Unveiling the Future of Robotics with TeslaBot and Composite Materials
- Pravin Luthada
- Dec 15, 2023
- 10 min read

Welcome to our exploration of the cutting-edge advancements in robotics, specifically focusing on Tesla's innovative TeslaBot and the game-changing role of composite materials. This blog offers a deep dive into the transformative impact of composites on robotic technology, bringing to light how these materials are revolutionizing the design and capabilities of robots. Here's a quick teaser of what you'll learn:
TeslaBot's Current State: Discover the design, materials, and technological advancements that define Tesla's TeslaBot.
The Power of Composites: Understand the role of continuous fiber 3D printing and Automated Fiber Placement (AFP) in enhancing robotic structures.
Revolutionizing Robotics with Composites: See how composites could dramatically improve the TeslaBot's body panels, actuator shafts, and legs, and embed multifunctionality like sensing and structural health monitoring.
Mimicking Human Strength: Learn how composites are being used to replicate the directional strength of the human body, enhancing the robot’s performance and efficiency.
Overcoming Manufacturing Challenges: Gain insight into the challenges faced in manufacturing with composites and the innovative solutions that AFP and continuous fiber 3D printing offer.
Future Outlook: Speculate on the future of robotics with the integration of advanced materials and the potential for further research and development in this exciting field.
Join us as we embark on this journey through the realm of advanced robotics and material science, where innovation meets practical application, paving the way for a new era in robotic capabilities. Whether you're a tech enthusiast, an engineer, or simply curious about the future of robotics, this blog has something for you. Let's dive in!
Current State of TeslaBot
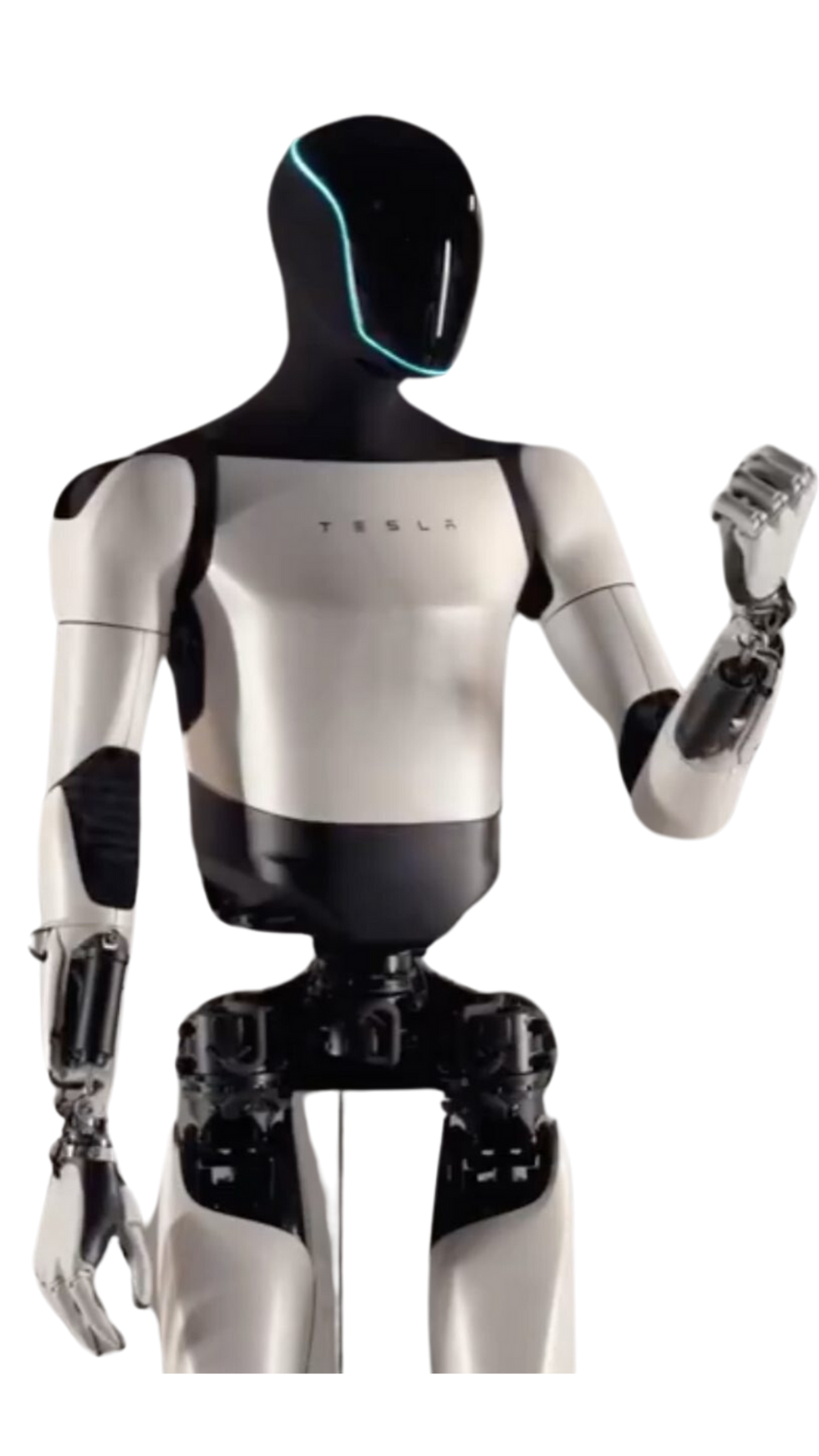
In this section, we explore the existing design and materials used in the TeslaBot, along with the recent technological advancements highlighted in the latest video release.
Design and Humanoid Features:
Humanoid Structure: TeslaBot, also known as Optimus, is designed as a humanoid robot, meaning its shape and size closely resemble those of a human. This design facilitates a broader range of tasks and interactions in human-centric environments.
Degrees of Freedom: With 40 degrees of freedom, TeslaBot can perform complex tasks with high precision, akin to human dexterity.
