The Shift in Composite Manufacturing: From Traditional to Intelligent
- Pravin Luthada
- Jul 28, 2023
- 7 min read
We would like to express our deepest gratitude to Yonglin Chen, Junming Zhang, Zefu Li, Huliang Zhang, Jiping Chen, Weidong Yang, Tao Yu, Weiping Liu, and Yan Li for the article "Manufacturing Technology of Lightweight Fiber-Reinforced Composite Structures in Aerospace: Current Situation and toward Intellectualization". Your invaluable insights into the manufacturing technologies for continuous fiber-reinforced polymer composites have significantly contributed to our understanding of the subject. You work has significantly contributed to the following blog. Your work has not only enlightened us but also our readers. We appreciate the depth of research and the comprehensive review of the technologies, their evolution, and future trends. Your contribution to this field is truly commendable. Thank you for your dedication and for sharing your knowledge with us
1. Key Highlights:
The review provides a comprehensive overview of the manufacturing technologies for continuous fiber-reinforced polymer composites.
It discusses the advantages and disadvantages of each technology, as well as the challenges they face.
The review highlights the trend toward numeralization and intellectualization of these technologies, with a focus on process monitoring, controlling, and property prediction.
It also provides a comparison of the main manufacturing technologies for fiber-reinforced composite structures.
The review concludes with a discussion on the future of composite manufacturing, highlighting the potential for the development of intelligent platforms and smart composite structures.

2. Traditional Molding Technology
Traditional molding technologies for fiber-reinforced polymer composites primarily include Autoclave and Out of Autoclave (OoA) methods.

2.1. Autoclave
Autoclave is a process that uses heat and pressure to cure composite materials. It is known for producing high-quality composites with good repeatability, high fiber volume content, low or no porosity, and reliable mechanical properties.
However, it is highly time-consuming, costly, and has size limitations.
2.2. Out of Autoclave (OoA)
OoA is a process that cures composites without the use of an autoclave. It is a lower-cost method that can produce large structure sizes.
However, it often results in high porosity and low fiber volume fraction in the final product.
Movement Towards Numeralization and Intellectualization
The traditional molding technologies are moving towards numeralization and intellectualization to improve efficiency, reduce costs, and enhance the quality of the final products. Here are some of the key developments:

Process Monitoring: The use of wireless strain meters and FBG-based sensors for process-induced strain monitoring is an example of numeralization. These technologies provide real-time data on the manufacturing process, enabling better control and optimization.
Process Controlling: The development of microwave curing setups and knowledge-based systems represents a move towards intellectualization. These technologies use advanced algorithms and machine learning techniques to control and optimize the manufacturing process.
Property and PID Prediction: The use of multi-physics coupling numerical models and the combination of finite element methods and convolutional neural networks (CNNs) for property and PID prediction is another example of numeralization and intellectualization. These models use numerical methods and artificial intelligence to predict the properties of the final product, enabling better design and optimization of the manufacturing process.
3. Liquid Composite Molding (LCM)
Liquid Composite Molding involves the use of a dry fiber preform laid in a mold cavity, followed by the injection of resin into the mold until the entire cavity is filled. The resin-infused preform is then cured, cooled, and demolded.
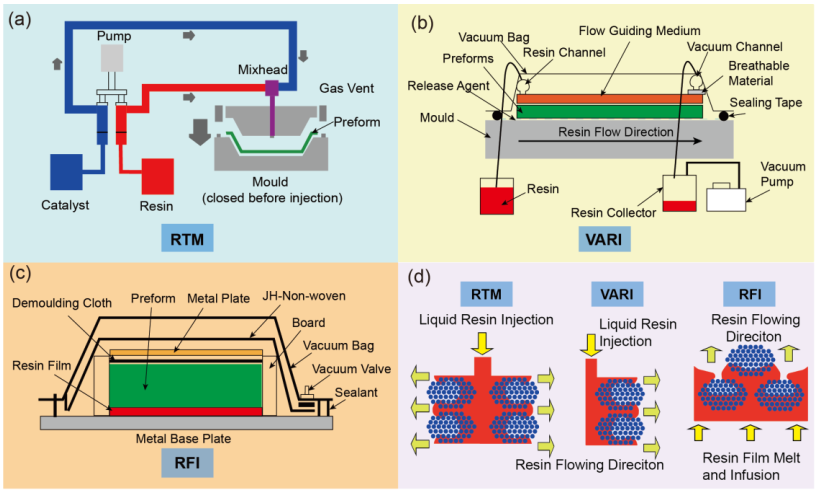
3.1. Resin Transfer Molding (RTM)
RTM is a variant of LCM that has been increasingly adopted by the aerospace industry for molding high-performance composite structures. It allows for excellent dimensional tolerance control and ensures high surface quality and net dimensional forming.
However, RTM can result in high porosity and has limited structure size.
3.2. Variants of RTM
There are three main variants of RTM: Low Pressure RTM (LP-RTM), High Pressure RTM (HP-RTM), and Compression RTM (CRTM).

