Understanding Composites in Production Machines
- Pravin Luthada
- Aug 13, 2023
- 7 min read
The blog article is a summary of the work "Composites in production machines" by wonderful authors H.-C. Möhring. The author, H.-C. Möhring, provides a comprehensive overview of the application of composite materials in production machines, highlighting their potential, challenges, and real-world implementations. Through the research, Möhring emphasizes the transformative role of composites in enhancing machine performance and design flexibility.
Did you know?
While most of us imagine machine tools to be made of heavy metals, the future is lighter, stronger, and... unexpected. Imagine a high-speed machine tool that's not made of traditional steel but of composite materials like carbon fiber. Surprised?

The world of production machines is undergoing a transformation, and the hero of this change is none other than composites. These materials, which were once the domain of aerospace and automotive industries for their lightweight properties, are now revolutionizing the very core of machine tools. From achieving a weight reduction of a whopping 18 kg in a single tool to enhancing machine performance with high stiffness and damping properties, composites are redefining what's possible.
And it's not just about weight. Composites are proving to be thermal champions, maintaining consistent performance even in varying temperatures. From spindles to tool bodies, the shift from traditional materials to composites is evident, and real-world examples are emerging everywhere.
So, the next time you think of a machine tool, don't just picture heavy metals. Envision a future where composites rule, making machines lighter, more efficient, and yes, unexpected! Read along if you are still curious!
1. Introduction
Evolution of Materials in Machine Tools:

Historically, the design, manufacturing, and application of composite parts have been primarily influenced by the aerospace and automotive industries.
The primary motivation behind using such materials was to achieve mass reduction, which in turn would lead to fuel savings.
Over the years, there has been a significant advancement in the manufacturing processes of composite parts, aiming for cost-efficient realization.
The last two decades have witnessed a substantial increase in automation levels in composite parts manufacturing, thanks to ongoing developments in both industry and research institutions.
Rising Popularity of Composite Materials:
Given the advancements in manufacturing and the inherent benefits of composite materials, their applications have expanded beyond the aerospace and automotive sectors.
The general machine construction domain, especially the machine tool sector, has started seeing the relevance and advantages of composite parts.
While initially, composite materials like Carbon Fiber Reinforced Polymers (CFRP) were mostly confined to scientific works and prototypes of machine tool structural elements, there's now a growing trend of their industrial implementation.
Modern machine tools and components are increasingly being designed with composite materials, showcasing their potential to enhance machine performance and efficiency.
2. Why Composites?
Lightweight Construction: The Weight-Saving Advantage
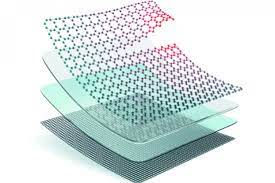
Composite materials, especially carbon fiber reinforced polymers (CFRP), offer significant weight reduction. This has been a primary motivation for their use, especially in industries like aerospace and automotive where fuel savings are crucial.
The lightweight nature of composites has made them increasingly relevant in machine construction, leading to more efficient and agile machine tools.
Enhanced Stiffness: Improving Machine Performance

The specific mass-related stiffness characteristics of composites provide a distinct advantage. This means that despite being lightweight, composites can offer high stiffness, ensuring robust machine performance.
Hybrid designs, where different materials are combined, often incorporate composites to achieve the best balance between mass reduction, static stiffness, and natural frequencies.
Damping Properties: Ensuring Smoother Operations
Composites, especially when used in hybrid structures, have shown to improve dynamic stiffness and damping, especially in higher frequency ranges.
Such advantageous damping properties ensure smoother operations of machine tools, reducing vibrations and enhancing precision.
Thermal Behavior: Maintaining Consistent Performance in Varying Temperatures
The thermal behavior of composite structures is another significant advantage. Composites can maintain their performance characteristics across a range of temperatures, ensuring consistent machine tool operations even under varying thermal conditions.
3. Applications in Machine Tools
Overview of Machine Elements Made from Composites:
Composite materials, particularly carbon fiber-reinforced polymers (CFRP), are now found in various machine tool components.
These components range from structural elements of the machine, tool structures, spindles, and even fixtures.
The unique properties of composites, such as low specific weight, high mass-related specific stiffness, and high material damping, make them ideal for these applications.
The Shift from Traditional Materials to Composites:
Historically, machine tools predominantly used traditional materials. However, the advantages of composites have led to a paradigm shift.
The thermal behavior, low thermal expansion, and the ability for functional integration have made composites a preferred choice for modern machine tools.
This shift is evident in the increasing number of industrial implementations of composite materials in machine tools.
Real-World Examples and Case Studies:
High-Speed Lightweight Machine Tool:
Developed by the company EEW Protec, this machine tool showcases the benefits of using composite materials in its construction.

