Fiber-reinforced Plastics Composites - Thermoplastic and Thermoset Resins
- Pravin Luthada
- Nov 18, 2022
- 5 min read
Updated: Nov 27, 2022
Fiber-reinforced plastics utilize two types of matrix materials: Thermoset and Thermoplastic. Though both matrices have been around since the dawn of the composites era, primary structural parts have been mainly manufactured using thermoset matrices due to their ease of processing.
However, since the emergence of thermoplastic additive manufacturing (commonly known as 3D printing) thermoplastic composites have created a new image of ease of processing and sustainability. There is now a growing trend toward the additive manufacturing of thermoplastic composites for primary structures.
The blog here focuses on introducing both types of matrices and their associated pros and cons for applications, ease of production, and sustainability. In this blog post, we are focusing on long-fiber composites only.
Thermoplastic Resin
Thermoplastics, like metals, softening and melting as more heat is applied, and re-hardening with cooling. This process of crossing the softening and/or melting threshold (Tg) can be repeated as often as desired without any appreciable effect on the material properties in either state. Typical thermoplastics used in structural composites parts include:
Acrylonitrile Butadiene Styrene (ABS)
Acrylonitrile Butadiene Styrene, often abbreviated as ABS, is an opaque engineering thermoplastic widely used in electronic housings, auto parts, consumer products, pipe fittings, Lego toys, and many more.
Polyaryletherketones (PAEK)
Polyaryletherketones (PAEK) are semicrystalline polymers. They exhibit good stability and mechanical strength at high temperatures. PAEK is extremely resistant to chemicals and hydrolysis, making them ideal for medical applications, oil drilling components, automotive gears, etc.
Polyetheretherketone (PEEK)
Polyetheretherketone (PEEK) is a semi-crystalline, high-performance engineering thermoplastic. This rigid opaque (grey) material offers a unique combination of mechanical properties, resistance to chemicals, wear, fatigue, and creep as well as exceptionally high-temperature resistance, up to 260°C (480°F). It is extensively used in demanding applications such as aerospace, automotive, electrical, medical, etc.
Advantages of Thermoplastic Composites
Thermoplastic composites offer two major advantages for some manufacturing applications: The first is that many thermoplastic composites have an increased impact resistance to comparable thermosets. (In some instances, the difference can be as much as 10 times the impact resistance.)
The other major advantage of thermoplastic composites is their ability to be rendered malleable. Raw thermoplastic resins are solid at room temperature, but when heat and pressure impregnate a reinforcing fiber, a physical change occurs (however, it isn't a chemical reaction that results in a permanent, nonreversible change). This is what allows thermoplastic composites to be re-formed and re-shaped.
For example, you could heat a pultruded thermoplastic composite rod and re-mold it to have a curvature. Once cooled, the curve would remain, which isn't possible with thermoset resins. Figure 1 below shows the general idea of thermoforming a thermoplastic component. This idea is the same for thermoplastic composites as it is for a purely thermoplastic sheet.
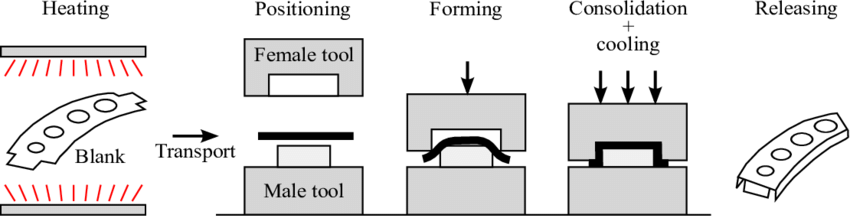
This ability to reform thermoplastic components shows tremendous promise for the future of recycling/repurposing thermoplastic composite products when their original use ends.
Disadvantages of Thermoplastic Composites
While it can be made malleable through the application of heat, because the natural state of the thermoplastic resin is solid, it's difficult to impregnate it with reinforcing fiber. The resin must be heated to the melting point and pressure must be applied to integrate fibers, and then, the composite has to be cooled, all while still under pressure.
Special tooling, techniques, and equipment must be used, many of which are expensive. The process is much more complex and expensive than traditional thermoset composite manufacturing.
Thermoset Resins
Thermosetting materials, or ‘thermosets’, are formed from a chemical reaction in situ, where the resin and hardener/catalyst are mixed and then undergo a non-reversible chemical reaction to form a hard, infusible product. Common thermosetting resins are:
Polyesters
Advantages:
Easy to use
Lowest cost of resins available (£1-2/kg)
Disadvantages
Only moderate mechanical properties
High styrene emissions in open molds
High cure shrinkage
Limited range of working times
Vinyl esters
Advantages:
Very high chemical/environmental resistance
Higher mechanical properties than polyesters
Disadvantages
Post-cure is generally required for high properties
High styrene content
Higher cost than polyesters (€2.25-4.50/kg)
High cure shrinkage
Epoxies
Advantages
High mechanical and thermal properties
High water resistance
Long working times available
Temperature resistance can be up to 140°C wet / 220°C dry
Low cure shrinkage
Disadvantages:
More expensive than vinyl esters (€3.25-€16.75/kg)
Critical mixing
Corrosive handling
Benefits of Thermoset Resins
Room-temperature liquid resin is fairly straightforward to work with, although it requires adequate ventilation for open-air production applications. In lamination (closed molds manufacturing), the liquid resin can be shaped quickly using a vacuum or positive pressure pump, allowing for mass production. Beyond ease of manufacturing, thermosetting resins offer a lot of bang for the buck, often producing superior products at a low raw-material cost.
Beneficial qualities of thermoset resins include:
Excellent resistance to solvents and corrosives
Resistance to heat and high temperature
High fatigue strength
Tailored elasticity
Excellent adhesion
Excellent finishing qualities for polishing and painting

