Winding the Future: An Exploration of Filament Winding Applications
- Aman Sahu
- Feb 7, 2023
- 7 min read
Updated: Apr 6, 2023
Introduction
Filament winding is a technique for creating composite structures by winding fiber reinforcement material around a mandrel or form. From its early use in the aerospace industry for rocket motor cases, filament winding has expanded to various industries, such as transportation, marine, and even sporting goods. The advances in automation and robotics have opened up new possibilities for filament winding, including the production of complex shapes and the use of thermoplastic tapes. In this article, we will delve into the different filament winding applications, traditional and enhanced robotic winding methods, and the recent innovations and new paradigms in the field. Get ready to discover how filament winding is transforming the manufacturing landscape, from rockets to racecars.
Jump to the right section
Filament winding application
Filament winding has a long history of producing axisymmetric shapes for various applications, including drive shafts, pipes/tubes, pressure vessels, tanks, rods, masts, missile cases, rocket motor cases, and aircraft fuselages. With the rapid advances in CNC and automation in filament winding equipment since the 1990s, the application of filament winding has expanded to include non-axisymmetric geometries. The section below provides a brief overview of current filament-wound composite structures in the industry.
Filament Winding: From Rockets to Racecars
Filament winding has been a key player in the aerospace industry for decades, playing a vital role in the design and manufacture of rocket engines, fuel tanks, and structural components. The high-strength-to-weight ratio of filament-wound composite materials makes them ideal for use in the harsh and demanding conditions of space travel.

One of the most famous examples of filament winding in the aerospace industry is the Space Shuttle's main fuel tank. This massive tank, which weighed nearly 140,000 pounds, was made up of a composite material that was filament wound around a mandrel. The intricate design of the tank was critical to the success of the Space Shuttle program, as it provided the necessary strength and lightness to withstand the rigors of space travel.

From the skies to the racetrack, filament winding is also being used to create high-performance sports equipment. The strength and durability of filament-wound composites make them ideal for use in car racing components, such as drive shafts and suspension components. In addition, the customizability of filament winding allows manufacturers to create unique shapes and designs that are optimized for maximum performance.
Filament Winding in the Marine Industry

Filament winding has also made a splash in the marine industry, where it is being used to create a range of products from boat hulls to mooring poles. The strength and durability of filament-wound composites make them ideal for use in harsh marine environments, where corrosion and abrasion are common challenges.

One of the most creative applications of filament winding in the marine industry is the creation of custom fishing rods. The use of filament winding allows manufacturers to create unique, lightweight, and high-strength fishing rods that are optimized for specific types of fishing. Whether you're trolling for marlin or casting for trout, filament winding is helping to create a better fishing experience for anglers around the world.
Complex shape structures with Filament winding
The automated filament winding process has been utilized since the 1990s to create intricate structures that deviate from cylindrical shapes. Advancements in technology have enabled the production of a variety of non-cylindrical designs such as toroidal, dome-end cylindrical, and isoprenoid pressure vessels. The filament winding method has also been used to manufacture items such as pipe elbows and tees, preforms for manufacturing, grid structures, aerospace components, car bumper frames, hockey sticks, aircraft radomes, helicopter blades, wind turbine blades, and aircraft fuselages.
Pressure vessels

The use of filament-wound pressure vessels has become widespread in the aerospace and transportation industries, with an estimated annual production of hundreds of thousands of units globally. The automotive sector also has a growing demand for low-pressure vessels for natural gas storage (35 MPa) as well as high-pressure vessels (70 MPa) for hydrogen and compressed natural gas storage.
Pipe fittings

