Preventing Fiber Waviness in 3D-Printed Continuous Fiber Thermoplastic Composites
- Pravin Luthada
- May 31, 2024
- 7 min read
TLDR
Challenges in 3D Printing Continuous Carbon Fiber Reinforced Thermoplastics

The key challenges in 3D printing Continuous Carbon Fiber Reinforced Thermoplastics (CFRTP) related to fiber not being straight or having waveiness include:
Fiber Misalignment and Breakage: During the fused filament fabrication (FFF) process, manufacturing-induced fiber misalignment and breakage can occur. This misalignment and breakage can significantly affect the mechanical properties of the printed parts, leading to reduced strength and stiffness.
Fiber Waviness: Fiber waviness is a common issue in 3D printing of CFRTP. This waviness can result from the printing process itself, where the fibers do not remain perfectly straight. This can lead to a reduction in the load-bearing capacity of the fibers and, consequently, the overall mechanical performance of the composite.
Voids and Porosity: The presence of voids and porosity within the printed structure is another challenge. These defects can arise due to incomplete impregnation of the fiber bundles with the thermoplastic matrix, leading to weak spots in the composite material. This issue is exacerbated by fiber waviness, which can create additional voids and reduce the overall density and strength of the material.
Interfacial Bonding: Poor interfacial bonding between the fibers and the matrix can occur due to fiber waviness. This weak bonding can lead to delamination and other failure modes under mechanical stress, further compromising the structural integrity of the printed parts.
Anisotropic Behavior: The anisotropic nature of CFRTP composites means that their mechanical properties vary significantly depending on the direction of the fibers. Fiber waviness can exacerbate this anisotropy, leading to unpredictable and often suboptimal performance in directions other than the primary fiber orientation.
Post-Processing Requirements: To address fiber waviness and improve the mechanical properties of the printed parts, additional post-processing steps such as compaction and stretching are often required. These steps can be time-consuming and costly, reducing the overall efficiency and cost-effectiveness of the 3D printing process.
Issues of Fiber Waviness and Voids in 3D-Printed c-CFRTP
3D printing of continuous carbon fiber reinforced thermoplastics (c-CFRTP) is an advanced manufacturing technique that promises high-performance composite structures. However, this process encounters several significant issues that undermine the mechanical properties of the printed parts.
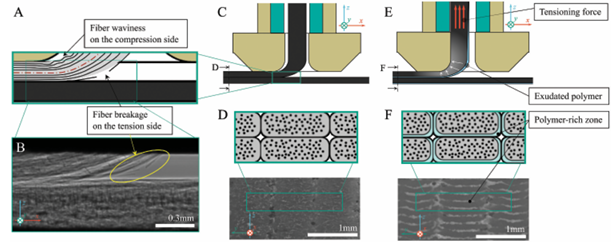
Fiber Waviness:
Definition: Fiber waviness occurs when the filament bends sharply as it exits the nozzle during the 3D printing process, causing the fibers to misalign and create a wavy pattern instead of remaining straight.
Causes:
90° bending of the fused filament
Differential strain and fiber twisting due to internal and external lengths of the bend
Effects:
Reduced load-bearing capacity and stiffness
Less effective in structural applications
Voids:
Definition: Voids are empty spaces that exist on two scales within the 3D-printed c-CFRTP:
Micro-scale voids within the filament itself
Macro-scale voids between the deposited layers or print paths
Causes:
Micro-scale voids: Introduced during the filament manufacturing process
Macro-scale voids: Insufficient compaction pressure and misalignment of print paths during layer-by-layer deposition
Effects:
Act as stress concentrators, weakening the printed material
Make the material prone to failure under mechanical loads
Impact on Mechanical Performance:
Fiber waviness leads to reduced stiffness and strength
Voids compromise the material's integrity and durability
These defects limit the application of 3D-printed c-CFRTP in high-performance sectors such as aerospace and automotive, where material reliability and mechanical performance are critical
Addressing the Issues:
Techniques to reduce fiber waviness:
Optimizing filament tension during printing
Methods to minimize voids:
Increasing compaction pressure
Employing vacuum conditions during printing
These steps are essential to improving the quality and performance of 3D-printed c-CFRTP
Application of Tension and Compaction Forces in 3D Printing
To address the challenges of fiber waviness and voids in 3D-printed continuous carbon fiber reinforced thermoplastics (c-CFRTP), the application of tension and compaction forces during the printing process has proven to be an effective approach. These techniques significantly enhance the mechanical properties of the printed parts by ensuring better fiber alignment and reducing void content.
