The Automated Fiber Placement Process: Design Cycle, Benefits, and Applications
- Pravin Luthada
- Jan 5, 2023
- 8 min read
Updated: Jan 20, 2023
Automated fiber placement (AFP) is a process used to manufacture composite materials in which continuous fibers are placed onto a substrate using a specialized machine. The process has been around for decades and has undergone numerous developments to improve efficiency and quality. Today, AFP is widely used in various industries for the production of composite parts with improved mechanical properties, fatigue life, and fracture toughness.

In this chapter, we will discuss the history and development of automated fiber placement systems, as well as their benefits and limitations. We will also cover the role of automation and robotics in the AFP process, and how to program and operate these systems. Additionally, we will explore the composites' design lifecycle and the potential applications of automated fiber placement systems. Overall, this chapter aims to provide a comprehensive overview of the automated fiber placement process, including its history, benefits, and potential applications.
Jump directly to the relevant section
AFP Process Description
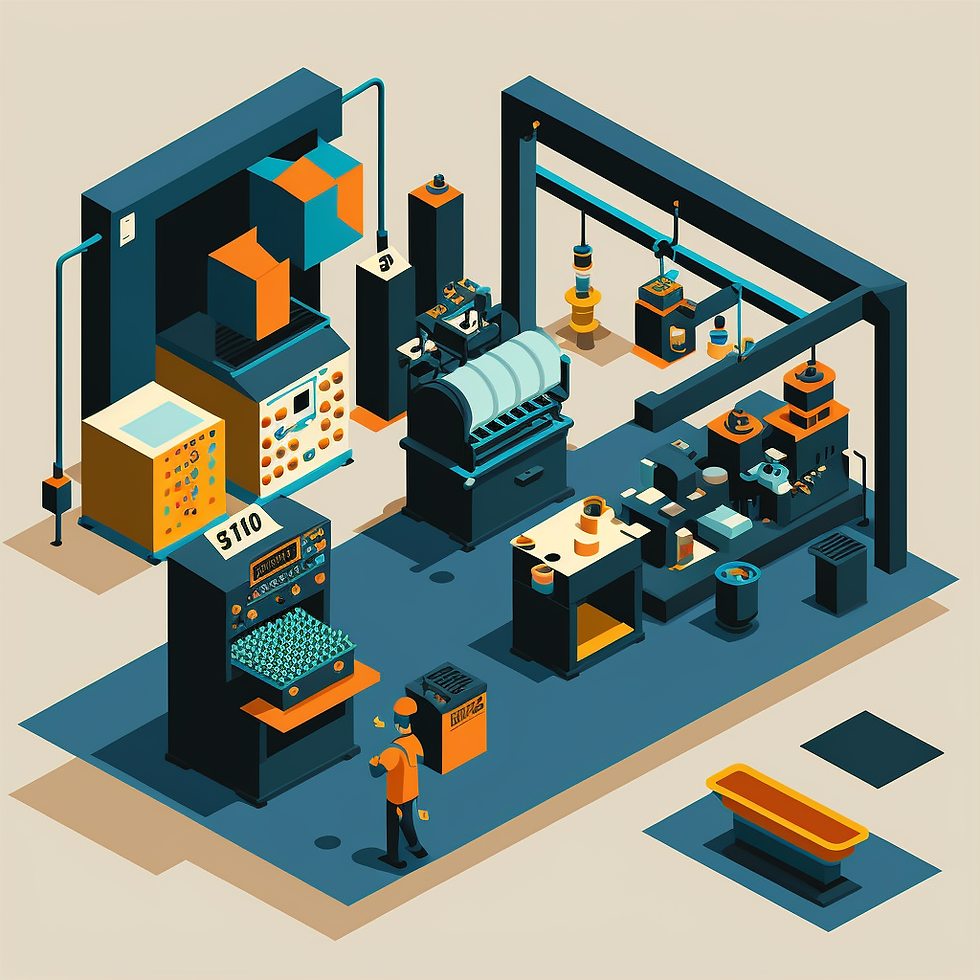
In an automated fiber placement process, an AFP head is attached at the end of an industrial robotic arm that is simulated and programmed using digital twin software like AddPath. As the AFP process is running, the head moves and places multiple strips of composite material tapes, or tows onto a tool surface. It is crucially important for the tape/tows to adhere with minimal defects. To ensure adhesion between incoming tows and substrate the fiber placement head utilizes heating and compaction. Tow tension plays a key role in ensuring the accurate placement of the tow. Each row of tows forms a course. Put together in a surface slice the course forms a ply, and all plies stacked together in a precise sequence form a laminate.
