Understanding Defects and Damage in Composite Materials and Structures
- Pravin Luthada
- Aug 8, 2023
- 8 min read
Updated: Aug 9, 2023
While Composites are hailed for their strength and versatility, did you know that even a tiny defect can compromise an entire structure? From invisible matrix cracks to the subtle aging of prepreg, these materials have their own set of vulnerabilities. But here's the twist: with the right knowledge and techniques, these issues can not only be detected but also repaired, restoring the composite to its original strength. Dive into our latest article to uncover the hidden world of composite materials and the unexpected challenges and solutions that come with them
1. Introduction to Composite Materials and Structures
1.1 Evolution of Composites:
Composite materials have evolved due to the need to reduce structural weight and enhance performance.
Attributes such as corrosion resistance, excellent surface profiles, enhanced fatigue resilience, and tailored performance have contributed to the rapid rise in composite materials application.
1.2 Performance Expectations:
New materials are expected to perform at higher stress levels while providing adequate levels of damage tolerance.
Advanced composite materials offer the necessary damage tolerance through relatively low, applied design strains.
1.3 Challenges with Composites:
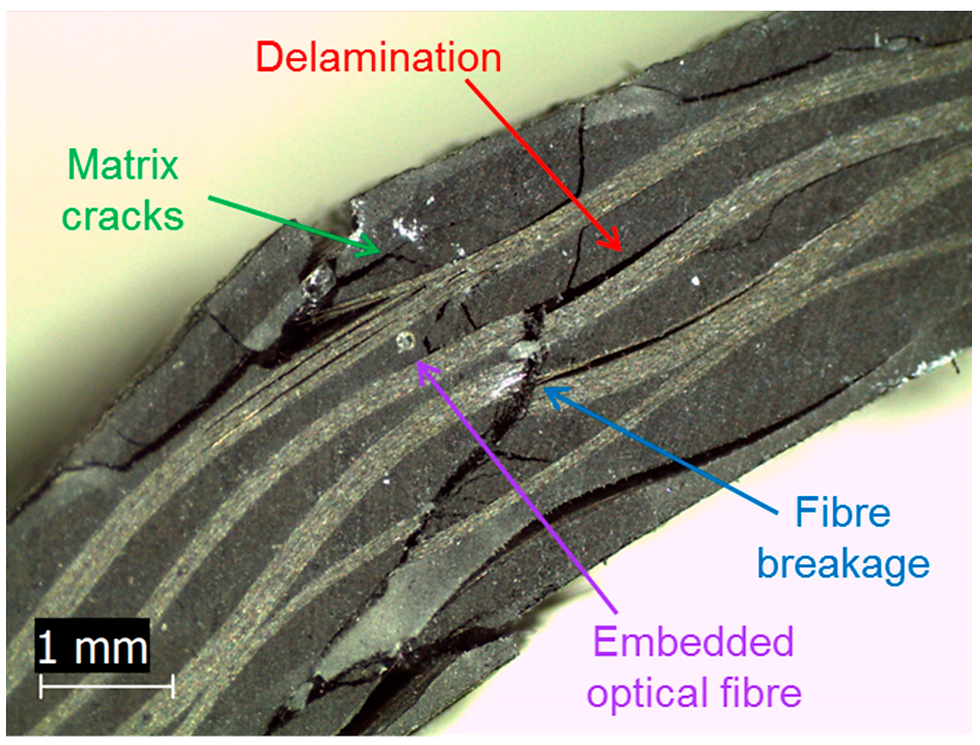
Despite their advantages, defects and damage can still occur in composite materials.
Assessing defect and damage criticality and determining subsequent repair requirements are challenges faced by operators of composite materials.
1.4 Identification and Repair:
When composite materials components are damaged or defective, it's crucial to determine the anomaly's size, shape, depth, type, and extent.
A typical repair procedure involves locating the damaged area, assessing the damage extent, designing a repair scheme, and conducting post-repair quality checks.
1.5 Applications in Aircraft:
Applications and Limitations of Composite Materials in Aerospace Engineering: A Comprehensive Guide : Composite materials are a vital part of aerospace engineering due to their lightweight, strong, and durable properties. Glass fiber, Kevlar, and carbon fiber are commonly used in the aerospace industry, along with matrix materials such as phenolic, polyester, and epoxy. Composite materials have been used in suborbital aerospace vehicles due to their lightweight and durability. However, these materials have limitations, and engineers must choose the right material for each application to ensure success.