Composite Tool Bars:
Hwang et al. proposed a design where a metal core or sleeve is inserted into the composite body of a toolbar. This design showcases the integration of traditional materials with composites to achieve optimal performance

Composite Reamer Tool:
A modular construction of a composite reamer tool was presented, highlighting the adaptability and flexibility of composite materials in tool design

Hybrid Material Circular Plate Tool Body:
This tool body is made of a combination of steel and composite materials, showcasing the hybrid approach to tool design
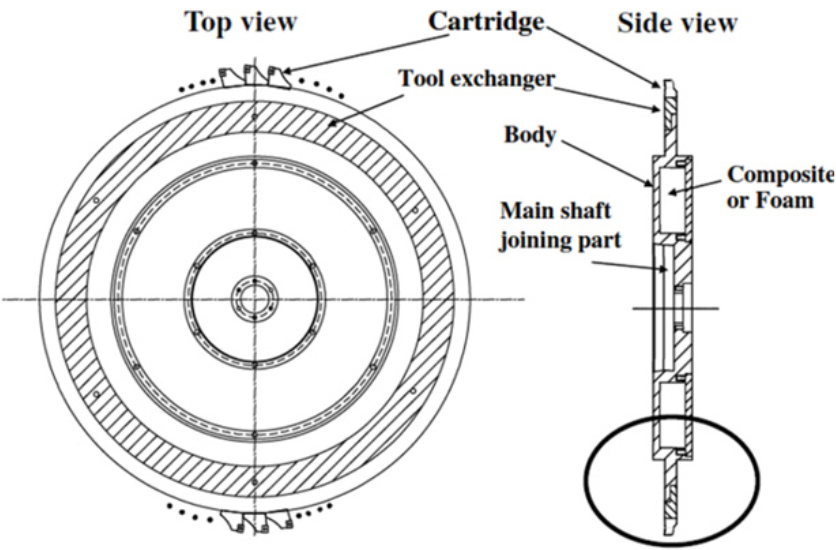
Composite Rotor for Machine Tool Spindles:
Lee et al. introduced the idea of a composite rotor for machine tool spindles. The composite rotor showcased a 20% increase in the maximum width of the cut compared to a steel spindle bearing system.

Composite Shaft of a High-Speed Air Spindle:
Bang and Lee introduced a composite shaft for a high-speed air spindle. The design considered the bending stiffness of the carbon composite shaft and the static stiffness of the air bearing.
Composite Rotor with Steel Core:
A design where a steel core was inserted into a composite rotor to improve magnetic flux was presented. This design showcases the integration of traditional materials with composites for optimal performance.
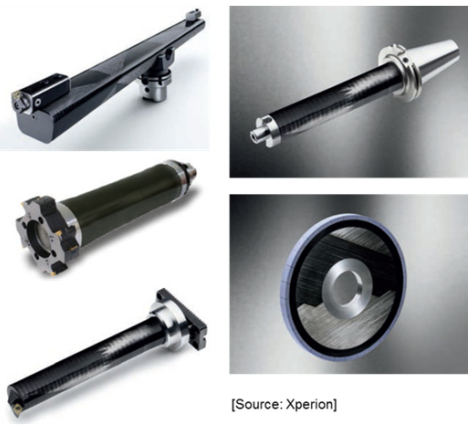
Reinforcement of Spindle Cover with Carbon Fiber Epoxy Composite:
The spindle cover was reinforced with carbon fiber epoxy composite material, showcasing the strength and durability benefits of composites.

