What is the Pultrusion Manufacturing Process?
- Pravin Luthada
- Jun 16, 2022
- 4 min read
Updated: Jul 1, 2022
Pultrusion is a method of manufacturing that refers to a continuous process that utilizes fiber reinforcements and resin matrices to produce constant cross-sectional profiles.

Figure 1. An illustration of the Pultrusion Process
Below are the links to navigate quickly to the key sections
History
Brandt Goldsworthy, an honored pioneer in the plastics and composites industries, invented the pultrusion process, and he was a major figure in the invention and development of composite material technology.
He came up with the idea of combining various materials together to make stronger plastics while working for an aircraft company that was supplying items for the US Army during the Second World War.
His creations were so successful that he eventually decided to open his own company, where he made several advancements in the field of composites and created certain plastics that were generally stronger than anything previously seen.
Manufacturing Process
Pultrusion refers to a manufacturing process in which continuous lengths of fiberglass reinforced polymers with a constant cross-section are produced.
During this process, reinforced fibers, liquid pultrusion resins, pigments, and other raw materials are normally pulled through a heated die, converting them into FRP composite products.
Figure 2. The Pultrusion Process
Step 1: Feed Raw Materials into the Guide
The pultrusion process involves pulling the necessary raw materials through a heated die, which means that the reinforced fibers need to be in continuous form.
In most cases, either roll of filaments known as rovings or continuous strand mats is used. They provide the tensile strength required to pull the rest of the fiber reinforcements through the die.
That said, the first pultrusion process step involves feeding the continuous roving filaments or mats into the machinery through the performing guides. In the guide, the roving filaments are often passed through a tensioner, then shaped into the finished profile.
It is, therefore, vital that the manufacturer maintains utmost accuracy when feeding the rovings in the guides, as this determines both the strength and the quality of the resulting profile.
Step 2: Impregnate the Fiber in Resin Bath
The reinforced rovings or mats go through a wet-out bath for resin impregnation. The forming guides are placed before, within, or after this resin bath. The wet-out bath usually contains a resin, most commonly polyester or vinyl ester, pigments, fillers, and also a catalyst to help in curing. It's critical to note that there are different types of wet-out baths.
The most common one involves an open-resin-filled bath that usually has separation bars within it, so the rovings are guided over and under the bars for impregnation. It's considered the standard resin impregnation method as it's cost-effective and also results in high-quality profiles.
Another type of wet-out bath also involves an open-filled bath; the only difference is that the reinforcement doesn't go up and down.
Therefore, it's more suitable for vertical reinforcements such as mats and veils as they'll remain horizontally positioned throughout the process. It's ideal for the production of hollow pultruded composite products.
Step 3: Go Into the Heating/Curing
The resin-impregnated reinforced fibers then go through a heated die. This step is also critical as it's where the hard shape of the resulting profile is formed. When the impregnated reinforcements are exposed to the heated die, the cross-linking process begins, and they gradually solidify.
It's vital to note that the cross-linking process is exothermic. This means that once initiated, it causes the temperature of the resin to exceed that of the die.
This usually happens towards the end of the heating process, and in turn, the resin pulls away from the die naturally. It's therefore incredibly important to maintain an optimum temperature.
If the temperature is too high, cracks will appear in the composite. On the other hand, if the temperature isn't hot enough, the resin will not achieve total cross-linking. Either way, the results are inferior quality composite profiles.
Step 4: Separate
As noted, separation begins at the end of the heating die process using a pulling mechanism. Many manufacturers often use a reciprocating hydraulic clamp puller for this purpose.
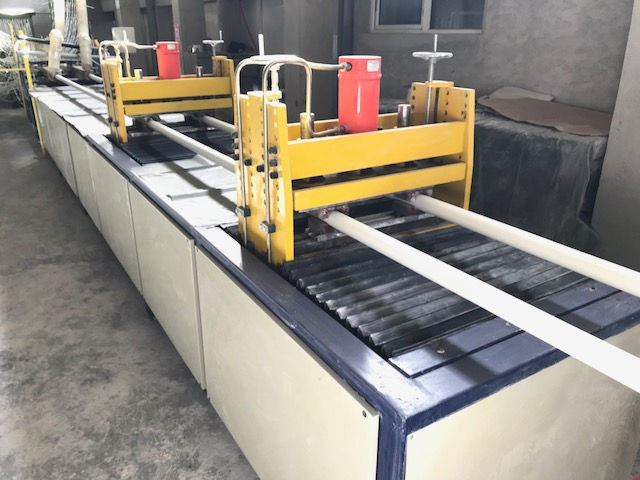
Once separated, the cured profiles are usually cut to the required length using an automatic saw. This is often the final pultrusion process step, and after this, the cured profile can either go through secondary processing at the factory or be packaged and shipped to the customer.
Summary
In general, the pultrusion manufacturing process is more economically attractive, convenient, and efficient compared to other types of manufacturing techniques currently available in the market.

Pultrusion also produces high-quality and error-free composites, which ensures that the resulting products have a longer life span compared to other old-school products. Because of this, it has become popular and in high demand in recent years.
About Addcomposites
Addcomposites is the provider of the Automated Fiber Placement (AFP) ecosystem - including the Fiber Placement System (AFP-XS), 3D Simulation and Programming Software (AddPath), and Robotic Cells (AddCell). With the leasing program for the AFP system (AFPnext), composites manufacturers can work with thermosets, thermoplastics, dry fiber placement, or in combination with 3D Printers on a monthly basis.
Subscribe to our newsletter and get our guidebook - "Composites Manufacturing Methods: An Ultimate Guide for 2022"
Comentários