Disadvantages of Thermoset Resins
A thermosetting resin, once catalyzed, can not be reversed or re-shaped. This means that once a thermoset composite is formed, its shape cannot be altered. Because of this, the recycling of thermoset composites is extremely difficult and expensive. Thermoset resin itself is not recyclable, however, a few newer companies have successfully removed resins from composites through an anaerobic process known as pyrolysis and are at least able to reclaim the reinforcing fiber.
Selecting the Right Matrix
Advances in thermoset and thermoplastic technology are ongoing and there's definitely a place for both. While each has its own set of pros and cons, what ultimately determines which material is best suited to any given application comes down to a number of factors
Mechanical and adhesive properties
Toughness
Resistance to environmental degradation
Ease/expense of manufacture
Recyclability
Mechanical and adhesive properties
The ideal resin failure mode should indicate high ultimate strength, high stiffness, and a high strain to failure. This means that the resin is initially stiff but at the same time will not suffer from brittle failure. Additionally, as the composite is loaded in tension, for the full mechanical properties of the fiber component to be achieved, the resin must be able to deform to at least the same extent as the fiber. The matrix adhesiveness must be enough to ensure efficient load transfer and cracking prevention at the fiber/resin interface.
Toughness
Match the strain to failure for resin compared to fiber
Generally, the more deformation the resin will accept before failure the tougher and more crack-resistant the structure becomes

Resistance to environmental degradation
Good resistance to the environment, water, and other aggressive substances, together with an ability to withstand constant stress cycling, are properties essential to any resin system.

Ease/expense of manufacture
Depending upon the production volume, the capital expenditure on production equipment should not be too high. Typically thermosets can be easy to get started but are difficult to scale up production volume
The knowledge gap to be able to produce composites part with minimal defects should be minimal. Ease of production through a cost-effective automated system is highly desirable
Recyclability
Recyclability of the resin system is very critical to reducing the carbon footprint.
Low toxicity and manually triggered bio-degradability are highly desirable
Selecting the right type of matrix for your application depends on many factors, and we hope this blog was able to provide you with enough of the basics to get started. If you have other questions related to different matrices and how they can be processed, reach out to the team at Addcomposites!
About Addcomposites
Addcomposites is the provider of the Automated Fiber Placement (AFP) ecosystem - including the Fiber Placement System (AFP-XS), 3D Simulation and Programming Software (AddPath), and Robotic Cells (AddCell). With the leasing program for the AFP system (AFPnext), composites manufacturers can work with thermosets, thermoplastics, dry fiber placement, or in combination with 3D Printers on a monthly basis.
Reference blogs and documents
Subscribe to the newsletter and get our guidebook - "Composites Materials: An Ultimate Guide for 2022"
Commentaires