The Composite Sky: Advanced Materials Defining Modern Aerospace
- Pravin Luthada
- Nov 12, 2023
- 17 min read
Advanced composites have transformed the landscape of materials used in civilian

aircraft, introducing a new era of performance, efficiency, and safety. These materials are not just incremental improvements over their predecessors; they represent a leap forward in materials science. Here we introduce the definition of advanced composites and their significance in civilian aircraft, along with an overview of their high-performance attributes.
Introduction to Advanced Composites
Definition and significance in civilian aircraft
Overview of fiber-reinforced materials and their high-performance attributes
Fiber Materials: The Building Blocks of Composites
Detailed examination of aramid, boron, carbon/graphite, and fiberglass fibers
Decision factors for material selection: performance vs. cost
Forms and Functions of Fiber in Composites
Explanation of strands, tows, fabrics, and their respective uses in composite structures
The science behind fiber orientation and its impact on load-bearing
Understanding Prepreg Materials
Introduction to unidirectional tape and fabric prepregs
Benefits of using preimpregnated materials in the manufacturing process
The Weave of Strength: Fabric Weaves in Composites
Exploration of plain, twill, and satin weaves
The role of weave patterns in the mechanical and handling characteristics of composites
Matrix Materials: The Glue Holding it All Together
Discussion on the role of the matrix in composites
Comparative analysis of different resin matrices: polyester, epoxy, phenolic, and thermoplastics
Advantages and disadvantages of thermoset and thermoplastic matrices
Advanced Forms and Future Materials
A look into three-dimensional woven, braided, and stitched forms
Innovations and future directions in fiber materials and composites
Design Considerations for Composite Materials
Factors influencing the choice of fabric: thickness, weight, construction, yarn size, and finish
The impact of these factors on the final composite product
Conclusion
The importance of material selection in the aerospace industry
The future of composites in civilian aircraft and beyond
Defining Advanced Composites

Advanced composites are engineered materials made from two or more constituents with distinct physical or chemical properties. One of these is typically a reinforcing fiber, such as carbon, aramid, or glass, known for its high strength-to-weight ratio. The other is a matrix material, like a polymer resin, which binds the fibers together, providing shape and protecting the fibers from environmental and operational damage.
In aerospace, these composites are meticulously designed to exploit the strengths of each constituent. The result is a material that outperforms traditional metal alloys in many respects, from strength and stiffness to corrosion resistance and fatigue life.
The Significance in Civilian Aircraft

The adoption of advanced composites in civilian aircraft manufacturing has been a game-changer. The primary driver for their use is the relentless pursuit of efficiency. Composite materials offer significant weight savings over traditional materials, leading directly to fuel savings—a critical factor in the economic and environmental sustainability of the aviation industry.
Additionally, the versatility of composites allows for innovative aircraft designs. The materials can be molded into complex shapes that would be difficult or impossible to achieve with metal, enabling more aerodynamic structures that further improve fuel efficiency and performance.
High-Performance Attributes of Fiber-Reinforced Materials
Strength and Stiffness: The high tensile strength of the reinforcing fibers allows composites to bear heavy loads, making them ideal for critical structural components in aircraft.
Weight Reduction: Composites are significantly lighter than metals, contributing to reduced aircraft weight and improved fuel efficiency.
Corrosion Resistance: Unlike metals, composites do not corrode, reducing maintenance costs and increasing the lifespan of aircraft components.
Fatigue Resistance: The endurance of composites under the cyclical stresses of takeoffs, flights, and landings is superior to many metals, enhancing the safety and longevity of the aircraft.
Design Flexibility: Composites can be molded into complex shapes, giving engineers greater design freedom to optimize aerodynamics and functionality.
Thermal Insulation: The low thermal conductivity of composites provides inherent insulation, contributing to the thermal efficiency of the aircraft cabin.
Damping Characteristics: The inherent damping properties of composites lead to a quieter cabin, improving the comfort of passengers.
Fiber Materials: The Building Blocks of Composites
At the heart of every advanced composite material are fibers that provide the fundamental properties required for aerospace applications. The choice of fiber is a strategic decision based on a blend of performance requirements and cost considerations. Let's explore the various fiber types and the science behind their selection.
Aramid Fibers
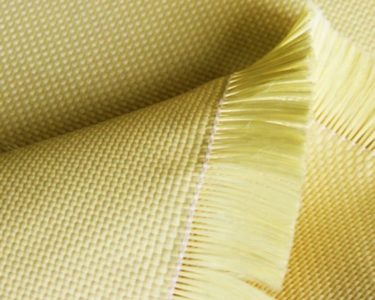
Aramid fibers, known for their golden-yellow color, are synthetic polymers derived from aromatic polyamides. They exhibit exceptional strength and resistance to impact, making them ideal for ballistic and aerospace applications. Notably, aramid fibers are not just strong; they're also lightweight and possess excellent fatigue resistance.
In the aerospace sector, aramid fibers are often used in honeycomb core structures, where their ability to absorb vibration and resistance to fatigue contribute to both the longevity and performance of aircraft components.
Boron Fibers

