The Evolution of Automated Fiber Placement: Early Developments to Modern Applications
- Pravin Luthada
- Jan 6, 2023
- 7 min read
Updated: Jan 27, 2024
Introduction
Automated fiber placement (AFP) technology has undergone significant development since its introduction in the late 1980s. This article will provide an overview of the evolution of AFP systems from 1990 to 2023, with a focus on the development of thermoset and thermoplastic applications. The benefits and limitations of AFP systems will also be discussed, as well as potential applications. Article concludes with a summary of the key points discussed.
Jump to the right section
Development of Automated Fiber Placement (AFP) systems from 1990 to 2000

![AFP head [2]](https://static.wixstatic.com/media/dfe896_2f5e095d151342638a9f61c4343c7752~mv2.jpg/v1/fill/w_204,h_247,al_c,q_80,enc_avif,quality_auto/dfe896_2f5e095d151342638a9f61c4343c7752~mv2.jpg)
AFP systems were introduced in the late 1980s, combining the features of ATL and filament winding
Limitations of the previous approach were overcome through separate bobbins and individually driven tapes
AFP machine demonstrated with an offline programming system in 1991
AFP System demonstrated controls of layup speed, pressure, temperature, and tape tension
Layup speed of 7 m/min resulted in productivity of 5 kg/h, comparable to Automated Tape Laying (ATL) in 1992
Layup reliability was improved in 1992 by using cooled creel houses
Mechanical properties of laminates made with AFP and hand layup were found to be comparable in 1992
A number of technical issues prevailed during the development of AFP, including tension in the tows, reliability, productivity, and layup accuracy
1992 saw an increase in the number of tows and the integration of the system with the CAD system which increased productivity.
The 1992 steering program improved productivity by focusing on the reliability and delivery of tows along curvilinear paths (steering). Steering allows for additional design freedom and potential improvement in mechanical performance with smaller tape widths.
The AFP reduced material wastage rates from 62% to 6% and increased productivity by 450% for a single 12.7 mm wide tape.
AFP reduces cost by 43% compared to manual layup.
AFP systems were extremely expensive, up to $6 million, with a limited range of affordability, reliability, and productivity
AFP developments that focus on thermoplastic
![Continuous press style process [1]](https://static.wixstatic.com/media/dfe896_5c65d9f2eee5463d9bfd3394ead8d00e~mv2.jpg/v1/fill/w_563,h_420,al_c,q_80,enc_avif,quality_auto/dfe896_5c65d9f2eee5463d9bfd3394ead8d00e~mv2.jpg)
![Long soak AFP process [1]](https://static.wixstatic.com/media/dfe896_a4ac764739ca4b688470b7115313dca7~mv2.jpg/v1/fill/w_709,h_475,al_c,q_80,enc_avif,quality_auto/dfe896_a4ac764739ca4b688470b7115313dca7~mv2.jpg)
Early approaches to developing thermoplastic layup with AFP identified trade-offs between layup pressure, temperature, and speed.
Layup quality is affected by layup speed, which is limited by the time needed to heat material above the melting point.
Layup speeds of 3.6 m/min to 5 m/min were reported, resulting in lower productivity compared to thermoset materials
Optimal processing conditions for reduced void growth and improved interfacial bonding were explored
Heating methods include hot gas torches and lasers
Curing of thermoset prepregs with electron beam or UV light for faster processing and reduced thermal stresses achieved with limited layup speeds and reduced mechanical properties.
Development of Automated Fiber Placement (AFP) systems from 2000 -2012
![Large AFP machine [3]](https://static.wixstatic.com/media/dfe896_19be3257cb0d4536851d19d589754f45~mv2.jpg/v1/fill/w_904,h_720,al_c,q_85,enc_avif,quality_auto/dfe896_19be3257cb0d4536851d19d589754f45~mv2.jpg)
From 2000, the focus shifted to addressing issues of affordability, process reliability, and productivity
AFP was mainly used in military and space programs until 2000
Process reliability improved through the use of automated splicing and layup error detection systems
Infrared heating of thermoset tape used to increase tack levels and reduce layup errors
Material delivery improved through the reduction of feed length and minimizing redirects and twists in the tow
The Current State of Automated Fiber Placement: A Review of the Latest Developments in AFP Technology
Industrial robots and advances in sensors, networks, and software have allowed for more powerful and smart AFP systems.
These systems can now be created using any industrial robotic arm or CNC, rather than being limited to complete CNC unit integration.
The cost of accessing new AFP systems has decreased about 100x, with one of the best AFP systems starting at around $3000-$4000 per month for a lease ready for industrial use.

The latest AFP systems are easier to program, monitor process data, and build quality layups thanks to their built-in offline and digital twin programming capabilities. This data can also be used to generate quality reports at the end of the layup process.
These systems can perform filament winding and tape winding for tanks, allowing manufacturers to produce all AFP and filament wound parts with one system.
These systems are not limited to thermosets or thermoplastics and can work with a variety of materials, including thermosets, thermoplastics, ceramic prepregs, and dry fiber tapes.
These systems have a wide range of applications, including:

Winding Hydrogen Tanks with Thermoset and Thermoplastics
Creating dry preforms for RTM machines
Creating thermoplastic preform blanks for thermoforming machines
Reinforcing large-scale 3D printed parts with thermoplastic tapes
The layup of thermoset prepregs on 3D open and closed shapes
The layup of thermoplastic prepregs on 3D open and closed shapes
Placement of ceramic tapes on 3D open and closed shapes
Placement of dry tapes on 3D open and closed shapes.
The recent advances allowed the AFP to reach 100-300 installations per year by 2025, enabling a widespread ecosystem for further development
Benefits and limitations of Automated Fiber Placement systems
It is important to note that while there are benefits to using AFP systems, there are also limitations to consider. It is important to weigh the pros and cons of using AFP in a specific application to determine if it is the right choice for a particular project. In some cases, the benefits of faster production times, improved efficiency, increased performance and strength, and cost-effectiveness may outweigh the limitations such as size and material constraints. In other cases, manual processes may be a better fit depending on the specific requirements of the project. It is important to carefully assess the needs and capabilities of a project before deciding on the best manufacturing approach.