Communication: It communicates through speech, text, and gestures, enhancing its ability to interact with humans.
Materials and Build:
Lightweight Materials: The construction of TeslaBot predominantly uses plastic, chosen for its weight-saving advantages. Metal is used selectively where necessary.
Sleek Shell Design: It features a sleek shell, emphasizing aesthetic appeal and functional design.
Advanced Technology Integration:
Tesla's AI and Autopilot Cameras: The robot uses Tesla's self-driving AI for navigation and includes eight autopilot cameras in its head for environmental sensing.
Interactive Display: An interactive screen on the face serves as a medium for communication and information display.
Battery and Power Efficiency:
Battery Pack: The initial prototype, Bumble C, is outfitted with a 2.3-kilowatt-hour battery pack, sufficient for a full day's work.
Energy Consumption: The robot consumes 100 watts of power while stationary and 500 watts while walking.
Recent Developments and Capabilities:
Environmental Adaptation: A recent video showcased TeslaBot's ability to adapt to new environments and interact with objects using advanced sensors.
Precision Task Performance: The bot can perform tasks like sorting blocks with human-like speed and precision.
Balance and Control: Demonstrations included the robot's ability to stand on one leg and perform balanced movements, indicative of advanced body control.
Safety and Security Features:
Remote Updating: A localized chip allows for remote updates, enhancing safety and adaptability.
Navigation and Obstacle Avoidance: Ultrasonic sensors and cameras aid in navigation and avoiding obstacles.
Technical Specifications:
Carrying Capacity: TeslaBot can carry up to 200 pounds, with hands capable of 11 degrees of freedom for precise object manipulation.
Speed: It is designed to walk at speeds up to 5 mph.
Potential Applications:
Versatility: TeslaBot's design and capabilities make it suitable for a variety of tasks, including manufacturing, logistics, healthcare, and customer service.
The Potential of Composites

In this section, we delve into the potential of composites in robotics, focusing on continuous fiber 3D printing and Automated Fiber Placement (AFP) solutions, and explore how these advanced materials could revolutionize the design and capabilities of robots like TeslaBot.
Introduction to Composites:
Definition: Composite materials are combinations of two or more materials that retain their individual properties while offering improved overall performance. They typically consist of a reinforcement (like continuous fibers) and a matrix.
