Things to Consider When Conducting Composites Repair
- Pravin Luthada
- Jun 23, 2022
- 4 min read
Updated: Jul 13, 2022
Table of Content
The need for repair
A composites product is designed along with materials selection to satisfy specified performance requirements. The shape will normally have been designed to meet known structural requirements and desired aesthetics. The product will continue to function satisfactorily until damage occurs due to material breakdown from wear, fatigue, external impact, or misuse. the decision to repair or replace is taken.
If it is a low-cost and easily disassembled item then direct replacement does not pose a problem. However, many replacement parts are very expensive, so repair must be an option to make a product viable in a service situation.
Repairs
“Best” repair techniques are heavily dependent on the details of the structure. In other words, because composites excel at being tailored to meet very specific needs, there are few “universal” materials and methods that can be used to achieve successful results. Composite repair specifics really have to be determined on a case-by-case basis. The basics process of composite repair remains largely the same i.e.
Inspect to assess damage (extent and degree)
Remove damaged material
Treat contaminated material
Prepare repair area
Complete composite repair; (e.g. replace damaged material and bolt or bond a patch)
Inspect repair for quality assurance (e.g. delaminations, inclusions, proper cure, etc.)
Restore surface finish
However, the decisions made in designing a composite structure, such as thickness, solid laminate or cored construction, shape and curvature, and use of bonded integral stiffeners, all affect what types of inspection and repair will be cost-effective and even possible, in turn affecting overall life-cycle cost.
All repairs of composite or bonded aircraft assemblies should be conducted according to the specific instructions outlined in the structural repair manual
Repairs category
As shown in the Figure below, repairs can be categorized as fill, injection, bolted, or bonded. Simple fill repairs are conducted with paste adhesives to repair such nonstructural damage as minor scratches, gouges, nicks, and dings. Injection repairs use low-viscosity adhesives that are injected into composite delaminations or adhesive debonds. bolted repairs are usually done on thick, highly loaded composite laminates, whereas bonded repairs are often required for thin-skin honeycomb assemblies.
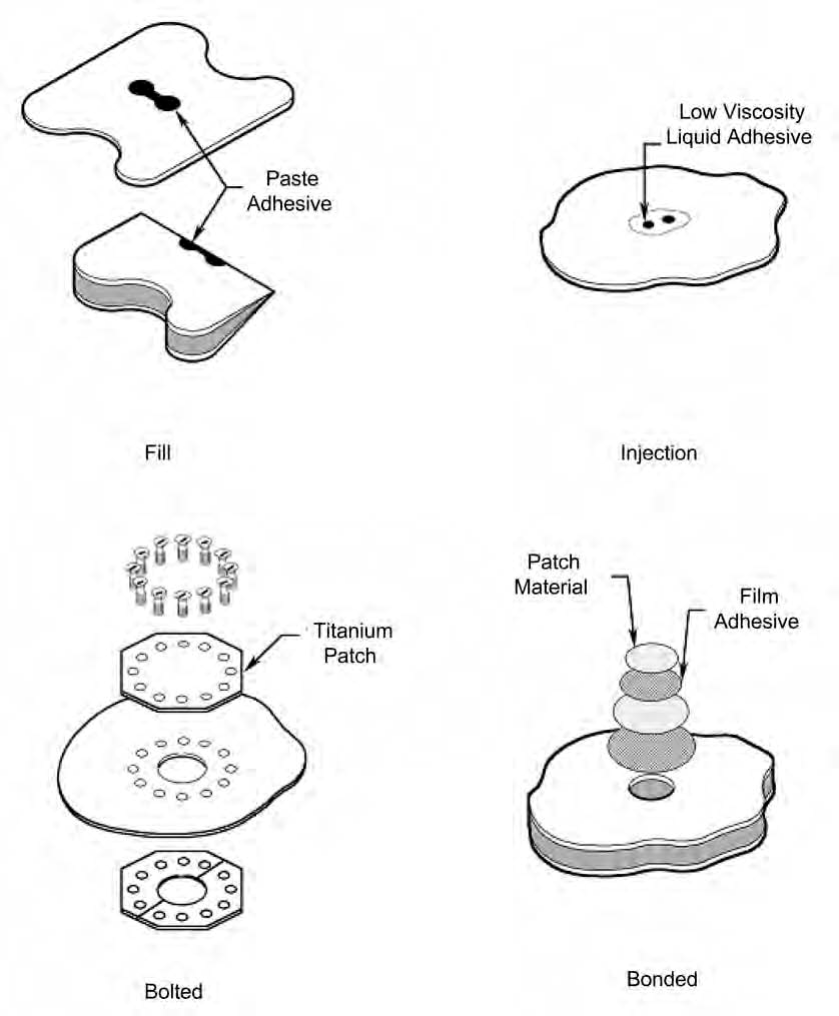
Figure 1. Repair Categories
Fill repairs
Fill repairs are nonstructural and therefore should be confined to minor damage. two-part high-viscosity thixotropic epoxy adhesives are normally used for these types of repairs. the surface to be repaired should be dry and free of any contamination that would prevent the filler from adhering. before filling, the surface should be lightly sanded with 180- to 240-grit silicon carbide paper. once the adhesive is mixed and applied to the surface, most epoxy adhesives will cure sufficiently within 24 hours at room temperature so that they can be sanded flush with the surface. Heat lamps are often used to accelerate the cure by heating the adhesive to 180 ºF (80 ºC) for one hour.
