Sustainable Manufacturing: Why Natural Fiber/Thermoplastic Composites
- Pravin Luthada
- Nov 23, 2022
- 3 min read
Table of Content
Natural fiber composites
A natural fiber composite with an outstanding combination of properties is no longer a pipe dream. The use of proper processing techniques, fiber treatments, and compatibilizers, or coupling agents, can lead to composites with optimum properties for a particular application.

The market for natural fiber-reinforced composites is expected to register a CAGR of 10.93% during the forecast period. A major factor driving the natural fiber-reinforced composites market is the increasing demand for bio-based composites and environmentally sustainable products.
Given the strong demand for sustainable production, the supply chain is also getting stronger to resolve geographical availability challenges, ensuring a consistent supply of materials.
Processing with Thermoset
Composites using thermosets as a matrix are processed using simple techniques such as hand layup and spraying, resin transfer molding, etc.

However, the use of these methods for natural fiber composites is hardly reported. In thermoset polymers, the fibers are used as unidirectional tapes or mats. These are impregnated with thermosetting resins and then exposed to high temperatures to begin the curing process.
Despite the ease of processing with low-cost tooling, thermoset composites are very difficult to recycle, contain harmful chemicals, and can not be repurposed for other uses at the end of life cycles. They are suitable for many applications, but not the best way to achieve sustainable production.
Natural fibers are usually not processed using thermoset resins because the curing temperature has to be quite high, with the exact temperature varying based on the resin used. If exposed to temperatures over 250˚C, the natural fibers have a very high likelihood of burning and compromising the structural integrity of the component.
Processing with Thermoplastic
Conventionally, the processing of natural fiber thermoplastic composites involves extrusion of the ingredients at melt temperatures followed by shaping operations such as injection molding and thermoforming. Oftentimes creating a sheet of natural fiber-reinforced composites (NFRC), and then shaping it via a thermoforming or similar process.

The properties of these composites can be influenced by the processing parameters in the case of thermoplastic composites, but as with CFRP and GFRP, the main properties are determined by the type of fiber.
The figure below shows how various natural fiber reinforcements compare to standard E-Glass regarding specific tensile strengths and stiffnesses.
A new age of NRFC processing
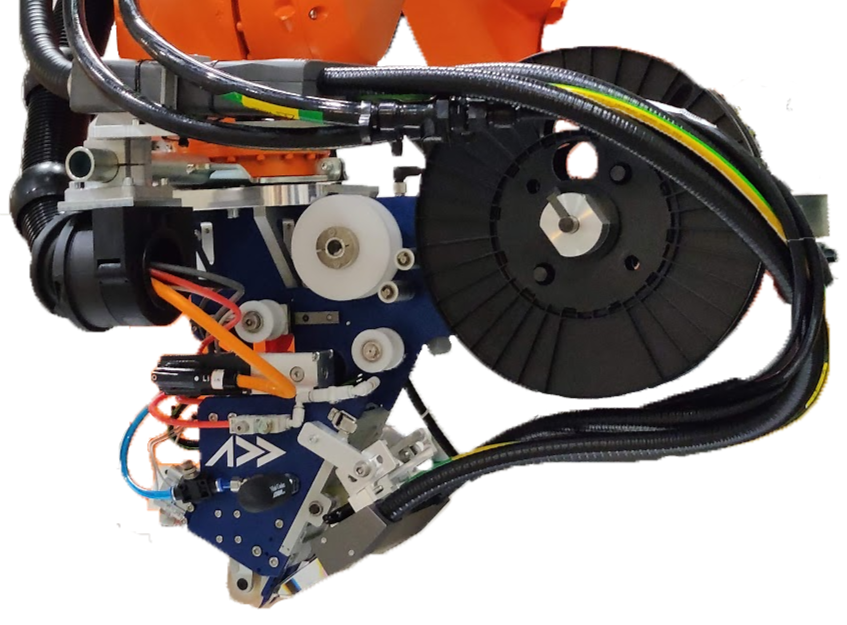
With the flood of demand for high-performance natural fiber composites, many material manufacturers are creating thermoplastic UD tapes for natural fiber composites.
The AFP-XS from Addcomposites supports the low processing temperature of all these thermoplastic tapes and provides automated fiber placement on 3D shapes to create customized layups. Any manufacturer or technical center can start experimenting with natural fiber-based thermoplastics with a monthly rental of the system.
The tool mounts onto any robotic arm to begin the production of high-performance parts using sustainable materials.
Increasing use cases: Thermoplastic
Here are a few good application cases using natural fiber with PE, PP, PS, and PVC, for which the processing temperature is about 200°C:
These composites with a density of around 0.9 g/cm, stiffness of around 3000 MPa, the impact strength of 25 kJ/m, and good sound absorption characteristics are being used by a number of leading companies.
Composites based on polyolefin offer the advantages of a 20% reduction in processing temperature and a 25% reduction in cycle time in addition to a weight reduction of about 30%.
These composites provide a wood-like appearance without requiring maintenance.
The extruded profiles can be used as a wood substitute in various applications such as window systems and decking.
Some more work to do!
Recently, there has been increasing interest in the commercialization of natural fiber composites and their use, especially for interior paneling in the automobile industry.
The real challenge for scientists is to improve the thermal stability of these fibers so that they can be used with engineering polymers, increasing the advantage of both the polymers and the fibers.
Improving the thermal stability of natural fibers for better performance is an indispensable task for scientists. Such attempts can widen the applications of natural fiber composites, making our world more eco-sustainable, without compromising on the structural integrity that made composites so sought after, to begin with.
Addcomposites
Addcomposites is the provider of the Automated Fiber Placement (AFP) ecosystem - including the Fiber Placement System (AFP-XS), 3D Simulation and Programming Software (AddPath), and Robotic Cells (AddCell). With the leasing program for the AFP system (AFPnext), composites manufacturers can work with thermosets, thermoplastics, dry fiber placement, or in combination with 3D Printers on a monthly basis.
Subscribe to the newsletter and get our guidebook - "Composites Materials: An Ultimate Guide for 2022"
Comments