Key Advantages: The main benefits of composites include high strength and stiffness coupled with low density. This results in significantly lighter components compared to bulk materials like metals, providing weight reduction without compromising on strength.
Continuous Fiber Composites in Robotics:
Automated Fiber Placement (AFP): AFP involves placing a band of continuous fiber tape on a mold surface, which is then heated and pressed. This process offers high strength-to-weight ratios, precise fiber placement, and the ability to steer fibers for optimal performance.
3D Printing with Continuous Fibers: In this method, continuous fiber strands are coated with a curing agent and laid into a thermoplastic matrix extruded via a print nozzle. Technologies like Structural Continuous Fiber 3D Printing (SCF3D) enable combining a thermoset impregnated fiber and a plastic matrix at the moment of printing, offering great customization in terms of fiber volume ratio and part complexity.
Advantages of Composites in Robotics:
Weight Reduction: Lighter materials like composites can reduce the overall weight of robots, leading to higher efficiency and longer battery life.
Customization and Flexibility: Technologies like SCF3D allow for significant customization in part design, with options to vary the fiber volume and choose different types of fibers and matrix materials. This flexibility can be crucial for creating parts that need to fit specific functional or aesthetic requirements.
Strength and Durability: Composites provide enhanced strength and durability, making them suitable for components that require high mechanical performance.
Applications in Various Industries: The versatility of composites, especially when combined with technologies like AFP and SCF3D, opens up possibilities for their use in diverse sectors, from aerospace to healthcare.
Innovations in Composite Manufacturing:
Integration with Robotic Programming: The combination of composites with robotic programming offers an elegant solution for manufacturing complex parts.
Continuous Improvement: The field of composite manufacturing, particularly in relation to robotics, is continuously evolving, with innovations in raw materials, processing, manufacturing tools, and design.
Benefits of Using Composites in TeslaBot
The incorporation of composites in the TeslaBot could lead to significant improvements in its design and functionality. Here's how composites could enhance various aspects of the TeslaBot:
Improvements in Body Panels, Actuator Shafts, and Legs:
Lighter and Stronger Body Panels: Composites can significantly reduce the weight of the TeslaBot's body panels while maintaining or even increasing their strength. This reduction in weight can improve the robot's agility and energy efficiency.
Enhanced Actuator Shafts: Using composites for actuator shafts can lead to more efficient power transmission. Their high strength-to-weight ratio ensures that these components are both lightweight and capable of handling the stresses of operation.
Optimized Leg Design: Composite materials can offer greater flexibility and strength in the legs of the TeslaBot. This could lead to improved stability, mobility, and adaptability to various terrains or activities.
Multifunctionality of Composites:
Embedded Sensing: Composites allow for the integration of sensors directly into the material. This could enable the TeslaBot to have enhanced capabilities in terms of environmental awareness, structural health monitoring, and responsive adaptation to changes in its surroundings.
Structural Health Monitoring: The integration of sensors within composite materials can provide real-time data on the condition of the robot's structure. This is crucial for preventive maintenance and ensuring the longevity of the robot.
Potential for Increased Battery Life:
Reduced Weight Leads to Energy Efficiency: The lighter weight of composite materials can significantly reduce the energy required for movement and operation, directly translating to longer battery life.
Potential for Energy Harvesting: Some composites can be designed to harvest energy from the environment (such as through piezoelectric materials), potentially providing an additional source of power for the TeslaBot.
Technical Considerations:
Customization in Composite Fabrication: Advanced manufacturing techniques like AFP and SCF3D allow for tailored designs of composite parts, enabling specific performance characteristics to be targeted.
Optimization of Mechanical Properties: By strategically aligning the fibers in composites, engineers can optimize the mechanical properties of various parts of the TeslaBot, such as its joints and frame, for specific tasks or environments.
Human-Like Structural Strength
In this section, we'll explore how the use of composites in robotics, specifically in the TeslaBot, can mimic the directional strength of the human body and the implications this has for the robot's performance and efficiency.
Mimicking Human Body's Directional Strength:
Anisotropic Properties of Composites: Composites, particularly those using continuous fibers, have anisotropic properties, meaning their strength and stiffness can vary depending on the direction of the fiber. This is similar to human muscles and tendons, which exhibit different strengths in different directions.