Boron fibers are produced by chemical vapor deposition on a substrate, resulting in a fiber with a large diameter relative to other advanced composite fibers. Their high stiffness and superior compressive strength make them suitable for applications where rigidity is paramount. However, the cost of boron fibers often restricts their use to highly specialized aerospace components where performance justifies the expense.
Boron fibers are commonly found in military aircraft, where they reinforce critical structures and improve the performance-to-weight ratio of the aircraft.
Carbon/Graphite Fibers
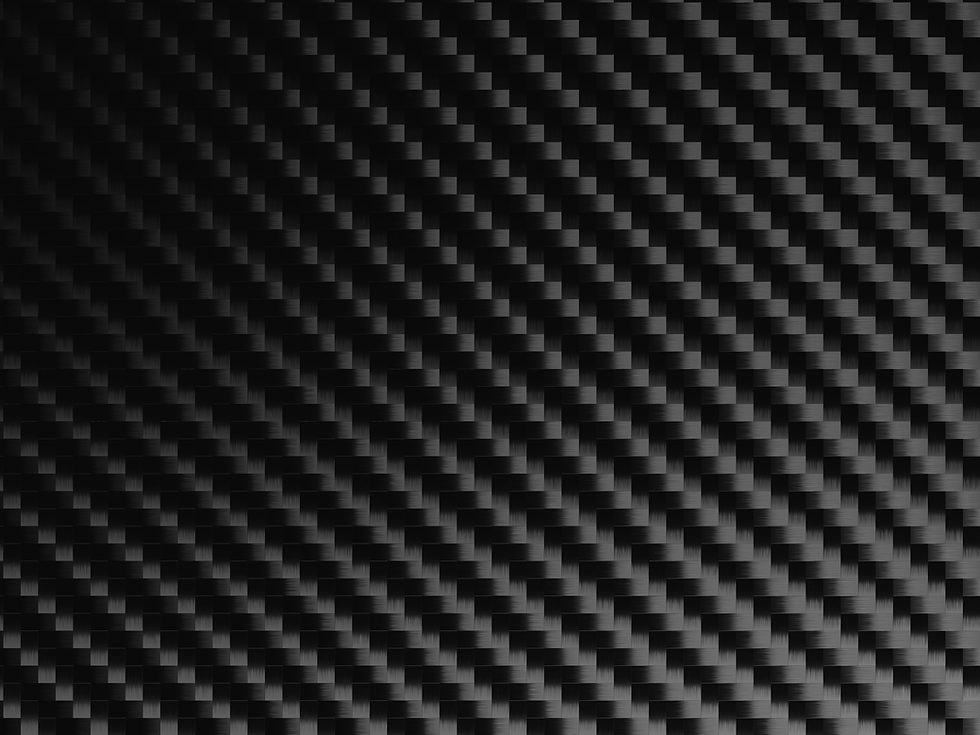
Carbon and graphite fibers are the workhorses of the aerospace composite world. Derived from organic precursors like polyacrylonitrile (PAN), these fibers undergo a thermal treatment process to achieve their desired high-strength and high-modulus characteristics.
The versatility of carbon fibers lies in their wide range of modulus, strength, and conductivity. Their ability to be processed into various forms, such as woven fabrics and unidirectional tapes, makes them adaptable to numerous aerospace applications—from the fuselage and wing skins to the empennage and control surfaces.
Fiberglass

