
AFP vs. Automated Tape Laying (ATL): Similarities, Differences, and Application Areas
Similarities: Both AFP and ATL are automated processes that lay down tapes of material onto a tool or mold. They share the goal of improving the efficiency and consistency of composite manufacturing compared to manual methods.
Differences:
Material Placement: AFP allows for the placement of narrower tapes (or tows) with the ability to steer them along complex curves and contours, offering greater design flexibility. In contrast, ATL typically uses wider tapes and is better suited for simpler, flatter parts.
Application Areas: Due to its flexibility and precision, AFP is preferred for manufacturing complex aerospace components with intricate geometries, such as fuselage sections and wing skins. ATL, on the other hand, finds its applications in larger, less complex parts where the high deposition rate of wider tapes is beneficial.
The Role of AFP in Advancing Composite Material Applications: AFP technology has been instrumental in advancing the use of composite materials across various sectors. Its precision and efficiency have made it particularly valuable in the aerospace industry, where the demand for lightweight, high-strength components is paramount. AFP's ability to accurately place fibers in optimized orientations enhances the performance and durability of aerospace structures, contributing to fuel efficiency and overall aircraft performance.
In the automotive sector, AFP is being increasingly adopted for manufacturing structural components and body panels, helping to reduce vehicle weight without compromising strength or safety. Beyond these industries, AFP's impact extends to wind energy, where it's used to create large, efficient wind turbine blades, and sporting goods, for the production of high-performance equipment.
6. Benefits and Limitations of AFP
Automated Fiber Placement (AFP) technology has revolutionized the field of composite manufacturing, bringing forth a host of advantages that cater to the demands for higher efficiency, quality, and performance. However, like any advanced manufacturing process, AFP also comes with its set of limitations. Understanding both aspects is crucial for manufacturers to leverage AFP effectively.
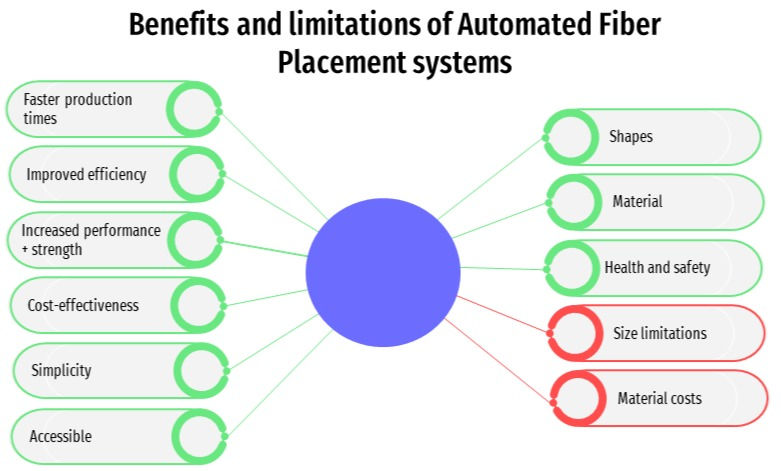
Advantages of AFP
Improved Production Times: AFP systems significantly reduce the time required to manufacture composite parts. The automation of the fiber placement process allows for continuous operation, drastically cutting down production cycles compared to manual layup methods.
Enhanced Efficiency: The precision of AFP systems minimizes material waste, as the placement of fibers is optimized according to the part design. This precise material placement also contributes to reduced scrap rates and more efficient use of raw materials.
Superior Performance: By enabling the precise orientation of fibers, AFP systems ensure that the mechanical properties of the composite parts are optimized for their specific application. This leads to parts with superior strength-to-weight ratios, essential for performance-critical applications in aerospace, automotive, and beyond.
Cost-Effectiveness: While the initial investment in AFP technology may be higher, the long-term savings in labor, material, and rework costs can be substantial. The increased throughput and reduced waste lead to a more efficient production process, offering significant cost benefits over the lifecycle of the technology.