Customizable Fiber Orientation: By aligning the fibers in specific directions, composites can be engineered to mimic the directional strength and flexibility of human muscles and joints. This allows for more human-like movement and load-bearing capabilities.
Implications for Performance and Efficiency:
Enhanced Movement and Agility: With composite materials designed to mimic human muscular structure, the TeslaBot could achieve more natural and agile movements. This would be particularly advantageous in tasks that require a high degree of precision or adaptability.
Increased Load-Bearing Capacity: The directional strength of composites can be optimized for load-bearing tasks, enhancing the robot's ability to carry or manipulate heavy objects without compromising its structural integrity.
Energy Efficiency: Efficient movement, aided by the strength and lightweight nature of composites, could lead to reduced energy consumption during operation, thereby increasing the robot's overall efficiency and battery life.
Durability and Longevity: Composites are known for their durability, which means the TeslaBot could have a longer operational life with less need for repairs and maintenance.
Technical Aspects and Optimization:
Strategic Design and Fabrication: Engineers can use computational models and simulations to strategically design the composite structure of the robot. This includes optimizing fiber orientation for specific tasks or movements.
Leveraging Modern Manufacturing Techniques: Techniques like AFP and 3D printing allow for precise control over the composite structure, enabling the creation of components that closely mimic the human body's strength and flexibility.
Manufacturing Challenges and Solutions
Incorporating composites into robotics, such as the TeslaBot, presents certain manufacturing challenges. However, advancements in Automated Fiber Placement (AFP) and continuous fiber 3D printing are providing solutions to these challenges.
Challenges in Composite Manufacturing:
Cost and Complexity: Historically, manufacturing with composites has been costly and complex. The materials themselves can be 5-50 times more expensive per kilogram than their metal counterparts, and the manufacturing process is intricate and labor-intensive.
Risk of Errors: Even slight errors in the manufacturing process can lead to compromised structural strength, material wastage, and decreased yield.
Safety Concerns: Working with fibers can be physically harmful, and chemically toxic resins used in the process pose health risks.
Equipment Cost: Traditional AFP systems, developed primarily with defense contracts and government financing, have been exorbitantly expensive, ranging from 1-5 million dollars, making automation inaccessible for many manufacturers.
Solutions Through Advanced AFP and 3D Printing:
AFP-XS: A Cost-Effective Approach: The AFP-XS system is designed to integrate seamlessly with existing industrial robotic arms or CNC systems, significantly lowering the entry barriers to AFP technology. It addresses safety concerns by offering multi-material capabilities and safer material processing options.
AFP Flexibility: AFP is highly flexible, allowing for the creation of complex shapes and angles. It's particularly suitable for industries that require large production volumes, such as aerospace and aviation.
Advanced Equipment and Software: Modern AFP equipment consists of a head with a compaction roller and a tape feeding system, a multi-axial kinematic system, and sophisticated software for precise control.
Reduced Costs and Increased Accessibility: Innovations like the AFP-XS are making composite manufacturing more accessible and cost-effective, even for smaller enterprises.

Combining AFP and Continuous Fiber 3D Printing:
Synergy in Manufacturing: The combination of AFP with continuous fiber 3D printing is leading to innovations at multiple levels - raw material, processing, manufacturing tools, software, inspection, and design.
Addressing the Limitations: New technologies are being developed to address the limitations of traditional AFP, such as the lack of flexibility in fiber path trajectories and the need for mechanical post-processing.
The Future Outlook:
Potential for Wider Adoption: With the costs coming down and the technology becoming more user-friendly, there is potential for a broader adoption of composite manufacturing in robotics.
Innovations Driving Change: Continuous innovations in AFP and 3D printing are expected to further bridge the gap between high precision composite manufacturing and industrial volume production needs.
Conclusion
As we reach the conclusion of our exploration into the integration of composites in Tesla's TeslaBot, let's summarize the key benefits and look towards the future of robotics with these advanced materials.
Summarizing the Benefits:
Enhanced Performance: Composites offer superior strength-to-weight ratios, drastically improving the robot's agility, efficiency, and battery life.