Tensioning Force Application
Applying tension to the filament during the 3D printing process helps straighten the fibers and minimize waviness. This tensioning force is generated by controlling the filament feeding speed asynchronously with the print speed. Specifically, a filament feeder acts as a tension amplifier, introducing a tension rate parameter to manage the tensioning force. The tension rate (𝑅𝑇) is defined by the relationship between the feeding length (Δ𝐹) and the print length (Δ𝑥):
𝑅𝑇=(1−Δ𝐹/Δ𝑥)×100%
When 𝑅𝑇RT is greater than 0, tension is applied, resulting in improved fiber straightness. By maintaining this tension throughout the printing process, the tendency of fibers to become wavy is significantly reduced, leading to enhanced stiffness and strength of the printed parts.
Compaction Force Application
Compaction force is applied by adjusting the gap between the nozzle tip and the build plate, a process parameter known as the compaction rate (𝑅𝐶RC). This force compresses the filament immediately after extrusion, thereby reducing voids within the printed layers. The compaction rate is defined as follows:
𝑅𝐶=(1−ℎthin/ℎ0)×100%
Here, ℎ0h0 is the default layer height, and ℎthin is the adjusted layer height for increased compaction. By decreasing the layer height, the extruded filament is compressed more effectively, resulting in fewer voids and stronger interlayer bonding.
Combined Application
Combining tensioning and compaction forces maximizes the benefits of both techniques. This approach involves using a flat-tip nozzle to apply a consistent compaction force while simultaneously controlling the tension rate to maintain fiber alignment. This combination addresses both major defects in 3D-printed c-CFRTP—fiber waviness and voids—leading to parts with superior mechanical properties.
Experimental results have shown that applying these forces increases the flexural stiffness and strength of c-CFRTP. Specifically, the combination of tensioning and compaction forces has achieved improvements of up to 45% in flexural stiffness and 28% in flexural strength compared to standard printing methods without these forces.
Adaptive Control
To further refine the application of tension and compaction forces, adaptive control strategies can be employed. For instance, when printing curved paths, the tension rate can be dynamically adjusted to prevent the filament from peeling off the build plate. By reducing or neutralizing the tension before entering a curve, the print path accuracy is maintained, ensuring consistent mechanical properties throughout the printed part.
Enhanced Flexural Properties through Controlled Printing Conditions
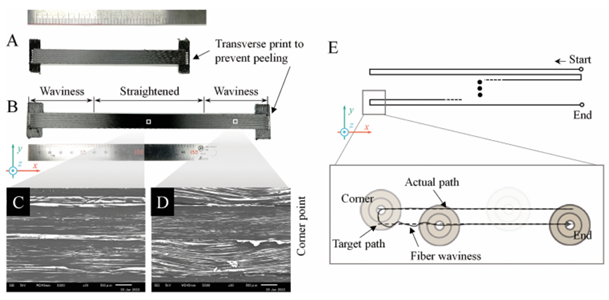
Advancements in 3D printing techniques for continuous carbon fiber reinforced thermoplastics (c-CFRTP) have demonstrated significant improvements in the mechanical properties of the printed parts. By carefully controlling the tensioning and compaction forces during the printing process, researchers have achieved notable enhancements in flexural stiffness and strength.
Improved Flexural Properties
The strategic application of tensioning and compaction forces has led to substantial improvements in the flexural properties of 3D-printed c-CFRTP. The following key findings highlight the benefits of these controlled printing conditions:
Increased Flexural Stiffness:
The combination of tensioning and compaction forces resulted in a 45% increase in flexural stiffness compared to standard printing conditions.