Faster production times: The AFP process involves laying down unidirectional fibers in a pre-programmed pattern, rather than manually placing individual strands. This can reduce production times by up to 40%.
Improved efficiency: AFP can improve efficiency and reduce material waste compared to traditional manual hand layup processes.
Increased performance and strength: AFP produces more consistent results than manual hand layup, resulting in stronger bonds between layers and improved performance and strength in the finished product.
Cost-effectiveness: The improved efficiency and reduced material waste associated with AFP can make it a more cost-effective option compared to other manufacturing processes.
Simplicity: Any graduate student knowing the basics of composites can easily operate the latest AFP system without requiring a high level of technical knowledge and expertise to program and operate the equipment.
Accessible: AFP-XS fiber placement systems can be very easy to acquire and can be operational within days, making it a compelling choice for smaller manufacturers.
Shapes: AFP systems can work as tape winding and filament winding systems, capable of producing highly complex shapes with complex fiber orientation
Material: AFP systems can work across thermoset, thermoplastic, and dry fabrics, allowing much greater freedom in material selection
Health and safety: Moving the operator away from the composites processing environment ensures better health conditions and lowers the consumables requirements.
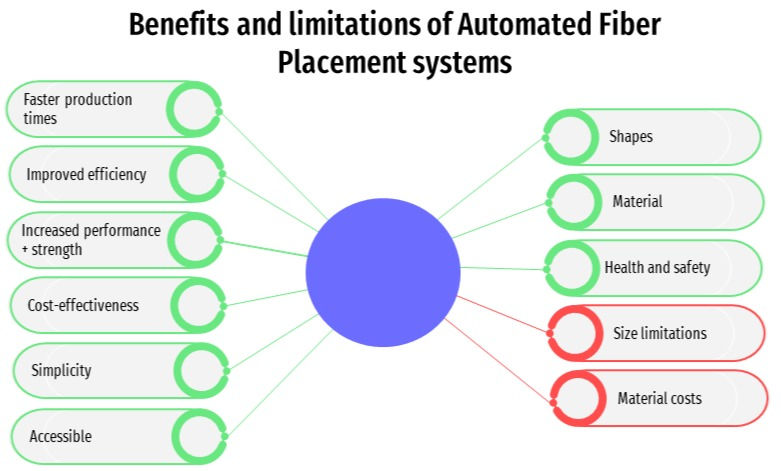
However, there are also some limitations to consider when using AFP systems:
Size limitations: AFP systems may not be suitable for parts with a very small or intricate geometry e.g. a watch case, small hinge, etc. as the tows may not be able to be placed accurately in these areas.
Material costs: Materials used in AFP processes are relatively expensive i.e. 10-15% higher cost compared to the materials used in manual processes.
Potential applications of Automated Fiber Placement systems
Automated fiber placement (AFP) systems are used in a variety of industries and applications, including:

Aerospace: AFP is widely used in the aerospace industry to manufacture aircraft components such as wing spars, fuselage panels, and bulkheads.
Automotive: AFP can be used to manufacture composite parts for the automotive industry, such as body panels, drivetrain components, and suspension parts.
Construction: AFP can be used to manufacture composite materials for use in construction, such as bridge decks, beams, and columns.
Wind energy: AFP can be used to manufacture composite wind turbine blades, which are typically longer and more flexible than traditional blades.
Sporting goods: AFP can be used to manufacture composite materials for use in sporting goods, such as golf clubs, tennis racquets, and skis.

Marine: AFP can be used to manufacture composite materials for use in the marine industry, such as hulls for boats and ships.
Medical: AFP can be used to manufacture composite materials for use in medical devices, such as implantable devices and prosthetics.
Consumer products: AFP can be used to manufacture composite materials for use in consumer products, such as electronics and appliances.

In general, AFP is well-suited for manufacturing lightweight, complex-shaped structures that are optimized for load-carrying and efficiency. Its ability to quickly and accurately place fibers in a predetermined pattern makes it a valuable tool for a wide range of industries and applications.
Summary
The automated fiber placement system has undergone significant development since its introduction in the late 1980s. In the early 1990s, the focus was on improving the reliability and productivity of the process. In the 2000s, the focus shifted to thermoset materials and improving the reliability of the system. In the present day, AFP systems have become more affordable and easier to program as they benefit from better robotics, computations, and software capability. Now, these can work with a wide range of materials including thermosets, thermoplastics, ceramic prepregs, and dry fiber tapes, enabling a wide range of applications, including the winding of hydrogen tanks, the creation of dry preforms for RTM machines, the production of thermoset and thermoplastic prepregs on 3D open and closed shapes, and the placement of ceramic and dry tapes on 3D shapes. Potential applications of AFP systems include the production of hydrogen tanks, aerospace parts, future mobility parts such as lightweight drones, etc. Overall, the AFP system has the potential to revolutionize the manufacturing industry with its advanced capabilities and versatility.
Комментарии