Fiberglass, made from a mixture of silica sand, limestone, and other minerals at high temperatures, is the most widely used fiber in composite materials. While it doesn't match the strength or stiffness of carbon or aramid fibers, it's significantly less expensive and still provides a favorable strength-to-weight ratio.
Fiberglass is particularly prevalent in less critical structures of civilian aircraft, where its cost-effectiveness is a major advantage. It's also widely used in interior components and secondary structures, providing a balance of performance and economy.
The Future of Fiber Materials

Advanced composites are continually evolving, with research pushing the boundaries of fiber performance. Future developments may include fibers with even greater strength and stiffness, enhanced thermal properties, and perhaps even self-healing capabilities. As the demand for performance and efficiency in the aerospace industry grows, so too will the science of fiber materials, leading to the next generation of aircraft design.
Forms and Functions of Fibers in Aerospace
In the realm of advanced composites for aerospace applications, the form that reinforcing fibers take is as crucial as the fiber material itself. These forms cater to specific functional demands of aircraft structures and dictate the composite material's behavior under various load conditions. Here, we explore the most common fiber forms and how their configurations are employed to create materials that meet the rigorous demands of the aerospace industry.
Strands, Tows, and Fabrics
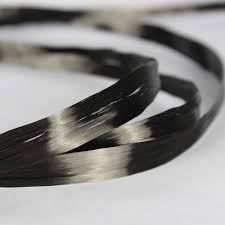
When it comes to composite construction, the physical form of the fiber—whether it's strands, tows, or woven into fabrics—plays a pivotal role in the composite's ultimate strength, stiffness, and weight.
Strands and Tows
In their simplest forms, fibers are bundled into strands or tows. Strands are typically single, untwisted bundles of filaments, which can be used as-is or chopped into shorter lengths for various manufacturing processes. Tows are similar but are specified by the number of filaments they contain, often numbering in the thousands, and are used in applications requiring continuous reinforcement.
These forms are versatile and can be adapted to a wide range of manufacturing techniques, from hand lay-up to automated fiber placement, each method affecting the orientation and distribution of the fibers within the matrix and thus the mechanical properties of the final part.
Woven Fabrics

Moving up in complexity, fibers can be woven into fabrics, interlacing warp and weft yarns in various patterns. This weaving process not only enhances the in-plane properties of the composite but also improves its out-of-plane toughness, a crucial factor in resisting delamination and other forms of structural failure.
Woven fabrics are particularly suited to complex shapes and contours found in aircraft designs. They offer better drape and can conform to the intricate geometries of airframe components. Moreover, the weave pattern can be optimized to prioritize strength in certain directions, a property known as anisotropy, which is essential for parts that experience directional loads.
Prepregs: Pre-impregnated Fibers

Prepreg materials represent a significant evolution in composite technology. These are fibers that have been pre-impregnated with a matrix material, such as epoxy resin, and partially cured. Prepregs offer uniform resin distribution, consistent quality, and ease of handling, making them highly favored in aerospace manufacturing.
Unidirectional tape is one form of prepreg where fibers are aligned in a single direction, providing maximum strength along that axis. Woven fabric prepregs, on the other hand, have fibers running in orthogonal directions, offering balanced strength properties.
Fiber Orientation and Lay-Up