Filament-wound pipe fittings have been used in the chemical and oil industries since the 1980s. With the development of advanced CNC winders with 6 or more axes, automated production has been possible since the 1990s. Generating winding patterns for non-axisymmetric shapes is challenging due to the high data processing requirements.
Motor cases
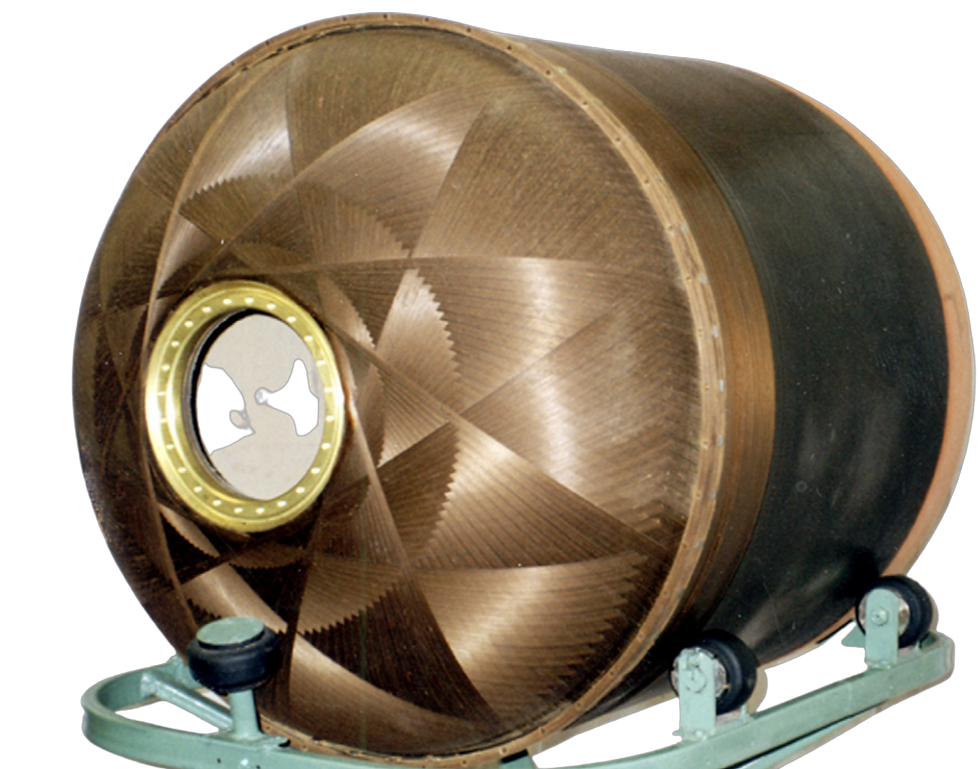
Filament-wound composite structures are widely used in aerospace components, such as rocket motor cases, for their high strength and specific stiffness which provides weight reduction and improved fuel efficiency. Filament winding for rocket motor cases started in 1960 and while it usually involves axisymmetric case designs, the dome area of such cases can have complex geometry and material properties requiring precise manufacturing control.
The Traditional classification of winding
Perimeter winding: the filaments are wound around the circumference of a tool.
Cross winding: the filaments are wound in between gaps in the tool.
Mono-axial cross winding
Mono-axial perimeter winding
Poly-axial cross winding
Poly-axial cross winding
Mono-axial perimeter winding, for example, is commonly used for the creation of rotational components. While monoaxial translation winding is typically applied to create two-dimensional framework structures. In order to realize three-dimensional truss structures poly-axial winding is mandatory to prevent fiber slippage while winding rods coming out of the plane.
![(A) Mono-axial cross winding [12]; (B) mono-axial perimeter winding [13]; (C) poly-axial cross winding [14]; (D) poly-axial cross winding](https://static.wixstatic.com/media/dfe896_529e7e325be0405faf4597bc51bb7f98~mv2.png/v1/fill/w_980,h_303,al_c,q_85,usm_0.66_1.00_0.01,enc_avif,quality_auto/dfe896_529e7e325be0405faf4597bc51bb7f98~mv2.png)
Traditional Filament Winding
Filament winding is a technique primarily used to manufacture hollow, circular, or prismatic parts such as pipes and tanks. It is performed by winding continuous fiber tows onto a rotating mandrel using a specialized winding machine. Filament wound parts are commonly used in the aerospace, energy, and consumer product industries.
Robotic Winding
The emergence of industrial robot technology has enabled the realization of novel winding approaches. In these methods, the fibers are either pulled off by the translation of a fiber guide around turning points or by the rotary motion of a mandrel about multiple axes instead of the traditional way of rotating about just one axis