2. Defects in Composite Materials

Nonuniform Agglomeration of Hardener Agents: This defect refers to the uneven distribution or clustering of hardening agents within the composite material. This can lead to areas that are either over-cured or under-cured. The failure mode can be a localized decrease in the mechanical properties of the composite, leading to premature failure under load. Corrective measures include ensuring proper mixing of the resin and hardener and using controlled curing processes.
Over-aged Prepreg: Over-aged prepreg refers to prepreg material that has been stored beyond its shelf life or has been exposed to adverse conditions, causing it to partially cure or degrade before final curing. This can lead to reduced adhesion between the fibers and the matrix, resulting in delaminations or reduced mechanical properties. Corrective measures include using fresh prepreg material and adhering to storage guidelines.
Over/Under Cured Materials: Over-curing can cause brittleness, while under-curing can result in reduced mechanical properties. Both defects can lead to premature failure under load. Corrective measures include optimizing the curing process and regularly calibrating curing equipment.
Pills and Fuzz Balls: These are small balls of fibers or resin that can form on the surface or within the composite material. They can act as stress concentrators and lead to reduced fatigue life or delaminations. Corrective measures include improving the layup process and ensuring a clean working environment.
Ply Underlap/Gap: This defect occurs when there is a gap or overlap between adjacent plies in a laminate. This can lead to stress concentrations and reduced load-bearing capacity. Corrective measures include ensuring accurate ply placement during the layup process.
Prepreg Variability: Variability in prepreg material can lead to inconsistencies in the final composite properties. This can result in areas of reduced strength or stiffness. Corrective measures include sourcing consistent quality prepreg material and regular quality checks.
Surface Oxidation: Oxidation of the composite surface can degrade its mechanical properties and reduce its lifespan. Corrective measures include protective coatings and storing composites in controlled environments.
Thermal Stresses: These are stresses induced in the composite material due to temperature changes. They can lead to warping, delaminations, or cracks. Corrective measures include designing composites to withstand expected temperature ranges and using thermal protection where necessary.
Variation in Density, Resin Fraction, and Thickness: Inconsistencies in these parameters can lead to areas of reduced strength or stiffness in the composite material. Corrective measures include optimizing the manufacturing process and regular quality checks.
Warping and Use of Wrong Materials: Warping can occur due to thermal stresses or incorrect curing processes. Using the wrong materials can lead to reduced performance or incompatibility issues. Corrective measures include proper material selection and controlled curing processes.
Each of these defects can significantly impact the performance and reliability of composite materials. Understanding their causes, effects, and corrective measures is crucial for anyone working with or studying composites.
3. Loss of Integrity in Composite Structures
3.1 Understanding the Impact of Defects on Structural Integrity:
Defects in composite materials can have a profound impact on the structural integrity of the component or structure. The severity of a defect is determined by the stress state it imposes on the local composite structure.
The location and orientation of a defect play a crucial role in determining its impact. Specific locations can either amplify or mitigate the stress severity caused by a defect. Similarly, the physical orientation of a defect can make it either severe or benign.
The frequency of a defect's occurrence can also influence its severity. Multiple occurrences of the same defect can compound the stress on the structure.
The component's load path criticality and stress state interact with the defect's location and orientation. Depending on these factors, the defect's criticality can either increase or decrease.
The ability to detect and classify a defect is vital. The capabilities of the detection equipment and the skill level of the operator play a significant role in this. Proper detection and classification are crucial for identifying defect criticality.
3.2 Evaluating the Severity of Damages:
The level of structural degradation in engineering material properties varies based on several factors, including defect severity, location, orientation, frequency of occurrence, component load path criticality, and stress state.
The idealization of the defect type, whether it's intralaminar matrix cracks, interlaminar matrix cracks, or fiber fraction, can influence the stress analysis and determination of defect criticality.
The design load levels and the nature of the load (static or dynamic) also play a role in determining the severity of the stress state in the presence of a defect.
The ability to detect the defect and classify its type depends on the capabilities of the detection equipment and the skill level of the operator. Proper detection is crucial for identifying the severity of the damage.
Understanding the loss of integrity in composite structures is essential for ensuring their safety and longevity. Proper detection, classification, and repair of defects can mitigate potential risks and extend the life of the structure.