In aerospace composites, fiber orientation is meticulously designed to align with the load paths of the aircraft structure. This strategic placement of fibers is key to achieving optimal strength, stiffness, and weight objectives. The lay-up process, whether manual or automated, is critical in realizing the intended fiber orientation, with the goal of fabricating a component that has the right balance of properties for its specific function.
The orientation of the fibers within the matrix can significantly impact the tensile, compressive, and shear strength of the composite material. For instance, fibers laid up in a zero-degree orientation relative to the primary load direction will provide maximum tensile and compressive strength, while fibers placed at 45 degrees can help to manage shear loads.
Mastery of Prepreg Materials in Aerospace
In the advanced composites used for aerospace applications, prepreg materials stand as a pinnacle of precision engineering. Prepregs, or pre-impregnated materials, are fibers that have been pre-coated with a resin system. This pre-application ensures uniform distribution of the matrix, optimizing the material properties and manufacturing process. Let's take an in-depth look at prepreg materials and their critical role in aerospace composites.
Prepreg Materials Defined
Prepregs are the result of fibers—be they carbon, aramid, or glass—saturated in a controlled amount of epoxy or other resin systems. This saturation takes place in a factory setting, ensuring consistent quality. The resin within prepregs is partially cured to a 'B-stage', where it is tacky and can be easily laid into molds before final curing.
Unidirectional Tapes and Fabrics
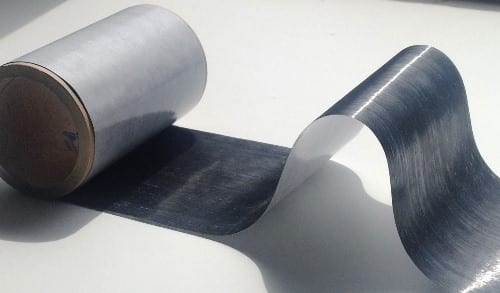
The most common form of prepreg comes in unidirectional tapes, where fibers are aligned in a single direction. This form is crucial for creating parts that need high strength in one specific direction. For instance, the spar of an airplane wing, which bears the brunt of the lift forces, benefits immensely from unidirectional prepregs that align with the wing's longitudinal axis.
Fabric prepregs, conversely, have fibers woven into a bidirectional pattern, lending the composite balanced strength properties in two directions. This makes fabric prepregs ideal for parts that encounter multi-axial stresses, such as fuselage panels or wing surfaces where forces are complex and multi-directional.
Advantages of Prepreg Materials
Prepreg materials offer several compelling advantages that make them highly sought after in aerospace design and manufacturing:
Quality Control: With resin uniformly distributed, there's a significant reduction in void content, enhancing the mechanical properties of the final composite.
Reduced Labor: The tackiness of B-staged prepregs eliminates the need for additional adhesives during lay-up, speeding up the process.
Precision: Prepregs allow for exact control over fiber orientation, resin content, and thickness, resulting in consistent performance.
Less Waste: Excess resin is removed in the prepreg process, reducing waste and ensuring a more eco-friendly manufacturing process.
Superior Performance: The fine-tuning of fiber-to-resin ratios and the alignment of fibers can be optimized for specific performance requirements.
The Manufacturing Process with Prepregs

The use of prepregs transforms the manufacturing process. Layers of prepreg material are cut to shape and laid into a mold in a predetermined sequence and orientation. This lay-up process is either done manually or with the help of automated machines. Once laid up, the prepreg assembly is subjected to heat and pressure, typically in an autoclave, to cure the resin fully and solidify the composite material.
The cure cycle for prepregs is carefully controlled to optimize the cross-linking of the resin matrix without compromising the integrity of the fibers. This results in a composite material with excellent strength-to-weight ratios, crucial for aerospace applications where every ounce matters.
Design Considerations with Prepregs
Designing with prepregs requires a deep understanding of the intended load paths and performance demands of the component. The fiber orientation in the prepreg must be designed to align with these load paths to ensure the part can handle the stress it will encounter in service.
For instance, if a part needs to withstand torsional forces, the fibers in the prepreg might be oriented at ±45 degrees to the axis of torsion. For bending loads, a 0/90 degree orientation could be more appropriate. The ability to tailor the fiber orientation is one of the key strengths of using prepregs in composite design.
The Weave of Strength in Aerospace
The structural integrity of composite materials used in aerospace relies heavily on the weave of the fabrics that form the basis of these advanced materials. In this section, we will explore the intricacies of fabric weaves, their impact on composite performance, and their application in the aerospace industry.
The Essence of Fabric Weaves
In composite materials, fabric weaves are more than just a pattern; they are engineered structures that determine the directional strength, flexibility, and bonding characteristics of the material. The weave pattern affects how the fabric handles during manufacturing, how it conforms to complex shapes, and its ability to absorb impacts.
Common Weave Patterns