Traditional vs. Enhanced Robotic Winding
Traditional filament winding is a fairly common industrial low-tech process, limited to axially symmetric shapes such as tubes, ducts, or pressure vessels. The two-axis winder, the simplest production layout, controls the rotation of the mandrel and the transverse movement of the conveying unit, so it is only capable of producing reinforced pipes and tubes. yarns. In addition, the traditional four-axis machine is a general-purpose winder, capable of producing pressure vessels as well. Controlled motion degrees of freedom typically include shaft rotation, horizontal conveying, perpendicular conveying (crossfeed), and rotating yarn delivery head mounted on the cross-feed mandrel. However, these solutions still depend on frequent operator intervention during various winding operations, which has a significant impact on productivity.

Robotic Winding is mainly used for advanced applications and it is a great match for tape winding, resulting in higher-quality parts. In this technique it is also possible to automate ancillary operations previously performed manually, Such as placing mandrels, knotting and cutting threads, and loading mandrels covered with wet yarn into the furnace. grill, chuck extraction, etc.
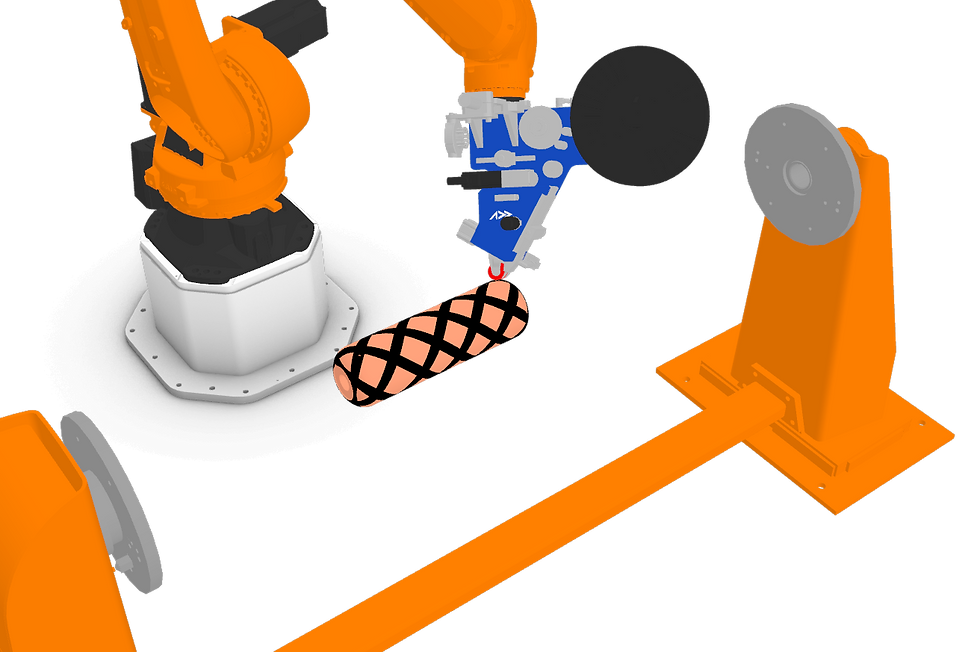
All configuration combinations can use ready-to-use or custom robots, with ABB, KUKA, and Fanuc being the main suppliers, and equipment investment directly correlates with the number of robots used. its use and degree of customization. The great flexibility offered by robotic winding could have broad market penetration potential, allowing the diversification of fiber-reinforced products and applications into new areas.
New Paradigms with Robotic Filament Winding
Thermoplastic Tape winding
Thermoplastic Tape Winding (TTW) is a highly automated process for manufacturing tubular-like fiber-reinforced thermoplastic composites such as flywheels and pipes. One of the crucial parameters in the TTW process is the temperature of the nip point at which the incoming prepreg tape is bonded with the substrate by a compaction roller.
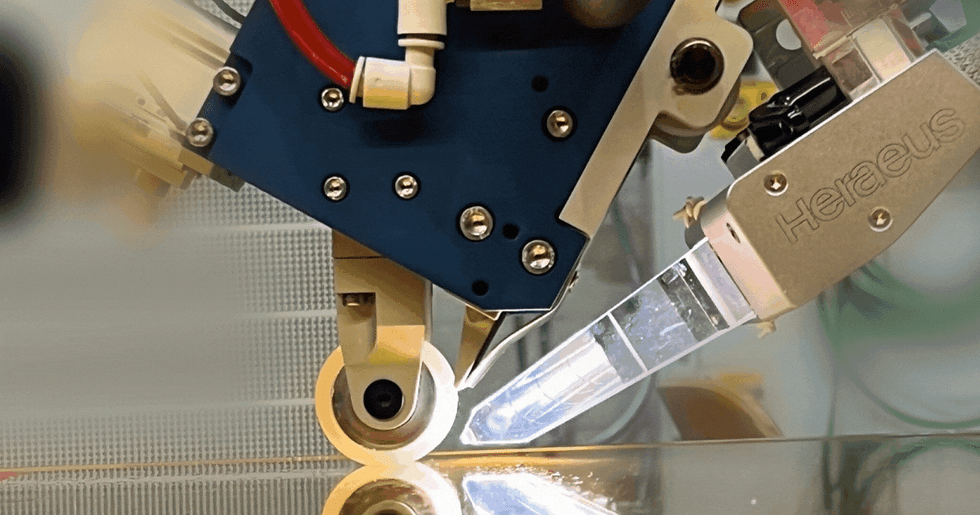
In thermoplastic tape filament winding, complete in-situ consolidation occurs during winding and no post-processing in the oven is required. Therefore, rolled thermoplastic parts can be processed in one production step. The inline fusion of the thermoplastic prepreg takes place instantly, in a fraction of a second, almost during a welding process. This allows for greater freedom of geometries that can be fabricated without post-processing, including flat and concave shapes. Another possible improvement involves the ability to orient the reinforcement locally. Thermoplastic consolidation avoids fiber slippage, providing stability for various winding paths beyond geodesic trajectories.