Use of Composites in Clamping Systems:
The research paper discussed the potential of using composite materials in fixtures and clamping systems. The low thermal expansion, dynamic stiffness, and structural damping properties of composites make them ideal for these applications. An example includes test fixtures with a CFRP frame component
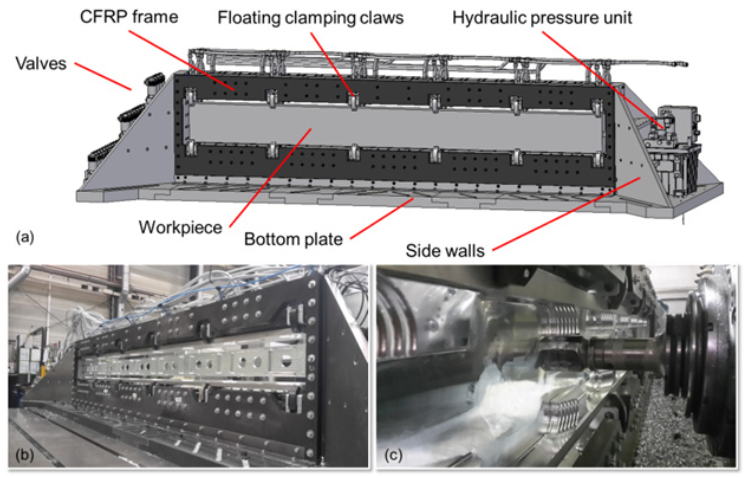
4. Designing with Composites
The Potential of Material Combinations:
Composite materials offer new degrees of freedom in machine component design, especially when material combinations are implemented.
The advantageous properties of composites, such as low specific weight, high mass-related specific stiffness, and high material damping, have been utilized in various exemplary implementations, prototypes, and products.
The integration of different materials, like carbon fiber with foam or honeycomb cores, or even with sheet metal elements, can lead to innovative and efficient designs.
Challenges and Considerations in Design:
While composite materials provide numerous advantages, there are challenges to consider. Material costs and the need for automated and reproducible manufacturing processes for precision parts are among the primary concerns.
It's essential to ensure the reliability of the structural performance, especially in overload or collision situations.
Influences of chips and coolant lubricant need careful consideration in component design to maintain the integrity and performance of the composite parts.
The Role of Automation in Manufacturing Composite Parts:
The last two decades have seen a significant increase in the level of automation in the manufacturing of composite parts. This is still improving, thanks to ongoing development work in industry and research institutions.
Automated processes are crucial for ensuring precision, especially for parts used in machinery. The requirement for automated and reproducible manufacturing processes is especially vital for precision parts in the machinery sector.
To fully implement composite technology in the machine tool industry, strategies for medium batch scenarios up to mass production are necessary.
5. Conclusion
The Future of Composites in Machine Tools:
Composite materials, especially like carbon fiber reinforced polymers (CFRP) and similar composites with glass, aramid, or basalt fibers, have been predominantly used in scientific works and prototypes of machine tool structural elements, tool components, and spindles.
The last two decades have shown a rising number of industrial implementations of composite materials in machine tools, indicating a promising future for composites in this sector.
The unique properties of composites, such as low specific weight, high mass-related specific stiffness, and advantageous damping properties, provide outstanding opportunities for improving machine performance and accuracy.
Encouraging Further Research and Adoption:
New degrees of freedom in machine component design can be exploited, especially when material combinations are implemented.
The research and development in the field of composites for machine tools are still ongoing, and there's a need to encourage further research to unlock the full potential of these materials.
The presented prototypes and industrial products in the research paper showcase the vast potential of composites, emphasizing the need for more industries to adopt and integrate these materials into their machinery.
What's Next!
Discover the future of composite manufacturing with Addcomposites! Here's how you can get involved:
Stay Informed: Subscribe to our newsletter to receive the latest updates, news, and developments in AFP systems and services. Knowledge is power, and by staying informed, you'll always have the upper hand. Subscribe Now
Experience Our Technology: Try our cutting-edge simulation software for a firsthand experience of the versatility and capability of our AFP systems. You'll see how our technology can transform your production line. Try Simulation
Join the Collaboration: Engage with us and other technical centers across various industries. By joining this collaborative platform, you'll get to share ideas, innovate, and influence the future of AFP. Join Collaboration
Get Hands-On: Avail our educational rentals for university projects or semester-long programs. Experience how our AFP systems bring about a revolution in composite manufacturing and leverage this opportunity for academic and research pursuits. Request for Educational Rental
Take the Next Step: Request a quotation for our AFP systems. Whether you're interested in the AFP-XS, AFP-X, or SCF3D, we are committed to offering cost-effective solutions tailored to your needs. Take the plunge and prepare your production line for the next generation of composite manufacturing. Request Quotation
At Addcomposites, we are dedicated to revolutionizing composite manufacturing. Our AFP systems and comprehensive support services are waiting for you to harness. So, don't wait – get started on your journey to the future of manufacturing today!
Comentários