Plain Weave: The most fundamental and widely used pattern, where each warp fiber alternates over and under each weft fiber. It's characterized by its stability and good strength in both the warp and weft directions. However, it's less drapable, which can make it more challenging to conform to curved surfaces.

Twill Weave: In a twill weave, each warp or weft fiber floats across two or more weft or warp fibers with a progression of interlaces by one to the left or right, forming a distinct diagonal pattern. This weave offers better drape than a plain weave and is easier to work with during lay-up, especially on complex shapes.
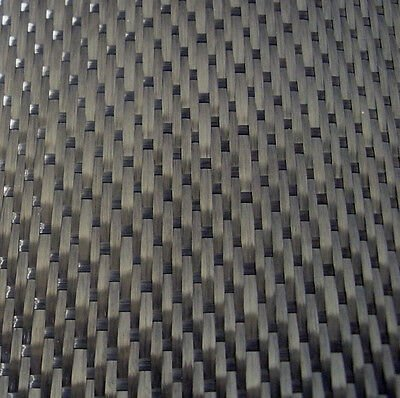
Satin Weave: Satin weaves are more complex, where warp fibers float over four or more weft fibers. This pattern results in a fabric with a smooth surface, excellent drape, and conformability. Satin weaves are typically used for composite parts that require a smooth finish or those that have compound curves.

Unidirectional Weave: Here, most of the fibers run in one direction with minimal cross-weave fibers. This arrangement provides very high strength in the direction of the fibers and is used in applications where maximum strength is required in one predominant direction.
Matrix Materials: The Glue Holding Composites Together
In the realm of advanced composites, particularly in aerospace applications, the matrix material plays a crucial role, often described as the 'glue' that binds the fibers together. This section delves into the function of the matrix in composites, provides a comparative analysis of different resin matrices like polyester, epoxy, phenolic, and thermoplastics, and outlines the advantages and disadvantages of thermoset and thermoplastic matrices.
Role of the Matrix in Composites
The matrix in a composite material serves several vital functions:
Load Transfer: It transfers load between the reinforcing fibers, ensuring that stress is distributed evenly throughout the material.
Protection of Fibers: It shields the fibers from environmental factors, mechanical damage, and stress concentrations.
Bonding: The matrix provides the adhesive force that binds the fibers together, maintaining the integrity and shape of the composite.
Thermal and Chemical Resistance: It contributes to the overall thermal stability and chemical resistance of the composite.
Types of Resin Matrices
Polyester Resins
Advantages: Cost-effective, good mechanical properties, easy to handle and cure.
Disadvantages: Lower thermal and chemical resistance compared to other resins, prone to water absorption.
Epoxy Resins
Advantages: Excellent adhesive properties, high strength, and stiffness, good durability, and low shrinkage upon curing.
Disadvantages: Generally more expensive than polyester, the curing process can be more complex.
Phenolic Resins
Advantages: Outstanding fire, heat, and smoke resistance, low cost, and good mechanical properties.
Disadvantages: Brittle, lower toughness, and can emit formaldehyde during curing.
Thermoplastics
Advantages: Recyclable, remoldable, high impact resistance, generally good chemical resistance.
Disadvantages: Higher processing temperatures required, can be more expensive than thermosets.
Thermoset vs. Thermoplastic Matrices