Enable complex shapes and product trials
Pressure tanks for storage of hydrogen, propellants, or compressed air
Tubes/ Pipes: for water, oil & gas
Structural components: booms, housings, grid structures, interstage
Axis-asymmetric parts: Ducts,
Summary
Filament winding is a versatile manufacturing technique that has a wide range of applications across various industries, including aerospace, automotive, sports, and medical. It offers several benefits, including high strength-to-weight ratios, consistent quality, and precision. The process involves winding fiber filaments around a mandrel to form a composite material with a matrix resin. The resulting structure can be customized to meet specific requirements, making it ideal for various applications, including pressure vessels, pipes, and sporting goods.
In the aerospace industry, filament winding is used to manufacture lightweight, yet strong components for aircraft and spacecraft. For example, the fuel tanks of the Space Shuttle were made using filament winding. The process is also commonly used in the automotive industry to produce high-performance, lightweight components such as steering wheels, drive shafts, and suspension systems. In the sports industry, filament winding is used to manufacture high-performance composite materials for golf clubs, fishing rods, and other sporting goods. The medical industry also benefits from filament winding, using it to produce components such as orthopedic implants and spinal rods.
Filament winding has evolved into robotically enhanced winding, which not only provides additional capability to winding technology but also allows the use of sustainable materials like thermoplastic composites. With the growth of the hydrogen economy and the demand for sustainable production in a labor-shortage market, filament/tape winding will continue to grow in popularity.
References
Faruk, O., & Pekcan, O. (2007). Manufacturing and processing of composites. Materials Science and Engineering: R: Reports, 56(1-6), 1-48.
Hashemi, H. R., Kiani, A. H., & Fazaeli, M. (2017). An overview of the filament winding process and its applications. Journal of Reinforced Plastics and Composites, 36(22), 1841-1855.
Wang, Q., Zhang, Y., & Li, X. (2019). Development of filament winding technology and its applications in composite materials industry. Journal of Cleaner Production, 222, 626-635.
Bouhala, K., & Hssaini, S. (2020). Filament winding: A review of its history, process, and applications. Materials Today Communications, 21, 100805.
Wimpenny, J. I., & Wildman, R. D. (1999). Handbook of composite materials (pp. 1-17). London: Chapman and Hall.
Comentários