What are the Applications of Composite Materials Today?
- Pravin Luthada
- Jul 30, 2021
- 7 min read
Updated: Jan 20, 2023
Composites are used in a wide variety of markets, including aerospace, architecture, automotive, energy, infrastructure, marine, military, and sports and recreation. Read about interesting applications of composites in select industries below and check back often as we continue to add new applications to this site.
Aerospace
Major Original Equipment Manufacturers (OEMs) such as Airbus and Boeing have shown the potential for large-scale composite applications in aviation, and NASA is continually looking to composites manufacturers for innovative space solutions for rockets and other spacecraft.

Figure 1. The use of composites in the Boeing 787 Dreamliner (Source: ResearchGate)
Each generation of new aircraft developed by Boeing has had an increased percentage of composite material, with the highest being 50% in Boeing 787 Dreamliner. The major structural elements of Boeing's 787 Dreamliner are made of more carbon 'sandwich' composites and advanced carbon laminate, a shift away from archaic fiberglass composites.
Aramid fibers, on the other hand, are widely used for constructing leading and trailing edge wing components and very stiff, very light bulkheads, fuel tanks, and floors. Advanced composites consisting of a combination of high-strength stiff fibers embedded in a common matrix material are also widely being used in the aerospace industry (Read more here).
Architecture
The architecture community is experiencing substantial growth in the understanding and use of composites. Composites offer architects and designers performance and value in large-scale projects and their use is increasing in commercial and residential buildings.
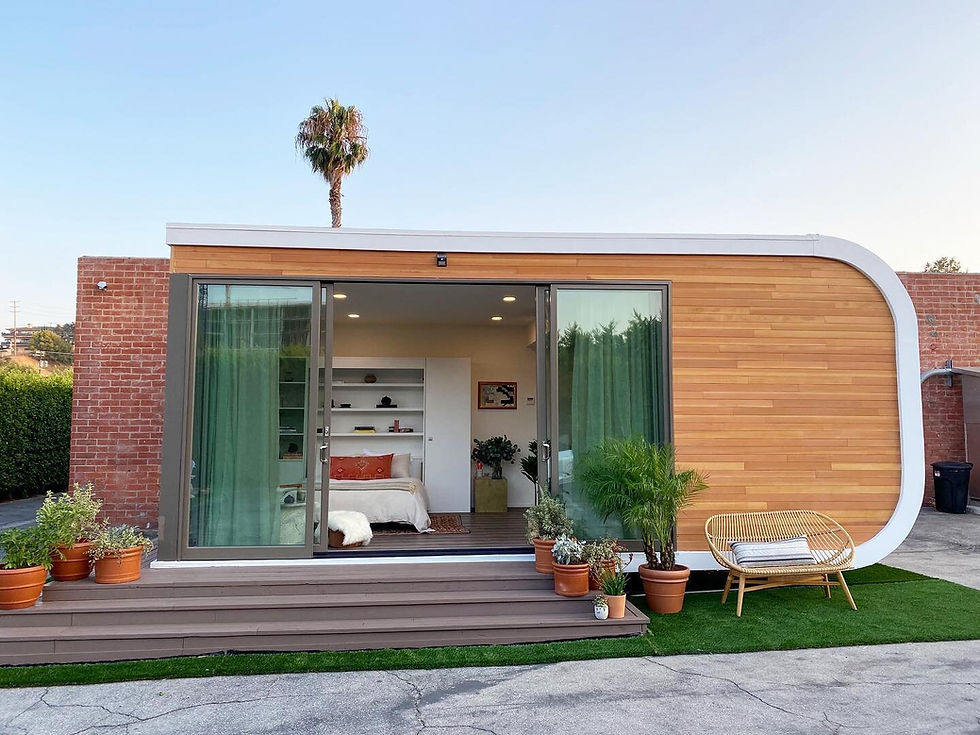
Figure 2. An application of composite materials in architecture. Image Credit: Mighty Buildings
From a recent article, Palari Group builds sustainable 3D-printed communities and homes. Mighty Buildings is a construction technology company creating affordable and sustainable homes using 3D printing, robotics, and automation. The two innovators are partnering to build a community of 3D-printed zero-net energy homes in California.