Tensioning the filament straightens the fibers, reducing waviness and enhancing the material's ability to resist bending.
Enhanced Flexural Strength:
The controlled application of these forces also led to a 28% increase in flexural strength.
Compaction force reduces void content and improves interlayer bonding, which contributes to the overall strength of the printed part.
Tensioning Force
The application of a tensioning force during printing ensures that the fibers within the filament remain straight, thereby reducing waviness. This is achieved by controlling the filament feeding speed asynchronously with the print speed. As the tension rate (𝑅𝑇) is increased, the fibers align more closely with the print path, minimizing distortions and enhancing mechanical performance.
Compaction Force
Compaction force is applied by adjusting the gap between the nozzle tip and the build plate, a process parameter known as the compaction rate (𝑅𝐶). By decreasing the layer height, the extruded filament is compressed more effectively, reducing void content. This improved compaction leads to stronger interlayer bonding, which is critical for enhancing the flexural strength of the printed part.
Adaptive Control
To address the challenges posed by curved print paths, adaptive control of the tension rate has been introduced. This method involves dynamically adjusting the tension rate before the filament enters a curve, preventing it from peeling off the build plate. By maintaining optimal tension throughout the printing process, accurate material placement is ensured, leading to consistent mechanical properties across the entire printed part.
Experimental Validation
The effectiveness of these controlled printing conditions was validated through three-point bending tests. Specimens printed with combined tensioning and compaction forces exhibited superior flexural properties compared to those printed under standard conditions. Specifically, the TENS-COMP specimens demonstrated the highest flexural stiffness and strength, confirming the benefits of these enhanced printing techniques.
In conclusion, the application of controlled tensioning and compaction forces during the 3D printing of c-CFRTP significantly improves the mechanical properties of the printed parts. These advancements enable the production of high-performance composite structures with reduced defects and enhanced reliability, making them suitable for demanding applications in aerospace, automotive, and other high-stress environments. By continuing to refine these techniques, the potential for 3D printing in advanced composite manufacturing will continue to expand.
References
We would like to extend our heartfelt gratitude to the authors, Naruki Ichihara, Masahito Ueda, Kentaro Kajiwara, Antoine Le Duigou, and Mickael Castro, for their invaluable contributions to advancing the field of 3D printing with continuous carbon fiber reinforced thermoplastics. Their study, "3D Printing with Tension and Compaction: Prevention of Fiber Waviness in 3D-Printed Continuous Carbon Fiber Reinforced Thermoplastics," provides significant insights into overcoming the challenges of fiber waviness and voids, ultimately enhancing the mechanical properties of 3D-printed composites. Their dedication and expertise have been instrumental in pushing the boundaries of composite material science. We are grateful for the opportunity to share their findings with a broader audience. Thank you for your exceptional work and for paving the way for future advancements in this exciting field.
What's Next!

Discover the future of composite manufacturing with Addcomposites! Here's how you can get involved:
Stay Informed: Subscribe to our newsletter to receive the latest updates, news, and developments in AFP systems and services. Knowledge is power, and by staying informed, you'll always have the upper hand. Subscribe Now
Experience Our Technology: Try our cutting-edge simulation software for a firsthand experience of the versatility and capability of our AFP systems. You'll see how our technology can transform your production line. Try Simulation
Join the Collaboration: Engage with us and other technical centers across various industries. By joining this collaborative platform, you'll get to share ideas, innovate, and influence the future of AFP. Join Collaboration
Get Hands-On: Avail our educational rentals for university projects or semester-long programs. Experience how our AFP systems bring about a revolution in composite manufacturing and leverage this opportunity for academic and research pursuits. Request for Educational Rental
Take the Next Step: Request a quotation for our AFP systems. Whether you're interested in the AFP-XS, AFP-X, or SCF3D, we are committed to offering cost-effective solutions tailored to your needs. Take the plunge and prepare your production line for the next generation of composite manufacturing. Request Quotation
At Addcomposites, we are dedicated to revolutionizing composite manufacturing. Our AFP systems and comprehensive support services are waiting for you to harness. So, don't wait – get started on your journey to the future of manufacturing today!
Commenti