Thermoset Matrices
Advantages: High thermal stability, good chemical resistance, excellent mechanical properties.
Disadvantages: Irreversible curing process, not recyclable, longer curing times.
Thermoplastic Matrices
Advantages: Can be reformed and recycled, generally have higher impact resistance, faster processing times.
Disadvantages: Typically more expensive, processing requires higher temperatures, can have lower heat resistance than thermosets.
The selection of the matrix material in a composite is a critical decision that influences the performance, processing, and application of the material. While thermosets like epoxy and phenolics have been the traditional choice in aerospace for their high performance, thermoplastics are gaining ground due to their recyclability and ease of processing. The ongoing development in matrix materials aims to enhance properties like toughness, thermal stability, and environmental resistance, further expanding the potential of composites in aerospace and beyond.
The Role of Weaves in Aerospace Composites
The choice of weave pattern is strategic and varies depending on the component's design requirements. For instance, an aerospace component that requires equal strength in both the horizontal and vertical directions might use a plain weave. Conversely, parts that need to be formed into complex shapes without compromising the integrity of the fibers might benefit from a satin weave.
Performance Implications
Strength and Stiffness: The way fibers are interlaced affects load distribution and the composite's ability to handle stress. For example, the straighter the fiber runs within the weave, the higher the tensile strength along that direction.
Impact Resistance: The interlocking nature of certain weaves, such as twill or satin, can distribute impact forces more effectively, enhancing the composite's ability to withstand sudden loads.
Thermal and Acoustic Insulation: Fabric weaves can also be designed to offer insulative properties against heat and sound, contributing to the thermal management and comfort of the aircraft cabin.
Advanced Weave Technologies
With advancements in textile technology, more sophisticated weave patterns are being developed to meet the specific demands of the aerospace industry. 3D weaving technology allows for the creation of near-net-shape preforms with fibers interlaced in three dimensions, providing superior out-of-plane strength and reducing the need for additional reinforcements.
Advanced Forms and the Horizon of Future Materials in Aerospace

The pursuit of aerospace innovation continuously drives the evolution of composite materials. Advanced forms such as three-dimensional weaves and the potential of emergent materials promise to revolutionize the industry. This section explores the cutting-edge developments and the future trajectory of materials that may define the next era of aerospace engineering.
Three-Dimensional Weaving: Shaping the Future
Three-dimensional (3D) weaving technology stands at the forefront of composite material advancement. Unlike traditional two-dimensional fabrics, 3D weaves interlace fibers in multiple directions, creating preforms with inherent strength in the x, y, and z axes. This multi-axial reinforcement translates to significant improvements in impact resistance, delamination resistance, and damage tolerance.
3D Woven Preforms

The creation of 3D woven preforms involves complex weaving processes that can yield near-net-shape components, reducing waste and the need for additional machining or assembly. These preforms are particularly suited for critical load-bearing aerospace structures, such as fuselage sections, where multi-directional strength is paramount.
Braiding and Knitting