The essential building block of the homes is the Mighty Panel, a 3D printed, 100% polymer composite panel complete with structure, insulation, MEP integration, air/moisture/fire barrier & interior/exterior finishes. Mighty Buildings prints the individual panels at its facility, and they are assembled into homes at the construction site.
Automotive
As the largest composites market, the automotive industry is no stranger to composites. In addition to enabling groundbreaking vehicle designs, composites help make vehicles lighter and more fuel-efficient. Automotive requires reliable, synchronized mechanisms with parts that can withstand friction, corrosion, and temperature fluctuations. Inaccuracies in design or production will impact performance and can represent a loss of business for the manufacturer.
When compared to steel, the capabilities of composite materials provide the ability to meet and surpass automotive industry demands. These unique features include:
A low coefficient of thermal expansion for heat conduction
Excellent dimensional stability for shape retention and reliability
Resistance to corrosion for performance in wet and dry conditions
High-impact strength to withstand repeated use
Relatively low weight to reduce overall vehicle mass
Sound baffling for quieter performance
Receptiveness to paint, including the ability to meet Class A surface requirements, the paint, and bake process
Ease of manufacturing for a relatively lower cost
Interior and Exterior Applications
Composites are widely used for a range of automotive parts, from headlamp housings for forward-facing headlamps, to beneath-the-hood electrical and heat-shielding components, to exterior body parts and interior structural and cosmetic components. More specifically, composites are used in parts including:
Air deflectors and spoilers
Air-intake manifolds
Battery casings and covers
Bumpers and bumper beams
Cylinder head (e.g. valve, rocker, cam) covers
Frames for windows/sunroofs
Front-end grill opening panels
Headlamp housings for forward-facing headlamps
Heat shields (e.g. engine, transmission)
Pillars and coverings

Figure 3. Both commodity and engineering polymers are playing an increasing role in automotive lightweight solutions. Image Credit: G. M. Oliver, Plastics and composites are reshaping car design, IHS report shows (2014).
Energy Production
the use of composites in renewable energy will play an increasingly vital role through the manufacture of structures that enable the harnessing of sustainable energy sources. Factors such as the reduced weight compared to metallic structures, lower transportation, and erection costs, and most importantly, lower maintenance costs over the lifespan of the structure are already positioning composites as a de facto material enabling economical solutions to large-scale projects.
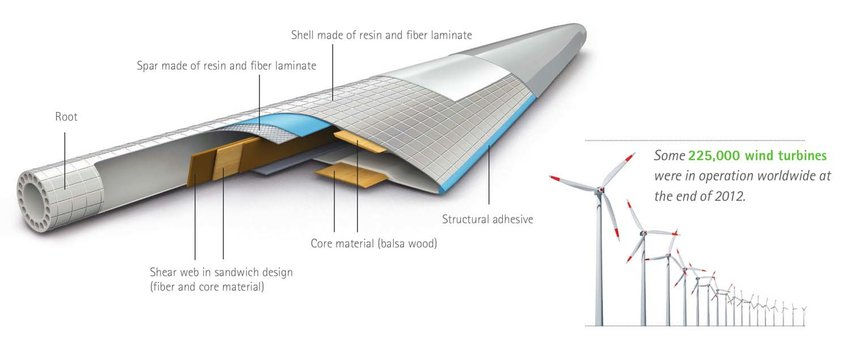
Figure 4. The use of composite materials in wind turbine. Image Credit: Nolet, 2011
The lightweight and complex airfoil shape of blades for wind turbines have made composites a leader in this sector using molds that are engineered to economically manufacture blades with minimal labor. Presently research and development are aimed at satisfying the increased size needed in turbine and rotor blades for land-based and off-shore systems.
Energy storage
Embed battery layers in structures
Multifunctional energy storage composites (MESC) embed battery layers in structures.
Interlocking rivets anchor battery layers which contribute to mechanical performance.