LP-RTM: This process uses an injection pressure of 10-20 bar and a final hydrostatic pressure similar to the curing pressure in VARI. It is cheaper and commonly used for manufacturing aerospace engineering parts.
HP-RTM: The injection pressure in HP-RTM is 60-100 bar, higher than that in LP-RTM. The high pressure can accelerate the resin flowing speed to reduce the injection time.
CRTM: This is an advanced composite molding process for high-fiber-volume components. Unlike the closed mold in RTM, in CRTM, a gap is left between the upper mold and the preform before the curing process.
Movement Towards Numeralization and Intellectualization
The LCM technologies are moving towards numeralization and intellectualization to improve efficiency, reduce costs, and enhance the quality of the final products. Here are some of the key developments:

Process Monitoring: The use of recurrent neural networks (RNNs) serving as soft sensors for process monitoring is an example of numeralization. These technologies provide real-time data on the manufacturing process, enabling better control and optimization.
Process Controlling: The development of simulation-based optimization and control methodologies represents a move towards intellectualization. These technologies use advanced algorithms and machine learning techniques to control and optimize the manufacturing process.
Property and PID Prediction: The use of finite difference methods for property and PID prediction is another example of numeralization and intellectualization. These models use numerical methods to predict the properties of the final product, enabling better design and optimization of the manufacturing process.
4. Automated Layup Technology (ALT)
Automated Layup Technology involves the use of automated systems to lay up composite materials, which can significantly improve efficiency, reduce material consumption, and increase the level of automation.

4.1. Layup Path Planning
Layup path planning is a crucial aspect of high-efficiency manufacturing and high-performance composite structures. It involves determining the sequence and direction of the tows or tapes laid on the mold surface.

4.2. In situ Consolidation Process Parameters
In-situ consolidation involves the simultaneous placement and consolidation of the composite material during the manufacturing process. This process can improve the quality of the final product by reducing defects and voids in the composite material.
4.3. In situ Inspection and Defect Detection
In-situ inspection and defect detection are critical in the automated layup process. Various inspection techniques, such as thermography and ultrasonic inspection, are used to detect defects in the composite material during the manufacturing process.
4.4. Characteristic Prediction
Characteristic prediction involves accurately predicting the properties of ALT composites, which are influenced by a variety of process parameters. The combination of ALT with AI can generate an intelligent technique for this challenge.
4.5. Advanced Placed Ply
Advanced placed ply is a new automated fiber placement method proposed for improving the damage tolerance of composites. It combines the advantages of fabrics and unidirectional layers in an automated production process.
Movement Towards Numeralization and Intellectualization
The ALT technologies are moving towards numeralization and intellectualization to improve efficiency, reduce costs, and enhance the quality of the final products. Here are some of the key developments:
Process Monitoring: The use of FBG-based sensors, interdigital electrode array films, piezoelectric material-based sensors, and convolution neural networks (CNNs) for process monitoring is an example of numeralization. These technologies provide real-time data on the manufacturing process, enabling better control and optimization.
Process Controlling: The development of thermographic online monitoring systems and explainable Artificial Intelligence methods represents a move towards intellectualization. These technologies use advanced algorithms and machine learning techniques to control and optimize the manufacturing process.
Property and PID Prediction: The use of comprehensive curing optimization algorithms, neural network-based control systems, and machine learning methods for property and PID prediction is another example of numeralization and intellectualization. These models use numerical methods and artificial intelligence to predict the properties of the final product, enabling better design and optimization of the manufacturing process.
5. Additive Manufacturing
Additive Manufacturing involves the use of 3D printing technologies to create objects from 3D model data, usually layer upon layer. It's a rapidly growing field that offers significant advantages over traditional manufacturing methods, including the ability to create complex geometries, use a wide range of materials, and customize products.