Injection repairs
Low-viscosity two-part epoxy adhesives are injected under low or moderate pressure, as shown in the two examples in Figure 2 below. If the delamination does not extend to an edge, small-diameter, flat-bottom holes 0.050 in. (1.3 mm) in diameter are drilled to a depth usually determined by pulse-echo ultrasonics. two or more holes are generally required, one for injection and one for venting. to help the resin flow into tight delamination, it is helpful to preheat the delaminated area to 120 to 140 ºF (50 to 60 ºC). preheating reduces the resin’s viscosity and helps it flow into the delamination.
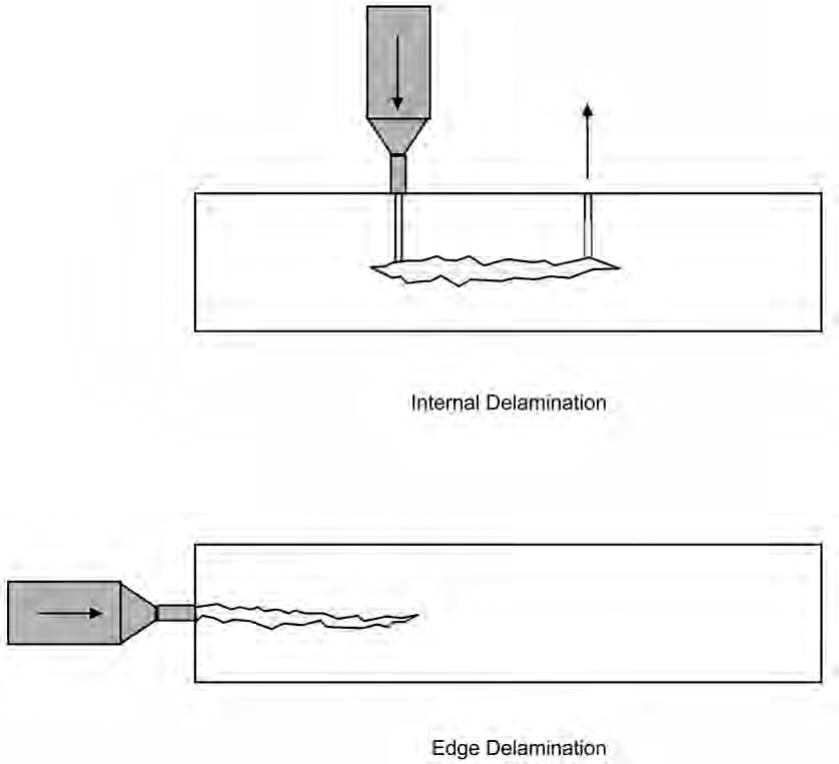
Figure 2. Internal Delamination and Edge Delamination
Bolted repairs
A typical bolted repair consists of an external titanium patch, a center plug in the damaged area, and a two-piece internal patch. the internal patch is split into two pieces so that it can be inserted inside the skin. normal composite drilling and fastener installation procedures are used. After all of the holes have been drilled and reamed to
their final sizes, the patch is removed and deburred. A layer of woven glass cloth is impregnated with sealant to provide both sealing and corrosion protection. the full-size holes in the patch are countersunk, and the patch is installed with either one-sided blind fasteners.

Figure 3. Bolted Repairs Procedure
Bonded repairs
A typical hot-bonded field repair procedure consists of the following steps:
the damaged area is mapped out with pulse-echo ultrasonics to determine whether the repair falls within the limits of the structural repair manual. (If it does not, then a strength engineer should be consulted for an alternative course of action.)
the damaged plies are carefully removed using high-speed routers with depth control.
the repair area is bagged with a heat blanket and subjected to full vacuum (22 in. (559 mm) of Hg vacuum minimum)
the cured patch is unbagged and the area cleaned up. the quality of the repair is inspected with pulse-echo ultrasonics. the repaired area is refinished to match the rest of the structure.
The process is shown in the quick video here:
Video 1. Composite Repair for Aviation Industry (Source: Q1 Aviation Ltd.)
Summary
Composite repairs are needed due to either manufacturing defects or in-service defects. Once the defect is identified depending on the nature of the defect fill, bonded, bolted or injection repairs can be carried out. After the repair, Non-destructive Testing is carried out to ensure the repair's success (You can read more about Non-destructive Testing here).
About Addcomposites
Addcomposites is the provider of the Automated Fiber Placement (AFP) ecosystem - including the Fiber Placement System (AFP-XS), 3D Simulation and Programming Software (AddPath), and Robotic Cells (AddCell). With the leasing program for the AFP system (AFPnext), composites manufacturers can work with thermosets, thermoplastics, dry fiber placement, or in combination with 3D Printers on a monthly basis.
Sources:
Subscribe to our newsletter and get our guidebook - "Composites Manufacturing Methods: An Ultimate Guide for 2022"
Comments