Experimental testing of MESC shows comparable electrochemical behavior to baseline.
At 60% packing efficiency, MESC gains 15× mechanical rigidity compared to pouch cells.

Figure 5. The energy-storing structure of Multifunctional Energy Storage Composites (MESC)
Other applications include:
Hydrogen tanks for aerospace
Hydrogen fuel cells
Battery cell with natural composites
Infrastructure
Construction engineering history may have reached a new stage with the advent and availability of the new, low-cost, high-performance structural composites. Not only the fiber-reinforced plastic (FRP) ‘pultruded’ sections can replace steel in many load-bearing structures, but the strengthening of concrete beams with internally or externally bonded fiber-reinforced plastics (FRP) has also been proved feasible to increase the load-carrying capacity and stiffness of existing structures.
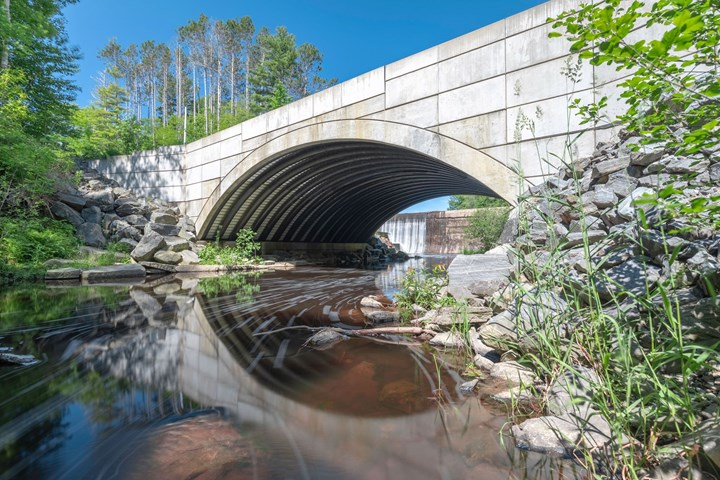
Figure 6. An arch bridge system by AIT Bridges uses a braided fiber-reinforced polymer (FRP) tube filled with concrete (Source: AIT Bridges)
Composites made with glass, aramid, or carbon fibers are being increasingly considered for pre-tensioning, post-tensioning, or reinforcing concrete. To replace the corroding steel rebars, the FRP system may eventually be used in concrete bridge decks or other outdoor concrete flooring structures.
Marine
FRP composites have been used successfully in marine applications for several decades in areas such as radomes and mass structures, superyachts, workboats, and leisure craft. More recently FRPs have been used in less well-known applications such as bearings, propellers, commercial hatch covers, exhausts, and topside structures.
The use of glass-fiber composites (GRP) in marine applications was one of the first significant areas of GRP use. It has revolutionized the capability to design and manufacture large composite structures in several sectors. Vessels are made in the UK by a variety of processes, including hand-lay GRP, resin-infusion, thermoplastics, and high-performance carbon fiber prepreg for racing yachts.
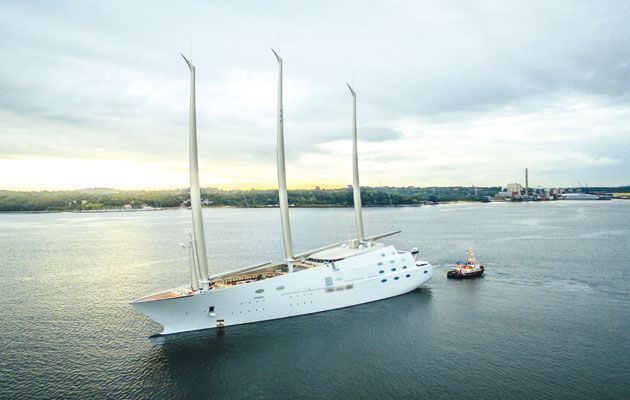
Figure 7. A Yacht built with a majority of composites materials. Image Credit: https://www.yachtingworld.com/
The main advantages of glass-fiber composites (GRP) for marine applications are:
Environmental resistance, including freedom from rotting, corrosion, etc.