Customization and Flexibility: Advanced manufacturing techniques like AFP and continuous fiber 3D printing allow for high levels of customization, enabling the creation of parts with specific functional and aesthetic requirements.
Durability: Composites are known for their durability, which translates into longer operational life for robots, reducing the need for frequent repairs and maintenance.
Multifunctionality: The ability to integrate sensors directly into composite materials enhances the robot’s capabilities in environmental awareness and structural health monitoring.
Speculating on the Future of Robotics:
Broader Applications: With the ongoing advancements in composite materials, we can anticipate broader applications of robotics in various fields, including aerospace, healthcare, and consumer industries.
Increased Autonomy and Adaptability: Future robots may exhibit increased autonomy and adaptability, thanks to the improved performance and sensing capabilities afforded by composites.
More Human-Like Robots: The ability of composites to mimic human-like strength and flexibility could lead to more sophisticated humanoid robots, capable of performing complex tasks with a higher degree of precision.
Encouraging Further Research and Development:
Continued Innovation: The field of composite materials in robotics is ripe for innovation, with opportunities for breakthroughs in material science, manufacturing processes, and robotic design.
Collaboration Across Disciplines: There is a need for collaboration across various disciplines, including materials science, robotics, engineering, and AI, to fully realize the potential of composites in robotics.
Investment in Research: Encouraging investment in research and development can accelerate the integration of these advanced materials into next-generation robotic systems.
References
For those interested in exploring the topic of composites in robotics, particularly in relation to Tesla's TeslaBot, here is a list of references and further reading materials:
Science Online, "Tesla robots (Optimus) review, use, advantages and disadvantages," provides an overview of the TeslaBot, its features, and potential applications. Science Online.
Lifeboat.com, "Tesla Unveils Gen 2 Tesla Bot: Impressive Advancements in Design and Capabilities," discusses the recent advancements and design features of the second generation TeslaBot. Lifeboat.com.
Millivolt.news, "Tesla Demonstrated New Abilities of Humanoid Robot TeslaBot," offers insights into the latest capabilities and technological developments of the TeslaBot. Millivolt.news.
Addcomposites.com, "Continuous Fiber Composites + Robotic Programming = An Elegant Composite Solution," delves into the integration of continuous fiber composites and robotic programming, highlighting the potential for manufacturing innovations. Addcomposites.com.
Anisoprint.com, "Composite 3D Printing 101: benefits, technologies and applications," provides a comprehensive overview of continuous carbon fiber 3D printing technologies and their applications in various industries. Anisoprint.com.
Addcomposites.com, "AFP-XS: A Revolutionary Response to Composite Manufacturing Challenges," discusses the challenges of composite manufacturing and the advancements in AFP technology as a solution. Addcomposites.com.
Anisoprint.com, "Advanced Composites Manufacturing: Automated Fiber Placement," explores the process, equipment, and features of AFP technology, along with its applications and cost considerations. Anisoprint.com.
What's Next!
Discover the future of composite manufacturing with Addcomposites! Here's how you can get involved:
Stay Informed: Subscribe to our newsletter to receive the latest updates, news, and developments in AFP systems and services. Knowledge is power, and by staying informed, you'll always have the upper hand. Subscribe Now
Experience Our Technology: Try our cutting-edge simulation software for a firsthand experience of the versatility and capability of our AFP systems. You'll see how our technology can transform your production line. Try Simulation
Join the Collaboration: Engage with us and other technical centers across various industries. By joining this collaborative platform, you'll get to share ideas, innovate, and influence the future of AFP. Join Collaboration
Get Hands-On: Avail our educational rentals for university projects or semester-long programs. Experience how our AFP systems bring about a revolution in composite manufacturing and leverage this opportunity for academic and research pursuits. Request for Educational Rental
Take the Next Step: Request a quotation for our AFP systems. Whether you're interested in the AFP-XS, AFP-X, or SCF3D, we are committed to offering cost-effective solutions tailored to your needs. Take the plunge and prepare your production line for the next generation of composite manufacturing. Request Quotation
At Addcomposites, we are dedicated to revolutionizing composite manufacturing. Our AFP systems and comprehensive support services are waiting for you to harness. So, don't wait – get started on your journey to the future of manufacturing today!
Comments