Advanced braiding and knitting techniques complement 3D weaving by offering additional geometric flexibility and the capability to integrate functional elements within the composite structure. For instance, braided composites can be engineered to include built-in channels for cooling systems or conduits for electrical wiring.
Next-Generation Fiber Materials
While carbon, glass, and aramid fibers have been the mainstay of composite materials, research is pushing boundaries to develop fibers with even greater capabilities.
Carbon Nanotubes and Graphene
Carbon nanotubes and graphene represent the frontier of high-strength, high-modulus materials. With their exceptional mechanical properties and electrical conductivity, they hold the potential for creating composites that are not only structurally superior but also functionally diverse.
Self-Healing Composites
Self-healing composites are another area of intense research. These materials are designed to autonomously repair microcracks that could otherwise lead to catastrophic failures. Incorporating microencapsulated healing agents or vascular networks within the composite matrix enables the material to recover its integrity upon damage.
Bio-based and Sustainable Composites
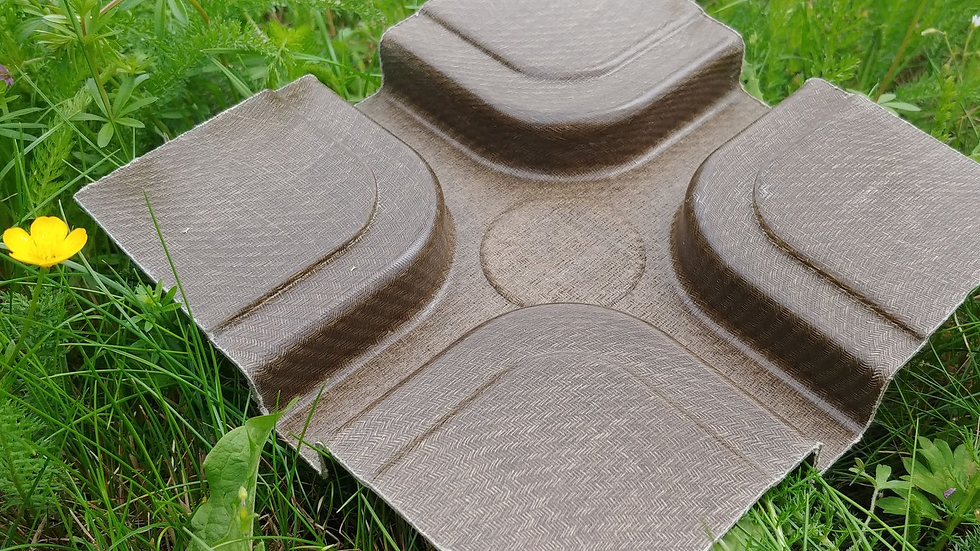
The aerospace industry is also focusing on sustainability. Bio-based composites derived from natural fibers and resins are being developed to reduce the environmental footprint of aircraft manufacturing and operation. These materials aim to match the performance of traditional composites while being recyclable or biodegradable at the end of their service life.
The Role of Smart Materials
Smart materials and structures that can adapt their properties based on external stimuli are no longer science fiction. Piezoelectric composites, shape memory alloys, and electrostrictive materials are being integrated into aerospace components, enabling active vibration control, morphing wing structures, and improved efficiency in aerodynamic profiles.
Design Considerations for Aerospace Applications
The design of composite materials for aerospace applications involves a complex interplay of factors tailored to meet the rigorous demands of flight. From the thickness and weight of the composites to the structural considerations and finish, every detail counts. Let’s delve into the critical design considerations that engineers must navigate when developing composite materials for aerospace use.
Thickness and Weight
In aerospace design, the thickness of the composite material is a critical factor that directly impacts the weight and performance of the aircraft. Optimizing the thickness not only pertains to strength and stiffness requirements but also to the overall weight efficiency of the aircraft. Lighter composites contribute to fuel efficiency and payload capacity, which are paramount in aircraft performance.
Weight Considerations
The weight of composite materials is largely determined by the type and volume of fibers used, the density of the matrix, and the compactness of the weave or lay-up. Advanced composites aim to maximize strength and minimize weight, balancing these attributes through meticulous design and material selection.
Construction and Yarn Size
The construction of composite materials refers to the arrangement and density of the fibers within the matrix. This includes the number of layers, the orientation of the fibers in each layer, and the weave or braiding pattern used.
Yarn Size
Yarn size is another essential consideration, as it determines the weight and thickness of the fabric. In aerospace applications, finer yarns may be used for detailed work or surface layers, while heavier yarns may be selected for their structural properties.
Finish and Surface Treatment
The finish of composite materials is not merely aesthetic; it plays a role in performance, particularly in the aerospace industry. Surface treatments and finishes can provide additional protection against environmental factors, such as UV radiation and moisture, and can also enhance the bonding between the composite and additional coatings or structures.
Compatibility with Other Materials
The finish must be compatible with other materials used in the aircraft. For example, the composite might need to adhere to aluminum or titanium components, requiring a specific surface treatment to ensure a strong bond.
Performance under Environmental Conditions
Composite materials in aerospace are exposed to a wide range of environmental conditions, from temperature extremes to varying humidity levels and exposure to chemicals and UV light. Design considerations must account for these conditions to ensure long-term durability and performance.
Thermal and Moisture Expansion
Engineers must consider the thermal expansion and moisture absorption rates of both the fibers and the matrix. A mismatch in these properties can lead to internal stresses and potential failure of the composite.
Manufacturing and Processability
The selection of materials and design of composites must also take into account the manufacturing processes. Certain designs or materials may require specialized equipment or may affect the speed and cost of production.
Ease of Fabrication
Composites must be designed with a consideration for how easily they can be fabricated into the final component shape. Complex shapes or sizes may necessitate additional steps or technologies in the manufacturing process.
Designing composite materials for aerospace applications is an intricate process that requires a deep understanding of material properties, environmental conditions, and manufacturing capabilities. Engineers must carefully consider each factor to develop composites that meet the high standards of the aerospace industry. As materials technology advances, these considerations will evolve, continuously pushing the boundaries of what is possible in aircraft design and performance.
The Future of Composites in Aerospace
As we conclude our exploration of advanced composites in the aerospace industry, it's clear that the material selection process is not just a matter of technical necessity but a strategic decision that significantly impacts the performance, efficiency, and sustainability of civilian aircraft. Looking forward, the role of composites is poised to expand not only in aviation but in various sectors where their unique properties can be leveraged.
The Crucial Role of Material Selection in Aerospace
The aerospace industry, characterized by its stringent safety standards and relentless pursuit of efficiency, demands materials that meet a complex array of requirements. Advanced composites have risen to this challenge, offering a combination of strength, lightness, and durability that traditional materials can't match.
Selecting the right composite material involves a deep understanding of the specific application, including load conditions, environmental exposure, and performance expectations. This decision-making process is a sophisticated blend of engineering acumen, scientific understanding, and practical considerations like cost and manufacturability.
Advancements and Innovations in Composites
The future of composites in civilian aircraft looks bright and broad. Innovations in fiber materials, such as the development of carbon nanotubes and graphene, are set to push the boundaries of what's possible, offering even higher strength-to-weight ratios and new functionalities.