Ability to mold seamless, complex-shaped structures
Ability to tailor strength to suit loading conditions
Excellent strength-to-weight characteristics - GRP marine structures are generally half the weight of equivalent steel structures.
Low maintenance and ease of repair
Excellent durability
Racing yachts use composites more extensively than any other marine structure. The materials used are not typical of marine construction because of special requirements. Minimal weight and maximum stiffness are crucially important in their design so that they can sail with maximal speed and resistance to the impact of waves and other elements in marine environments. Carbon fiber reinforced epoxy composites are usually used in boat hulls cored with honeycomb or foam, frames, keels, masts, poles and boom, carbon winch drums, and shafting. The use of FRPs can contribute to improved performance and minimize the danger of sailing drawbacks and failure in the different international sailing conditions.
Pipe & Tank
Composite ductwork has been used in chemical manufacturing plants for more than 25 years. During the 1970s, the use of composites in industrial applications became widespread. Today, composite pipe, duct, and tank installations are on the rise – above and below ground, in commercial, municipal, and residential applications. Low-cost natural gas is further expanding the market with the development of new chemical facilities and the expansion of older ones for chemical processing.

Figure 8. A tank made of composite material. Image credit https://discovercomposites.com/industrial/pipe-and-tank/
Applications and products:
Air Pollution Control
Aquaculture
Chemical Processing
Desalination
Oil & Gas
Water and Wastewater Treatment
Pipes
Pipe fittings and liners
Ductwork
Tank liners
Storage tanks
Process vessels
Scrubbers
Valve
Sports & Recreation
Composites are found in products used in 7 of the 10 most popular outdoor sports and recreational activities. Glass- and carbon-reinforced composites (alone or in hybrids with other fibers) continue to replace wood and metal in fishing rods, tennis racquets, spars/shafts for kayak paddles, windsurfing masts and boards, hockey sticks, kites, and bicycle handlebars, as well as in niche applications, such as fairings for recumbent bikes.

Figure 9. 3D-printed unibody electric bike (Source: Superstrata)
Transportation
There is a trend in the transportation industry for larger vehicles. Whether it’s busses, trains, or articulated trucks, the idea is simple; carry more cargo. The challenge is to find ways to safely carry greater loads while saving fuel and reducing environmental impact. Composites offer impressive answers to this challenge.
With growing sustainable trends in Electric Vehicles (EVs), Arrival has shown how the use of composite materials in their body panel can help reduce the factory footprint while keeping the production rate really high.

Figure 10. The application of composite materials in electric vehicles (EV) in Arrival Ltd. 's Vans and Buses
A Case Study from Addcomposites with Automated Fiber Placement (AFP) System
In collaboration with MBDA (France), the Compositadour team based in Bayonne, France recently demonstrated the process for manufacturing rectangular tubes with the Single-tow Fiber Placement System (AFP-XS). The layup program was generated using the winding feature of our 3D Simulation and Programming Software (AddPath), and as shown in the video below, the Single-tow Fiber Placement System (AFP-XS) performs the layup on the sharp radial corners ensuring wrinkle/pucker-free layup through sharp steering, while monitoring the process.
Rectangular tubes are one of the most basic building blocks for many modular systems in the industry. The following section highlights the key benefits of building rectangular tubes with the Automated Fiber Placement (AFP) process.
Tubes are commonly used as structural elements in buildings, bridges, and other engineering applications, and in a wide variety of end-use consumer products. Rectangular tubing has many benefits: aesthetic appeal, high strength-to-weight ratios, uniform strength, cost-effectiveness, and more.
Learn more about the Case Study "Production of Rectangular Tubes using AFP-XS".
About Addcomposites
Addcomposites is the provider of the Automated Fiber Placement (AFP) system. The AFP system can be rented on a monthly basis to work with thermosets, thermoplastic, dry fiber placement, or in combination with 3d printers.
Sources
Subscribe to the newsletter and get our guidebook - "Composites Basics: An Ultimate Guide for 2022"
Comments