The Thermoset Composites Odyssey: An Expedition
- Aman Sahu
- Jul 11, 2023
- 3 min read
Introduction
In the vast landscape of composite materials, thermoset composites are a standout, boasting unique properties and a plethora of applications. This article delves into the world of thermoset composites, shedding light on their properties, manufacturing processes, and joining techniques. We aim to provide a comprehensive understanding of these materials, which have revolutionized various industries due to their distinct characteristics and wide-ranging uses.
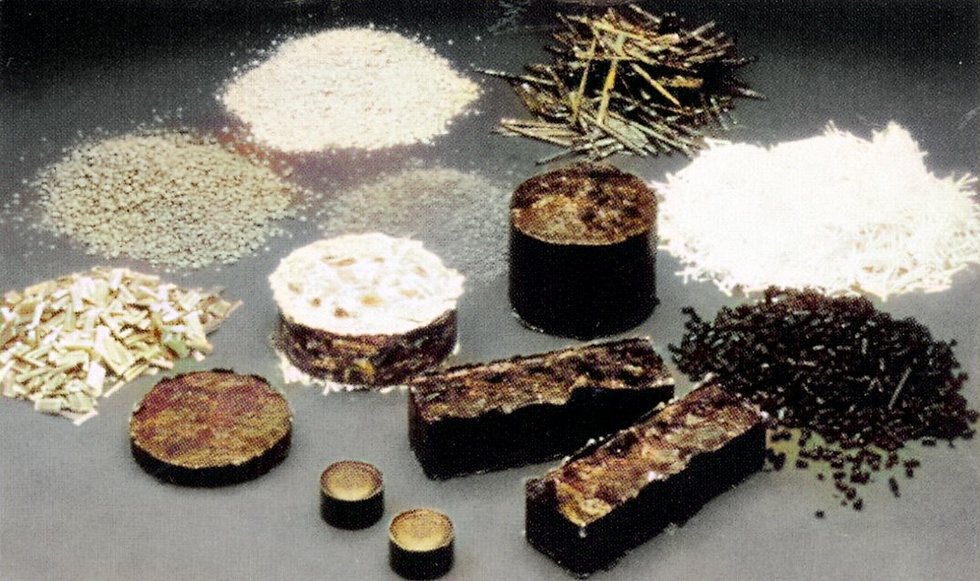
Decoding Thermoset Composites
Thermoset composites are a class of materials that, once cured, cannot be remelted or reformed. They form rigid three-dimensional molecular chains through a process called cross-linking. The density of these cross-links dictates the rigidity and thermal stability of the material. Thermosets may soften to some extent at elevated temperatures, a characteristic sometimes used to create a bend or curve in tubular structures, such as filament-wound tubes. Despite their brittle nature, thermosets are often used with some form of filler and reinforcement. Thermoset resins offer easy processability and better fiber impregnation due to their liquid state at room temperature, making them ideal for various processes such as filament winding, pultrusion, and RTM. They also offer superior thermal and dimensional stability, rigidity, and resistance to electricity, chemicals, and solvents. The most common resin materials used in thermoset composites include epoxy, polyester, vinyl-ester, phenolics, cyanate esters, bismaleimides, and polyimides.
Fabrication Techniques for Thermoset Composites
The fabrication of thermoset composites depends on the specific manufacturing method in use. For instance, the injection molding process utilizes molding compounds in pellet form, unsuitable for filament winding or pultrusion. Filament winding and pultrusion, on the other hand, utilize continuous fibers and wet resin systems. The roll wrapping process requires prepreg systems for making various products such as golf club shafts and bicycle tubes. Prepregs are used in a wide array of applications, including aerospace parts, sporting goods, printed circuit boards, medical components, and industrial products. Despite their higher cost, prepreg materials offer advantages over metals such as higher specific stiffness, specific strength, corrosion resistance, and faster manufacturing.

Joining Techniques for Thermoset Composites
Joining thermoset composites is a critical aspect of their manufacturing process. The choice of joining method hinges on the specific requirements of the application, including the type of thermoset composite, the design of the parts to be joined, and the performance requirements of the final product. Thermoset prepregs require a longer
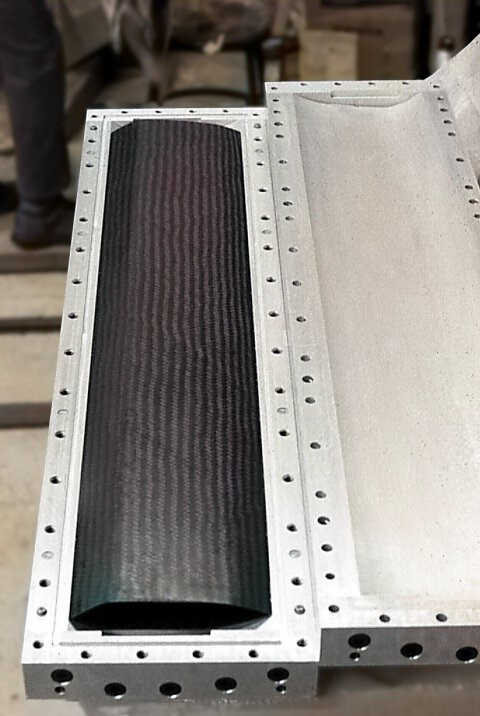
process cycle time, typically in the range of 1 to 8 hour due to their slower kinetic reactions. To meet higher production needs, rapid-curing thermoset prepregs are being developed. The most common resin used in thermoset prepreg materials is epoxy. These prepregs are generally stored in a low-temperature environment and have a limited shelf life. Room-temperature prepregs are also becoming available. Usually, the resin is partially cured to a tack-free state called B-staging. Several additives (e.g., flame retardants, catalysts, and inhibitors) are added to meet various end-use properties and processing and handling needs.
Conclusion
Grasping the complexities of thermoset composite materials, their manufacturing, and joining techniques is vital for their effective application across various fields. This knowledge not only deepens our understanding of these materials but also paves the way for innovation and design. As we continue to navigate the world of composite materials in our forthcoming articles, we will delve deeper into these topics, offering a detailed exploration of specific manufacturing methods, material selection strategies, and more. This article serves as a stepping stone for the upcoming deep dives into the fascinating world of composite materials. Stay tuned for more enlightening content on this captivating subject.
What's Next!
Discover the future of composite manufacturing with Addcomposites! Here's how you can get involved:
Stay Informed: Subscribe to our newsletter to receive the latest updates, news, and developments in AFP systems and services. Knowledge is power, and by staying informed, you'll always have the upper hand. Subscribe Now
Experience Our Technology: Try our cutting-edge simulation software for a firsthand experience of the versatility and capability of our AFP systems. You'll see how our technology can transform your production line. Try Simulation
Join the Collaboration: Engage with us and other technical centers across various industries. By joining this collaborative platform, you'll get to share ideas, innovate, and influence the future of AFP. Join Collaboration
Get Hands-On: Avail our educational rentals for university projects or semester-long programs. Experience how our AFP systems bring about a revolution in composite manufacturing and leverage this opportunity for academic and research pursuits. Request for Educational Rental
Take the Next Step: Request a quotation for our AFP systems. Whether you're interested in the AFP-XS, AFP-X, or SCF3D, we are committed to offering cost-effective solutions tailored to your needs. Take the plunge and prepare your production line for the next generation of composite manufacturing. Request Quotation
At Addcomposites, we are dedicated to revolutionizing composite manufacturing. Our AFP systems and comprehensive support services are waiting for you to harness. So, don't wait – get started on your journey to the future of manufacturing today!
Comentarios