Traditional Filament winding vs. Robotic Winding
- Pravin Luthada
- Dec 5, 2022
- 4 min read
Updated: Jan 5, 2023
Contents
Overview
Traditional filament winding is a fairly common industrial low-tech process, limited to axially symmetric shapes such as tubes, ducts, or pressure vessels. The emergence of industrial robot technology has enabled the realization of novel winding approaches. In these methods, the fibers are either pulled off by the translation of a fiber guide around turning points or by the rotary motion of a mandrel about multiple axes instead of the traditional way of rotating about just one axis.
The article covers a brief description of each winding approach with their pros and cons. towards the end hybridization trend is highlighted with AFP and CFRP 3D printing technology.
Traditional Filament Winding
Filament winding is a technique primarily used to manufacture hollow, circular, or prismatic parts such as pipes and tanks. It is performed by winding continuous fiber tows onto a rotating mandrel using a specialized winding machine. Filament wound parts are commonly used in the aerospace, energy, and consumer product industries.

Continuous fiber tows are fed through a fiber delivery system to the filament winding machine, where they are wound onto a mandrel in a predetermined, repeating geometric pattern. The tow location is guided by a fiber delivery head, which is attached to a movable carriage on the filament winding machine. The relative angle of the tow to the mandrel axis, called the winding angle, can be tailored to provide strength and stiffness in the desired directions. When sufficient layers of tow have been applied, the resulting laminate is cured on the mandrel. The overall size and shape of the finished part are determined by the mandrel shape and thickness of the laminate.
The winding angles will determine the mechanical properties of the composite part, such as strength, stiffness, and weight. The density of the laminate is the result of the tension of the tows during winding. The composite parts made through these methods generally have good strength-to-weight properties.
Robotic Winding
The emergence of industrial robot technology has enabled the realization of novel winding approaches. In these methods, the fibers are either pulled off by the translation of a fiber guide around turning points or by the rotary motion of a mandrel about multiple axes instead of the traditional way of rotating about just one axis

The traditional classification of winding
Perimeter winding: the filaments are wound around the circumference of a tool.
Cross winding: the filaments are wound in between gaps in the tool.
Mono-axial cross winding
Mono-axial perimeter winding
Poly-axial cross winding
Poly-axial cross winding
Mono-axial perimeter winding, for example, is commonly used for the creation of rotational components. While monoaxial translation winding is typically applied to create two-dimensional framework structures. In order to realize three-dimensional truss structures poly-axial winding is mandatory to prevent fiber slippage while winding rods coming out of the plane.
![(A) Mono-axial cross winding [12]; (B) mono-axial perimeter winding [13]; (C) poly-axial cross winding [14]; (D) poly-axial cross winding](https://static.wixstatic.com/media/dfe896_529e7e325be0405faf4597bc51bb7f98~mv2.png/v1/fill/w_980,h_303,al_c,q_85,usm_0.66_1.00_0.01,enc_avif,quality_auto/dfe896_529e7e325be0405faf4597bc51bb7f98~mv2.png)
Traditional vs. Robotic Winding
Traditional filament winding is a fairly common industrial low-tech process, limited to axially symmetric shapes such as tubes, ducts, or pressure vessels. The two-axis winder, the simplest production layout, controls the rotation of the mandrel and the transverse movement of the conveying unit, so it is only capable of producing reinforced pipes and tubes. yarns. In addition, the traditional four-axis machine is a general-purpose winder, capable of producing pressure vessels as well. Controlled motion degrees of freedom typically include shaft rotation, horizontal conveying, perpendicular conveying (crossfeed), and rotating yarn delivery head mounted on the cross-feed mandrel. However, these solutions still depend on frequent operator intervention during various winding operations, which has a significant impact on productivity.
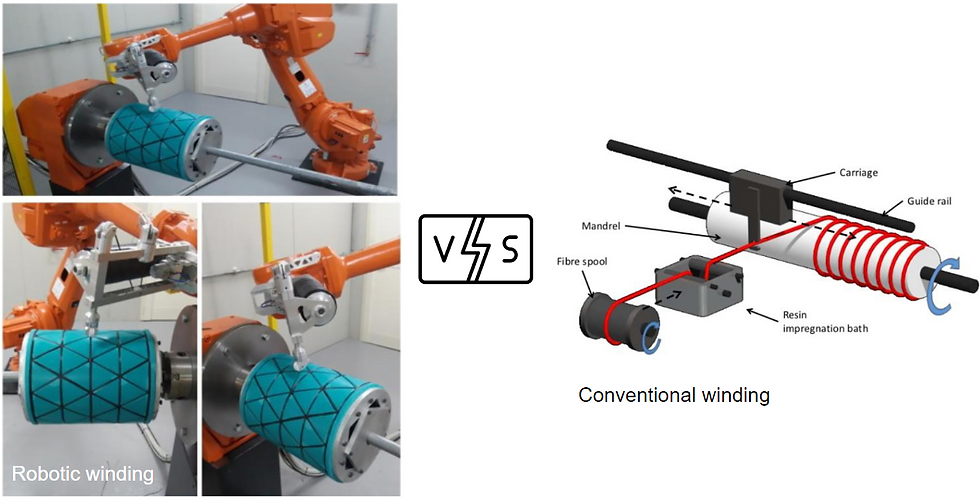
Robotic Winding is mainly used for advanced applications and it is a great match for tape winding, resulting in higher-quality parts. In this technique it is also possible to automate ancillary operations previously performed manually, Such as placing mandrels, knotting and cutting threads, and loading mandrels covered with wet yarn into the furnace. grill, chuck extraction, etc.

All configuration combinations can use ready-to-use or custom robots, with ABB, KUKA, and Fanuc being the main suppliers, and equipment investment directly correlates with the number of robots used. its use and degree of customization. The great flexibility offered by robotic winding could have broad market penetration potential, allowing the diversification of fiber-reinforced products and applications into new areas.
Adoption trend
Prospects of development for the fabrication of composite tanks using robotic winding keep emerging. A consolidated trend is the adoption of automated and integrated industrial cell units and production lines for composite tank construction, therefore, offering a complete turnkey solution in manufacturing. Another technological breakthrough may be represented by winding hybridization with other processes such as continuous fiber 3D printing and Automated Fiber Placement, which can add fibers where they are needed with speed, precision, and practically zero waste.
Tape and Filament Winding capability for Automated Fiber Placement (AFP) system
Addcomposites now offers the tape and filament winding capability for the AFP system that can work across the material line from Dry Fiber, Thermoset, and Thermoplastic. (Learn more >)
Don't miss out on the opportunity to upgrade your AFP system with tape and filament winding capability! Contact Pravin Luthada or James Kuligoski via LinkedIn now to customize a solution for your business.
Complete course
The above article is part of the course Design and Development of Compressed Hydrogen Storage Tanks. The course covers a lot more, starting with discussing challenges in material selection and manufacturing practices, as well as cutting-edge trends being explored. Key problems in the design and analysis of the hydrogen reservoir are also addressed. Finally, testing and certification requirements are discussed as they play an important role in industry acceptance.
About Addcomposites
Addcomposites is the provider of the Automated Fiber Placement (AFP) ecosystem - including the Fiber Placement System (AFP-XS), 3D Simulation and Programming Software (AddPath), and Robotic Cells (AddCell). With the leasing program for the AFP system (AFPnext), composites manufacturers can work with thermosets, thermoplastics, dry fiber placement, or in combination with 3D Printers on a monthly basis.
Comments