5.1. Traditional Additive Manufacturing

Traditional Additive Manufacturing for continuous fiber-reinforced composites includes processes such as Fused Deposition Modeling (FDM), Fused Filament Fabrication (FFF), Directed Energy Deposition (DED), and Laminated Object Manufacturing (LOM).
These processes have their advantages and limitations, with FDM being the most widely used due to its simplicity, low cost, and rapid production efficiency.
5.2. Multi-Degree of Freedom Additive Manufacturing
Multi-Degree of Freedom Additive Manufacturing is a more advanced method that can overcome some of the limitations of traditional additive manufacturing. This method uses a spatial multi-degree-of-freedom device, such as a five-axes machining center or a six-axes manipulator, to accomplish non-single direction manufacturing.
Movement Towards Numeralization and Intellectualization
The Additive Manufacturing technologies are moving towards numeralization and intellectualization to improve efficiency, reduce costs, and enhance the quality of the final products. Here are some of the key developments:
Process Monitoring: The use of neural network-based inverse predictive mode for process monitoring is an example of numeralization. These technologies provide real-time data on the manufacturing process, enabling better control and optimization.
Process Controlling: The development of neural network-based predictive models represents a move towards intellectualization. These technologies use advanced algorithms and machine learning techniques to control and optimize the manufacturing process.
Property and PID Prediction: The use of teaching learning-based optimization and artificial neural networks for property and PID prediction is another example of numeralization and intellectualization. These models use numerical methods and artificial intelligence to predict the properties of the final product, enabling better design and optimization of the manufacturing process.
6. Summary and Future Trends
In the ever-evolving world of manufacturing, the technologies for creating fiber-reinforced polymer composites have seen a significant transformation. This journey, from traditional molding technologies to more advanced and efficient methods, has been both challenging and rewarding.
We've seen how traditional molding technologies like Autoclave and Out of Autoclave have served as the foundation of composite manufacturing, despite their limitations in terms of cost, time, and product size.
Liquid Composite Molding has emerged as a cost-effective and efficient alternative, although it too faces challenges such as high porosity and limited structure size.
The advent of Automated Layup Technology has brought about a new era of efficiency and automation, leveraging advanced techniques like layup path planning and in situ consolidation.
Additive Manufacturing, a rapidly growing field, offers significant advantages over traditional methods, enabling the creation of complex geometries and customized products.
But the journey doesn't end here. The future of composite manufacturing lies in the numeralization and intellectualization of these technologies. We're moving towards an era where intelligent platforms will integrate design and manufacturing technologies, leading to the development of smart composite structures. These structures will not only be used in advanced aircraft but will also play a crucial role in the exploration of outer space.
What's Next!
Discover the future of composite manufacturing with Addcomposites! Here's how you can get involved:
Stay Informed: Subscribe to our newsletter to receive the latest updates, news, and developments in AFP systems and services. Knowledge is power, and by staying informed, you'll always have the upper hand. Subscribe Now
Experience Our Technology: Try our cutting-edge simulation software for a firsthand experience of the versatility and capability of our AFP systems. You'll see how our technology can transform your production line. Try Simulation
Join the Collaboration: Engage with us and other technical centers across various industries. By joining this collaborative platform, you'll get to share ideas, innovate, and influence the future of AFP. Join Collaboration
Get Hands-On: Avail our educational rentals for university projects or semester-long programs. Experience how our AFP systems bring about a revolution in composite manufacturing and leverage this opportunity for academic and research pursuits. Request for Educational Rental
Take the Next Step: Request a quotation for our AFP systems. Whether you're interested in the AFP-XS, AFP-X, or SCF3D, we are committed to offering cost-effective solutions tailored to your needs. Take the plunge and prepare your production line for the next generation of composite manufacturing. Request Quotation
At Addcomposites, we are dedicated to revolutionizing composite manufacturing. Our AFP systems and comprehensive support services are waiting for you to harness. So, don't wait – get started on your journey to the future of manufacturing today!
Commenti