Limitations of AFP
Size Constraints: The size of parts that can be manufactured using AFP is limited by the reach of the robotic arm or the size of the machine bed. This can pose challenges when manufacturing very large composite structures, requiring innovative solutions or the use of multiple AFP systems in tandem.
Material Costs: The materials used in AFP, such as pre-impregnated carbon or glass fibers, can be more expensive than those used in traditional manufacturing processes. The higher material costs must be weighed against the benefits of improved performance and reduced waste.
Technical Challenges: The operation of AFP systems requires specialized knowledge and skills, from programming the machine to monitoring the layup process. Ensuring the quality of the final part can also be challenging, as defects such as gaps, overlaps, or misoriented fibers need to be detected and corrected in real-time.
Despite these limitations, the advantages of AFP make it a compelling choice for the manufacturing of composite parts, particularly where performance, weight, and manufacturing efficiency are critical considerations. As technology continues to advance, ongoing research and development efforts are likely to address many of the current limitations, further expanding the applicability and effectiveness of AFP technology.
7. Potential Applications and Future Outlook
Automated Fiber Placement (AFP) technology has not only proven its worth in the current manufacturing landscape but also promises an exciting future with expanding applications and technological advancements. Its versatility and efficiency have paved the way for its adoption across a wide range of industries, each benefiting from the unique advantages AFP offers.
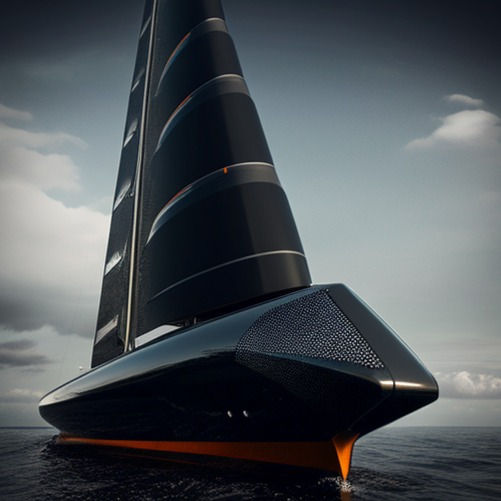
Diverse Industries Benefiting from AFP
Aerospace: In the aerospace industry, AFP is used for manufacturing structural components such as fuselage sections, wing spars, and tail fins. The technology's ability to create lightweight, high-strength parts makes it ideal for applications where weight reduction is critical to performance and fuel efficiency.
Automotive: The automotive sector utilizes AFP for creating composite parts that contribute to vehicle lightweighting, such as body panels and structural components. This not only improves fuel efficiency but also enhances the vehicle's overall performance.
Construction: AFP technology is being explored for its potential in constructing durable, lightweight composite materials for buildings and infrastructure. Its application can lead to innovative architectural designs and improved construction methodologies.
Wind Energy: In wind energy, AFP is instrumental in manufacturing large, efficient wind turbine blades. The precise fiber placement allows for optimized blade designs that improve energy capture and reduce manufacturing complexities.
Future Trends and Research Directions
The future of AFP technology is geared towards achieving higher throughput, minimizing defects in layups, and exploring innovative material usage. Key trends and research directions include:
High Throughput Systems: Efforts are being made to increase the speed of AFP systems while maintaining precision and quality. This involves advancements in machine hardware, software algorithms, and material handling processes to accommodate faster layup rates.
Minimal Defect Layups: Research is focusing on developing advanced monitoring and control systems that can detect and correct defects in real-time during the layup process. This includes the integration of sensors, AI, and machine learning technologies to predict and prevent potential issues before they occur.
Innovative Material Usage: The exploration of new materials compatible with AFP processes is ongoing. This includes the development of new resin systems, hybrid materials, and thermoplastic composites that can offer enhanced performance and environmental benefits.
Sustainability: There's a growing emphasis on making AFP more sustainable, both in terms of the materials used and the energy efficiency of the process. This includes the use of bio-based resins and recyclable fibers, as well as advancements in process efficiency to reduce energy consumption.