Role of automation and robotics in the AFP process
The use of robotics allows for precise and repeatable placement of the tows onto the substrate, with a level of accuracy and precision that may not be possible with manual techniques. Automation also allows for a faster production process, as a single robotic arm can lay up to 10kg of material in one hour, resulting in significant time and cost savings compared to manual labor.
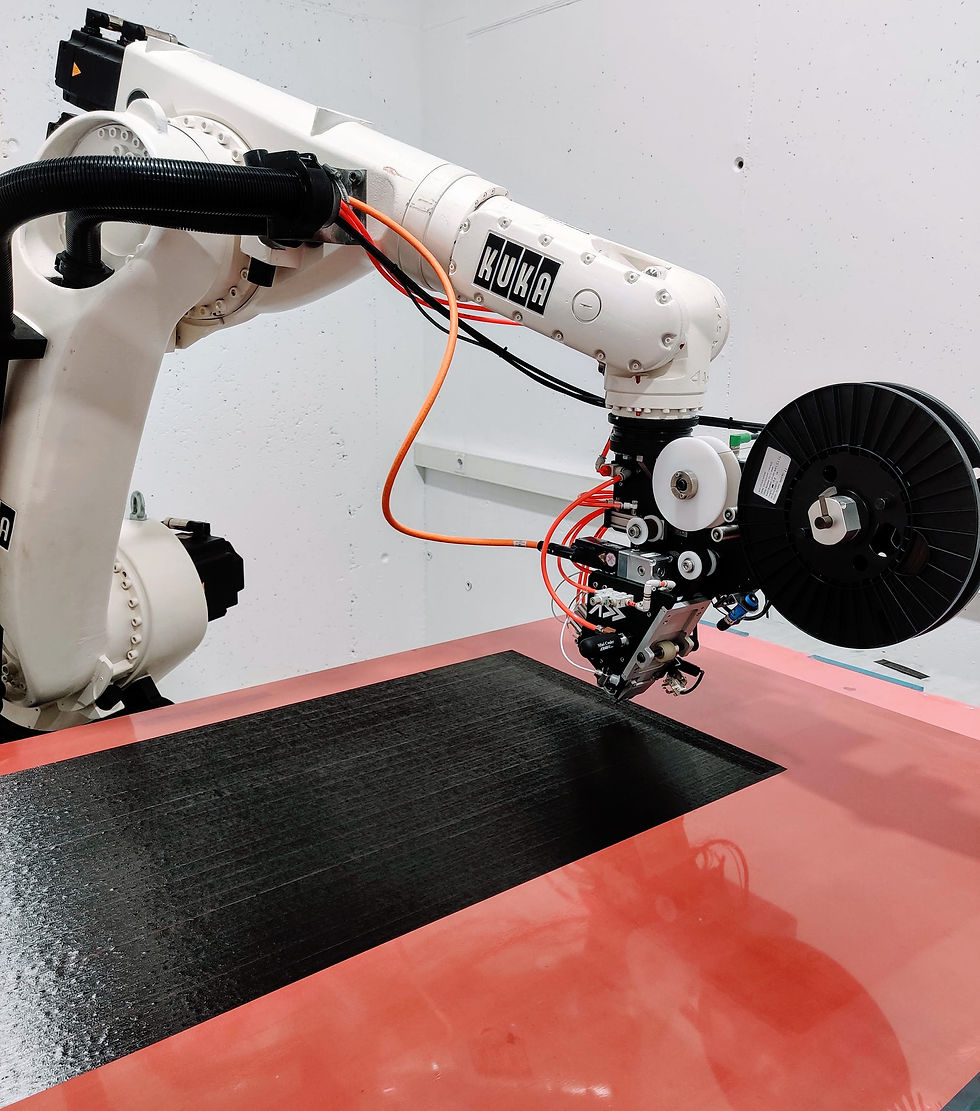
In addition to improving accuracy and efficiency, the use of robotics and automation in the AFP process also helps to reduce the risk of human error and improve the overall quality of the composite parts being produced. This is especially important in industries such as aerospace, where the performance and reliability of composite parts are critical.
Overall, the use of robotics and automation in the AFP process is essential for improving efficiency, accuracy, and quality in composite manufacturing.