4. Restitution and Repair of Damaged Composites
4.1 Fundamentals of Developing a Repair Scheme:
Once damage or a defect has been identified and evaluated against appropriate criteria to determine the loss of structural or performance integrity, a repair scheme is developed. The development of a repair scheme needs to consider several practical implementation issues and review the specific repair requirements for successful design and installation.
4.2 Practical Implementation Issues in Repair:
The restitution of a defect or damage requires a good appreciation of the severity to determine the best repair scheme for the composite structure. Several factors impact the repair scheme selection and can drive the best structurally efficient repair design to a more complex repair design. For instance, using a flush repair because of aerodynamics when a doubler repair would be ideal for strength restoration.
4.3 Specific Repair Requirements for Successful Design and Installation:
The development of generic repair types in composite structures describes repairs for generalized defect/damage types, such as intralaminar matrix cracks, delaminations, and broken fibers. The repair design and installation requirements are crucial for ensuring the longevity and performance of the repaired composite structure.
4.4 Generic Repair Types in Composite Structures:
There are four basic levels of generic repair designs: filling and sealing the damaged area (cosmetic), filling and applying a doubler patch to the damaged area (semi-structural), bonding a flush patch to the damaged area (structural), and bolting a patch to the damaged area (structural).
4.5 Repairs for Generalized Defect/Damage Types:
The defect/damage restoration can range from a simple low-viscosity resin infusion to a complex bolted repair scheme. The restoration of defects or damages is an essential requirement in the initial design of the structure. If the structure cannot be made damage-tolerant, then it needs to be inspectable. If defects/damages are found, then it needs to be designed for repair.
4.6 Damage Removal and Repair Scheme Installation Process:
The concluding section provides an overview of the damage removal and repair scheme installation process. This includes a detailed discussion of surface preparation requirements and processes.
5. Conclusion
Composite materials, with their unique properties and advantages, have found extensive applications in various industries. However, like all materials, they are susceptible to defects and damages that can compromise their structural integrity. This article delved deep into:
Composite Material Basics: Highlighting the fundamental aspects of composite materials, their types, and their applications. The inherent advantages of composites, such as high strength-to-weight ratio and corrosion resistance, make them a preferred choice in many industries.
Defects in Composite Materials: A comprehensive overview of the various defects that can arise in composites, from damaged filaments to matrix cracking. Understanding these defects, their causes, and their impact on structural integrity is crucial for anyone working with or studying composites.
Loss of Integrity in Composite Structures: This section emphasized the importance of understanding the impact of defects on the structural integrity of composites. It also highlighted the need for evaluating the severity of damages to ensure the safety and longevity of composite structures.
Restitution and Repair of Damaged Composites: Addressing the challenges and methodologies associated with repairing damaged composites. From the fundamentals of developing a repair scheme to the practical implementation issues, this section provided a roadmap for effectively restoring the integrity of damaged composites.
In essence, while composite materials offer unparalleled benefits, it's imperative to understand, detect, and address their potential defects and damages. Proper detection, classification, and repair of these issues not only ensure the safety of structures but also extend their operational life. Whether you're a professional in the field or a student, a deep understanding of these aspects is crucial for the effective use and maintenance of composite materials.
What's Next!
Discover the future of composite manufacturing with Addcomposites! Here's how you can get involved:
Stay Informed: Subscribe to our newsletter to receive the latest updates, news, and developments in AFP systems and services. Knowledge is power, and by staying informed, you'll always have the upper hand. Subscribe Now
Experience Our Technology: Try our cutting-edge simulation software for a firsthand experience of the versatility and capability of our AFP systems. You'll see how our technology can transform your production line. Try Simulation
Join the Collaboration: Engage with us and other technical centers across various industries. By joining this collaborative platform, you'll get to share ideas, innovate, and influence the future of AFP. Join Collaboration
Get Hands-On: Avail our educational rentals for university projects or semester-long programs. Experience how our AFP systems bring about a revolution in composite manufacturing and leverage this opportunity for academic and research pursuits. Request for Educational Rental
Take the Next Step: Request a quotation for our AFP systems. Whether you're interested in the AFP-XS, AFP-X, or SCF3D, we are committed to offering cost-effective solutions tailored to your needs. Take the plunge and prepare your production line for the next generation of composite manufacturing. Request Quotation
At Addcomposites, we are dedicated to revolutionizing composite manufacturing. Our AFP systems and comprehensive support services are waiting for you to harness. So, don't wait – get started on your journey to the future of manufacturing today!
Comments