The Evolving Landscape of AFP Technology
The evolving landscape of AFP technology is marked by continuous innovation aimed at overcoming current limitations and expanding its application domains. As AFP becomes more integrated with Industry 4.0 technologies, we can anticipate a future where composite manufacturing is more efficient, versatile, and sustainable. The potential impact on future manufacturing includes the creation of complex, high-performance parts with reduced environmental footprint, opening up new possibilities in design and functionality across industries.
8. Conclusion

The journey through the Automated Fiber Placement (AFP) process and its evolutionary impact on manufacturing underscores a transformative shift towards precision, efficiency, and innovation in composite material applications. From its inception in the late 1980s to the present day, AFP technology has continuously evolved, breaking new ground in the capabilities and applications of composite manufacturing.
Recap of the AFP Process and Its Significance
AFP stands out as a hallmark of modern manufacturing technology, enabling the precise and automated placement of composite fibers to create structures that are lighter, stronger, and more complex than ever before possible. Its integration with advanced robotics, programming, and materials science has not only streamlined production processes but also opened up new possibilities in design and functionality. By significantly reducing waste, enhancing product quality, and increasing production efficiency, AFP has set a new standard in composite manufacturing.
The significance of AFP in the evolution of manufacturing cannot be overstated. It represents a leap forward in our ability to meet the growing demand for high-performance, lightweight materials across a wide range of industries, from aerospace and automotive to construction and wind energy. The precision and control afforded by AFP have led to improvements in material utilization, structural integrity, and overall product performance, setting the stage for a future where composite materials play an even more critical role in technological advancement.
Final Thoughts on the Future of AFP
Looking ahead, the future of AFP is bright with potential. As we push the boundaries of what's possible in composite manufacturing, AFP will continue to play a pivotal role in advancing material applications. The ongoing research and development efforts are poised to further enhance the throughput, reduce defects, and explore new materials that are more sustainable and performant. The integration of AFP with emerging technologies such as artificial intelligence, machine learning, and the Internet of Things (IoT) promises to create even smarter, more adaptive manufacturing systems capable of unprecedented levels of optimization and customization.
The role of AFP in advancing composite material applications is evolving rapidly, driven by the relentless pursuit of innovation and efficiency. As we continue to explore the limits of composite materials and manufacturing technologies, AFP will undoubtedly remain at the forefront of this exploration, shaping the future of manufacturing and opening up new horizons for design and engineering.
Complete course
The above article is part of the course Mastering Automated Fiber Placement: A Comprehensive Guide for Manufacturers. This course offers an in-depth understanding of Automated Fiber Placement (AFP) in composite manufacturing. It covers the basics of composites, AFP processes, machine operation, programming, troubleshooting, and practical applications, aimed at empowering manufacturers with the knowledge and confidence to efficiently operate AFP systems.
What's Next!
Discover the future of composite manufacturing with Addcomposites! Here's how you can get involved:
Stay Informed: Subscribe to our newsletter to receive the latest updates, news, and developments in AFP systems and services. Knowledge is power, and by staying informed, you'll always have the upper hand. Subscribe Now
Experience Our Technology: Try our cutting-edge simulation software for a firsthand experience of the versatility and capability of our AFP systems. You'll see how our technology can transform your production line. Try Simulation
Join the Collaboration: Engage with us and other technical centers across various industries. By joining this collaborative platform, you'll get to share ideas, innovate, and influence the future of AFP. Join Collaboration
Get Hands-On: Avail our educational rentals for university projects or semester-long programs. Experience how our AFP systems bring about a revolution in composite manufacturing and leverage this opportunity for academic and research pursuits. Request for Educational Rental
Take the Next Step: Request a quotation for our AFP systems. Whether you're interested in the AFP-XS, AFP-X, or SCF3D, we are committed to offering cost-effective solutions tailored to your needs. Take the plunge and prepare your production line for the next generation of composite manufacturing. Request Quotation
At Addcomposites, we are dedicated to revolutionizing composite manufacturing. Our AFP systems and comprehensive support services are waiting for you to harness. So, don't wait – get started on your journey to the future of manufacturing today!
Comentários