How to program and operate automated Automated Fiber Placement systems

To program and operate AFP systems, operators typically need a basic knowledge of composites processing and operational knowledge of CNC machine operation. The specific steps involved in programming and operating an AFP system may vary depending on the specific equipment and software being used. However, the general process typically includes the following steps:
Planning and simulating the part production using software such as AddPath. This involves creating a digital model of the part to be produced and simulating the AFP process to ensure that the tows will be placed in the desired pattern.
Generating the NC (numerical control) code from the simulated part. The NC code is a set of instructions that tells the robotic arm how to move and place the tows during the AFP process.
Uploading the NC code to the robot and setting up the AFP tool by loading the material. This may involve preparing the tool surface and attaching the AFP head to the robotic arm.
Starting the part layup with a slower speed, typically around 15-30% of the programmed speed or less than 100 mm/sec. This allows the operator to ensure that the AFP process is running smoothly before increasing the speed.
Gradually increasing the speed to 100%. Quality monitoring software may be used to alert the operator in case of any defects and pause the operation for correction.
Checking the production data for any anomalies or unplanned interruptions after the program is completed. This can help the operator identify any issues and make adjustments as needed.
Overall, programming and operating an automated AFP system requires a combination of technical knowledge and careful attention to detail to ensure that the composite parts being produced are of high quality.
History of ATL/AFP Developments
The automated fiber placement (AFP) process has a long history of development, with the first AFP machines becoming commercially available in the 1980s. These machines were a combination of the differential payout capability of filament winding and the compaction and cut-restart capabilities of automated tape laying and had the ability to vary layup speed, pressure, temperature, and tow tension. In the 1990s, research focused on improving the productivity of the AFP process, including the development of a system that could deliver up to 24 tows at once and the use of thermoplastic composites for aerospace structural applications.
Starting in the 2000s, a significant portion of the research was focused on continuing to improve process reliability and productivity, including the development of automated defect detection systems and high-speed AFP machines. More recent research has focused on high throughput AFP, minimal defect layups, and in-situ thermoplastic layups, with the goal of improving the overall quality and efficiency of AFP-manufactured structures.
Composites Design Lifecycle and AFP
The integration of digital technologies into the composites manufacturing process is essential for overall success. This integration should be intelligent, connected, and involve communication between the four fundamental pillars of composites design and production:
Design
Process planning
Manufacturing
Inspection.
An Industry 4.0 automated fiber placement (AFP) workflow would involve seamless connections between all of these pillars, ensuring that design is not just a starting point but rather a continuous improvement cycle that integrates with the other pillars.
At the design and process planning stage, data sharing can help to eliminate the common issue of designers failing to account for manufacturing limitations and streamline the process of getting the part from the designer to the manufacturing floor.
The next stage of the workflow involves connecting process planning and manufacturing, with the use of a digital twin allowing the machine to draw on operation data and propose changes to the manufacturing process based on data analysis.
The next stage involves connecting manufacturing with inspection, with the aim of creating a data-driven composite manufacturing approach. This may involve representing data in a virtual or augmented reality environment to assist with inspection tasks.
Finally, the loop is closed with the connection of inspection and design, allowing for the optimization of design parameters based on data from the inspection.
Benefits and limitations of Automated Fiber Placement systems
It is important to note that while there are benefits to using AFP systems, there are also limitations to consider. It is important to weigh the pros and cons of using AFP in a specific application to determine if it is the right choice for a particular project. In some cases, the benefits of faster production times, improved efficiency, increased performance and strength, and cost-effectiveness may outweigh the limitations such as size and material constraints. In other cases, manual processes may be a better fit depending on the specific requirements of the project. It is important to carefully assess the needs and capabilities of a project before deciding on the best manufacturing approach.
Faster production times: The AFP process involves laying down unidirectional fibers in a pre-programmed pattern, rather than manually placing individual strands. This can reduce production times by up to 40%.
Improved efficiency: AFP can improve efficiency and reduce material waste compared to traditional manual hand layup processes.
Increased performance and strength: AFP produces more consistent results than manual hand layup, resulting in stronger bonds between layers and improved performance and strength in the finished product.
Cost-effectiveness: The improved efficiency and reduced material waste associated with AFP can make it a more cost-effective option compared to other manufacturing processes.
Simplicity: Any graduate student knowing the basics of composites can easily operate the latest AFP system without requiring a high level of technical knowledge and expertise to program and operate the equipment.
Accessible: AFP-XS fiber placement systems can be very easy to acquire and can be operational within days, making it a compelling choice for smaller manufacturers.
Shapes: AFP systems can work as tape winding and filament winding systems, capable of producing highly complex shapes with complex fiber orientation
Material: AFP systems can work across thermoset, thermoplastic, and dry fabrics, allowing much greater freedom in material selection
Health and safety: Moving the operator away from the composites processing environment ensures better health conditions and lowers the consumables requirements.