Moreover, the advent of smart composites, capable of changing their properties in response to external stimuli, opens up possibilities for more adaptive and resilient aircraft designs. These materials could lead to aircraft that self-monitor and respond dynamically to varying flight conditions, enhancing performance and safety.
Sustainability and Composites
Sustainability is another frontier where advanced composites are making significant inroads. The development of bio-based composites and efforts to make composites more recyclable align with the growing emphasis on environmental stewardship in the aerospace industry. These advancements are not just beneficial for the planet; they also resonate with the shifting priorities of consumers and regulators.
Beyond Aerospace
The potential of advanced composites extends beyond the aerospace industry. Their high-performance characteristics make them ideal candidates for a variety of applications, including automotive, renewable energy (especially in wind turbine blades), and infrastructure. In each of these fields, the advantages of composites can lead to more efficient, durable, and sustainable solutions.
What's Next!
Discover the future of composite manufacturing with Addcomposites! Here's how you can get involved:

Stay Informed: Subscribe to our newsletter to receive the latest updates, news, and developments in AFP systems and services. Knowledge is power, and by staying informed, you'll always have the upper hand. Subscribe Now
Experience Our Technology: Try our cutting-edge simulation software for a firsthand experience of the versatility and capability of our AFP systems. You'll see how our technology can transform your production line. Try Simulation
Join the Collaboration: Engage with us and other technical centers across various industries. By joining this collaborative platform, you'll get to share ideas, innovate, and influence the future of AFP. Join Collaboration
Get Hands-On: Avail our educational rentals for university projects or semester-long programs. Experience how our AFP systems bring about a revolution in composite manufacturing and leverage this opportunity for academic and research pursuits. Request for Educational Rental
Take the Next Step: Request a quotation for our AFP systems. Whether you're interested in the AFP-XS, AFP-X, or SCF3D, we are committed to offering cost-effective solutions tailored to your needs. Take the plunge and prepare your production line for the next generation of composite manufacturing. Request Quotation
At Addcomposites, we are dedicated to revolutionizing composite manufacturing. Our AFP systems and comprehensive support services are waiting for you to harness. So, don't wait – get started on your journey to the future of manufacturing today!
Commentaires