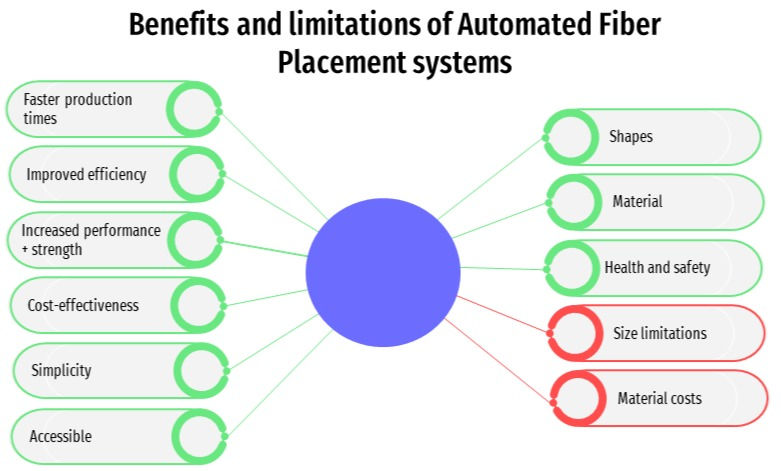
However, there are also some limitations to consider when using AFP systems:
Size limitations: AFP systems may not be suitable for parts with a very small or intricate geometry e.g. a watch case, small hinge, etc. as the tows may not be able to be placed accurately in these areas.
Material costs: Materials used in AFP processes are relatively expensive i.e. 10-15% higher cost compared to the materials used in manual processes.
Potential applications of Automated Fiber Placement systems
Automated fiber placement (AFP) systems are used in a variety of industries and applications, including:

Aerospace: AFP is widely used in the aerospace industry to manufacture aircraft components such as wing spars, fuselage panels, and bulkheads.
Automotive: AFP can be used to manufacture composite parts for the automotive industry, such as body panels, drivetrain components, and suspension parts.
Construction: AFP can be used to manufacture composite materials for use in construction, such as bridge decks, beams, and columns.
Wind energy: AFP can be used to manufacture composite wind turbine blades, which are typically longer and more flexible than traditional blades.
Sporting goods: AFP can be used to manufacture composite materials for use in sporting goods, such as golf clubs, tennis racquets, and skis.

Marine: AFP can be used to manufacture composite materials for use in the marine industry, such as hulls for boats and ships.
Medical: AFP can be used to manufacture composite materials for use in medical devices, such as implantable devices and prosthetics.
Consumer products: AFP can be used to manufacture composite materials for use in consumer products, such as electronics and appliances.

In general, AFP is well-suited for manufacturing lightweight, complex-shaped structures that are optimized for load-carrying and efficiency. Its ability to quickly and accurately place fibers in a predetermined pattern makes it a valuable tool for a wide range of industries and applications.
Summary
The automated fiber placement (AFP) process is a manufacturing method that involves using a robotic arm to place composite material tapes, or tows, onto a tool surface with a high level of accuracy and precision. The AFP process utilizes heating and compaction to ensure adhesion between the incoming tows and the substrate, and the tow tension plays a crucial role in ensuring accurate placement. The use of robotics and automation in the AFP process allows for faster production, improved accuracy and quality, and reduced risk of human error, making it an essential part of composite manufacturing.
To program and operate automated AFP systems, operators typically need to have a basic understanding of composites processing and CNC machine operation. The process usually involves simulating the part production using software, generating NC code from the simulated part, uploading the code to the robot and setting up the AFP tool, starting the layup process at a slower speed, gradually increasing the speed to 100%, and checking for any anomalies or interruptions after the program is completed. The history of AFP developments dates back to the 1980s, with the first AFP machines becoming commercially available. Research has focused on improving the productivity and capabilities of the AFP process, including the use of fiber steering and the development of high-performance composite materials. Potential applications of the AFP process include aerospace, automotive, and sports equipment industries, among others.
About Addcomposites
Addcomposites is the provider of the Automated Fiber Placement (AFP) ecosystem - including the Fiber Placement System (AFP-XS), 3D Simulation and Programming Software (AddPath), and Robotic Cells (AddCell). With the leasing program for the AFP system (AFPnext), composites manufacturers can work with thermosets, thermoplastics, dry fiber placement, or in combination with 3D Printers on a monthly basis.
Comments